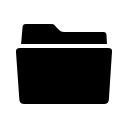
Uncategorised (4996)
Using pump data to predict downtime and identify engineered solutions
For those in the energy industry, being able to identify pre-failure conditions and anomalous operation can offer a considerable advantage to a repeatable budget and bottom-line margins. Using this intelligence to permanently remove failure modes through retrofit solutions will further extend the service life of rotating equipment.
Seth Tate, Technical Advisor with Sulzer, looks at how a cutting-edge software solution can analyze existing pump telemetry to reduce downtime and justify engineering improvements.
Around the world, operators of high-energy pumps are well aware of the high running costs and therefore looking for effective and reliable strategies to reduce them. Implementing pro-active maintenance strategies is well-known to have a positive effect on downtime. Now it is possible to use data from existing sources to provide intelligence that will allow system availability and reliability to be improved.
Experienced machine tool operators are key to setting up and operating precision equipment for extensive repairs or retrofits
Cost of downtime
The reduction in maintenance costs and equipment repair time are directly linked to corrective maintenance strategies, such as preventative maintenance, discrete predictive maintenance or online predictive maintenance. As the techniques to identify pre-failure conditions become more sophisticated, it is possible to perform the right maintenance task at the most opportune time. In addition, the insight provided can also be used to justify retrofit solutions.
These extend the normal operating conditions of high value assets. At the same time, predictive maintenance strategies can leverage existing data sources and maximize their efficiency by applying big data analysis principles. This enables operators to achieve maximum availability and throughput and when high-value commodities are involved, this can amount to a lost profit opportunity (LPO) of USD 200’000 per day.
In terms of performance and efficiency, a 4’000 hp (3’000 kW) pump operating at 43% of its best efficiency point (BEP) flowrate will present an LPO of approximately USD 300’000 per year. Looking at how reliability affects outcome, chronic seal failures in high-energy equipment can cost USD 18’000 per occurrence but including lost production can see costs rise to USD 144’000 per failure.
Therefore, being able to implement remedial actions during planned maintenance periods before component failure occurs as well as understanding the root cause of an issue can deliver considerable value for the business.
A well-organized pump repair workshop reduces downtime and minimizes costs
Pump data acquisition
In order to translate equipment performance data into actionable intelligence, the related sensors as well as a conduit between the sensors and software must exist. Many pumping systems already have the necessary resources to satisfy data acquisition needs. The historical performance data that is already being stored can provide insights that are essential for the active monitoring process. By making better use of this stored data, it is possible to accelerate the journey to realizing value.
Advanced pump analytics
By developing a software solution that integrates with existing data platforms, the opportunity already exists to conduct big data analyses. Equipment that is designed using advanced physics can be monitored under the same principles. Sulzer’s solution, known as BLUE BOXTM, creates a prediction map of equipment operation using both Sulzer’s expertise in failure mode and effects analysis (FMEA) modeling and machine learning intelligence.
What if operators were informed that equipment is running below minimum continuous stable flow? What advantage is there to knowing that a bearing is failing?
Using the gathered data, this advanced analytics approach goes beyond just a digital twin to detect pre-failure conditions and optimization opportunities. Key to the added value are an out-of-the-box readiness, false positive prevention, advanced physics and an operational dashboard.
At the same time as identifying future maintenance interventions, there is a requirement to derive the most effective solution and justify the cost in terms of lost performance or downtime that can be saved. This enables engineering managers to assess potential solutions and provide a cost analysis, all before the predicted issue has an impact on production.
Retrofit solutions can be used to permanently remove causes of failure through improved engineering, design, maintenance or operation
Retrofit to improve existing assets
Having identified the issue, retrofit solutions can be used to permanently remove causes of failure through improved engineering, design, maintenance or operation. The best course of action can be identified through gap analysis – comparing the current solution, which is experiencing reliability issues, to the best-in-class design. Today, the latest engineering technology can do more than just remove specific failure causes on legacy equipment.
In addition, retrofits can be implemented to address new or updated hydraulic needs. Having identified the performance topography, a new hydraulic profile can be manufactured without disturbing the footprint of the pump installation by applying computational fluid dynamics (CFD) and an original equipment manufacturer’s (OEM’s) considerable hydraulic experience.
Total cost of ownership
In a world where downtime can be measured in hundreds of thousands of dollars per day, even modest improvements in availability can have a significant improvement in operating costs. For instance, an improvement of 0.08% in the performance of a high-energy pump will equate to 72 hours per year of uptime that would have otherwise been lost. This can potentially deliver an improved annual income of approximately USD 650’000.
In the example of pump performance, the data analysis solution can illuminate tangible opportunities for effective improvements. In addition, removing the residual effect with off-BEP performance can eliminate failure modes and extend the service life of the pump, promoting uptime and reducing the total cost of ownership (TCO). Putting this into numbers, recovering 32 efficiency points equates to approximately USD 290’000 in running costs.
Expert pump support
As an original equipment manufacturer (OEM), Sulzer has combined its expertise in pump engineering and extensive experience in pump operation to create BLUE BOX, an advanced analytics solution that can deliver expert insight into any pumping system.
Simple integration, with no additional hardware and a secure interface, BLUE BOX uses existing telemetry and communication protocols to analyze the data. It is designed to grow with future technological changes and provide continuous visualizations through a customized operator dashboard. Now, it is possible to predict the future of maintenance operations and use this information to optimize business performance.
About Sulzer
Sulzer is a global leader in fluid engineering. We specialize in pumping, agitation, mixing, separation and application technologies for fluids of all types. Our customers benefit from our commitment to innovation, performance and quality and from our responsive network of 180 world-class production facilities and service centers across the globe. Sulzer has been headquartered in Winterthur, Switzerland, since 1834. In 2019, our 16’500 employees delivered revenues of CHF 3.7 billion. Our shares are traded on the SIX Swiss Exchange (SIX: SUN).
