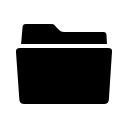
Uncategorised (4996)
OnRobot Expands Product Capabilities, Empowering Customers to Use Tools in Ever-Broadening Applications
AdministratorOnRobot showcases its commitment to continuous and rapid product enhancement with the launch of a software update for the popular ‘Eyes’ robot vision system. The update is part of a broad application-focused strategy to give OnRobot customers ongoing enhancements across its product portfolio.
Traditional single-purpose industrial robots are losing ground to affordable, easy to use robots and peripherals that can be flexibly redeployed for a wide range of applications. This empowers manufacturers to gain even greater productivity increases from their automation investments. OnRobot is extending its commitment to ongoing customer empowerment with the launch of a software update for its popular, 2.5D camera-based Eyes vision system.
“Traditional approaches to industrial automation place the product at the centre, which results in costly, over-complicated solutions to simple automation problems,” says Enrico Krog Iversen, CEO at OnRobot. “OnRobot takes a more practical, application-centred approach. This means providing our customers with easy-to-use tools tailored to specific application needs. But it also means empowering customers through updates to existing products that enable deployments in new application domains.”
The new features, which enable Eyes to be deployed in quality inspection applications and on mobile setups, include one-shot detection for multiple objects, colour and blob detection and automatic landmark calibration tools designed to speed cycle time for mobile robot setups.
“OnRobot prides itself on having meaningful conversations with customers and on having the agility to respond to those conversations quickly through new releases and product updates,” says Iversen. “Our customers told us that they love Eyes' ease of use, but that they would like to see new features tailored to common quality inspection tasks. Today’s Eyes update delivers that functionality.”
New visual inspection features for reduced cycle time and fast ROI
Eyes' new inspection features enable the system to easily sort, inspect, or pick & place unstructured objects using colour and contour detection – a capability that is beyond most competing vision systems. This detection method requires no workpiece teaching and finds items based on colour and size information input by the operator. Eyes' inspection features can be used to inspect parts removed from CNC machines, for example, or to check IMM parts for excessive or inadequate material after part has been moulded. The tools also support manual inspections: operators can set up a camera and inspection program, manually place a workpiece in view and execute inspection. No robot required.
The update also provides users with one-shot detection for multiple objects, allowing the system to pick all workpieces with only one picture. This reduces complexity for users and improves cycle times. The update includes tools that allow users to request specific workpiece types and specify gripper clearance parameters.
Adding Eyes to mobile robots
A new Landmark feature has been added to Eyes' powerful toolkit, enabling easy deployment of Eyes on mobile robots and setups with carts, trays, and pallets. The Landmark feature makes it simple to program mobile robots to move from station to station using end user-defined Landmarks as their guide. Landmarks can also be used to initiate specific robot operations: for example, when Eyes detects the arrival of a mobile cart in its workspace loaded with parts for picking, it can easily switch to pick & place routines.
“More and more manufacturers are looking to deploy robot arms on mobile platforms for various factory and warehouse applications. Today’s update gives our customers the ability to put ‘Eyes’ on mobile robots and does so without sacrificing the ease of use that makes our products such a compelling proposition for manufacturers of all sizes,” says Iversen.
Regulators Release Draft Environmental Impact Statement on Stibnite Gold Project
AdministratorMidas Gold Corp. has just announced that the U.S. Forest Service’s (“USFS”) had released the Draft Environmental Impact Statement (“DEIS”) on the Stibnite Gold Project (“Project”) for public comment. Individuals will have 60 days to comment on the proposed redevelopment and restoration of the former Stibnite gold, silver, antimony and tungsten mine, which is located in Valley County, Idaho. The comment period is legally required to be 45 days and the USFS has decided to grant a 15-day extension. In addition to producing gold and silver, the Stibnite Gold Project would produce the only domestically mined source of the critical mineral antimony in the United States, invest approximately $1 billion in construction, provide approximately 500 direct, family wage jobs for Idahoans as well as numerous indirect jobs in the supply, services and contracting sectors, address numerous legacy mining issues affecting the environment and reconnect migrating salmon to their native spawning grounds for the first time in more than 80 years.
“We are one step closer to recognizing the full benefits of the Stibnite Gold Project,” said Stephen Quin, CEO of Midas Gold Corp. “Our company has worked hard for the last decade to design and permit a mining project that could redevelop and restore an abandoned brownfields site and have a positive economic impact on the local community and Idaho in general. We have carefully developed an approach to use the proceeds of mining to restore fish passage and habitat, address numerous legacy environmental impacts and improve water quality in the region. If permitted, we will bring hundreds of well-paying jobs to rural Idaho and invest hundreds of millions of dollars in the state. We encourage community members to write to regulators and let them know why they support the Stibnite Gold Project, if they want to see all of this happen.”
Midas Gold designed the Stibnite Gold Project to integrate responsible, modern mining with the restoration of legacy and new disturbances. At first glance of the extensive DEIS released today, readers should note that the Executive Summary prepared by the U.S. Forest Service only summarizes the impacts of proposed mining. The reader should look to the rest of the document and Appendix D to see the holistic impact analysis with the voluntary and required mitigation proposed for the various resources incorporated.
The project has strong support in Idaho, with more than 1,000 people signed up as members of the Support Stibnite Coalition, most of them Idaho residents.
“I have lived in Idaho since I was 17,” said Willie Sullivan, co-chair of the Support Stibnite Coalition. “I have memories of the old mining operations up at Stibnite, having roamed there as a child, and I have fond memories of hunting and fishing in the area as a child. If you’ve been to the site, you know it is a mess and needs to be cleaned up. I support Midas Gold’s plans to use modern mining to restore the site because I want my grandchildren to see this area cleaned up. Plus, the project will be a boon for our economy and provide jobs to many families in our region.”
