
Administrator
Pump package to Russian longwall coal mine
Mining equipment supplier the Kopex group is delivering a turnkey solution for the Vladimirskaya longwall coal mine in Russia.
Part of this project is the powered roof support system to be installed at the coalface itself. Kopex has awarded the supply of the critical pumping systems to RMI Pressure Systems Ltd., based in Manchester, UK.
The Kopex Group is, amongst other things, a manufacturer of powered roof support systems which delivers products into the most demanding markets, including China, Russia and Australia. These systems are specifically designed to provide roof support structures for longwall coal mining.
A crucial part of these systems is the pumping system, which must have completed rigorous testing before being deployed in the field to ensure the safety of the miners operating the equipment.
The practice of longwall mining has been developed and refined with the use of hydraulic roof support systems, which provide support at the coalface to allow the shearer to cut the coal from the seam. Each support can weigh 30-40 tonnes and be rated at 1000-1750 tonnes and also have the ability to hydraulically advance itself 1 metre at a time.
As the roof supports advance, so the roof of the mine is allowed to collapse behind them and the shearer continues to pull the coal from the seam. This all makes the roof support system of critical importance to the mining operation and to the safety of the miners involved in operating the machinery. Any equipment which is selected to operate in this hazardous environment must be proven in reliability and require a minimum level of maintenance.
The efficient operation of the roof support system directly affects the productivity of the mine and any down-time on the system in such a difficult operating environment would be very counter-productive. The reliable performance of these systems is essential if the client is to maximise output from the mine and return on investment.
Power source
The roof support systems require a power source and this takes the form of a sophisticated hydraulic pump capable of producing extremely high pressures. The reliability of these pumps must also be beyond any doubt and bench testing has to be carried out for thousands of hours to ensure their operation in the mine will be faultless.
In this case, Kopex has selected RMI Pressure Systems, which has a proven track record in the mining industry and has considerable experience in supplying equipment for the longwall mining operation.
RMI has delivered three Trimax S300 pumps to power the roof support system, each capable of providing 244 litres/min at up to 353 bar, as well as two of Trimax S300 pumps for the water pumping system, which are cable of providing 319 litres/min at up to 92 bar. The entire contract also includes a service and spares package as well to ensure continued reliable service.
In 2012, the Russian government approved a long term investment plan for the coal industry, with $123 billion to be invested over the next 17 years. This is deemed necessary to meet the future requirements for coal which is used to generate 25% of the electricity requirement in Russia.
With coal production from the underground mines expected to increase by nearly 50% over the next 20 years, the prospects for future contracts within the Russian coal industry are looking good, said RMI.
Shell network event for Brent decommisioning
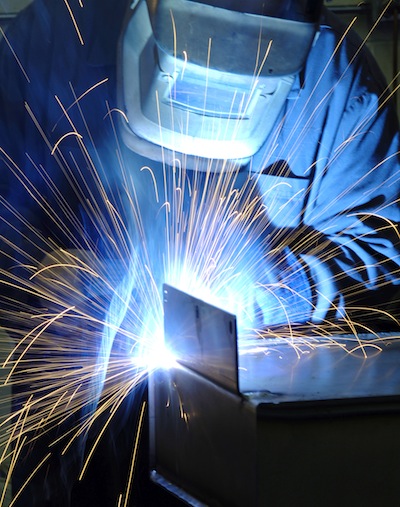
Shell UK E&P is holding a decommissioning networking lunch focused on the Brent Project on 15 April, Hardwick Hall Hotel, North East England.
The event will feature a presentation from Austin Hand, general manager decommissioning & restoration, Shell U.K Exploration & Production, who will give and update on the project.
Decommissioning of the Brent field (50/50 Shell/ExxonMobil) is one of the largest decommissioning projects in the North Sea with the scope comprising four platform topsides, three concrete substructures referred to as GBSs, one steel jacket, 154 wells tom plug and abandon and some 36 pipelines to decommission.
Three platforms are still in production; the fourth, Brent Delta has now ceased production. Work is underway to engineer down, in readiness for topsides removals of Brent Delta in 2016.
The project is planning to submit a single field wide decommissioning programme to the UK regulator DECC during 2014.
While companies continue to invest heavily in the North Sea other mature assets are reaching the end of Field Life. Over the next 20 years or so more than £30 billion pound will be spent on Decommissioning in the North Sea.