Throughout the Americas, Sulzer provides cutting-edge parts as well as maintenance and repair solutions for pumps, turbines, compressors, motors and generators. We service our own original equipment as well as third-party rotating equipment operated by our customers. Our technology-based solutions maximize reliability and lifecycle cost effectiveness.
For more information on Sulzer, visit www.sulzer.com
- Sulzer
- pump analysis
- energy industry
- retrofit
- rotating equipment
- cutting-edge software
- maintenance costs
- predictive maintenance
- best efficiency point (BEP)
- pumping systems
- BLUE BOX
- failure mode and effects analysis (FMEA)
- gap analysis
- computational fluid dynamics (CFD)
- original equipment manufacturer’s (OEM’s)
PROSEAL SOLUTIONS MEET QUALITY PET FOOD PACKING REQUIREMENTS
AdministratorProseal tray sealing technology is enabling pet food manufacturers to meet growing demand for high quality products and packaging, as well as providing mass customisation solutions that can help businesses in the sector to diversify and introduce online ordering for home delivery services.
A recent report from Transparency Market Research has predicted a CAGR of 6% in the global pet food market in the ten years from 2019, reaching an expected value of US$168.3 bn by autumn 2029. Increasing consumer demand for premium quality products has led manufacturers to use high quality materials and ingredients while streamlining their production techniques and processes, with the corresponding need for appropriate quality packaging to reflect this premium image.
The comprehensive Proseal tray sealer range has the flexibility to perform in a wide range of disciplines, including Gas Flush Modified Atmosphere Packaging (MAP), Vacuum MAP with lid control and Skin Packaging. In particular, the company’s advanced sealing systems ensure absolute control and integrity of the seal between the lid and the tray, a vital requirement for applications that incorporate a substantial controlled-retortion-process or other High Pressure sterilisation processes after sealing.
The tray sealers also include several Proseal-developed features that help to maximise performance, reliability and efficiency, such as the company’s pioneering Eseal® energy saving technology, ifilm™ intelligent film monitoring, and ProTect™ RFID access login system that provides full audit trail visibility and layered security.
In addition, Proseal’s AP60 linear conveyor tray sealing system is able to provide bespoke automated solutions for high speed applications and demanding production conditions, based around individual customer production processes and requirements.
Among the system’s many features, the length and width of the indexing conveyor can be customised to accommodate particular de-nesting and filling requirements. Full or partial vacuum systems can be incorporated to enable post seal processes such as retort or High Pressure Processing (HPP), and X-ray inspection systems and checkweighers can be included after sealing for enhanced quality control. The AP60 also offers seamless integration with third party process equipment including depositors, multihead weighing applications and CIP systems with sealing speeds of up to 240 packs per minute.
Furthermore, Proseal’s AP60 benefits from shared technology across the Proseal machinery range. Options can be specified and retro-engineered at the customer request, allowing a more flexible approach to each distinct application.
All Proseal machines offer a user-friendly interface and easy to maintain design, with a rugged and hygienic food industry approved construction geared to full washdown protection.
“As the pet food market continues to expand, we were keen to provide solutions for companies requiring a significant upscale in their production of core products in new packaging formats, which could be met on one machinery platform,” said Tony Burgess, Head of Sales and Control Systems, Proseal.
“The flexibility of our technology and the wide variety of machines available, including fully integrated conveyor systems, mean we can offer a full turnkey production line solution which is key for this particular market.
We are delighted that our expertise can help companies to achieve a point of differentiation in the competitive pet food sector.”
Founded in 1998, Proseal designs and manufactures high quality tray sealing machines, conveyor systems and sealing tools for food industry markets worldwide. The company became part of the US-based JBT Corporation in 2019. JBT is a complete solutions provider to the growing pet food sector, committed to exceeding customer expectations.
For further information about Proseal’s AP60 tray sealer please visit: https://www.proseal.com/machines/conveyor/ap60/
Or
https://www.jbtc.com/en/north-america/foodtech/markets/pet-food
UK upstream sector remains resilient through turbulent times, says GlobalData
AdministratorThe UK upstream oil and gas sector has become leaner and more resilient over recent years, as pullbacks in investment and reduced operating costs has helped provide a stronger cash flow outlook under newly weakened oil and gas prices, says GlobalData, a leading data and analytics company.
Daniel Rogers, Oil and Gas Analyst at GlobalData, comments: “Despite a relatively expensive operating environment, a favorable fiscal regime and vast active infrastructure has helped the UK oil and gas sector to remain attractive.
“Under a base case oil price of US$45/bbl for 2020, the outlook for post-tax cash flow/boe is in line with 2013 levels when oil prices were over US$100/bbl. The country has been able to improve cash flow margins as investments are reduced and costs optimized.”
Despite the direct impacts of COVID-19 on the UK oil and gas sector, production levels are expected to remain relatively unaffected in spite of a number of operational assets being hit by related disruptions.
Rogers adds: “The last three years have seen significant field reserves come on-stream in the UK through developments sanctioned prior to the 2014 price crash. The UK has a steady near term production outlook through already sanctioned developments and COVID-19 disruptions are unlikely to drastically hamper 2020 volumes. Despite this, investment in the sector is forecast to dip this year from 2019 levels and the capital expenditure outlook remains particularly weak.”
- Quotes provided by Daniel Rogers, Oil and Gas Analyst at GlobalData
About GlobalData
4,000 of the world’s largest companies, including over 70% of FTSE 100 and 60% of Fortune 100 companies, make more timely and better business decisions thanks to GlobalData’s unique data, expert analysis and innovative solutions, all in one platform. GlobalData’s mission is to help our clients decode the future to be more successful and innovative across a range of industries, including the healthcare, consumer, retail, financial, technology and professional services sectors.
