
Administrator
AMEC/Jacobs alliance nets Magnox contract
Jacobs Engineering Group Inc. has announced that its VELA alliance with AMEC was awarded a contract by Magnox Ltd to provide project management resources in support of Magnox’s decommissioning program in the UK.
The Project Management Resource Partnership agreement is an extension of the Magnox Resource Transfer Protocol that was established with Jacobs and AMEC in 2011.
Under the terms of the contract, the VELA alliance is providing project management expertise, skills development, coaching, and employment opportunities for Magnox employees.
“This agreement is a unique opportunity for the three companies to work together in an innovative way, and it gives Magnox the opportunity to balance its resourcing requirement for both the long- and short-term while investing in long-term career opportunities for our staff," said Peter Burns, Magnox director of projects.
"Our aim is the retention of skills within the entire nuclear industry and this agreement will play a key role in achieving that aim,” he added.
Image All rights reserved by MagnoxSites
United Utilites boss sets out investment plans
United Utilities has some 9000 projects ongoing in the current AMP, investing £787 million in 2012/13 – about £100 million higher than the previous year. Cumulative investment across the first three years of AMP5 is now just over £2 billion.
The Capex, said CEO Steve Mogford, reflects a smoother and more effective investment profile than the previous five-year cycle. The company, he added, is on track to deliver the five-year programme within the regulatory allowance of around £3.5 billion.
The utility recently recorded its best performance for many years on the Environment Agency’s operational performance metrics, and Mogford promised more investment in the wastewater network to help adapt to changing weather patterns.
For 2012/13, United Utilities returned to a minimum of 'stable' on all its key serviceability measures – having last year seen the rating for its wastewater infrastructure slip from 'stable' to 'marginal'.
A programme for recovery is now in place, targeting sewer cleaning, CCTV surveys, defect discovery and remediation, Mogford said.
"In AMP4, our poor performance in delivering our regulatory commitments led to us receiving a shortfalling revenue penalty of over £80 million at the last price review. Whilst we still have two years to go in this AMP, our performance to date is significantly better than in the last five-year period," he reported.
United Utilities is considering extending its integrated pipeline network between Manchester and Liverpool to north west Cumbria to improve security of supply there, according to its CEO.
Following a £100 million-plus investment, the pipeline is now contributing to United Utilities integrated water network and helped keep customers supplied throughout the dry period in the first half of 2012.
Reviewing other major projects, Mogford said a £200-million Liverpool wastewater treatment works expansion – the utility's largest capital programme in AMP5 – was progressing within budget and ahead of schedule.
The extended treatment works is expected to come online in early 2016 and will treat up to 11,000 litres of wastewater per second – helping the rejuvenation of the River Mersey.
In Preston, meanwhie, a £100-million+ project to improve river and bathing water quality is nearing completion. It involves building a 3.5km-long storm water storage tunnel, 2.85 metres in diameter, to divert storm water flows to the utility's existing treatment works.
The project is intended to reduce the number of spills to the River Ribble from combined sewers and contribute to significant improvement in bathing water quality in the Ribble Estuary and along the Blackpool coastline.
Looking ahead, Mogford said new and more stringent environmental legislation, such as the European bathing water standards coming into effect from 2015, would drive further investment in wastewater assets.
In response to Government plans to reform water abstraction arrangements in the UK, United Utilities has launched a pioneering scheme to restore two rivers in the Trough of Bowland in Lancashire.
The project, which is in conjunction with the Environment Agency, is helping to rejuvenate the rivers by taking less water for the local population in dry periods.
To compensate for any resulting shortfall of water for homes in the area, United Utilities is building a new £12 million pipeline to connect the local water treatment works to a nearby service reservoir.
"Partnerships like this will increasingly become a way to deliver the changes needed as we adapt to climate change," said Mogford.
Metso valves for desert project

Sierra Gorda Sociedad Contractual Minera (SCM) requires the valves to control the flow of process and make-up water for a variety of applications in the mine.
The Atacama Desert is one of the driest regions on earth. Precipitation is extremely rare and there is no surface water at the project area. Therefore, the project will rely heavily on sea water delivered via a 350km-long pipeline from the Pacific Ocean.
To combat the highly corrosive effects of seawater, Metso will provide valves constructed of SMO254tm austenitic stainless steel, which is highly resistant to the effects of chlorides.