Jacobs JV nets Shell ONEgas extension
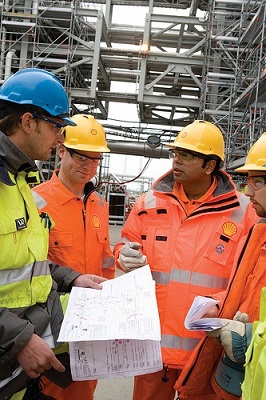
Jacobs Engineering Group Inc. has announced recently that its AJS joint venture with AMEC and Stork has secured a contract extension to continue providing integrated services to the Shell ONEgas Southern North Sea (SNS) asset base.
Shell ONEgas is a combined business unit of Shell UK Exploration & Production (Shell) and the Nederlandse Aardolie Maatschappij B.V. (NAM).
Under the terms of the contract, AJS is providing integrated engineering and project management services for maintenance, modifications and capital projects.
The work is executed offshore on 54 assets in the Southern North Sea, and onshore at gas plants in Bacton in the UK and Den Helder in the Netherlands.
Around 1,250 personnel are employed by the joint venture across the assets, and from office locations in Great Yarmouth, UK, and Leiden, Netherlands. Working as an integrated team, the AJS joint venture has successfully delivered multiple services for Shell ONEgas since 2003.
“The contract extension builds on our long-term relationship with Shell and NAM in Europe,” said Mark Bello, Jacobs group vice president.
UK offshore industry must get it together
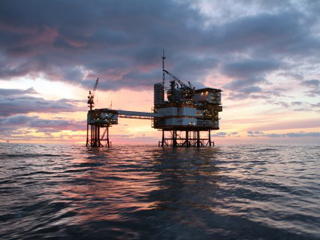
A new blueprint for oil & gas production on the UK Continental Shelf (UKCS) has been set out by the Wood Review, which maps out a new stewardship regime for the industry.
The report, issuedon 24 Feb, targets the recovery of an extra four billion barrels of oil equivalent - worth £200 billion - on the UKCS over the next 20 years.
Towards this goal, the UK government is to establish a new regulatory body to enforce greater co‐ordination of activities across the industry. This will include collaboration in areas such as exploration, third-party access to infrastructure, production efficiency and decommissioning.
A model for this approach is Norway's Exploration and Production Information Management (EPIM) association - a non-profit organisation governed by the operators on the Norwegian Continental Shelf.
Owned by 40 major oil companies, EPIM's remit is to facilitate IT-based solutions and services for the oil & gas industry through standardisation of requirements and processes.
Around 150 companies - authorities, contractors and suppliers - use the association's services. These are provides via a private Cloud-based system and include hubs dedicated to areas including environmental management, safety training, license administration, equipment information and logistics tracking.
These collaborative platforms improve the quality and flow of information, and lower costs for each individual operator, according to Ove Ryland, executive director of EPIM. They also, he said, introduce best-practice in life-cycle information management.
Moreover, these gains are being achieved "without impacting competition between companies or joint ventures or any reduction in information security," Ryland emphasised at the SMi E&P Information and Data Management conference in London on 12-13 Feb.
"[Collaboration] can be done, it has been done, and needs to be done to ensure a cost-effective and information management-efficient oil & gas industry," said Ryland.
The EPIM director concluded, though, by warning that "there is no point in collaboration and standardisation if you continue to do things the 'old' way or its not implemented properly across the organisations."
This level of industry-wide collaboration will, therefore, require new approaches to data-management at the oil & gas majors - as seen at Shell, which has recently formalised how information is processed throughout the organisation.
"The Shell data model is unambigious, system-agnostic, business-owned and is enabling our senior people to inform, discuss and articulate KPIs," Johan Stockman, an IT leader at Shell Global Solutions, said at the SMi conference in London.
At Shell, experienced, senior managers are now responsible for ensuring that the definitions in the data model actually reflect the requirements of their particular business area. They must, for example, specify what is meant by particular KPIs for well-injection performance, rather than assume that everyone will know what they mean.
"It all comes down to defining what you need," explained Stockman. "If you havn't thought this through, how are you going to have a successful application that you will be able to deploy?"
The increasing emphasis on data-management is closely linked to the digital oilfield concept in which IT and control and instrumentation technologies are combined within the enterprise data system. With their capacity to analyse large volumes of data, these systems give managers and engineers real-time access to engineering data and operational metrics.