BASF and IntelliSense.io partner to accelerate the mining industry’s digital transformation
AdministratorGlobal chemical company BASF and IntelliSense.io, a leading industrial artificial intelligence (AI) company, announced an exclusive partnership which will combine their expertise in mineral processing, ore beneficiation chemistry and industrial AI technology. The joint offering is called the ‘BASF Intelligent Mine powered by IntelliSense.io’ and delivers AI solutions embedded with BASF’s mineral processing and chemical expertise. This solution will enable mine operations to become more efficient, sustainable and safe.
- BASF and IntelliSense.io announce strategic partnership combining chemical, mineral processing and digital expertise
- BASF Intelligent Mine powered by IntelliSense.io delivers artificial intelligence solutions for ore beneficiation providing remote 24/7 optimization across the mine-to-market value chain
- Optimization as a Service (OaaS) applications can be configured for individual mine sites within three months
BASF Intelligent Mine powered by IntelliSense.io is an open, real-time, decision-making platform that can be configured for individual sites, typically within three months. Each mining process, such as grinding, thickening, flotation and pumping, is supported by an Optimization as a Service (OaaS) application which predicts and simulates future performance, generating process-specific recommendations for insights and optimization. As multiple OaaS applications link together, customers can generate efficiency gains throughout the entire mine-to-market value chain.
Remote operations access allows for 24/7 visibility of mine operational and financial performance, with BASF process experts available to provide real-time support. Additionally, the in-built simulation tool can be used to test alternative operating conditions, train staff and run non-intrusive ‘what if’ scenarios.
The AI solutions are based on a hybrid cloud architecture, enabling both on site and cloud deployments, to help mining industry partners accelerate their digitalization programs in their operations.
Early adopters of the Intelligent Mine, Image Resources, have experienced promising results from the Intelligent Mine deployment in the mineral sands industry. “Image Resources is both excited and optimistic about the potential the BASF Intelligent Mine powered by IntelliSense.io can have to positively impact the accuracy and efficiency of our process control functions to meaningfully improve our bottom-line,” said Patrick Mutz, Image Resources Managing Director. “From our experience so far, we are confident it will achieve these results whilst simplifying and de-stressing operational decision making.”
“Our partnership with IntelliSense.io combines state of the art artificial intelligence and decades of ore beneficiation experience in to a powerful, fast and easy to deploy optimization platform,” said Damien Caby, Senior Vice President, BASF Oilfield Chemicals & Mining Solutions. “Efficiency improvements resulting from the first implementations by our joint dedicated team are helping customers accelerate the digital transformation of their mining operations.”
"In a tough economic climate, the need to focus on mining productivity, within sustainable and remote operational constraints, is driving pressure on operating and capex budgets and requires innovative solutions with accelerated value delivery,” added Sam G. Bose, CEO IntelliSense.io. “The partnership between BASF and IntelliSense.io ensures mining organizations have a partner that understands both their operational risk as well as new technologies.”
For those looking to accelerate their current digitalization efforts, more information on the BASF Intelligent Mine powered by IntelliSense.io can be found on www.basfintellisense.io or via a BASF Mining Solutions representative.
NEW DATA REVEALS ONE THIRD OF THE FOOD AND DRINK INDUSTRY ARE VERY CONCERNED ABOUT THEIR SAFETY IN RETURNING TO WORK
Administrator- 81% of business owners are concerned about profits not returning to normal
- Over half (56%) of food catering businesses are very concerned about job security following the pandemic
- One third of the food manufacturing industry are currently furloughed or unable to work
Since the 4th of July, many industries, businesses, and establishments have been able to return to work, with social distancing guidelines in place. But how do some staff members in those industries feel about going back? Are they ready and do they feel safe?
Virtual College surveyed the retail, manufacturing and catering sectors of the food and drink industry to understand their views on returning to work following the Covid-19 pandemic, and the results are very surprising. The main concerns being how are businesses going to be profitable, access to adequate PPE and how to return safely both for themselves and their customers.
Food Catering:
- 64.5% of people working in food catering are very concerned or about the safety of customers/guests
- 69% are very concerned about the safety of themselves/colleagues
- 87% feel that it is very important that they have access to adequate PPE
- 55% of food catering business owners are very concerned profits will not return to normal
- 56% are very concerned about job security following the pandemic
- 63% are concerned about social distancing in the workplace on returning to work
Food Manufacturing:
- 31% in food manufacturing are currently furloughed or unable to work
- 44% are not at all concerned about social distancing in the workplace
- Only 41% are very concerned about job security
- 64% are very concerned about profits
- 92% feel it is very important to have access to adequate PPE
- 52% are concerned about social distancing in the workplace on returning to work
Food Retail:
- 27% feel that their business/employer is not prepared to return to work safely
- 58% are very concerned about the safety of themselves/colleagues
- 86% feel it is very important for them to have access to adequate PPE
- 70% are concerned about social distancing in the workplace
Many concerns were raised within the survey, so to provide information and suggest best practice for businesses in the current climate, Virtual College have gone on to deliver over 150,000 online COVID-19 courses to both businesses and individuals
“Virtual College reached out to obtain the views of people working in the food industry to ensure the online training we provide is tailored to the immediate needs of our customers. Indeed, some of our courses are updated every week due the constantly changing Covid-19 situation”. – Peter Hilliard, Marketing Manager
For more information on the study and the free courses to aid businesses, please visit:
https://www.virtual-college.co.uk/resources/2020/07/post-lockdown-the-return-to-work-for-the-food-and-drink-industry
About Virtual College
Virtual College - https://www.virtual-college.co.uk
Virtual College is one of the UK’s leading providers of online learning. We have been at the forefront of e-learning for over twenty years and have a wealth of experience developing and providing training that positively impacts individuals, teams and organisations.
