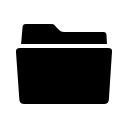
Uncategorised (4996)
Walki®Apron 45 has been certified and is now ready for delivery
AdministratorWalki’s high-performance protective material for single use hospital aprons, Walki®Apron 45, has achieved the highest class according to the standard based on the DIN EN 14126: 2004 norm.
The material is now ready to be delivered to customers, who will make the aprons needed in hospitals all over the world in the fight against COVID-19.
The Walki®Apron 45 was certified to resist penetration by contaminated liquids under pressure and infective agents due to mechanical contact with substances containing contaminated liquids.
The material was also tested and certified for resistance to contaminated aerosols and solid particles.
“This means that the Walki®Apron 45 meets all the necessary safety standards, and the material is safe to use in protective gear for hospital personnel”, says Bart Vansteenkiste, Business Development Manager Engineered Materials at Walki.
The Walki®Apron 45 is based on a high-performance extrusion coated non-woven fabric suitable for medical applications.
The material used in hospital aprons needs to be highly tear-resistant to hinder the material from suffering damages during the manufacturing process. As hospital personnel work long days in difficult conditions, it is also important that the apron is comfortable to wear.
“The softness in the Walki®Apron makes it pleasant to wear”, says Vansteenkiste.
The first batches have been delivered to customers already and the feedback from hospital staff has been very positive.
Walki Group is a leading manufacturer of technical laminates and protective packaging materials specialising in the production of fibre-based, intelligent multi-laminate products for markets as diverse as energy-saving facings and construction membranes to barrier packaging applications. The Group has production facilities in Finland, Germany, the Netherlands, Belgium, Poland, the UK, Russia and China. The Group has a workforce of around 1100 people. In 2018, the Group’s annual turnover was EUR 317 million.
KROHNE Remains in Full Production Shipping Critical Products within 48 hours
AdministratorKROHNE, a world-leading manufacturer and supplier of solutions in industrial process instrumentation, announces it continues to quickly ship full product line from its Beverly facility despite current global supply chain constrictions that have impacted numerous industrial process operations as a result of the global health pandemic.
“Magmeters, level radar and TDR and even Coriolis mass flow meters are assembled or produced in KROHNE’s new facility in Beverly, Massachusetts and we can ship several model configurations as quickly as 48 hours from date of order,” says Bob Senk, Vice President of Operations for KROHNE, Inc. “We are eager to be of service to our customers who need critical products in this time of crisis.”
Customers looking for flow or level measuring instruments should contact KROHNE or their local KROHNE representative for assistance during this challenging time.
About KROHNE
KROHNE is a worldwide technological leader in the development, manufacture and distribution of accurate, reliable and cost-effective measuring instruments for the process industries. KROHNE focuses on forming partnerships with its customers to provide them with the most reliable and innovative solutions available in the marketplace. For more information about KROHNE’s complete line of measuring instrumentation for the process industries, contact KROHNE at 1-800-FLOWING (978-535-6060 in MA); fax: (978) 535-1720, email: This email address is being protected from spambots. You need JavaScript enabled to view it.
Outotec received a grinding mill order from Kazakhstan’s largest gold miner RG Gold
AdministratorOutotec has signed a contract with Kazakhstan’s largest gold miner RG Gold for the delivery of two grinding mills for the Raygorodok gold mine in northern Kazakhstan. The contract price is not disclosed, but deliveries with similar scope are typically worth approximately EUR 10 million. The order has been booked in Outotec’s 2020 first quarter order intake.
Outotec’s delivery includes two ball mills with associated ancillaries and spare parts to the customer’s carbon-in-leach plant expansion project. The ball mills feature the newly released Outotec® Polymer Hydrostatic Shoe Bearing (HSB) system, which improves grinding mill availability and simplify maintenance. Deliveries are scheduled for 2021.
The Raygorodok gold deposit is one of the largest gold deposits in Kazakhstan with 6 million ounces of estimated reserves.
“We are committed to working closely with our customers to keep the mining industry moving even during these exceptional times," says Paul Sohlberg, head of Outotec’s Minerals Processing business.For further information please contact:
OUTOTEC
Paul Sohlberg, interim President - Minerals Processing business unit
tel. +1 289 983 0362
Outotec develops leading technologies and services for the sustainable use of Earth’s natural resources. Our 4,000 top experts are driven by each customer’s unique challenges across the world. Outotec's comprehensive offering creates the best value for our customers in the mining, metal, and chemical industries. Outotec shares are listed on NASDAQ Helsinki. www.outotec.com
~ Navigating bearing retainer design options~
In mathematics, Pascal’s triangle is an arrangement constructed by summing adjacent elements in preceding rows. It has applications in algebra, probability and is a useful model for calculating combinations — commonly referred to as “n choose k”. Here, Chris Johnson, managing director at specialist bearing supplier, SMB Bearings, explains how to navigate the seemingly endless choices in the bearing design process.