The system is supported by production-level technologies as seen, for example, at Ithaca Energy (UK) Ltd, which is using a digitally enabled well performance monitor (WPM) from Honeywell Process Solutions (HPS) at its Athena oilfield in the UK North Sea.
Using WPM, Ithaca’s engineers can monitor how their wells are performing, while visual models predict what each well is capable of producing. Summary information and KPIs from real-time process data historians, production databases and engineering well models, allow operators to track field performance data and manage equipment assets.
The large flows of data generated by such digital oilfield systems is, meanwhile, increasing the need to connect offshore platforms with onshore bases via wireless and mobile networking and satellite communications.
According to a Deloitte report, these trends will drive demand for remote wireless sensors to monitor parameters such as temperature and pressure changes in the oilfield. The information, it notes, is increasingly being monitored by specialist engineering teams based at remote centres dedicated to tracking multiple offshore facilities.
Demand for such capabilities is driving M&A activity in the process control sector, as seen with Rockwell Automation's recently announced acquisition of vMonitor - owner of the world’s largest installed base of wireless wellhead monitoring systems, with more than 6,000 well sites.
The company’s technologies include an all-wireless portfolio of wellhead sensors and transmitters, remote terminal units, gateways and modems, as well as turn-key monitoring and control systems and services for oil & gas wells, pipelines, pumping and lift stations.
Some observers, though, believe the UK sector could do much more to leverage existing installed base of intelligent instruments. These already comprise the vast majority of the field devices employed in offshore oil and gas production fields.
According to figures from Emerson Process Management, up to 90% of the diagnostic data generated by this equipment is stranded in the field and never used. By integrating technologies that are in many cases already in place, production companies can utilise the diagnostic data acquired from smart field devices and digital valve controllers to improve operations and safety, the vendor believes.
Indeed, perhaps, the biggest lever for the digital oilfield and collaboration between operators on the UKCS will be the industry's commitment to safety - as defined by the many policies and practices adopted in the wake of the Deepwater Horizon disaster in the Gulf of Mexico.
This is acknowledged in the Wood report, which concludes: "Industry has achieved very successful collaboration on health & safety and there is no reason why this cannot work just as well in areas such as production efficiency, deployment of new technologies, shutdown co-ordination and a collaborative approach to decommissioning."
Technologies to Watch: Augmented reality
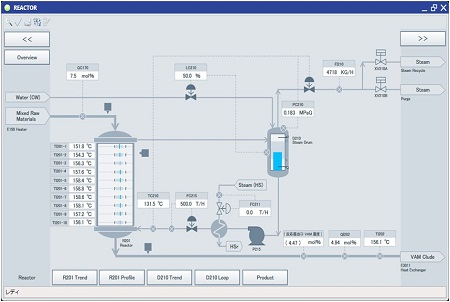
Industrial augmented reality (AR) promises to eliminate human error at process facilities: carrying out double checks on operators actions, walking them through procedures, and providing feedback on whether tasks were completed properly and any problems that may arise.
Omega Simulation Co. Ltd. (OSC), a JV between Yokogawa Electric Corp. and Mitsui Chemicals Inc. is one of the pioneers of this technology. Since its formation in 2007, it has been developing advanced simulation systems based on Yokogawa's control & instrumentation technologies and Mitsui expertise in modelling simulation.
Dynamic simulators are widely used for operations training but OSC aims to extend this to every stage of a plant lifecycle - from the EPC phase to providing operational assistance and plant optimisation by recognising and predicting plant and process conditions.
These efforts have led to the launch of Mirror Plant, which is claimed to be an industry first for the use of online simulator technology in optimising the safety and efficiency of industrial process facilities. It is designed, particularly, to help operators in industries, such as oil & gas and petrochemicals, who are often required to adjust many variables in real-time.
For example, chemical plant operators need to adjust the state of catalysts and the composition of the reagents and product materials in a chemical reactor in real time. However, explains Yokogawa, many of the process variables are difficult to measure or cannot be measured directly.
Synchronised with the plant control system, the simulator is said to visualise the internal state of a plant process and make accurate predictions on various process parameters, explains a Yokogawa press release.
A proprietary function adjusts model parameters to visualise the current state of the plant, and up to several hours ahead. It can also be used at plant locations where it is not possible to measure temperature or pressure.