We constantly strive to deliver up-to-date and engaging online learning, supported by the very latest in learning management system technology, to enable individuals and organisations to reach their full potential. That’s why we recently won ‘Learning Technologies Supplier of the Year 2016-17’ and ‘E-learning Development Company of the Year 2015-16’.
About the Study
Virtual College received over 350 responses to a survey sent to people who own businesses or work in the food and drinks industry to establish their views on their imminent return to work following the COVID-19 pandemic.
SCHROEDAHL Announces the New All-in-One Pump Protection TDL Automatic Recirculation Valves in 10 and 12 nominal pipe size (NPS) with High Bypass Flow
AdministratorHigh-efficiency self-modulating pump protection valves offer reliability and cost savings.
SCHROEDAHL, a CIRCOR International brand and an international leader in pump protection and flow control technology, announces new, self-modulating TDL Automatic Recirculation Valves (ARVs) in 10 and 12 NPS are now available with high Bypass Flow offering maximum flexibility in bypass trim sizes for pumping systems. These reliable all-in-one pump protection solutions are designed to keep pumping systems in process, firefighting, refinery, power and chemical applications modulating and running smoothly, without cavitation, vibration or overheating.
Without minimum flow, a pump can quickly suffer grave damage, causing downtime and costly repairs—but control valves for recirculation require continuous control of complex equipment, a flow measurement device, control unit, and energy supply. Unlike control valve packages, the self-operated flow-sensitive SCHROEDAHL TDL Automatic Recirculation Valves operate without a separate power supply or any control system—and begin protection immediately once installed.
SCHROEDAHL TDL Automatic Recirculation Valves combine a high-quality main line check valve and the automatic bypass control system in an innovative and durable design. The valves’ self-actuated integrated bypass control function ensures minimum flow rate, guarding pumps against overheating and cavitation. The systems provide high pump stability—with less vibration and fewer coupling or gear problems—for less downtime and lower maintenance costs. TDL ARVs’ modulation bypass function also offers savings for operators with reduced energy consumption for frequent partial load operation.
Additionally, the bypass check valve prevents reverse pump flow, and allows for parallel pump installations. With extremely low valve hysteresis, TDL ARVs promote increased and reliable pump performance.
These valves are designed and built with high bypass trims size flexibility. TDL ARVs’ high bypass flow offers maximum flexibility in bypass trim sizes for pumping systems with 10 or 12-inch nominal pipe size (NPS). Available in EN/DIN and ASTM materials,
For more information about SCHROEDAHL Automatic Recirculation Valves, visit www.circor.com/products/valves/pump-protection.
About SCHROEDAHL and CIRCOR International, Inc.
With the invention of the original Automatic Recirculation Valve for pump protection, CIRCOR SCHROEDAHL is an international leader in pump protection and flow control technology. The company designs, manufactures, distributes, and maintains high-class specialty pump protection and control valves. CIRCOR SCHROEDAHL valves are designed at the highest level of quality for high-pressure applications in nuclear and fossil power, industrial process, and commercial systems, as well as production, extraction, and refining systems in the oil and gas sector. For more information about SCHROEDAHL products, visit https://www.circor.com/schroedahl.
CIRCOR International, Inc. designs, manufactures and markets differentiated technology products and sub-systems for markets including oil & gas, industrial, aerospace & defense and commercial marine. CIRCOR has a diversified flow and motion control product portfolio with recognized, market-leading brands that fulfill its customers’ mission critical needs. The company’s strategy is to grow organically and through complementary acquisitions; simplify CIRCOR’s operations; achieve world class operational excellence; and attract and retain top talent. For more information, visit the company’s website at www.circor.com.
Venezuela’s oil and gas sector sees worst crisis during 2020, says GlobalData
AdministratorVenezuela’s oil and gas sector was already caught in a vicious cycle well before the COVID-19 outbreak created a world economic crisis. Even though there are several international companies still remaining in the country, they are not investing in any relevant manner and have minimum personnel. GlobalData Oil & Gas Analyst Adrian Lara notes that it is fair to assume that, for most of these operators, the best scenario would be to wait for a change in government that could kick-start the sector under renewed rules or laws and improve their partnership terms with PDVSA. However, the political situation in the country seems to be going nowhere in the near future, and even with a change of regime, the oil and gas sector will require many years to recover.
Lara explains: “The country’s hydrocarbon sector has suffered from chronic underinvestment for years, with noteworthy kicks including 2019, when the US Government imposed sanctions on the country’s oil trade - its main source of revenue. This has effectively restricted the exporting capabilities of the country, created operational bottlenecks and left the Venezuelan Government, and its NOC PDVSA, with fewer and fewer means to invest in the sector. The outcome of all these events has been a continuous oil production decline since 2015, with a historic low output in May, reported at 570 thousand barrels per day (mbd), and with only one oil rig operating in the country.
“After the 2019 sanctions, exports to China and India somehow compensated the loss of US buyers. However, during 2020, both lower demand for crude worldwide and a tightening of sanctions have reduced export capability to its worse level to date. Lower exports have led to an increase in the storage capacity utilization of the country, which has a peak operating capacity estimated at less than 40 million barrels. In consequence, the Orinoco Belt has experienced additional production cuts. Production in this area is currently estimated at 161mbd, already three times lower than in 2019.
“As for natural gas, there were some promising projects announced to develop Venezuela’s vast offshore reserves. In fact, during the last five years. negotiations between the Venezuelan government with Russia’s and Trinidad and Tobago’s counterparts had put these projects back on track. However, after a worsening of the political and economic climate of the country these projects are currently on hold.”
About GlobalData
4,000 of the world’s largest companies, including over 70% of FTSE 100 and 60% of Fortune 100 companies, make more timely and better business decisions thanks to GlobalData’s unique data, expert analysis and innovative solutions, all in one platform. GlobalData’s mission is to help our clients decode the future to be more successful and innovative across a range of industries, including the healthcare, consumer, retail, financial, technology and professional services sectors.