If a design engineer wanted to choose any four bearing components from a group of 20 design options, the possible number of combinations would be a whopping 4845. Suddenly, choice overload stunts any kind of decision-making process, when purchasing bearings.
An exploded view of a standard bearing clearly shows its main physical components: the closure, the inner and outer raceway, the balls and the optional retainer. But with four important physical design decisions to make and an increasing number of innovative possibilities, how do design engineers choose the best options for their application?
The best place to start is to consider the environment and specific conditions the bearing will be operating in. A bearing’s inner and outer raceway, balls, retainer and closures may be fabricated from different materials, yet must function effectively in unison. For example, a food and beverage grade bearing may have acetal resin (POM-C) rings, a nylon (PA66) retainer, balls made from 316 stainless steel or glass and a contact seal consisting of nitrile/BUNA-N rubber bonded to a metal washer. This combination would provide good contamination protection and corrosion resistance.
Are retainers necessary?
Often a crucial feature in bearing design, retainer options are often an afterthought when purchasing bearings. But they shouldn’t be. Retainers or cages perform a fundamental job. They are designed to keep the balls evenly spaced around the raceway and help retain grease around these elements.
They aren’t always required though. Bearings without a retainer have more balls and are called full complement bearings. This increased number of balls allows these bearings to withstand heavier loads and cope with impact or shock, as the load can be distributed more evenly around the raceway. However, full complement bearings experience additional friction and are generally not suitable for high speed applications or axial loads. Once the more popular design option, full complement bearings are now less common thanks to the advancements in steel technology.
Choosing your retainer
Metal retainers are the most common type and suit most applications. They can be manufactured from carbon steel or stainless steel and come in either a crown or ribbon form. A riveted steel ribbon retainer should be used for high vibration applications due to its greater strength. Crown metal cages are used primarily on smaller miniature bearings and thin-section bearings, where space is more limited. Whereas a crown type is guided by the inner ring, a ribbon type retainer is mainly ball guided.
Certain applications, such as MRI scanners, where non-magnetic properties are required, call for an entirely non-metal bearing with a non-metal retainer. While these may be more costly, non-metal retainers are often necessary and can increase a bearing’s lifespan in the long run.
Applications where retainer selection must be carefully considered are those involving temperature extremes. A nylon or polyethylene retainer will not cope with temperatures above 100-120°C. In applications that exceed these temperatures, the retainer will lose strength and lead to early bearing failure. A stainless-steel retainer can be used up to 300°C and will equally maintain its strength under -40°C as will PEEK and PTFE retainers. At extremely low temperatures, a nylon or polyethylene retainer will not perform well and will become brittle so 316 stainless steel and PTFE are favoured.
Similarly, a nylon or polyethylene retainer will be affected by certain chemicals and corrosive environments. These materials will cope better than stainless steel with some chemicals, but not as well with others, so this must be assessed on an individual basis. These synthetic retainers do however offer better resistance to water and salt water than stainless steel retainers, making them the best choice in marine environments.
Polyether ether ketone (PEEK) and polytetrafluorethylene (PTFE) retainers are often used in corrosion resistant bearings used in aggressive environments as these materials are highly corrosion resistant. This is an essential consideration for bearings in chemical or pharmaceutical environments.
Reinforced nylon retainers have good sliding characteristics and will cope better than metal retainers at very high speeds. They also produce fewer fluctuations in running torque and can increase maximum speeds by up to 60 per cent.
In many instances, retainer material choice will be led by the raceway material choice. To prevent non-useful friction, increased wear and premature equipment failure, it is important that the bearing retainer doesn’t have too much radial movement, so it needs to be guided by either the balls or one of the rings. Plastic bearings usually have nylon retainers and full ceramic bearings normally have PEEK retainers, PTFE retainers or have no retainer at all.
While having 4845 design options, may initially seem like an impossible number. By asking the right questions and considering your environmental conditions carefully, it quickly becomes manageable to eliminate unsuitable design combinations and deduce the best matches for each individual bearing design.
For further information on nylon, polyethylene, PEEK, PTFE or metal retainer design options, visit the technical area of the SMB Bearings’ website or contact a specialist: This email address is being protected from spambots. You need JavaScript enabled to view it..
About SMB Bearings: SMB Bearings originally specialised in miniature bearings, thin-section bearings and stainless steel bearings. By natural progression, the company expanded the range to include other corrosion resistant bearings such as plastic bearings, 316 stainless bearings and ceramic bearings.