Individuals who wish to view the document or comment on the Project can visit www.RestoreTheSite.com. Additional information about the Project and Midas Gold’s plans for site restoration, redevelopment of mining operations, reconnecting salmon to their spawning grounds, protecting the environment, jobs, and producing the critical mineral antimony, can be found at www.midasgoldidaho.com/news/deis-released/. Comments on the DEIS are due by October 13, 2020.
Comprehensive Review of the Stibnite Gold Project
Midas Gold has been studying the Stibnite Gold Project for the past decade. During this time, the company has worked closely with regulators to provide all of the information they needed to conduct a comprehensive review of the project. Under the National Environmental Protection Act (“NEPA”), regulators need to ensure they meet the regulatory requirements to support a robust and defensible Record of Decision.
Midas Gold has delivered more than 80 reports totaling 27,522 pages of scientific data and analysis to the 11 federal, state and local agencies reviewing the Project. These documents included baseline studies, technical reports, scientific modeling data and other supporting information. During the review process, regulators made 114 requests for additional information (“RFAI”) and 22 additional requests for clarifications (“RFC”) in order to evaluate the thoroughness of the environmental impact analysis. Midas Gold responded to all of these requests with additional data and analysis to aid regulators in their careful consideration of the proposed plan and various alternative development scenarios.
About Midas Gold and the Stibnite Gold Project
Midas Gold Corp., through its wholly owned subsidiaries, is focused on the exploration and, if warranted, site restoration and redevelopment of gold-antimony-silver deposits in the Stibnite-Yellow Pine district of central Idaho that are encompassed by the Stibnite Gold Project.
Automated monitoring of cleaning, sharpening and maintenance cycles on the fresh food counter, centralized data and an intelligent, networked service concept: for slicing, SmarterSlicing solutions from Bizerba open up unforeseen potentials.
The retail industry is marked by ever increasing chains which also has an impact on fresh food counters. The new challenges: high throughput, many different operators, complex technical solutions and increased customer demands. SmarterSlicing provides companies more support, efficiency and transparency. This approach combines optimized operator, management and service support.
At the fresh food counter, indicators for cleaning, sharpening and maintenance inform the team about intervals due. This ensures hygiene, efficiency and impeccable results allowing the team to fully concentrate on shoppers. With unique error codes, malfunctions can be quickly eliminated.
For central inventory and logging, the slicers are connected with the management. The networking also allows an overview across stores of all slicers with status and utilization. This transparency forms a solid foundation for process optimizations and need-based, planned investments.
The service support includes, for example, automated monitoring of maintenance intervals for trouble-free operation. Service visits can be much more efficient through previous data exchange. And, announced already now: with package backup, update & restore via RetailControl, SmarterSlicing will very soon allow to restore lost data remotely across all stores. Intelligent support minimizes downtimes, maximizes the service life of the slicers and allows efficient planning of maintenance tasks.
Common Bizerba slicers for various demands in the retail area are already today available with SmarterSlicing: Models VSP, GSP and VSI. The manual slicers VSP and GSP combine superior design with a high-end performance package including SmarterSlicing; available either as a vertical slicer or a gravity feed slicer. The fully automatic vertical slicer VSI is suitable for both, the retail sector and for industrial use.
Further information can be found here.
BIZERBA SE& CO.KG
Since 1866 Bizerba has made a significant contribution to the developments in the area of weighing technology and today is represented in 120 countries. The customer base includes globally operating companies in trade and industry as well as retailers, bakeries and butcheries. With 4,100 employees worldwide and with its headquarters in Balingen, Germany, Bizerba has been in the same family for five generations. Additional production facilities are located in Germany, Austria, Switzerland, Italy, France, Spain, China, Canada and USA. Bizerba also has a global network of sales and service locations.
DSM introduces glass-filled polypropylene granules optimized for easy 3D printing of structural and demanding applications
Administrator
Royal DSM, a global science-based company in Nutrition, Health and Sustainable Living, have just announced a new glass-filled polypropylene (PP) pellet material which has been developed especially for 3D printing, enabling easy and consistent production of structural and demanding applications using fused granulate fabrication technology. Widely used for its mechanical, thermal and chemical performance, polypropylene (PP) is the second most frequently used polymer worldwide. Automotive, industrial or infrastructure manufacturers looking to adopt additive manufacturing technology for low volume or decentralized production - where the elimination of tools helps decrease cost - desire to use the same material they are familiar with from traditional manufacturing. To meet this growing need, DSM is introducing a glass-filled PP for fused granulate fabrication (FGF), suitable for additive manufacturing. Arnilene® AM6001 GF (G) - the (G) stands for granulates – stems from the same base material used in high volume production and is optimized for FGF 3D printing. By combining materials knowhow, expertise in modeling and simulation, design for additive (vs traditional manufacturing) and printing expertise, DSM secured all of the desirable mechanical, thermal and chemical performance of glass filled PP with the flexibility of a proven 3D process.
The new Arnilene® AM6001 GF (G) is ideally suited for direct printing of structural, lightweight applications for automotive, infrastructure and water management, as well as tooling. DSM Additive Manufacturing experts worked with equipment partners to validate the material on closed and open chamber build printers to optimize the material for FGF printing. The material’s low carbon footprint, due to reduced energy consumption, and its low LCA (Life Cycle Assessment), inherent to the PP’s chemistry, make it a sustainable solution. Geoff Gardner, Innovations director Additive Manufacturing at DSM, commented: “Availability of engineering-grade materials with the right property set is the next step in the additive manufacturing revolution. Developed by our experts, Arnilene® AM6001 GF (G) offers industrial customers an industry standard material with robust mechanical, thermal and chemical performance in an additive manufacturing format. By using a material they already have experience with, they can fully focus on 3D printing and its benefits for their business.” |
Marathon Oil to drive break-even prices as low as $30/bbl in Bakken and Eagle Ford by reducing well costs by 10% in H2, says GlobalData
AdministratorFollowing the release of Marathon Oil’s Q2 results;
Andrew Folse, Oil & Gas Analyst at GlobalData, a leading data and analytics company, offers his view on the current events:
“Marathon Oil’s net loss of US$750m in Q2 2020 was well anticipated due to the drop in oil prices and the current economic crisis that impacted domestic demand. However, despite the average realized price for US crude oil and condensate falling to US$ 21.65 per barrel - representing a 63% decrease from a year prior - the company upholds an optimistic outlook and is expected to be able to improve cost efficiency by reducing well costs and maintaining well productivity.