Alfa Laval launches new product range for safe and clean tap water duties
AdministratorAlfa Laval – a world leader in heat transfer, centrifugal separation and fluid handling – launches the first 100 percent stainless steel heat exchanger, Alfa Laval AlfaNovaTW, to address the challenge with contaminated tap water. The new heat exchanger eliminates the risk of unsafe drinking and tap water due to metal release from equipment made of nickel and copper.
Limiting heavy metal contamination in drinking water is critical for public health and required by law in many jurisdictions. As many of the heat exchanger technologies still used in tap and warm water applications leak traces of nickel and copper into water supplies over time, Alfa Laval is now addressing this challenge. The new Alfa Laval AlfaNovaTW, with the patented fusion bonding technology, is a 100 percent stainless steel construction which thereby eliminates the risk of contaminating the tap water by heavy metals.
“This latest addition to our AlfaNova heat exchangers’ range is a proof of how we work with innovation to improve the conditions for people and planet,” says Susanne Pahlén Åklundh, President of the Energy Division. “Not only does this new heat exchanger address and solve a problem that is critical for human health, the 100 percent stainless steel design gives us a product that is fully recyclable, which is beneficial for the environment.”
Did you know that… today each AlfaNova heat exchanger is made with up to 90% recycled materials?
This is Alfa Laval
Alfa Laval is active in the areas of Energy, Marine, and Food & Water, offering its expertise, products, and service to a wide range of industries in some 100 countries. The company is committed to optimizing processes, creating responsible growth, and driving progress – always going the extra mile to support customers in achieving their business goals and sustainability targets.
Alfa Laval’s innovative technologies are dedicated to purifying, refining, and reusing materials, promoting more responsible use of natural resources. They contribute to improved energy efficiency and heat recovery, better water treatment, and reduced emissions. Thereby, Alfa Laval is not only accelerating success for its customers, but also for people and the planet. Making the world better, every day. It’s all about Advancing better™.
Alfa Laval has 17,500 employees. Annual sales in 2019 were SEK 46.5 billion (approx. EUR 4.4 billion). The company is listed on Nasdaq OMX.
Asia dominates global LNG regasification capacity additions through 2024, says GlobalData
AdministratorAsia is expected to witness the highest global liquefied natural gas (LNG) regasification capacity additions, contributing about 69% of the total regasification capacity additions by 2024, says GlobalData, a leading data and analytics company.
The company’s report, ‘Global Capacity and Capital Expenditure Outlook for LNG Regasification Terminals, 2020–2024 – China Spearheads Global Regasification Capacity Additions and Capex Spending, reveals that Asia is likely to witness a total regasification capacity additions of 11.1 trillion cubic feet (tcf) by 2024. Out of this, capacity of planned projects that have received necessary approvals for development accounts for nearly 7.9 tcf.
Haseeb Ahmed, Oil and Gas Analyst at GlobalData, comments: “Asia is expected to witness the start of operations of 53 new-build LNG regasification terminals by 2024. Out of these, 39 are planned and the remaining 14 are announced terminals. China’s Tangshan II is the largest upcoming LNG regasification terminal with a capacity of 584 bcf by 2024, followed by Son My II with a capacity of 450 bcf.”
GlobalData identifies Europe as the second highest contributor to the global LNG regasification capacity additions contributing around 10% by 2024. The region is expected to witness the start of operations of seven planned and three announced projects. Germany’s Wilhelmshaven Floating and Brunsbuttel are two of the largest upcoming terminals in the region with a capacity of 353 bcf and 282 bcf, respectively, by 2024. Spain’s El Musel is the third largest terminal with a total capacity of 247 bcf during the outlook period.
Middle East ranks third across the globe contributing about 9% of world’s LNG regasification capacity additions during the outlook period 2020–2024. The region has two planned projects, with a combined capacity of 1,447 bcf. Kuwait’s Al-Zour is the largest among the two with a capacity of 1,155 bcf by 2024, while Bahrain Floating is expected to have a total capacity of 292 bcf by the end of outlook period.
- Comments provided by Haseeb Ahmed, Oil & Gas Analyst at GlobalData
- Information based on GlobalData’s report: Global Capacity and Capital Expenditure Outlook for LNG Regasification Terminals, 2020–2024 – China Spearheads Global Regasification Capacity Additions and Capex Spending
- Announced/Planned: Denotes only new-build assets that are in different stages of development and have not started commercial operations
- A new-build project that has not received relevant/ required approvals to develop/build the project is considered as Announced
- A new-build project that has received relevant/ required approvals is considered as Planned
- This report was built using data and information sourced from proprietary databases, primary and secondary research, and in-house analysis conducted by GlobalData’s team of industry experts.
About GlobalData
4,000 of the world’s largest companies, including over 70% of FTSE 100 and 60% of Fortune 100 companies, make more timely and better business decisions thanks to GlobalData’s unique data, expert analysis, and innovative solutions, all in one platform. GlobalData’s mission is to help our clients decode the future to be more successful and innovative across a range of industries, including the healthcare, consumer, retail, technology, energy, financial and professional services sectors.
Datalogic Introduces the AV900 image-based code reader for Logistics applications
AdministratorDatalogic is pleased to introduce the AV900 industrial 9MP image-based code reader for applications in transportation, logistics, distribution and airports. The AV900 extends the Datalogic AV family with a new product that delivers more resolution and power allowing one device to do the work of multiple devices. The AV900 delivers enhanced processing power coupled with an increased field of optical view that maximizes throughput and reduces system costs.
This new device has an industry-leading high resolution 9MP sensor combined with the Intel Pentium QUAD core processor. Together, they deliver image acquisition at 32 frames per second along with dynamic and adjustable focus. These features allow the AV900 to excel in several applications from inbound to sorting on large conveyors at high speed.