Remaining a specialist business, SMB Bearings provide a high level of product knowledge, providing bearing and lubrication solutions to existing or potential customers, whether individuals or large corporations. SMB Bearings does not just sell bearings, but helps to solve your problems.
For further information please visit http://www.smbbearings.com/
VTT and 52 companies to cooperate to reduce need for plastics by using natural fibres
AdministratorMaterials based on natural fibres are an interesting alternative to replace fossil-derived plastics. In the future, they may replace plastics in, for example, packaging, hygiene products, building materials and textiles. The Piloting Alternatives for Plastics project brings together a wide range of Finnish and international companies to take materials developed in laboratories towards more industrial production. The project is funded by the European Regional Development Fund, VTT and companies.
Plastic is an excellent material with many unique properties in, for example, packaging applications. Plastic consumption is estimated to double over the next 20 years. The biggest challenge for plastic products is their recyclability. For example, only 14% of plastic packaging is recycled, so the majority of plastic ends up being incinerated or in landfills and, unfortunately, also improperly disposed of in forests and oceans (Ellen MacArthur Foundation, 2017).
In a three-year piloting project, VTT is working with companies to take the manufacture of new generation fibre products towards the scale of industrial production. The pilots are being carried out at VTT in Jyväskylä, with access to, among other things, the first research environment in the world to utilise the foam-forming process. The selected piloting targets include fibre-based materials to replace the plastics used in, for example, food packaging, filters, textiles as well as wiping, hygiene and construction materials.
VTT's foam forming research environment is situated in Jyväskylä. (Photo by VTT).
“In this project, we are creating a new understanding of bio-based fibre networks and how, by tailoring them, we can produce new types of recyclable materials that do not burden the environment”, says Vice President Jani Lehto from VTT.
From laboratory through piloting to the product development phase
In the research of new materials, the challenge is to select the most interesting from a wide range of raw material and manufacturing options, and to reduce the time it takes to scale the results obtained on a laboratory scale to commercial production scale. The development work done in the project will result in expertise in various raw materials, equipment and manufacturing technologies. Based on the development work, companies can move to the product development phase for different solutions in company-driven projects.
The Piloting Alternatives for Plastics project started on 1 April 2020 and ends on 31 March 2023. Its total budget is EUR 6.7 million. The project is implemented with funding from the European Regional Development Fund (ERDF), VTT and companies coordinated by the Regional Council of Central Finland.
Participants in the project include 52 companies from Finland and elsewhere in Europe. A total of 28 companies from Finland are involved, of which 18 are small and medium-sized companies.
Corporate project partners
Ahlstrom-Munksjö Glassfibre Oy, Andritz Küsters GmbH, Anpap Ltd, Berndorf Band GmbH, Betolar Ltd, BillerudKorsnäs AB, CH-Polymers Oy, CP Kelco Oy, DAIO Paper Corporation, Domtar Paper CO LLC, DS Smith Paper Limited (GBCE), Elomatic Consulting & Engineering Ltd, Epira Oy, Essity Hygiene & Health AB, Evergreen Packaging LLC, Fiber-X Finland Oy, Huhtamäki Oyj, Ibema Cia Brasileira de Papel, Kemira Oyj, Kimberly-Clark Corp., Kuraray Europe GmbH, Lenzing AG, MegaTrex Oy, Metsäliitto Cooperative, Moorim P&P Co. Ltd, Nalco Finland Oy, Neenah Gessner GmbH, OrganoClick AB, Pankakoski Mill Ltd, Paptic Ltd, Pixact Ltd, ProSolve Oy, P.T. Bukit Muria Jaya (BMT), PT. Riau Andalan Pulp and Paper – APRIL Group, Sappi Netherlands Services BV, Serres Oy, Solenis LLC, Sonoco-Alcore Oy, Spinnova Ltd, Stora Enso Oyj, Sulzer Pumps Finland Oy, Suominen Corporation, Södra Skogsägarna, Termex-Eriste Oy, TetraPak Packaging Solutions AB, Trinseo Europe GmbH, UPM-Kymmene Corporation, Valmet Technologies, Inc., Visuvari Oy, Vologda Pulp LLC, Weidmann Electrical Technology AG and Wetend Technologies Ltd.
Outokumpu’s Board of Directors has appointed Heikki Malinen, M.Sc. (Econ.), MBA (Harvard), as President and CEO of Outokumpu and the Chairman of the Leadership Team. He will join the company on May 1 and assume his role as the CEO on May 16, 2020. Heikki Malinen has previously worked as CEO in Posti Group Corporation and in Pöyry PLC. Prior to these, he has held various leadership positions in UPM in the USA and in Finland. Malinen has been a member of the Outokumpu Board of Directors since 2012, and due to his appointment, he will resign from the Board at the end of April.