“Marathon Oil’s Bakken acreage is the company’s most promising, with high productivity and low well cost. If Marathon Oil is able to drive well costs below US$450 per lateral foot, and maintain oil productivity above 30 days initial production (IP-30) of 1,500 barrel of oil per day (bopd), the company will very likely be able to average a breakeven oil prices well below US$30/bbl in Bakken.
“As for its Eagle Ford acreage, if Marathon Oil is able to drive well costs below US$750 per lateral foot - while maintaining oil productivity above IP-30 of 970bopd - the company will be able to average a breakeven price below US$35/bbl.
“With a competitive breakeven oil price, Marathon Oil is confident in taking on an unhedged risk going into 2021 to maximise on potential gains if commodity prices were to recover from the current level. However, this poses a huge threat to the company as the economic crisis is yet to be over and industry volatility persists. However, Marathon Oil is backed by a strong liquidity profile, with a US$522m cash balance in Q2 2020 and US$3bn in its undrawn credit facility. The company has US$5.5bn in long-term debt value with US$1bn maturing in the second half of 2022.”
Graphene and related materials inks improve solar cells
AdministratorImagine the environmental benefits if we could all simply paint solar cells onto the roof of our houses, or onto any surface for that matter. We could do this using perovskite solar cells (PSC), but, due to their instability, they have not yet been widely introduced. Now, researchers from the Graphene Flagship have developed hybrids of graphene and molybdenum disulphide quantum dots to stabilise PSCs.
Progress in PSCs means that they are primed to become an affordable and flexible solar cell option for smart, low-intensity applications. This is because PSCs are less complex to produce, are made with cheaper materials and, due to their flexibility, can be used in locations where traditional silicon solar cells cannot be placed.
A collaboration between the Flagship Partners Istituto Italiano di Technologia, University of Rome Tor Vergata, and BeDimensional resulted in a novel approach based on graphene and related materials to stabilize PSCs.
PSCs are improving fast. When they were first developed in 2009, they had an initial efficiency of 3.8%. Today, they can achieve efficiencies above 22%. In comparison, silicon solar cells have been around since 1880, only reaching efficiency levels of 26.1% in 2018.
The main weakness of PSCs is their stability. This is where the molybdenum disulphide quantum dot/graphene hybrids come into play. The collaboration between research institutions and industrial partners enabled by Graphene Flagship, yielded a GRM based ink. Layering this over the PSCs saw them drastically increase the stability.
Graphene was central, as molybdenum disulphide was anchored to reduced graphene oxide. This allowed for both materials’ properties to be applied and the ink not only increased the stability but also the performance of the PSC.
“The Graphene Flagship was central to this development,” explained Professor Emanuel Kymakis, work package deputy leader for energy generation. “The funding and structure that they put in place were key to allowing new research teams to take part, such as the University of Rome Tor Vergata.
“Thanks to this research, we have overcome a major hurdle to adopting this new technology,” continued Professor Kymakis. “With the new levels of stability and performance, we could see the mass adoption of PSCs in the next few years.”
Once the PSCs stability is solved, attention can focus on scaling up production. Manufacturing PSCs requires solution processing, that can be ramped up to an industrial scale. Due to the flexibility, PSCs can be applied to nearly any surface and produce electricity.
Stable PSCs could change the way we power our homes and devices, as every available surface could be made to generate electricity.
Andrea C. Ferrari, Science and Technology Officer of the Graphene Flagship and Chair of its Management Panel added: "the potential of graphene and related materials to improve solar cells has been recognized since the beginning of the Flagship. Their combination with the emerging field of perovskite solar cells now allows a crucial step forward in stability. This validates the major investments in spearhead projects on solar cells done by the Flagship.”
Reference:
Graphene-Induced Improvements of Perovskite Solar Cell Stability: Effects on Hot-Carriers
P. O’Keeffe, D. Catone, A. Paladini, F. Toschi, S. Turchini, L. Avaldi, F. Martelli, A. Agresti, S. Pescetelli, A. E. Del Rio Castillo, F. Bonaccorso, and A. Di Carlo
Nano Letters 2019 19 (2), 684-691
DOI: 10.1021/acs.nanolett.8b03685
About: The Graphene Flagship
The Graphene Flagship is one of the largest research projects funded by the European Commission. With a budget of €1 billion over 10 years, it represents a new form of joint, coordinated research, forming Europe's biggest ever research initiative. The Flagship is tasked with bringing together academic and industrial researchers to take graphene from academic laboratories into European society, thus generating economic growth, new jobs and new opportunities.
Meldrum Ltd will rebrand as Actemium Carlisle on the 30th September 2020 and join the wider Actemium network of Business Units in its mission to boost industrial performance.
Established in 2005, Meldrum provides electrical and instrumentation engineering services, predominantly within the industrial sector. It partners with companies working at the forefront of the UK’s nuclear sector to provide services including electrical installation, safety and security enhancement, testing, automation services and maintenance.
Since the acquisition of Carlisle-based Meldrum Ltd by VINCI Energies UK & RoI in April 2017, the electrical and instrumentation engineering specialist has been working closely with Actemium, the VINCI Energies brand dedicated to industry, to enhance the company’s offering in the nuclear sector.