A field test conducted 2011-13 at a Mitsui Chemicals plant showed that the technology could efficiently stabilise and optimise the operation of a distillation tower, Yokogawa has reported.
Related article
TECHNOLOGY - Yokogawa develops 'industry-first' process simulator
Contracts and projects: Oil & Gas Feb 2014
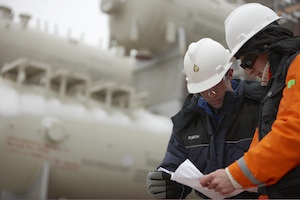
In Indiana, Emerson Process Management has completed a process automation project, as part of a major BP upgrade of its refinery in Whiting - the group's largest refinery in the US. As main automation contractor, Emerson provided technologies and services that helped enable the Chicago-area refinery to modernise its facility to process advantaged crude supplies. (Read more)
The Arctic countries together rank as the top seven most attractive mining destinations in the world, according to UKTI - citing the findings of Fraser Institute global mining survey, Led by Finland, Sweden, Canada, Norway and Greenland, the region offers major opportunities to UK businesses across different products and services. These, say UKTI, include exploration and mining, construction and infrastructure, financial and professional services, and equipment and machinery. (Read more)
ConocoPhillips has placed a £600k order with Amarinth for the design and manufacture API 610 OH2 separator recirculation pumps for the Britannia-operated Alder platform in the North Sea. The pumps, which have to fit into the existing Alder structure, are for high pressure duties on the platform separator recirculation process where the suction pressure can fluctuate between 1 and 60 bar. (Read more)
Energy production technology services company Proserv has extended its subsea manufacturing capabilities with the acquisition of the entire share capital of UK-based KRG Industries from majority shareholder Torishima Pump Mfg. Co. Ltd of Japan. KRG provides precision engineering services including machining, welding, inspection and testing to oil & gas OEMs, oilfield service companies and defence contractors.
Gazprom Energy on 5 Feb announced a new commercial partnership with Tata Chemicals Europe to support production at the business’ combined heat and power (CHP) plant in Cheshire. The deal will see the business energy firm supply natural gas to the chemical company’s existing CHP facility in Northwich in addition to buying back excess electricity generated by the plant.
Energy production technology services company Proserv has extended its subsea manufacturing capabilities with the acquisition of the entire share capital of UK-based KRG Industries from majority shareholder Torishima Pump Mfg. Co. Ltd of Japan. KRG provides precision engineering services including machining, welding, inspection and testing to oil & gas OEMs, oilfield service companies and defence contractors.
Shell has begun production from the Mars B development through Olympus – its seventh, and largest, floating deep-water platform in the Gulf of Mexico. It is the first deep-water project in the Gulf to expand an existing oil and gas field, it is expected to extend the life of the greater Mars basin to 2050 or beyond. Combined future production from Olympus and the original Mars platform will deliver an estimated 1bn barrels of oil equivalent, Shell said 4 Feb.
KBR has been awarded a contract for the basic design development for Heerema Offshore Services' large new semisubmersible crane vessel (NSCV). Subsidiary GVA completed seven months of feasibility and conceptual studies on the NSCV in 2013. The basic design phase of the new vessel will cover the major part of 2014, KBR announced 4 Feb.
Bechtel is designing and building the facility, also known as the Vit Plant, for the US Department of Energy. When complete, the plant will treat 56m gallons of radioactive waste stored in underground tanks in Washington state. Watch a company video of the progress.One of the largest oil companies in Poland is looking for specialised pit-drilling equipment, including pumps, cables and modules, along with appropriate certificates. The tender is split into two parts: Supply of six complete sets of pit-drilling equipment: Supply of six complete sets of pit pumps, along with ESP. The deadline for responses in 9 Feb. UKTI details - external site.
Air Products is to supply main cryogenic heat exchangers for the Yamal LNG project. Under an deal with a consortium including Technip and JGC Corp, three of its MCR units will be employed wiithin the propane pre-cooled mixed refrigerant liquefaction process. Each of these units using Air Products LNG process technology and equipment will produce 5,500ktpa of LNG, for the overall 16,500ktpa three-train facility.