The 9MP sensor provides a 40% larger field of view allowing enterprises to use fewer devices to cover the same area when compared to 5MP units, greatly reducing the overall system cost.
Unlike other adjustable focus devices that can only be defined during the installation or tuning process, the AV900 has extensive focusing capabilities including:
- Unique Sequential two-zone focus: the AV900 can go between two different preset zones. This is ideal for sorting objects in bomb bay sorters or code reading on a pallet where focusing device are not mounted.
- Dynamic Focusing: Interfacing with a focusing device such as a sensor, light curtain or dimensioner providing the best reading capabilities on objects of different dimensions at high-speed.
These flexible, dynamic focus capabilities greatly increase the depth of focus, the quality of the images and provide excellent performance over a wide range of applications. This is especially useful for hard-to-read bar codes.
The high-quality image capability coupled with a dedicated high speed ethernet port for image transfer makes AV900 ideally suited for OCR, video coding applications and postprocessing inspection analysis.
Other features such as continuous frame acquisition, no-flashing white or red integrated illumination, and colored spot indicator make the AV900 image-based code reader the perfect solution for operator attended applications. This includes manual object presentation in overhead scanning mode, manual conveyor loading or pallet traceability.
The AV900 seamlessly integrates with other products in AV family that can be combined to deliver a top performance traceability solution at the lowest system cost. The AV900 includes new automatic software-based redundancy and configuration sharing with the complete line of Datalogic AV cameras. These features greatly reduce system down time and make easy to install new units.
Interfacing and monitoring the AV900 is easy. The device is compatible with Datalogic’s WebSentinel™ PLUS for real-time performance monitoring. Moreover, it can be interfaced to major industrial networks such as Fieldbus and PROFINET. It can interface with Ethernet IP enabled PLC’s through two Ethernet TCP/IP and two serial communication interfaces.
The new Datalogic AV900 raises the standard for industrial and logistics applications. Integrators and enterprises in transportation, logistics, distribution and airports can easily create solutions that reap the benefits of maximized traceability and more efficient processes for a reduced Total Cost of Ownership.
Learn more at
Datalogic Group
Global leader in the automatic data capture and factory automation markets since 1972, Datalogic empowers the efficiency and quality of processes in the Retail, Manufacturing, Transportation & Logistics and Healthcare industries.
Datalogic S.p.A. is listed in the STAR segment of the Italian Stock Exchange since 2001 as DAL.MI. Visit www.datalogic.com
Datalogic and the Datalogic logo are registered trademarks of Datalogic S.p.A. in many countries, including the U.S.A. and the E.U.
More...
MOL makes gas and condensate discovery in the TAL Block, Pakistan
AdministratorMOL, as the operator of TAL Block in Pakistan, has made a new gas and condensate discovery. This marks the company’s 13th discovery in Pakistan and the 10th discovery in the TAL Block.
The Mamikhel South-1 exploratory well successfully reached a total depth of 4,939 m on 23 May 2020. Upon testing the well flowed gas and condensate from Lockhart & Hangu formation at a flow rate of 6516 boepd (16.12 MMscf/d and 3240 bpd respectively), with flowing well-head pressure of 4,476 PSI at 32/64” choke. Further testing of the well is ongoing.
- MOL as an operator discovered significant gas and condensate reserves in Pakistan
- This is the 13th discovery of MOL in Pakistan during the last 21 years since the company is present in the country
- MOL Pakistan is a highly successful operator and an important contributor to Pakistan’s energy security, in addition, employs more than 400 people
- It’s the 2nd time in 3 months that MOL discovers hydrocarbon reserves - in March 2020 MOL Norge discovered oil and gas in the North Sea
MOL aims to transform its E&P division into an international platform and the new discovery strengthens this ambition further
MOL has a proven track record of successfully operating in Pakistan’s upstream sector for 21 years and holds equity stakes in four blocks in the country. MOL has made 13 oil, gas and condensate discoveries in Pakistan since 2000 and discovered over 400 million boe hydrocarbon reserves.
As the operating shareholder MOL is responsible for 89 mboepd gross production (as of Q1 2020) in the TAL block, one of the largest hydrocarbon producing blocks in the country, where MOL has 8.4% share.
MOL’s partners in the Joint Venture consortium are OGDCL, PPL, POL and GHPL. MOL Pakistan is the country’s second largest producer of LPG, crude oil and condensate. As the operator it currently addresses around 9% of the natural gas needs of Pakistan, 25 % of oil and condensate needs and 22% of LPG.
Dr. Berislav Gašo, MOL Group’s E&P EVP commented:
“I am delighted to announce that we have made another discovery in Pakistan. This new discovery has de-risked an exploration play in deeper reservoir in the TAL Block, leading to new upside opportunities. The Mamikhel South-1 discovery will also help to improve the energy security of the country from indigenous resources. We are thankful to our Joint Venture partners as well as the Government of Pakistan for their continued support.”
MOL aims to transform its E&P division into an international platform and the new discovery strengthens this ambition further. Currently, MOL Group has Upstream presence in 14 countries with production activities in 9 of them. Besides its core region, Central & Eastern Europe (Hungary and Croatia), MOL has a well-established presence and partnerships in the CIS region (Russia, Kazakhstan, Azerbaijan), the Middle East, Africa and Pakistan as well as the North Sea region (UK, Norway).
About MOL Group
MOL Group is an integrated, international oil and gas company, headquartered in Budapest, Hungary. It is active in over 40 countries with a dynamic international workforce of 25,000 people and a track record of more than 100 years in the industry. MOL’s exploration and production activities are supported by more than 75 years’ experience in the hydrocarbon field. At the moment, there are production activities in 9 countries and exploration assets in 14 countries. MOL Group operates three refineries and two petrochemicals plants under integrated supply chain management in Hungary, Slovakia and Croatia, and owns a network of about 1900 service stations across 10 countries in Central & South Eastern Europe.