The rebrand of Meldrum Ltd to Actemium Carlisle is the direct result of this successful and close relationship with the wider network of Actemium Business Units and demonstrates its clear ambitions for growth.
Actemium is a global network of over 400 specialist Business Units, assisting customers in the transformation to a smarter industry through the design, build and maintenance of industrial processes and sites.
It has a strong presence in the UK with sites in Birmingham, Coventry, Nottingham, Gloucester, Teesside and Walsall, and the combined expertise of this network will support Actemium Carlisle in the next stage of its development.
Actemium Carlisle Business Unit General Manager Martin Hand added: “We are delighted and excited to announce this next phase of our company’s development. Joining Actemium will enhance our capabilities and offering to our customers, by enabling us to draw on the technical know-how and experience of a vast network of international engineers.”
Actemium UK Director Andrew Hunter commented: “By joining the wider Actemium network, Meldrum Ltd is not only enhancing its capabilities and expertise, it is joining a family. In joining this family, it will make collaborating with other Actemium Business Units and connecting with UK and International customers much easier.”
HARTING UK awarded prestigious IRIS Silver Quality Performance Level
AdministratorHARTING UK are delighted to announce that they have been awarded the prestigious Silver Quality Performance Level award from the International Railway Industry Standard (IRIS). This is a globally recognised standard which evaluates management systems for the railway sector.
Silver Performance is currently the highest performance level issued by IRIS and is a significant achievement for HARTING UK, making them one of only 60 companies worldwide to receive Silver status and putting them in the top 3% globally of all IRIS certified companies.
IRIS is established as a European Rail Industry Association (UNIFE) group and is recognised by both system manufacturers and railway operators. It was set up with the aim of establishing higher quality and reliability of rolling stock and infrastructure in the railway industry. Via an efficient system for auditing railway suppliers, the aim is to create transparency throughout the supply chain.
HARTING UK manufactures bespoke cable assemblies and intercar jumpers for the rail market.
Stuart Fisher, Director of Operations at HARTING Manufacturing UK Ltd, was delighted with the award, saying:
“To receive such a prestigious award is great testimony to everybody at HARTING and really endorses our commitment to quality. It also clearly demonstrates our passion for quality throughout the business and offers our customers great confidence in our products. It's also clear that as a business we have a culture of continuous improvement and that we will strive to get even better at what we do.”
The HARTING UK manufacturing facility in Northampton produces bespoke cable assemblies and intercar jumpers for the rail market, based on the extensive HARTING product portfolio. Additional services include full design and development support and onsite testing of cabling and wiring. As well as the IRIS Silver Quality Award, the facility also holds ISO 9001 certification for Quality Management, the ISO 14001 Environmental Standard and UL certification for Wiring Harnesses ZPFW2 / ZPFW8.
To learn more about HARTING UK’s manufacturing capabilities, please visit www.harting.com/UK/en-gb/solutions/harting-customised-solutions-uk
About HARTING:
The HARTING Technology Group is one of the world's leading providers of industrial connection technology for the three lifelines of Data, Signal and Power and has 14 production plants and 44 sales companies. Moreover, the company also produces retail checkout systems, electromagnetic actuators for automotive and industrial series use, charging equipment for electric vehicles, as well as hardware and software for customers and applications in automation technology, mechanical and plant engineering, robotics and transportation engineering. In the 2017/18 business year, some 5,000 employees generated sales of EUR 762 million.
For further information visit https://www.harting.com/UK/en-gb
Metso Outotec to bring unique fasteners and wear monitoring technology to its minerals customers by acquiring Davies Wear Plate Systems in Australia
AdministratorMetso Outotec has closed today the acquisition of the Australia-based fastener and wear monitoring technology provider Davies Wear Plate Systems, extending its wear lining portfolio and capabilities.
The acquired technology includes fasteners with a unique locking mechanism that does not require traditional studs and nuts and thus enables faster and safer maintenance work. Davies Wear Plate Systems’ portfolio also includes wear monitoring technology, which provides a real-time forecast of wear and expected liner change-out timing. The monitoring solution can be fitted to any metallic or ceramic liner, independent of attachment systems.
“This acquisition supports our target to offer comprehensive and unique solutions for the entire wear lining value chain. We are eager to introduce these advanced solutions globally to our customers; we now have the market’s widest range of optimized wear protection solutions, tools and services. The new technology will increase safety during maintenance and increase uptime. I warmly welcome the new colleagues to become part of the Metso Outotec team,” says Sami Takaluoma, President of Consumables business area at Metso Outotec.
WearSense™ monitors wear in real time and tells when it is time to change the liners
The acquired technology is already used by major mining companies, such as Rio Tinto, BHP Group and Fortescue Metals Group in Australia.
“We have been improving our product offering for years and we have received good feedback from our customers in Australia. Our products are ready to be rolled out to the global mining market. We are excited that we are now a part of a truly international company,” says Brian Davies, Founder, Davies Wear Plate Systems.
The parties have agreed not to disclose the value of the transaction.
About Davies Wear Plate Systems
The Davies Wear Plate Systems offering includes patented fastening systems, wear liner monitoring system and wear plates. Davies also supplies tools that provide safer and faster change-outs.
The company’s sales in fiscal year 2020 were AUD ~ 17 million (EUR 10 million) and it has approx. 30 employees. Davies has an office in Malaga, Perth and an operation facility in Esperance, Western Australia. https://www.davieswps.com/
Metso Outotec offers a wide range of optimized wear protection solutions, tools and services
Metso Outotec is a frontrunner in sustainable technologies, end-to-end solutions and services for the aggregates, minerals processing, metals refining and recycling industries globally. By improving our customers’ energy and water efficiency, increasing their productivity, and reducing environmental risks with our product and process expertise, we are the partner for positive change.