Kari Jordan, Chairman of the Outokumpu Board of Directors: “Following an extensive international search process, Heikki Malinen singled out as the top candidate for the CEO position due to his previous CEO roles in demanding environments, as well as international experience in sales and process industry. His long Board membership in Outokumpu naturally is an additional advantage providing profound knowledge and understanding of Outokumpu’s business. I am confident that as the CEO Heikki will be a great asset to the company.”
“I am honored to get the opportunity to lead Outokumpu which is a global leader in the stainless steel industry. Thanks to the transformation that has been carried out during the past four years, the company is in a good shape with world-class assets and motivated, skilled employees,” says Heikki Malinen. “Being a Board member for eight years gives me a strong background for my new position – I know the company and the management, and I am looking forward to developing the company further and through this create value for our stakeholders.”
As announced earlier, Roeland Baan will leave his position as President and CEO of Outokumpu on May 15, 2020.
“On behalf of the entire Board of Directors, I would like to thank Roeland Baan for his contribution to Outokumpu’s improved operational and financial performance and I wish him all the best for the future,” says Kari Jordan.
Outokumpu is the global leader in stainless steel. We aim to be the best value creator in stainless steel through customer orientation and efficiency. The foundation of our business is our ability to tailor stainless steel into any form and for almost any purpose. Stainless steel is sustainable, durable and designed to last forever. Our customers use it to create civilization’s basic structures and its most famous landmarks as well as products for households and various industries. Outokumpu employs 10,000 professionals in more than 30 countries, with headquarters in Helsinki, Finland and shares listed in Nasdaq Helsinki. www.outokumpu.com
Small components play a large role in medical equipment
AdministratorSeveral of the companies within the Lesjöfors Group have many years of experience supplying the medical industry. We would like to introduce some examples of spring products specially manufactured for this industry of current interest.
Highly demanded medical components
European Springs & Pressings in the UK is one of the Lesjöfors companies with customers in the medical industry. Their medical range includes springs that go into the mouthpieces for ventilators, catheter clips to syringe drivers, patient beds and trolley systems, instrumentation and numerous electrical components for medical technologies including defibrillators. ESP manufacture the largest range of springs and pressings in the UK and have some of the most advanced high-volume machinery available. At peak, the machines can manufacture 5 million springs an hour and specific production lines have been repurposed and upscaled to manage orders.
Stuart McSheehy, Managing Director comments on the situation: “We have developed tooling and manufactured medical components for the healthcare sector for decades but today’s climate and subsequent increase in demand has highlighted the market share with which we and our customers operate in. Normally validation as a new supplier takes months of trials before volume production but in this very abnormal period we’ve been fast-tracking processes to suit our customers and are beyond proud to be able to play a supportive role in today’s climate.”
Other medical spring solutions
Below is a selection of other spring solutions for the medical industry signed Lesjöfors:
- Medical springs for implants and applications like pacemakers
- Improved needle protection for a catheter
- Customized wire form for garment lifting
- Springs in healthcare monitoring equipment that sends data from patients’ home
Cleanliness and hygiene
Our companies that supply components for the healthcare technology and medicine industries meet the highest demands of cleanliness in products and manufacturing environment. Since Lesjöfors has sales and production facilities in many countries worldwide, we can assure deliveries.
Contact us for medical requirements
We have well-established relationships with many med-tech companies which we regularly meet e.g. at exhibitions like Medtec Ireland. Nevertheless, we can assist many more customers within this field with customized solutions for springs, gas springs or pressings.
Lesjöfors is one of the leading spring suppliers with internationally well known customers. The products are demanded in many markets, in diverse industries. The assortment of springs, stampings and pressings has a unique range, where one of the largest selections of standard springs are combined with high-tech, customized solutions. Lesjöfors has both manufacturing and sales offices in several European countries, Asia, United States and Mexico.
China may buck trend of Covid-19 related delays in Asian oil & gas industry, says GlobalData
AdministratorWith coronavirus (Covid-19) being declared a global pandemic by the World Health Organisation (WHO) and the oil price war resulting from the OPEC+ disagreement, the oil and gas industry in Asia is facing an unprecedented uncertainty. Companies are being forced to rethink the ongoing project timelines and ‘projects in the pipeline’ for 2020. Projects expected to take final investment decision (FID) this year are at elevated risk of deferral, says GlobalData, a leading data and analytics company.
However, China is now in the recovery phase and its major national oil companies (NOCs) are set to focus on their domestic output growth goals.
Cao Chai, Oil and Gas Analyst at GlobalData, says: “Field developments in India have already been disrupted and more are likely to be at risk as the country is currently enduring a 21-day lockdown. The latest news that India reduced its domestic natural gas price to a record low of US$2.39 per mmBtu will further impact the country’s top gas producer ONGC.