Pumps perfected for first-of-a-kind plant to have the power to be its best
AdministratorPumps for circulating clean engine oil; a reasonably ordinary application? But then there’s nothing ordinary whatsoever about Arjun Infrastructures’ remarkable power plant in London, which generates 17MW of renewable energy from food waste and can also utilise fats, oils and greases (FOG).
”This is a first-of-a-kind plant”, said Phil Jones, Director at 2OC, who developed the plant and now manage it on behalf of Arjun.
He added: “Joining up assets that haven’t previously been linked together before has presented many engineering challenges”.
Originally specified by Jacobs Engineering, the two 90kW lubrication pumps for the Combined Heat and intelligent Power (CHiP) plant had to be installed by main contractor J. Murphy and Sons in a very tight space, presenting the first in a series of obstacles to be overcome.
David Brown, from the pump manufacturer Börger explained: “At first we thought that this was going to be a relatively uncomplicated job, but then the small footprint was just one of many hurdles to negotiate – not to mention the fact that the pumps had to go below ground, beneath the plant’s engine”.
He added: “We designed a special base frame so that the very robust EL1550 Classic pumps could be mounted vertically into the small footprint (just 3m by 4m) – and then for easy servicing, lifted out and put on their side. Over-pressure protection was required too. All a bit tricky, but often the case when there’s not much space available.“
Producing enough energy for approximately 40,000 homes, Arjun’s power station presents no shortage of high temperatures for its assets to cope with. This includes the Börger pumps, which had special cooling radiators for the gearboxes and motors installed.
So far so good, but with the Börger pumps and the rather demanding need to make all of the new power plant’s equipment work together efficiently and economically, came a demanding, non-extendable deadline.
“We were fully aware of this from day one”, continued 2OC’s Phil Jones, “but I can’t deny that the pressure was well and truly on. We had to meet the deadline for all-important government ROCs (Renewables Obligation Certificates) that support large-scale renewable electricity projects in the UK. To get the plant off on the right operational and financial footing, we had to make things happen to hit that deadline. We could not take our time”.
The construction contractors’ engineers were initially concerned about the noise and vibration of the two Börger pumps. As everyone in the supply chain knows, this can be a delicate balance when both parties believe they are right!
“The pumps were performing fine, but we were a little anxious at first”, added Phil Jones. “Failure wasn’t an option”.
“For us”, continued David Brown from Börger, “we believed it was simply down to natural pulsation, but as well going to site, we also brought over our top engineers from Germany. It didn’t help us or 2OC that due to the space limitations, the pipework for one pump was straight, whilst the other one was more complex, so had to cope with some pressure loss. Ultimately, we ran a test in Germany with 2OC in attendance to show that the pumps were performing fine. As it turned out, the vibration was down to nothing more than extra torque being required. Later, after another 500 hours running time, an inspection confirmed that there were no issues. It has been a bit of journey, but we always knew there was a reason, a solution.
2OC’s Phil Jones added: “Börger were totally professional – taking our concerns very seriously to get to the bottom of this mystery. Through the very positive dialogue between the two companies, it was also decided to change the pump’s removable rotor tips from rubber to a fully stainless-steel solid rotor design because of the high temperatures. Together with the stainless-steel pump-head, it now means that there is almost zero maintenance required”.
Built by J. Murphy and Sons, Arjun’s power plant sees 75GWh of the electricity sold to Thames Water for its Beckton sewerage processing plant (home to 64 Börger pumps), whilst the remaining 55GWh is purchased by Centrica.
Heat from the engine is supplied to the adjacent gas pressure reduction station owned by the Cadent (with whom Börger also has pumps in a very important application), largely replacing old gas boilers that used to pre-heat the gas – whilst heat recovery cycles of the CHiP technology increase the thermal efficiency of the Arjun plant.
Phil Jones from 2OC concluded: “Our pursuit of getting this unique power station where it needs to be has not been easy, but very much in line with what government is promoting, we now have a very neat and efficient plant. This includes the Börger pumps, which are proving very efficient, reliable and easy to maintain thus far”.
Mexico to remain highly dependent on natural gas imports from the US, says GlobalData
AdministratorEven during the current COVID-19 crisis of lower economic activity, natural gas imports from Mexico have remained at levels of around 5,300 mmcfd during the first quarter of 2020. The US is the primary exporter of natural gas to Mexico, with volumes reaching an all-time high in July 2019 with 6.2 bcfd. Mexico is expected to remain highly dependent on natural gas imports from the US in the future, says GlobalData, a leading data and analytics company.
Over the next decade, Mexico’s dependency on natural gas will continue to grow as the national oil company (NOC), Pemex, focuses on crude oil production and the US continues to have an excess in natural gas supply. Indeed, the price differentials between the US natural gas price and Mexico’s incentivize the trade. Furthermore, since the end of June 2020, Wahalajara’s pipeline system connecting Waha hub gas with the central-west part of Mexico is in full operation. This pipeline will encourage more export volume from Texas Permian to Mexico of up to 0.89 bcfd and the permanent demand from Mexico should continue supporting the already narrower differential of Waha hub prices with respect to other US natural gas hubs.
Adrian Lara, Senior Oil & Gas Analyst at GlobalData, comments: “In the short term, there are no planned assets in Mexico that can significantly increase domestic natural gas production. There is potential for undeveloped resources in the onshore region of Burgos on the north eastern part of the country, across the same geological basin continuing from southeast Texas. However, on average, the required breakeven price for full development of such reserves is higher than the price of imported natural gas challenging the viability of potential new projects.