Headquartered in Helsinki, Finland, Metso Outotec employs over 15,000 people in more than 50 countries and its illustrative combined sales for 2019 were about EUR 4.2 billion. The company is listed on the Nasdaq Helsinki. mogroup.com
Brenntag links its distribution network of caustic soda in the Eastern United States
AdministratorBrenntag (ISIN DE000A1DAHH0), the global market leader in chemical and ingredients distribution, announces the acquisition of the operating assets of US-based Suffolk Solutions, Inc’s caustic soda distribution business.
“The business and the related terminals of Suffolk Solutions fit seamlessly into our ambitions to further link Brenntag’s caustic soda network in the Eastern United States. There is great potential to strengthen our supply chain and expand our customer base in this geography,” says Steven Terwindt, Member of the Management Board of Brenntag Group and CEO Brenntag North America.
The Virginia headquartered company, founded in 2005, has access to a bulk terminal as well as to a rail transloading facility within the state. The business relies on long-term suppliers and a loyal customer base.
Anthony Gerace, Managing Director Mergers & Acquisitions at Brenntag Group, summarises the locational advantages of the acquisition: “Suffolk Solutions will strengthen Brenntag’s footprint in the Virginia market and thus will enable us to improve our logistical infrastructure throughout the region. It will provide us with greater supply flexibility, manoeuvrability, and additional storage capacity on the east coast of the United States.”
The acquired business generated sales of approximately USD 15.6 million in a 12-month period ending April 30, 2020.
About Brenntag:
Brenntag is the global market leader in chemical and ingredients distribution. We connect our suppliers and customers in value-adding partnerships. Our almost 17,500 employees provide tailor-made application, marketing and supply chain solutions. Technical and formulation support, market, industry and regulatory expertise as well as advanced digital tools are just some examples of our services that are aiming to create an excellent customer experience. Our full-line portfolio comprises specialty and industrial chemicals and ingredients of a world-class supplier base. Building on its long-standing experience, unmatched global reach and local excellence, Brenntag works closely alongside its partners to make their business more successful. We are committed to contribute towards greater sustainability in our own business and the industries we serve, and to achieve sustainable profitable growth. Headquartered in Essen (Germany) and with regional headquarters in Philadelphia, Houston and Singapore, Brenntag operates a unique global network with more than 640 locations in 77 countries. The company generated sales of EUR 12.8 billion (USD 14.4 billion) in 2019. Brenntag shares are traded at the Frankfurt Stock Exchange (BNR).
More...
US metals & mining industry sees a rise of 9.5% in deal activity in Q2 2020
AdministratorThe US metals & mining industry saw a rise of 9.5% in overall deal activity during Q2 2020, when compared with the last four-quarter average, according to GlobalData’s deals database.
A total of 46 deals worth $1.84bn were announced in Q2 2020, compared to the last four-quarter average of 42 deals.
M&A was the leading category in the quarter with 42 deals which accounted for 91.3% of all deals.
In second place was venture financing with four deals, accounting for 8.7% of overall deal activity in the country’s metals & mining industry during the quarter.
In terms of value of deals, M&A was the leading deal category in the US metals & mining industry with total deals worth $1.83bn, followed by private equity deals totalled $5.19m.
The US metals & mining industry deals in Q2 2020: Top deals
The top five metals & mining deals accounted for 99.1% of the overall value during Q2 2020.
The combined value of the top five metals & mining deals stood at $1.82bn, against the overall value of $1.84bn recorded for the month.
The top five metals & mining industry deals of Q2 2020 tracked by GlobalData were:
- ‘s $1.78bn merger of Alacer Gold and SSR Mining
- The $23.78m merger of Evrim Resources and Renaissance Gold by
- Metalla Royalty and Streaming’s $5.77m asset transaction with
- The $4m acquisition of Idaho North Resources by Metalla Royalty and Streaming
- Greenpro Capital’s acquisition of Millennium Sapphire for $4m.
This analysis considers only announced and completed deals from the GlobalData financial deals database and exclude all terminated and rumored deals. Country and industry are defined according to the headquarters and dominant industry of the target firm. The term ‘acquisition’ refers to both completed deals and those in the bidding stage.
GlobalData tracks real-time data concerning all merger and acquisition, private equity/venture capital and asset transaction activity around the world from thousands of company websites and other reliable sources.
About GlobalData
4,000 of the world’s largest companies, including over 70% of FTSE 100 and 60% of Fortune 100 companies, make more timely and better business decisions thanks to GlobalData’s unique data, expert analysis, and innovative solutions, all in one platform. GlobalData’s mission is to help our clients decode the future to be more successful and innovative across a range of industries, including the healthcare, consumer, retail, technology, energy, financial and professional services sectors.
ABB’s new analytics and AI software helps producers optimize operations in demanding market conditions
AdministratorABB launches analytics software and services that combines operational data with engineering and IT data to deliver actionable intelligence
The ABB Ability™ Genix Industrial Analytics and AI Suite is a scalable advanced analytics platform with pre-built, easy-to-use applications and services. It collects, contextualizes and converts operational, engineering and information technology data into actionable insights that help industries improve operations, optimize asset management and streamline business processes safely and sustainably.
Analyst studies suggest that industrial companies typically are able to use only 20 percent¹ of the data generated, which severely limits their ability to apply data analytics meaningfully. ABB’s new solution operates as a digital data convergence point where streams of information from diverse sources across the plant and enterprise are put into context through a unified analytics model. Application of artificial intelligence on this data produces meaningful insights for prediction and optimization that improve business performance.
“We believe that the place to start a data analytics journey in the process, energy and hybrid industries is by building on the existing digital technology – the automation that controls the production processes,” said Peter Terwiesch, President of ABB Industrial Automation. “We see a huge opportunity for our customers to use their data from operations better, by combining it with engineering and information technology data for multi-dimensional decision making. This new approach will help our customers make literally billions of better decisions.”