“Elsewhere in the region, the construction at the Merakes field in Indonesia is disrupted due to a shortage of workers and challenge of logistic supply, operator ENI has declared force majeure on the project as a result of Covid-19.”
The projects in Asia targeting FID this year will inevitably face delays, as countries continue to struggle through the uncertainties. Large scale capital intensive projects, which are facing financial constraints or with existing uncertainties will be difficult to draw investment. Smaller-scale operators will require capital discipline to maintain ongoing operations and growth, therefore projects awaiting FID would likely be postponed too.
But China could be an exception. The country, which was the center of the Covid-19 outbreak earlier this year, will see the planned projects progress as the country recovers from the worst of the coronavirus, though minor delays may still occur. Domestic developments will be prioritized over international investment for China National Offshore Oil Corporation (CNOOC), after its recent capex review to trim the annual budget by 10-15%.
China Petroleum & Chemical Corporation (Sinopec) marginally cut its capex by 2.5%, which will come predominantly from its refining business and sales sector. To date, there are no confirmed budget cuts from China National Petroleum Corporation (CNPC); however, it has announced an adjustment of 2020 production and operational plans in accordance to market trends.
Chai Concludes: “While Chinese NOCs are focusing on raising domestic output and cutting overseas operations, elsewhere in Asia delays and disruptions are seen across the upstream sector in 2020. The projects under development are at risk of slowdowns and operational disruptions as countries have taken stricter measures to control the spread of Covid-19, a multi-year low in upstream project FIDs is also expected in the region.”
- Comments provided by Cao Chai, Oil and Gas Analyst at GlobalData
- This report was built using data and information sourced from proprietary databases, primary and secondary research, and in-house analysis conducted by GlobalData’s team of industry experts
About GlobalData
4,000 of the world’s largest companies, including over 70% of FTSE 100 and 60% of Fortune 100 companies, make more timely and better business decisions thanks to GlobalData’s unique data, expert analysis and innovative solutions, all in one platform. GlobalData’s mission is to help our clients decode the future to be more successful and innovative across a range of industries, including the healthcare, consumer, retail, technology, energy, financial and professional services sectors.
Walki has developed a high-performance protective material for single use hospital aprons amid the Covid-19 crisis
AdministratorThe demand for protective clothing has significantly increased in the last weeks in hospitals and other health care facilities due to the Covid-19 crisis. To fulfill this need, Walki has decided to act fast and develop a new material that meets the stringent quality demands.
“Walki is known for producing sustainable laminates for a broad range of applications from construction to packaging and thus possesses extensive material knowledge. Doctors, hospitals and other medical specialists have reached out to us, asking us to supply them with a protective apparel”, explains Bart Vansteenkiste, Business Development Manager Engineered materials at Walki.
The material for protective clothes in hospitals need to fulfill a broad range of requirements. It should be highly tear resistant to make sure the material is not torn apart in the manufacturing process. It also needs to be resistant to water and splash to protect the person who is wearing it. Another important feature is that it’s comfortable to wear. The material Walki has developed, called Walki®Apron 45, is a high-performance extrusion coated polypropylene non-woven suitable for medical applications.
“It meets all the requirements: it’s flexible and highly tear-resistant with good barrier properties against water”, explains Vansteenkiste.
Walki®Apron 45 has been produced on an industrial scale and has been tested at Walki premises with very positive results. As hospitals all over the world are grappling with supply shortage, it’s of utmost importance that the materials needed can be supplied promptly.
“Currently the Walki®Apron 45 is in the process of being certified and we expect to have the feedback within a week”, says Vansteenkiste.
For more information, please contact:
Silvia Hanzelova
Category Manager, Technical Products
e-mail: This email address is being protected from spambots. You need JavaScript enabled to view it.
tel. +32 475 689 098
Walki Group is a leading manufacturer of technical laminates and protective packaging materials specialising in the production of fibre-based, intelligent multi-laminate products for markets as diverse as energy-saving facings and construction membranes to barrier packaging applications. The Group has production facilities in Finland, Germany, the Netherlands, Belgium, Poland, the UK, Russia and China. The Group has a workforce of around 1100 people. In 2018, the Group’s annual turnover was EUR 317 million.
Russian oil and gas operators emerge on top despite the plummeting oil prices, says GlobalData
AdministratorFollowing the news that global oil prices plummeted to an 18-year low on March 18 as a result of the coronavirus-fueled demand shock and the supply shock led by Saudi Arabia cutting oil prices and boosting exports;
Anna Belova, Senior Oil & Gas Analyst at GlobalData, a leading data and analytics company, offers her view:
“As US and Saudi companies slash spending in response to plummeting oil prices, Russian oil and gas operators show no signs of slowing down.