Metso will deliver 54 Neles V-port segment control valves from 1″ to 12″, on/off valves from 3″ to 18″ – with series B1, QPX pneumatic actuators or BIFFI electric actuators – as well as many Jamesbury ball valves. All of the valves are rated to ANSI#150.
The Sierra Gorda mining facility is expected to process 110,000 tonnes/day of mineral and its operations will begin late in 2014. The anticipated life of the project is 21 years and the equipment supplied has a 25-year life expectancy.
Chemoxy set for growth
Chemoxy was recently awarded £1.5 million from the Regional Growth fund to expand capacity at its Billingham site to install a multi-purpose combined reaction and distillation plant at a total cost of £6 million.
Chemoxy's new plant is to provide additional capacity for low-emission latex paint additives and provision of recycling facilities for various waste and by product streams. The new facility will create 15 direct jobs and provide at the Billingham site, and generate sales of £7.5 million, 70% of which will be sold overseas.
The company's bid was supported by NEPIC, Stockton upon Tees Borough Council, Tees Valley Unlimited and the University of Northumbria.
Chemoxy has since awarded Redhall Engineering a three-year contract to deliver project, maintenance and engineering support services to its two Teesside-based assets.
In December 2011, the current management team led the buyout of Dow Chemical Co’s custom processing facilities at Middlesbrough and Billingham. The Middlesbrough site has been carrying out distillation since 1868, while Billingham was added to the portfolio in 1994. The business employs over 100 workers across the two sites.
Chemoxy claims to be one of Europe’s largest providers of custom manufacturing services to blue chip petrochemical and speciality chemical companies as well as to smaller companies with niche applications. It also manufactures solvents for use in the latest generation of paints and cleaning products.
Chemoxy Details:
Sales revenue £35M/year
No. of employees >100
Annual output 30-40ktpa
Storage capacity 18,000m3
Distillation columns 9
Reactor capacity 165m3
Two sites 17 acres & 3 acres
Middlesbrough site:
- 7 high resolution fractionation columns
- Up to 50 theoretical plates
- 0.75 to 1.75m diameter
- Vacuum (to 5mmHg) and side stream capabilities
- 6 Reaction Vessels
- Stainless steel (25m3)
- Solids addition facility
- Solids handling plant
- Hydrogenation unit – 3 barg
- Temperatures to 230 C
- Drumming and IBC filling facility
- 2 high resolution fractionation columns
- Up to 30 theoretical plates
- 0.75 to 1.25m diameter
- Vacuum (to 5mmHg) and side stream capabilities
- 3 Reaction Vessels
- Stainless steel (25m3)
- Glass lined (9m3)
- Solids handling plant
- Chloride resistant Duplex stainless steel (24m3)
- Solids addition facility
- Methyl Chloride direct feed to reactors from bulk storage
- Temperatures to 200C
- Drumming and IBC filling facility
To find out more please follow this link http://www.chemoxy.co.uk/
Chemical industry reports lower sales
UK chemicals and pharmaceuticals manufacturing companies have reported a fall in sales to customers over the previous six months.
In its latest survey of member companies, the industry’s trade body the Chemical Industries Association found 44% of companies had seen lower sales volumes, and only 22% an increase.
Looking ahead, on balance companies saw rising sales, albeit by a smaller margin than in the previous survey three months ago: the proportion expecting volumes to increase has fallen from 46% to 39%.
R&D expenditure is also set to be hit with 26% of companies now forecasting an increase, whereas in the last survey 46% expected R&D expenditure to rise.
Commenting on the figures, the Association’s Chief Executive said “It is clear we continue to operate in difficult times. The one encouraging piece of news is that 70% of companies expect employment numbers to increase or remain the same.
"We will be working hard to ensure the contribution of our sector is recognised and we can return to a position where manufacturers in this country and abroad maintain and enhance their buying of chemicals - which are the essential raw materials in so many products we take for granted - from companies in the UK”.
(Image source: ICCA)
Total in Euro1bn upgrade at Antwerp site
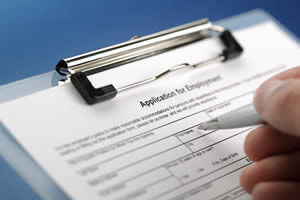
The upgrade programme includes two major projects, which will be implemented in the near future: a new refinery upgrading complex and a plant to convert low value refinery fuel gases into feedstock.
The upgrading facility is to comprise a solvent de-asphalting unit and a mild hydrocracking unit. Intended primarily to convert heavy fuel oil into desulphurised diesel and ultra low sulfur heating oil, the planned complex responds to the shift in demand toward products with a lower environmental impact. The facility is to start up in early 2016.