ABB AbilityTM Genix is composed of a data analytics platform and applications, supplemented by ABB services, that help customers decide which assets, processes and risk profiles can be improved, and assists customers in designing and applying those analytics. Featuring a library of applications, customers can subscribe to a variety of analytics on demand, as business needs dictate, speeding up the traditional process of requesting and scheduling support from suppliers.
Scalable from plant to enterprise, ABB Ability™ Genix supports a variety of deployments including cloud, hybrid and on-premise. ABB Ability™ Genix leverages Microsoft Azure for integrated cloud connectivity and services through ABB’s strategic partnership with Microsoft.
“The ABB Ability™ Genix Suite brings unique value by unlocking the combined power of diverse data, domain knowledge, technology and AI,” said Rajesh Ramachandran, Chief Digital Officer for ABB Industrial Automation. “ABB Ability™ Genix helps asset-intensive producers with complex processes to make timely and accurate decisions through deep analytics and optimization across the plant and enterprise.
“We have designed this modular and flexible suite so that customers at different stages in their digitalization journey can adopt ABB Ability™ Genix to accelerate business outcomes while protecting existing investments.”
A key component of ABB AbilityTM Genix is the ABB Ability™ Edgenius Operations Data Manager that connects, collects, and analyzes operational technology data at the point of production. ABB Ability™ Edgenius uses data generated by operational technology such as DCS and devices to produce analytics that improve production processes and asset utilization. ABB Ability™ Edgenius can be deployed on its own, or integrated with ABB AbilityTM Genix so that operational data is combined with other data for strategic business analytics.
“There is great value in data generated by automation that controls real-time production,” said Bernhard Eschermann, Chief Technology Officer for ABB Industrial Automation. “With ABB AbilityTM Edgenius, we can pull data from these real-time control systems and make it available to predict issues and prescribe actions that help us use assets better and fine-tune production processes.”
Further details can be found online:
ABB Industrial Automation ABB’s Industrial Automation business offers a broad range of products, systems, and solutions for customers in the process and hybrid industries. These include industry-specific services, as well as measurement and analytics, marine and turbocharging offerings. ABB’s Industrial Automation business is #2 in the market globally. With deep domain knowledge, experience and expertise, ABB Industrial Automation helps customers increase their competitiveness, improve their return on investment and run safe, smart, and sustainable operations.
ABB (ABBN: SIX Swiss Ex) is a leading global technology company that energizes the transformation of society and industry to achieve a more productive, sustainable future. By connecting software to its electrification, robotics, automation and motion portfolio, ABB pushes the boundaries of technology to drive performance to new levels. With a history of excellence stretching back more than 130 years, ABB’s success is driven by about 110,000 talented employees in over 100 countries. www.abb.com
¹ARC Advisory Group
Nidec ASI presents its 8 Guidelines for restarting the economy in the name of sustainability
AdministratorThe Group is committed to creating an electric and green future, placing the Made-in-Italy excellence of its technologies at the heart of this revolution. Nidec ASI's goal is to increase its current turnover of €400 million to €1 billion by the end of 2023, concentrating on the energy sector, mobility and industrial efficiency
Nidec ASI, the commercial platform of the Nidec Group, which has always been committed at an international level to ensuring a more sustainable economic development, has decided to elaborate some guidelines for a green restart inspired by concepts of sustainability and circular economy which focus on the transformation towards an “All Electric” world. A responsibility that the globally present multinational has been particularly aware of throughout this delicate and challenging period which has created an important sense of community.
Each of the 8 Guidelines elaborated focuses on a different aspect: renewables, energy efficiency, logistics, mobility, circular economy, digital, young people and health. They represent Nidec ASI's desire to inform everyone on how the Group is evolving (also by strengthening its R&D) and what principles and areas it is working on in order to contribute to an evolution which can no longer be delayed, creating awareness among institutions, businesses and citizens alike on the need to take climate change very seriously and restart in the wake of this crisis by acting decisively as true enablers of a green and digital future.
"As Nidec ASI, we firmly believe that by supporting the evolution of energy, logistics and industry, it really is possible to make a difference and we are developing solutions that can reduce energy consumption by building on renewables, the sustainable movement of people and goods and on promoting greater energy efficiency, not only in the industrial sector, but also in every aspect of our lives," said Dominique Llonch, CEO of Nidec ASI and Chairman of Nidec Industrial Solutions. "The future will be electric; this is the only key for promoting a model of sustainable development. Institutions must allow this change to happen in the shortest possible time while companies currently operating in the industrial solutions market must make the technologies they produce accessible to all. An offer of quality and affordable green technologies which are also sustainable must represent the main and moral objective of the players operating in the market, and as always, we want to do our part, continuing to develop technologies such as Power Quality, at the center of hydrogen production, and BESS, which are essential for optimizing the use of renewables and represent the excellences of our Italian production facilities."
1) Renewables
Today the Energy & Utilities sector is undergoing a radical transformation which is impacting every phase of the value chain. Upstream of the value chain, we are witnessing the progressive transition from a centralized system to a much more distributed, interactive and interconnected ecosystem for the production of electricity from renewable sources. The transition towards renewable energies is in fact the most effective way to combat climate change and air pollution and, rightly so, the European Recovery Plan envisages investments to support growth of the clean energy sector. It is therefore more necessary than ever to move away from a fossil fuel economy towards an electric economy and an "All Electric" world.
Italy, a land of sun, water and wind, is starting out from an environmentally advantageous position, consequently it is desirable that institutions work with the aim of facilitating this essential change, allocating funds to the development of renewables.