Dubai Petroleum Establishment has signed up Technip for the engineering, procurement, construction and installation of the Jalilah B field development project, 90km offshore Dubai, at water depth reaching 60m. The scope includes the Jalilah B platform, a 900-tonne deck, a 500-tonne jacket, 13 new risers on existing platforms and 110km of pipelines. Technip’s center in Abu Dhabi will execute the project for completion in the second half of 2014.
The AMEC Tekfen Azfen (ATA) consortium has won a $974m contract for the BP-operated Stage 2 development of the Shah Deniz gas field in the Caspian Sea, AMEC said 28 Jan. ATA's remit covers the fabrication, load out and offshore hook-up and commissioning of the topsides units of the two Stage 2 platforms. (Read more)
Jacobs Engineering Group Inc. has been awarded a new two-year oil sands and plant services contract by Suncor Energy Services Inc. at its Fort McMurray base plant, Jacobs announced 28 Jan.
(Read more)
Alfa Laval has won an SEK65m order to supply its Packinox heat exchangers to an integrated refinery-petrochemical complex in the Middle East. Delivery is scheduled for 2014 and 2015. The heat exchangers will be included in a process to remove substances, such as sulfur, from the feed stock.
Weir Group PLC has signed a two-year contract with Lukoil Oil Co. to provide general maintenance services for the West Qurna-2 oilfield in Southern Iraq. The £59m deal will see Weir engineers deliver mechanical, electrical, maintenance and pipeline services for the related production facilities, including the Mishrif central processing plant, Weir said 24 Jan.
Wood Group GTS has won a long-term contract with Rockland Capital to provide maintenance services for two GE Frame 7EA gas turbines at the company's 225MW Eagle Point power facility in Westville, New Jersey. The 13-year deal covers parts, repairs, field services, installation of the ECOMAX combustion management system, and remote monitoring and diagnostics to provide predictive performance management of the gas turbines.
January 2014 Listing:
Process contracts and projects: Global Jan 2014
TECHNOLOGY - Enter the flying drones
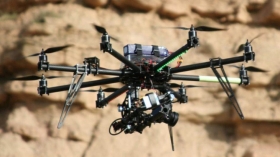
Air space above process facilities in the oil & gas, power generation is increasingly being visited by unmanned flying devices sent to monitor conditions that would be much more difficult to check from the ground or vessels at sea.
Academics at the University of Aberdeen are the latest to join this 'high' tech approach which is in growing demand among oil & gas and power plant operators, including at the stricken Fukushima nuclear reactor in Japan.
Working in collaboration with a group at the University of Bergen in Norway, the Scottish team is using remotely operated flying machines to scan rock formations in remote areas of the North Sea.
Drilling a well in the North Sea, enables companies to directly measure the rocks in the borehole, Given, though, that two wells are often miles apart, it is difficult to predict what the rock layers in between the boreholes look like.
A drone, however, can collect large volumes of data from otherwise inaccessible cliff sections in remote and often dangerous places.
The work is part of a project called SAFARI which features the use of laser scanning to create virtual rock formations that are accurate to within less than a few millimetres.
The spider-like helicopter vehicle used in the project costs around £10,000 and is remotely operated using radio controls and carries two cameras which allow it to collect stereo, 3D imagery.
“We look at similar rock units which occur in cliffs above sea level and we use the drone to make extremely detailed 3D models, which we can then adapt for the subsurface," explained professor John Howell, a geoscientist at the University of Aberdeen.
"This gives us a much better idea of what conditions are like between these two bore holes and then allows us to predict how the oil will follow and how much we can recover.
"As the drone can make extremely detailed 3D models, we can then adapt for the subsurface to give a much better idea of what conditions are like between two bore holes."
The research work in the SAFARI project is supported by 24 oil companies seeking to build better models of the subsurface and improve recovery from oilfields. The next phase, which will be the first to fully utilise the drones will start later this year.
Cyberhawk survey manager Stuart Thomas presented at the recent ESRI European Petroleum User Group conference alongside Shell. The presentation highlighted work completed for Shell using our fixed-wing and multi-rotor UAVs.
Another recent convert to the technology is Shell, which has started using UAVs to acquire aerial data was to enhance Shell’s emergency response capability by having highly detailed and up-to-date aerial imagery for its sites.
The energy company engaged CyberHawk carry out aerial inspection and surveying using remotely operated aerial vehicles (ROAVs) whether it’s a close visual inspection of a live flare stack, flare tip, live transmission tower or topographic land survey from the air.