The fuel gas conversion unit will produce low cost petrochemical feedstock, replacing expensive oil-based naphtha. By further enhancing the integration between the platform’s refining and petrochemical units, this project will increase the competitiveness of the latter, said Total. The facility is due to start up in early 2017.
The modernisation also involves the closure of two existing production facilities will be shut down, as they are no longer competitive in the world economic environment:
The smallest and oldest steam cracker, currently idled for lack of markets, will be permanently stopped and dismantled.
The smallest and oldest polyethylene production line will be closed at end-2014, once an investment in other polyethylene lines to produce a new range of polymers has been completed.
The aim is to develop the Antwerp facilities into one of the most profitable platform of the refining and chemicals business of Total, explained Patrick Pouyanné, President of Total Refining & Chemicals.
“With this investment, Total is demonstrating not only its commitment to maintaining its position as a competitive industry leader in Europe and but also its ability to adapt to market trends by reducing its production capacities and emphasizing higher value-added products that meet the most stringent environmental standards,” he said.
Total said the Antwerp platform’s workforce would remain unchanged at around 1,700 people. Employees working in the facilities scheduled for shutdown will all have the opportunity to further develop their careers at the platform’s newly created production facilities.
Welsh Water adds Veolia WWT units
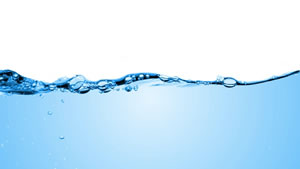
Dŵr Cymru Welsh Water is to install Veolia tertiary treatment technology at Connahs Quay WwTw. The project is part of a £1.65-million upgrade being carried out by Imtech Water, Waste and Energy – one of the utility's AMP5 partners.
This new contract, which follows similar installations at a number of other Dŵr Cymru Welsh Water wastewater treatment works, will see two Hydrotech HSF2212/11-1F Discfilter units being installed.
The upgrade, due for completion in July 2013, will accommodate growth and improve final effluent quality at the 20,000 population equivalent works.
Each of the Discfilters will treat 113l/s of final effluent to a suspended solids standard of 15mg/l 95%ile. The contract includes design, supply, and installation of the two filters, which will be fabricated in 316 stainless steel and GRP and fitted with self-cleaning backwash spray nozzles. The advanced nozzles will provide further operational robustness and reduce operator intervention.
The Hydrotech Discfilter uses a series of rotating segmented discs that support 10 micron polyester filter fabric panels. As the wastewater flows through the disc segment, suspended solids including biomass flocs and precipitated phosphates are captured on the fabric and removed from the effluent.
When required, backwashing of the fabric is initiated automatically on headloss, with the dirty backwash water being returned to the head of works. Low backwash water volumes, typically only 1 – 3% of throughput, low power consumption and minimum maintenance are among the selling points for the Hydrotech Discfilter.
The units are also providing tertiary treatment at Dŵr Cymru Welsh Water’s Churton, Farndon and Mold wastewater treatment works, treating 10, 14.6 and 92 l/s respectively – in addition to installations at Thames Water, Scottish Water, Yorkshire Water, Anglian Water, Severn Trent and United Utilities.
Green light for Viridor EfW project
The London Borough of Sutton Development Control Committee has decided to grant Viridor planning permission for the construction of its proposed Energy Recovery Facility (ERF) in Beddington, Viridor announced 16 May
The move follows a 15 May announcement from the Environment Agency that it is “minded to grant” the Environmental Permit required to operate the proposed facility at the company’s recycling and landfill site in Beddington.
In reaching its decision, the Environment Agency said that it had required Viridor to go beyond the measures they would need to apply if this plant was located elsewhere and which would normally be considered best available technology (BAT). The permit, it added, would ensure a “high level of protection” for both the environment and human health.
The Environment Agency’s position showed that the proposed Energy Recovery Facility is a safe and sustainable alternative to landfill disposal in the area, according to Robert Ryan, Viridor’s head of projects.
“The ERF will deliver real economic, social and environmental benefits to the local community; a view that has been supported by the London Borough of Sutton’s own planning officers,” said Ryan.
Viridor's proposed ERF is to convert around 275,000 tonnes of non-recyclable waste into electricity – enough to power around 30,000 homes – and heat, potentially, to be utilised locally whilst diverting around 95% of waste inputs away from landfill.