Nidec ASI has understood the needs arising from the transition towards renewable energy sources, offering solutions that enable optimum usage, such as: BESS (Battery Energy Storage Systems), a sector in which the Group is a leader with more than 70 projects worldwide and over 700MWh of systems installed, microgrids, important innovations in the field of LNG (Liquefied Natural Gas) extraction and the development of the hydrogen market. Nidec technology is also present in two of the three most important nuclear fusion research centers.
2) Improving energy efficiency
A reduction in greenhouse gas emissions, but above all improved electricity consumption efficiency, must apply in every socio-economic context.
Our homes and public buildings can represent a good starting point, as highlighted by the European Recovery Plan. The adoption of innovative technologies, new low energy impact home appliances, heat pumps and photovoltaic panels that make it possible to zero energy needs, together with the renovation of buildings with the aim of achieving net-zero energy, represent the simplest and most effective solutions in this race against climate change.
Nidec Group supports the decision of the European Council, included in the latest Recovery Plan, to move in this direction, setting up over 20 research laboratories dedicated to studying how to optimize the efficiency of electric motors and drives.
In addition to houses, however, it is also essential to focus on the energy efficiency of industry, especially heavy industry. The goal, which Nidec ASI has also adopted as its own, is therefore to transform these plants to make them more efficient.
3) Diversified and digital logistics
The COVID-19 emergency uncovered a number of weak points in logistics leading to considerations useful for rethinking the approach towards a more agile, flexible, green and sustainable supply chain. In the future, those businesses which adopt enlightened procurement policies and logistics, relying on diversified zero-kilometer suppliers, located in different countries, and not only those able to offer the lowest price, will find themselves with a huge competitive advantage also in times of emergency situations.
It is precisely with a view to diversifying the supply chain that the European Union will implement the Trade Policy Review, to ensure a continuous flow of goods and services. In this scenario, Nidec ASI already has a head start, given that the Group's flagships are still the Italian factories.
Consequently, it becomes evident that it is essential for those players operating in logistics to rethink their way of seeing things, activating leaner decision-making processes, accelerating the digital transformation by making use of IoT (Internet of Things) solutions, thus strengthening the entire supply chain. Another important aspect in this transformation concerns accelerating port automation which, thanks to digitalization, will be able to significantly reduce emissions.
Connected, fast and streamlined logistics will increase the efficiency of moving vehicles, goods and even people, and will make it possible to reduce energy consumption and, consequently, also the environmental impact.
4) Electric mobility
The world of mobility, increasingly strategic for the development of all economic sectors, especially those related to the digital economy, will become 100% electric: ports, ships, cars, trains and public transport will all be connected and powered through the electricity grid.
Promoting this transformation is fundamental, partly because this is the sector where it is most necessary to reduce CO2 emissions and where the objectives set by the authorities are highest and partly to guarantee a green restart of tourism, of primary importance above all in a country like Italy, where this sector accounts for 13% of the national GDP and employs 15%-20% of the Italian workforce, thus confirming its strategic nature for relaunching the country.
Also in this case, the European Recovery Plan traces out the direction to be followed, focusing on the need to support the development of electric transport, the relative recharging infrastructure and alternative fuels.
Electric vehicles will become increasingly more popular, as they represent the most efficient option to completely eliminate emissions. This process has been going on for years, but it must also be supported through the allocation of ad hoc funds for the widespread diffusion of recharging points and upgrading of the electricity grid to ensure that during times of peak demand sudden drops in voltage are avoided that could cause blackouts in the cities and also to meet car sharing needs which will become more and more common.
Nidec is at the forefront of this sector, thanks to its Ultra Fast Charger for electric vehicles. The Group also contributes to the development of hybrid and electric buses connected via cable and wheels by making use of its knowledge of the battery market.
Maritime transport, which also contributes heavily to the emission of pollutants harmful to the air, will also have to undergo a radical green transformation. Nidec ASI was among the first players in the world to promote the adoption of solutions for electric navigation, starting with the electrification of port docks, which allow ships to turn off their engines and hook up to the electricity grid. It is in fact currently involved in a "shore-to-ship" project for the port of Genoa as well as in 8 other similar projects around Europe. The Group also offers solutions for on-board energy storage systems, such as those installed on the Seasight ferries which today navigate Norwegian waters without producing any type of pollution or noise.
5) Circular economy
A further essential pillar for an industrial restart from a green perspective follows the principles of the circular economy, an area into which huge European investments will be channeled, as envisaged by the new Circular Economy Action Plan, with particular reference to the development of infrastructures and technologies capable of optimizing waste management.
The world in which we find ourselves has increasingly scarcer resources, hence the need for effective recycling and the activation of a virtuous circle is emerging that makes it possible to minimize waste and the use of raw materials.
Nidec ASI, which invests 3% of its turnover in power electronics alone, is committed, with its research activities, to dealing with these principles, reducing the number of components in the field. A virtuous example is its VDF AFE, a new variable frequency medium voltage drive. By eliminating the transformer, it guarantees extremely high energy efficiency, it is 30% more compact and about 60% lighter than other solutions, reducing not only energy consumption and emissions but also the use of difficult to dispose of metals such as copper and iron. A particularly innovative product is also the CAplus, a new electric motor characterized by the fact that over 95% of the materials used in its construction can be recycled at the end of its service life.
6) Digital transformation
The electric and green transformation of logistics, transport and industry goes hand in hand with digital transformation, where connectivity is able to bring enormous benefits not only with a view to more sustainable development, but also in terms of quality of the services offered, safety and competitiveness of the relative industries.
In the future, for example, ports will be increasingly integrated and connected thanks to the Internet of Things, based on the extensive use of sensors, and the evolution of big data, which will make it possible to optimize the collection and analysis of the data produced, improving the traceability of goods, staff safety and sustainability.