“As for deepwater and unconventional resources for these type of developments, Pemex would have to partner with another operator to share risk and capital investment. Given the more technical and capital intensive nature of such projects, it has long been established this is a most effective manner for the NOC to exploit these resources. However, Mexico’s current government policy is to favor and support Pemex and this means stopping all bidding rounds that can bring new participants to the sector.
“The reality is that at present there are practically no new natural gas resources to be developed in Pemex’s portfolio that can reverse the decline in production. For that reason, imports from the US to satisfy an increasing demand for natural gas in power generation and industrial use will continue to be more than necessary over the current decade.”
About GlobalData
4,000 of the world’s largest companies, including over 70% of FTSE 100 and 60% of Fortune 100 companies, make more timely and better business decisions thanks to GlobalData’s unique data, expert analysis and innovative solutions, all in one platform. GlobalData’s mission is to help our clients decode the future to be more successful and innovative across a range of industries, including the healthcare, consumer, retail, financial, technology and professional services sectors.
New Hägglunds Service Website From Bosch Rexroth Provides Easy Access for Certified Repair Work
AdministratorOnline service portal helps users with factory-authorized maintenance and repair for Hägglunds hydraulic direct drive systems and motors, including legacy Marathon motors.
Bosch Rexroth has introduced a new online service portal for its Hägglunds hydraulic motors, giving users a single source of information to maintain, repair, modernize or upgrade their equipment with certified specialists and genuine Hägglunds parts. The service portal is accessible from www.boschrexroth-us.com/Hagglunds
With more than 60,000 motors installed globally, Hägglunds low-speed high-torque radial piston drive systems are used in a wide range of industries – from mining and pulp and paper production to recycling systems, marine applications and more.
The new Hägglunds Service Center website from Bosch Rexroth provides information to help users with servicing, repairing, modernizing or upgrading Hägglunds drive systems
“We developed this website to help customers maintain the highest productivity and reliability for their Hägglunds motors, whether they need original, warrantied spare parts or guidance from a certified specialist,” said Brian Howell, Hägglunds Sales and Operations Manager. “No one knows a Hägglunds motor or drive system better than the original equipment provider, and that’s us. When users choose authorized Hägglunds service from Bosch Rexroth, our certified technicians bring their drives and systems back to new performance levels, along with a full factory warranty.
“We know customers rely on Hägglunds motors and drives to last a long time, and we can help them accurately assess the condition and advise the repair necessary to continue a long-life and maintain uptime.”
The website makes it easy for Hägglunds customers to request a motor return via a simple form submission. They can also learn about upgrading motors and drive units with information on motor comparisons, upgrade kits, cooling improvements for drive units and scalable options to fit their needs. In addition, users can access repair and maintenance resources for legacy Hägglunds Marathon motors, which are no longer in production. In addition, the website provides information about:
- Direct support from certified Hägglunds technical experts for complete system component inspection and analysis
- On-site examinations by certified service specialists equipped for inspection, repair and preventive maintenance support
- Hägglunds-authorized repairs, carried out by skilled, factory-certified personnel at the customer location or at a Rexroth U.S. Hägglunds facility in Ohio or Texas
- Preventive maintenance program offering a full range of services, including written inspection reports, oil level and pressure checks and electrical element inspections
- Genuine Hägglunds spare parts, backed by extended warranty options and fast shipping from strategically located inventories
- Hands-on, in-depth training covering the major hydraulics, electronics and controls of Hӓgglunds large hydraulic drives; training is provided by factory-certified trainers and can be conducted at a customer location or at a Rexroth training facility
The online service center is the latest addition to the Bosch Rexroth portfolio of informative, free resources. The company also offers a free Hägglunds Resource Kit with information ranging from detailed customer case studies to online engineering tools.
Visit www.boschrexroth-us.com/Hagglunds for more information.
About Bosch Rexroth:
As one of the world’s leading suppliers of drive and control technologies, Bosch Rexroth ensures efficient, powerful and safe movement in machines and systems of any size. The company bundles global application experience in the market segments of Mobile Applications, Machinery Applications and Engineering, and Factory Automation. With its intelligent components, customized system solutions and services, Bosch Rexroth is creating the necessary environment for fully connected applications. Bosch Rexroth offers its customers hydraulics, electric drive and control technology, gear technology and linear motion and assembly technology, including software and interfaces to the Internet of Things. With locations in over 80 countries, roughly 31,000 associates generated sales revenue of roughly 6.2 billion euros ($7.3 billion) in 2019.
To learn more, please visit www.boschrexroth-us.com.
About Bosch:
The Bosch Group is a leading global supplier of technology and services. It employs roughly 400,000 associates worldwide (as of December 31, 2019). The company generated sales of 77.7 billion euros ($84 billion) in 2019. Its operations are divided into four business sectors: Mobility Solutions, Industrial Technology, Consumer Goods, and Energy and Building Technology. As a leading IoT provider, Bosch offers innovative solutions for smart homes, Industry 4.0, and connected mobility. Bosch is pursuing a vision of mobility that is sustainable, safe, and exciting. It uses its expertise in sensor technology, software, and services, as well as its own IoT cloud, to offer its customers connected, cross-domain solutions from a single source. The Bosch Group’s strategic objective is to facilitate connected living with products and solutions that either contain artificial intelligence (AI) or have been developed or manufactured with its help. Bosch improves quality of life worldwide with products and services that are innovative and spark enthusiasm. In short, Bosch creates technology that is “Invented for life.” The Bosch Group comprises Robert Bosch GmbH and its roughly 440 subsidiary and regional companies in 60 countries. Including sales and service partners, Bosch’s global manufacturing, engineering, and sales network covers nearly every country in the world. The basis for the company’s future growth is its innovative strength. Bosch employs some 72,600 associates in research and development at 126 locations across the globe, as well as roughly 30,000 software engineers.
Additional information is available online at www.bosch.com, www.iot.bosch.com, www.bosch-press.com, www.twitter.com/BoschPresse.