“Shielded by devaluing currency and progressive taxes that automatically adjust to oil price, producers in Russia remain above the breakeven level even at crude prices below US$24 per barrel. This price represents a 66% drop from the year high on January 6; however, in Russia, the state absorbed the majority of losses with Mineral Extraction Tax (MET) and export duty decreasing by US$36 for every barrel of crude produced in the country.
“Russian operators further benefit from the rapid devaluation of the Ruble as oil prices decline. The country’s currency closely follows global oil prices. The current exchange rate to the US dollar also represents an 18-year low and this allows for costs in Russia to be significantly reduced when expressed in dollar terms.
“Since all oil services, contracts and labor costs are paid in Russian Rubles, the devaluation effectively represents a reduction in costs by 24% from the year peak. This enables Russian operators to bring combined capital and operating costs to well below US$10 per barrel, keeping them competitive throughout the Saudi-initiated price war and the coronavirus-induced global demand decline.”
About GlobalData
4,000 of the world’s largest companies, including over 70% of FTSE 100 and 60% of Fortune 100 companies, make timelier and better business decisions thanks to GlobalData’s unique data, expert analysis and innovative solutions, all in one platform. GlobalData’s mission is to help our clients decode the future to be more successful and innovative across a range of industries, including the healthcare, consumer, retail, financial, technology and professional services sectors.
More...
Industry’s First Ultrasonic Transducer with Metal 3D-Printed Mini-Horn Array Enhances Flow Meter Performance
AdministratorEmerson’s titanium-housed gas ultrasonic transducer delivers enhanced performance and long-term reliability in extreme wet, sour and corrosive chemical gas environments
Emerson has released the Daniel™ T-200, a titanium-housed transducer, for its gas ultrasonic flow meter product line, marking the first use of metal 3D printing to enhance the acoustic performance of ultrasonic flow meters in custody transfer applications. The T-200’s robust design provides increased reliability, uptime and safety while achieving the highest accuracy class attainable in gas measurement.
In an ultrasonic flow meter, transducers generate acoustic signals that are sent back and forth across the fluid stream. The difference in the transit times of these signals is used to determine the fluid flow velocity. Signal quality and strength are critical to measurement accuracy, which is paramount in custody transfer applications. An error of only 0.1% can equate to hundreds of thousands of euros annually in a large diameter high pressure pipeline.
Emerson’s titanium-housed gas ultrasonic transducer delivers enhanced performance and long-term reliability in extreme wet, sour and corrosive chemical gas environments.
“The T200’s mini-horn array could not be made without metal 3D printing technology, making it transformational to the sound quality and performance achievable through a titanium barrier,” said Kerry Groeschel, director of ultrasonic technology, Emerson. “Emerson is committed to developing innovative solutions that help our customers achieve safer, more efficient operations.”
The meter’s all-metal housing provides a barrier from corrosive hydrocarbon fluids and wet gas, thereby extending the life of transducer components and ensuring stable performance. This unique design allows the meter to be hydrotested with transducers in place, steam cleaned while in the operating line and blown down with no limits on the rate at which the meter can be depressurised.
The T-200 can also be safely extracted while the meter is under pressure without special high-pressure extraction tools, which reduces the possibility of greenhouse gas emissions during extraction. The capsule which contains the piezoelectric crystal used to produce ultrasonic sound waves is retractable as a single piece for simplicity and ease of use.
The new design is rated for a wide range of operating conditions, including pressures from 1 bar gauge (barg)/103 Kilopascal (kPa) to 255 barg/25,855 kPa and temperatures from -50 to 125 degrees Celsius.
For more information, go to www.Emerson.com/ultrasonicflowmeters.
About Emerson
Emerson (NYSE: EMR), headquartered in St. Louis, Missouri (USA), is a global technology and engineering company providing innovative solutions for customers in industrial, commercial and residential markets. Our Automation Solutions business helps process, hybrid and discrete manufacturers maximise production, protect personnel and the environment while optimising their energy and operating costs. Our Commercial & Residential Solutions business helps ensure human comfort and health, protect food quality and safety, advance energy efficiency and create sustainable infrastructure. For more information visit Emerson.com.
Reduction in gas flaring benefits producers and the environment, says GlobalData
AdministratorMore than 4.6 trillion cubic feet of natural gas were flared globally in 2019. The potential value of this flared gas could be as high as US$24bn, if priced at the European gas benchmark, says leading data and analytics company GlobalData.
Soorya Tejomoortula, Oil and Gas Analyst at GlobalData, comments: “Key countries in the world flared more than 3.5 trillion cubic feet of natural gas in 2019, which constituted more than US$9.5bn in foregone revenue - when priced at US Henry Hub gas prices - and over US$19bn when priced at UK NPB prices.”