Even the evolution of steel works is undergoing integration with new technologies, primarily wi-fi, up to a prospective vision of creating a "Steel Industry 4.0", experiments into which are already in progress. Nidec ASI's automation and system integration solutions are developed and implemented to successfully complete revamping projects, even very complex ones, with the aim of making advanced solutions, such as wireless technologies 'talk' to older technologies.
As rightly envisaged by the European Recovery Plan, investing in the process of digitalization of Italy and Europe in general (which has accelerated during this period of crisis) is therefore a priority in order to be able to bring about a real transformation in the direction of dematerialization and therefore a reduction in emissions, with consequent benefits everywhere. However, all of this requires, first and foremost, substantial investments in telecommunication networks and innovative technologies (AI, robotics, cybersecurity, data cloud infrastructure, blockchain), adequate partners and incentives, a reduction in red tape and an effective education process.
7) Engagement with young people
In the race towards a sustainable economy, it will be essential to guarantee a future for young people and engage them, given that they are increasingly more attentive to green issues. Companies and institutions must therefore target the main issues concerning sustainability at the new generations who can become the main testimonials of the urgency for a green restart.
Also in the industrial solutions sector, it will be essential to continue to attract and retain young talents who will be able to develop the sustainable innovations of the future, increasing funding for internships, also extending the time spent in companies and supporting the insurance / additional costs caused by the new safety standards, as well as investing in advanced welfare programs capable of ensuring a good work-life balance and a satisfactory training path.
With the aim of initiating a constructive dialog with young people on these issues, the idea was born to launch Nidec ASI's new social communication campaign, I WANT A GREEN FUTURE on a worldwide level, which aims to awaken everyone's consciences, starting with young people, raising awareness on the values of environmental sustainability.
8) Health
The spread of the coronavirus throughout the world has highlighted the undeniable link and interconnection between all human beings on the planet, uncovering enormous economic imbalances that still persist in different parts of the globe.
In this scenario, it is increasingly more evident how a company cannot grow and thrive in an unhealthy environment where safeguarding health is not a priority. Institutions must therefore allocate huge investments to protecting people's health.
A concrete demonstration of how the focus on people's health is crucial is given by the path Nidec has taken, also with the recent announcement of the "Nidec Health Declaration", aimed at strengthening and focusing even more on the management of employee wellbeing, and the establishment, by the Nidec Group, of a Health Promotion Committee. The Group also boasts an employee welfare program, which offers wellbeing benefits.
Nidec ASI is also committed to continuously minimizing the impact of its activities on the environment and society by adopting a vision of the future that is also "collective", and therefore takes the community into huge consideration. Recognizing that we are part of the ecosystem which surrounds us and understanding that our actions can have an impact on the territory where we operate is the duty of each and every one of us.
Nidec Industrial Solutions is the commercial platform created by Nidec Group which brings together all Nidec ASI products and services. The company designs, manufactures and installs reliable and efficient control and power systems, with particular attention to life cycle, performance and energy consumption, making it one of the world's technological leaders operating in the process of energy transition towards an "All Electric" and therefore green and sustainable future. Nidec Industrial Solutions offers customised solutions throughout the world for a wide range of industrial applications. Its reference markets are the petrochemical, traditional and renewable energy, steel, naval and industrial automation markets. The multinational is specialised in heavy duty applications in which high power and high performance are key: electric motors and generators up to 65 MW of power (87,000 HP); power electronics inverters and converters; automation and software for industrial processes; retrofitting of power plants and hydroelectric generators; integrated systems for producing electricity from renewable sources and their integration in power grids; medium and low power drives. Thanks to the acquisitions of Control Techniques and Leroy-Somer, the company is also able to offer technologies optimised for the control of motors and to develop automation solutions for specific applications, tailored to the needs of the client to provide a flexible response to each requirement.
US metals & mining industry M&A deals total $1.83bn in Q2 2020
AdministratorTotal metals & mining industry M&A deals in Q2 2020 worth $1.83bn were announced in the US, according to GlobalData’s deals database.
The value marked an increase of 65.5% over the previous quarter and a rise of 11.9% when compared with the last four-quarter average of $1.64bn.
The US held a 20.7% share of the global metals & mining industry M&A deal value that totalled $8.86bn in Q2 2020.
In terms of deal activity, the US recorded 42 deals during Q2 2020, marking a rise of 35.5% over the previous quarter and a rise of 20% over the last four-quarter average.
The US metals & mining industry M&A deals in Q2 2020: Top deals
The top five metals & mining industry M&A deals accounted for 99.4% of the overall value during Q2 2020.
The combined value of the top five metals & mining M&A deals stood at $1.82bn, against the overall value of $1.83bn recorded for the month.
The top five metals & mining industry deals of Q2 2020 tracked by GlobalData were:
- ‘s $1.78bn merger of Alacer Gold and SSR Mining
- The $23.78m merger of Evrim Resources and Renaissance Gold by
- Metalla Royalty and Streaming’s $5.77m asset transaction with
- The $4m acquisition of Idaho North Resources by Metalla Royalty and Streaming
- Greenpro Capital’s acquisition of Millennium Sapphire for $4m.
This analysis considers only announced and completed deals from the GlobalData financial deals database and exclude all terminated and rumored deals. Country and industry are defined according to the headquarters and dominant industry of the target firm. The term ‘acquisition’ refers to both completed deals and those in the bidding stage.
GlobalData tracks real-time data concerning all merger and acquisition, private equity/venture capital and asset transaction activity around the world from thousands of company websites and other reliable sources.
About GlobalData
4,000 of the world’s largest companies, including over 70% of FTSE 100 and 60% of Fortune 100 companies, make more timely and better business decisions thanks to GlobalData’s unique data, expert analysis, and innovative solutions, all in one platform. GlobalData’s mission is to help our clients decode the future to be more successful and innovative across a range of industries, including the healthcare, consumer, retail, technology, energy, financial and professional services sectors.