The inspection was completed despite a 250m exclusion zone around the mast due to worries about its structural condition.
Cyberhawk conducted the inspection with a two man team operating from a supply vessel. The team collected hundreds of high definition images of the mast and completed a detailed report on its structural condition.
This allowed the client to gain a valuable assessment of an otherwise unreachable asset. The ROAV inspection saved the client hundreds of thousands of pounds, as a jack-up was not subsequently needed.
Cyberhawk’s met mast inspection compliments a range of other innovative services for the renewables sector including wind turbine blade, tower, transition piece and transformer platform inspections.
Another pioneers in this field is Honeywell, which supplied its T-Hawk micro air vehicle (MAV) to help emergency workers at Japan’s Fukushima Daiichi nuclear facility get up-close video and photos inside the plant as they battled radiation releases.
Weighing just 17 pounds, the T-Hawk is a ducted-fan vertical takeoff and landing air vehicle. Pilots can determine manual or autonomous flight paths from up to six miles away for up to 40 minutes at a time.
Three Honeywell employees, trained to fly the unmanned T-Hawks remotely, flew five missions and captured hours of video and dozens of photos of the nuclear reactor. The four T-Hawks in service at Fukushima Daiichi have been adapted to carry radiation sensors.
The T-Hawk features a hover-and-stare capability that enables pilots to hold it in one place and zoom in on features inside the damaged reactors while the T-Hawk sends live video and still images back to recovery workers.
The T-Hawk also is capable of sending live in-flight video feeds to help workers focus on critical areas and adjust direction mid-flight. Pilots can control T-Hawk cameras to alter angles and get better views of damaged equipment. Just 14 inches in diameter, the T-Hawk can be flown into tight spaces where humans and other aircraft cannot go.
“The T-Hawk reminds us that innovative technologies initially created for defense purposes can find crucial roles in humanitarian and disaster recovery efforts,” Mahoney said.
Shale fuels move to 'self-configurable' control systems
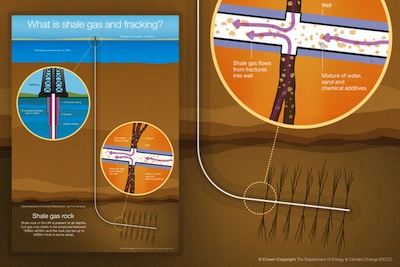
The concept of self-configuring process automation systems that do not require lengthy and costly support from IT specialists has moved a step closer to reality with a software development for the shale gas industry.
In a shale gas drilling operations, wells are added almost every day to maintain and increase production, with some fields having up to 5000 wells. As wells come on-line - or off-line for maintenance - IT engineers must frequently create new code and graphics to modify reports accordingly.
To reduce these demands, Invensys has developed software technology that enables administrators or field engineers to readily add wells to a control system, along with details of the equipment and operating parameters involved.
"They can add or subtract wells as they need to. They just go into the system, close that well off, and it is no longer in the report," John Gilmore, director of upstream oil & gas at Invensys, said in an interview with PIM.
"Changing the configuration, or adding say a compressor to that well, just means [ticking] check boxes," the Invensys expert added.
The product called Well Field Application is part of Invensys' Wonderware suite and is based on technology acquired six years ago from Pure Automation a small company that developed the basic concept.
According to Gilmore, Invensys has a number of clients for the application in the US, including two major players with 20,000 wells - but he was unable to disclose their names for confidentiality reasons.
"What we are really doing is taking a standard product, working closely with the owner to understand how he wants to run his business," said Gilmore. "We match and adapt the solution-set to meet his needs so that he can then take it from there.
"This is as opposed to saying 'I have got this great product, it will work, you will love it, now what do you want to do with it.' You have got to talk with the client to see what he wants to do."
Gilmore went on to cite a range of other potential applications for the software in batch processes and product mixing & blending. This included deployment at speciality chemicals plants, where a change of ingredient can lead to an entire control system being redefined.
"We want to automate that process to drive down the costs and make it a much more useful system for the end users," said Gilmore. "We are not there yet, but we are trying to move towards something that is much more configurable by the user, as opposed to [only being] configurable by the IT people or other specialists."