The project is set to create hundreds of jobs during construction and 40 permanent roles once operational, the company has stated.
Key details:
Vacancies:
Viridor vacancy information
Europe's largest water plant to use GE technology
The largest drinking water purification plant in Europe to feature GE’s ZeeWeed 500 water treatment technology is under construction in Ravenna, on the east coast of Italy
Several years ago, Romagna Acque – Società delle Fonti SpA, the public company in charge of the water wholesale supply for Italy’s Romagna region, decided to heavily invest in supplementing its existing water supply to ensure water always is available.
The municipality selected GE’s membrane technology for the project due to its ability to convert deteriorated raw source water into high-quality, safe drinking water.
Often hit by long periods of drought that cause the reservoirs to reach critically low levels, the region turns to the Po River, the longest river in Italy, as a drinking water source.
The raw water from the Po River has a high variation of solids and turbidity especially after rain, and the new drinking water plant needed a reliable method to purify the severely deteriorated incoming water.
“Our region’s economy depends on industrial assets and on seasonal tourists who come to Ravenna’s coastal area for popular beaches and historical sites. Safe and reliable drinking water is essential to ensuring visitors continue to patronize the Romagna region,” said Andrea Gambi, CEO, Romagna Acque – Società delle Fonti SpA.
“We had been experiencing water shortages and needed to add to our reliable supply of water. Building a new drinking water plant with GE’s ZeeWeed technology is the key to turning the river into a safe and dependable source of potable water.”
Once operational, the new drinking water plant utilising GE’s ZeeWeed 500 technology will treat an average flow of 95 million liters per day (MLD), which is enough water to serve around 400,000 people.
GE will provide the technology to the engineering, procurement and construction joint venture led by Torricelli S.r.l., in partnership with Degrémont SpA. Featuring 40 cassettes filled with ZeeWeed 500 modules and distributed in eight filtration trains, the new facility will be the largest potable plant of its kind in Europe using GE technology.
The Nearly 1,000 plants worldwide use this GE filtration technology to separate particles, bacteria and viruses from water or wastewater.
It has a unique ability to handle high peaks of solids and turbidity, combined with the high-efficient process and low energy and chemicals usage, claims GE. This, it said, makes it suitable for treating deteriorated or high variation raw water sources and always producing high and stable drinking quality water.
Ultrafiltration uses a semi-permeable membrane barrier to reject suspended solids, bacteria, viruses, endotoxins and other pathogens in water to produce treated water known as permeate with very high purity and low silt density. It serves as a pretreatment for surface water, seawater and biologically treated municipal effluent before reverse osmosis and other membrane water treatment systems.
Metso for Finland's largest pellet-fired heating plant
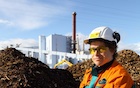
Finland's largest pellet-fired heating plant, which was supplied by Metso to Tampereen Energiantuotanto Oy, Tampere, is employing a technology that is said to be the first of its kind in the country. The plant has been producing energy in Tampere since last December.
Tampereen Energiantuotanto, part of Tampere Power Utility, is responsible for the group's electricity and district heating production, maintenance and development.
The company's plant is mainly fired with wood pellets and its heat output is around 33 MW. The plant has replaced some of the capacity of the oil- and gas-fired boiler plants and has thus helped substantially reduce the CO2 emissions from the production of district heat.
"The plant will help us to secure the competitiveness of district heat, lower CO2 emissions and improve our delivery reliability in the southern region of Tampere," said Antti-Jussi Halminen MD of Tampereen Energiantuotanto.
Metso's delivery comprised a complete turnkey boiler plant solution and its DNA automation system. The new plant operates unmanned with remote monitoring from the main control room of the Lielahti power plant.
By using the automation technology, the operators are able to flexibly control the district heat production process and quickly respond to changes. The technology used at the plant is based on the pellet fuel being pulverized in separate grinding mills and burned in a pulverized combustion boiler.
The start-up and load control of the combustion process is remarkably high and the pulverized fuel allows for clean, energy efficient and flexible heat generation.
Pulverised pellet combustion is new to Finland, but Metso has been using it in Sweden on a smaller scale.
This was a major delivery for Metso, as it is the first reference using this technology for district heat generation on such a large scale, said says Jussi Orhanen, director, heat & power plants, part of Metso's power business unit.
The Bioheat RampUp plant delivered by us enables the use of pellets and oil, simultaneously in any proportion or separately, in one and the same boiler, which is operated unmanned."