The company’s report, ‘Gas Flaring Market Analysis 2020’, found that some of the major oil producing countries in the world such as Iraq, Iran, Russia, the US, Venezuela, Nigeria, Libya, Indonesia, Angola and Algeria were jointly responsible for over 80% of the associated gases flared globally in 2019. Recently, flaring in countries such as the US and Iraq has increased considerably due to a corresponding growth in crude oil production.
However, some of the major oil producing countries such as Nigeria have been able to decrease associated gas flaring in the past decade due to enforcement of government regulations, re-injection of associated gas and increasing utilization of associated gas.
Russia is also able to reduce flaring marginally despite growing crude oil production due to toughening regulatory measures. Also, companies such as SIBUR are actively using associated gas as a feedstock for their petrochemical operations, contributing an overall decline in flaring volumes.
Tejomoortula concludes: “Utilization of associated gas is one of the most effective means to reduce gas flaring and benefits both the upstream producers and the environment.
“Opportunities for use of associated gas include re-injection of gas into wells to enhance recovery of oil, using as a feedstock for petrochemical plants, and for power generation. Small-scale solutions for utilization include mini GTL (gas to liquids) plants, mini/small-scale liquefaction plants, and compressed natural gas (CNG) plants.”
Information based on GlobalData’s report: Gas Flaring Market Analysis 2020
Quotes provided by Soorya Tejomoortula, Oil and Gas Analyst at GlobalData
Information based on GlobalData’s report: Global Gas Flaring Market Analysis, 2020 – Over 12.5 Billion Cubic Feet of Associated Gas per Day Flared Globally Represent US$24 Billion in Forgone Revenue Annually
About GlobalData
4,000 of the world’s largest companies, including over 70% of FTSE 100 and 60% of Fortune 100 companies, make more timely and better business decisions thanks to GlobalData’s unique data, expert analysis and innovative solutions, all in one platform. GlobalData’s mission is to help our clients decode the future to be more successful and innovative across a range of industries, including the healthcare, consumer, retail, financial, technology and professional services sectors.
Hatching New Solutions for Boiler Corrosion: Cortec’s Brand New Boiler Egg™ Revolutionizes Boiler Startup!
AdministratorCortec® Corporation is proud to unveil its new Boiler Egg™, an exciting companion to an innovative line of water treatment “animals” for corrosion protection of industrial water systems. These water treatment animals reduce the risk of extra downtime, clogging, leakage, and shortened service life that comes from corrosion. They are also some of the easiest and safest treatments to use on the market!
Cortec’s Boiler Egg™ is designed to scavenge oxygen and passivate metal during the initial filling of makeup water after seasonal or long-term dry layup of boilers. The Boiler Egg™ comes in an easy-to-handle pouch that is readily dissolved upon water contact, releasing the active ingredients as the boiler is being filled. It protects against the threat of oxygen pitting during the critical startup phase of a boiler when the makeup water is normally not pre-heated and the operating chemical program has not yet been implemented.
The Boiler Egg™ can be used in conjunction with the Boiler Lizard® as a complete preservation kit for dry layup of boilers, or it can be used on its own for applications where oxygen-scavenging and metal passivation are needed during the equipment startup phase. Special features of the Boiler Egg™ include that it is
- Readily water soluble
- pH neutral
- Non-hazardous by OSHA Standard (OSHA 29 CFT 1910.1200)
- Biodegradable
Bringing a boiler back online is a critical time for corrosion protection because of the higher threat from oxygen-rich makeup water flooding the system. The innovative Boiler Egg™ makes the solution simple and easy by releasing a powerful dose of oxygen scavengers when and where they are needed most. In addition to protecting the main boiler area, the Boiler Egg™ provides corrosion protection in other components—such as condensate, deaerator, and feedwater tanks—during initial startup.
The choice of adding Boiler Egg™ either at the beginning of layup or first thing when returning the boiler to service offers extreme flexibility with convenient application. No product or inner bag removal is required prior to boiler startup after the Boiler Egg™ has been removed from its outer bag and laid in the boiler at the lowest point possible. When the boiler is put back into service, personnel should simply fill the boiler with water and employ the common startup procedure. The PVA bag will dissolve as the boiler is filled, releasing the contents of the Boiler Egg™ and incorporating them into the makeup water. One Boiler Egg™ is designed to treat 1,000 gallons (3,800 L) of makeup water during the refilling process.