Turning data into good decision-making
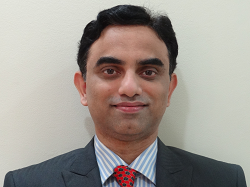
Process Technology Trends: Viewpoint from Anand Vishnubhotla, who leads the global center of excellence for intuition executive at Honeywell / Honeywell Process Solutions:
A key trend we are seeing this year is around making sense of all the data in a plant and across the enterprise, which is now a constant struggle for many operations.
At manufacturing facilities, critical information is often scattered throughout a variety of databases, enterprise applications and operational systems in a wide range of formats. If this information does not come together in a meaningful way, the opportunity for plant and business personnel to collaborate and then take effective action is lost.
Industrial organizations, therefore, require better ways to deal with the mountain of disparate data collected in plants or across facilities. Multiple applications and spreadsheets typically are used to manage production, monitor processes and make operating decisions. These systems are usually isolated or linked with complex, custom interfaces that make it difficult to use the data and maintain its integrity.
The latest data-integration and visualisation technologies, however, enable users to anticipate, collaborate and act with confidence on data. That’s why developers of operational intelligence solutions now focus on providing context to information, which starts with a unified view of data assets enabling capture of valuable knowledge across the enterprise and sharing of key learnings and best practices.
Solutions supporting continuous performance monitoring can be used to trigger notifications and tasks or workflows, with sophisticated dashboards and dynamic handling of problems and opportunities in near real time.
Data is harnessed and delivered across the enterprise so personnel can collaborate between business units and take the right actions when needed. In addition, companies can replace rapidly out-of-date print documentation and capture the knowledge of experts prior to retirement or staff attrition.
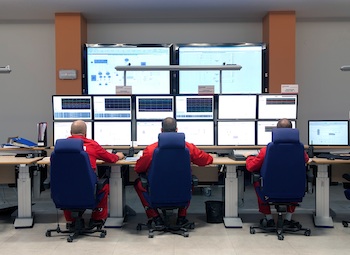
In a typical process plant, operations-intelligence solutions simplify reporting and eliminate errors by automating data entry for business analytics and process safety. They also serve as the main interface for controlroom operators to observe processes and dialog.
Since data is correlated, aggregated and presented in a uniform manner, plants achieve real-time visibility and systematic capture of know-how of their workforce. This saves time and allows employees to concentrate on their core activities or consider process improvements.
With today’s advanced technology, companies can make more agile decisions, drive intelligent operations and solve key challenges. Operations management can progress from data to decisions faster with visual key report analysis and diagnostic data, and then act on knowledge in a systematic manner.
This also helps plants to stop reinventing and start reusing assets and procedures in order to squeeze more value out of current investments.
The latest technologies and software provide the means to streamline workflows across the plant, improve personnel productivity, and reduce interface cost and complexity. Capturing expert knowledge in a repeatable set of actions facilitates collaboration across functional silos and geographic boundaries, and can enable staff reductions in remote locations.
Organisations with access to the right information at the right time are able to identify opportunities for optimisation and avoid problems that previously passed unnoticed. Plus, they transition from locating and analyzing information to taking action on it more quickly.
The ability to see, understand and act on the relationships within critical data is key to creating a competitive advantage, and this can only be achieved when all applications and underlying data are amalgamated.
Once industrial organisations do this, they can identify and take advantage of opportunities earlier, mitigate potentially damaging plant events and make confident business decisions.
Integrated drive systems to change VSD perceptions
John InskipProcess Industry Trends: Viewpoint from John Inskip, Siemens Industry Drives specialist:
The major topics of 2014 likely to make a positive impact on the process industry will be centred around integrated drive systems (IDS).
By using integrated drive technology we change how we traditionally perceive variable speed drives (VSD). Rather than purely a ‘product’, they become much more - an intrinsic part of a fully integrated drive solution.
Using an integrated approach from VSDs right down to the mechanical system allows a drive train to be optimised in order to deliver the best solution in terms of energy efficiency, operational performance, reliability and safety technology. These are all key factors that process industries are taking into account right now.
The philosophy of IDS allows for data to be acquired upstream. All data regarding production variables can be monitored and key data regarding performance of the drive system can be accessed locally or remotely. This helps make predictive maintenance truly effective, and a far better system than planned maintenance, with the potential for significant cost savings, too.
IDS also offers the opportunity for an organisation to align its business to a single source supplier; as a result the business and commercial aims of the customer are more fully understood, which can lead to reductions in project lead times and commercial costs associated with multi-vendor supply chains.