Learn more about the exciting new Boiler Egg™ solution for boiler startup here: https://www.cortecvci.com/wp-content/uploads/Boiler_Egg_NEW.pdf
Learn more about Cortec’s corrosion solutions for boilers here:https://www.cortecwatertreatment.com/products/boilers/
Cortec® Corporation is the global leader in innovative, environmentally responsible VpCI® and MCI® corrosion control technologies for Packaging, Metalworking, Construction, Electronics, Water Treatment, Oil & Gas, and other industries. Our relentless dedication to sustainability, quality, service, and support is unmatched in the industry. Headquartered in St. Paul, Minnesota, Cortec® manufactures over 400 products distributed worldwide. ISO 9001, ISO 14001:2004, & ISO 17025 Certified. Cortec Website: http://www.cortecvci.com
Poland Quadruples Solar Energy Output, Becomes 5th Largest Producer in Europe
AdministratorThe European Union increased its solar energy market by more than 100% making 2019 the most successful year so far. Being one of the five countries contributing to this growth the most, Poland has almost quadrupled its solar capacities in one year to reach 784MW. The leading solar developer in the region, Sun Investment Group, credits the self-consumption model and government efforts for unprecedented growth.
Last year was the most fortunate year for the European Union in the solar energy sector. In 2019, the EU added 16.7 GW solar energy installations to its portfolio, increasing the number by 104% since 2018. The sharp rise marked the biggest growth in solar energy generation since 2010. So far, five member countries have contributed the most, including Spain (4.7 GW), Germany (4 GW), the Netherlands (2.5 GW), France (1.1 GW), and Poland (784 MW).
Although the other 18 member states are lagging behind to meet the EU’s energy plans, the majority of the members are contributing to the progress, including a significant Poland’s achievement. The country quadrupled its solar power installations from 203 MW connected to the grid in 2018 to 784 MW in 2019. In 2020, Poland is planning to almost double its installations to 1.3 GW. These changes are important for the EU and Poland, as the country is the biggest coal producer in the Union.
Previously, the country has been struggling to meet the Union’s renewable energy plans, but in 2019, Poland had a sharp rise in solar energy generation. Although the biggest renewable source is wind power, Poland is turning its focus on expanding the solar energy sector.
With many new projects on the way in Poland, Sun Investment Group - the leading solar plant developer in Central Europe - shares their take on it. The organization has been working with the Polish market for years, and they have already developed 109 MW solar power capacity in the country. And with the rapid increase in the solar energy market, the organization is expanding further. They have 500+ MW of projects under the advanced development stage in different regions around.
Deividas Varabauskas, CEO and managing partner at Sun Investment Group, comments on aspects contributing to the transition to renewables and the sector’s further growth. “We are excited that Poland is now turning to be one of the fastest-growing solar power producers in the European Union. We believe that the progress was only possible due to source-specific auctions organized by the state (for PV projects of less than 1MWp), which will soon be boosted even further by big PV projects that will replace wind projects in technology-neutral auctions as there are very few new wind projects that comply with new regulations. This is a win-win approach, as current price bids are very close to the market price, giving a predictable revenue for 15 years to the PV generator and very soon an additional revenue for the Polish state treasury.”
Mr Varabauskas adds that the transition to solar energy will benefit not only air quality and environment but also the Polish state treasury and energy system. “Due to the rising CO2 certificate prices, the state will soon start generating income from the difference between auction price awarded to the generator and a market price of electricity, that in a few years will become higher than auction price awarded to PV (photovoltaics) generators. The impact of CO2 European Emission Allowances price increases will severely affect power prices in Poland, as coal is the most CO2 intensive source of energy, and Poland is mostly dependent on coal for its power and heat generation. Obviously, this is an enormous motivation for Poland to transition from coal to renewables as soon as possible, however, it will still take a very significant time to fully transform its energy infrastructure, which means PV is going to help save money to Poland and its citizens and businesses.”
According to Mr Varabauskas, these changes would be impossible without the country’s government’s significant dedication to establishing the solar power production market in Poland. It is also very important that auction system is prolonged beyond 2021 to ensure the uninterrupted investments in new PV projects, as relying on purely market solutions is just wishful thinking, especially in the current economic recession environment. “Although the solar energy market in Poland is in its early stage, the 2019 Global Infrastructure Index ranked the country as one of the top markets for clean energy production, which makes it very attractive to investments in solar energy and renewables.”
The European Union is growing its renewable energy market and breaking new records each year. The progress would be impossible without countries like Poland joining the train and expediting the transition. With many new projects on the way, the EU can expect even more prominent growth.
ABOUT SUN INVESTMENT GROUP
Sun Investment Group (SIG) was founded in 2011 as an investment management and development company focused on solar energy assets within investment-grade markets. It has extensive experience in developing solar power projects across Central Europe and the Baltic region. SIG has a track record of 158 separate projects delivering a total of 131 MW capacity. 500+ MW of projects are currently under the advanced development phase.
For more information, visit www.suninvestmentgroup.com