
Administrator
SI signals return of the 'smaller vendors'
Pressure to reduce costs across the process supply chain is prompting companies to reconsider their automation-buying strategies, according to an executive of systems integrator Capula.
While there now is a growing pipeline of automation project in the UK, approvals for some larger projects are still being delayed, said Simon Coombs, business development director of the independent SI, focused on energy and utilities markets.
"It is momentum with these large projects that makes all the difference," noted Coombs, adding that even clients with strong balance sheets and good access to funding are not starting projects without a "clear and compelling" business case.
For example, he said that "obsolescence upgrades and interesting demonstrator projects that historically were done simply for engineering reasons are tending not to get approved."
Capula specialises in combining automation control and real-time IT with electrical and instrumentation systems. It increasingly has to demonstrate how these projects clearly benefit clients' businesses with defined approaches to minimising delivery and risk.
These demands, said Coombs, are "increasing the importance of effective automation control and real-time IT solutions ... and of having domain expertise and proven credentials - in addition to a good price, of course."
Over recent years in the automation and drives sector, companies have tended to buy products from the main global vendors. This has been seen as the best way to keep up-to-date with the latest R&D and standardisation requirements across different markets.
But Coombs said the need to reduce capital or operational costs means clients are "looking for innovative approaches that can decrease the delivery and the whole-life costs of solutions.
However, he added, this is conflicting with the trend by large, global automation vendors "to steadily increase the price of their products year-on-year in response to increasing energy, materials and manufacturing costs."
With system integrators being squeezed between these conflicting pressures, Coombs concluded that a future trend might be "the re-emergence of bespoke, innovative products from smaller, nimble vendors that can provide more cost effective, albeit less standardised solutions, for our clients."
PIM EfW leaders prefer proven technologies .. for now
Support for tried-and-tested energy from waste (EfW) technologies and scepticism over newer alternatives seems to be the order of the day for major players in the waste management industry.
Among the technologies to have earned its spurs is anaerobic digestion, according to Adam Read, practice director responsible for waste management and resource efficiency at Ricardo-AEA – an international consultancy covering global energy and environmental issues
"While the UK might not have the 1000s of facilities operating that the government predicted, AD is now proving itself as long as you've got the feedstock quality and the site and markets," Read told delegates at the recent Green in the City conference in London.
CHP with large- or medium-sized thermal facilities was another viable and deliverable technology and would play an increasingly significant role in the UK's energy security over the next five to 10 years, he forecast.
"I am a big fan of heat production in terms of thermal efficiencies but you can only do that if you have got a heat-user on tap nearby: logistics centres, refrigeration units, industrial units all make ore sense than an old landfill site in the middle of nowhere," he said.
On the other hand, while he saw a role for newer technologies such as gasification and pyrolysis, Read would "not be putting my money into any just yet: "Give it another year and I think you will see some newer facilities operating to give us more comfort about the scale of those projects and the quality of the feedstock and the outputs. "
Axion Polymers processes rigid waste plastics and ELV shredder residue at plants in Salford and Manchester , Company director Roger Morton emphasised the need to be realistic about the chances for newer schemes, particularly in the areas of gasification and pyrolysis.
"We have been working on that for up to 12 years and I am also having to say the same things like gasification to make liquids doesn't work without a very expensive gasifier that is fed with oxygen, There are lots of air-blown gasifier projects that claim to make liquids, but don't believe it.
"Another myth is that pyrolysis of biomass can make a usable liquid; it makes a horrible soup of disgusting carcinogenic chemicals. You can make it with a great yield but not a reusable liquid fuel."
A better bet, perhaps was fuel-from-plastics. This technology, said Morton, is showing promise but still required more effort to get the waste plastic clean enough to give a good yield in a pyrolysis plant than simply making recycled material from it.
"On the whole we think that mechanical recovery is a good idea," he said. "If you are going to burn it, and usually about half of our material is burned, then a lot of the pyrolysis and gasification technologies around are really incineration by another name only more expensive.
However, the choice of which EfW technology to back is no longer just a game for big guys within the waste management industry, according to Peter Jones of Ecolateral.
"People at big companies like Air Products and IneosChlor are reading the Ofgem report warning that we could be having brow outs next year. If you think about the political impct of brown-outs in Jan, Feb March 2015 just before a general election. These are big energy users are going to start putting in facilities and making them work,
For the major chemical and process companies, EfW offers a way to reduce their exposure to the vulnerabilities of the international coal, gas or other energy markets.
"Those are the people that are going to move in: we are just in this phoney war period," the waste management expert concluded.
BP expert wants suppliers to embrace tagging
BP is seeking to build on the success of an initiative to track equipment currently being built and shipped around the world for the engineering construction work on the ambitious Clair Ridge and Quad 204 projects.
At Clair Ridge, west of the Shetland Islands, BP is replacing an ageing platform with two new production platforms, due to be operational by around 2016.
A related project is the Quad 204 FPSO (floating production storage and offloading) facility, which will replace an existing vessel currently being decommissioned there.
With the production and accommodation jackets already in place, the topsides are being constructed by Hyundai Heavy Industries (HHI) in, Ulsan, South Korea. As all the metalwork has been procured by HHI, the tracking effort is focused solely on the equipment going into the building of the new Clair Ruge platforms and FPSO.
Over $1-billion worth of equipment is being procured by BP directly. This typically includes shell-and-tube heat exchangers, instrumentation, compressors, piping, pumps and valves, and even right down to small instruments and fittings.
BP is dealing with around 150 different vendors - predominantly in Europe - on the project. This presents a huge challenge in moving hundreds of thousands of assets, explains Blaine Tookey, senior technical consultant at BP's Chief Technology Office (CTO).
Based in London and Houston, the CTO is a team of just 12 of BP's top technology specialists, whose job it is to bring emerging and interesting technologies from outside of the oil & gas industry into the company.
A couple of years back, BP's materials handling people flagged up how millions of dollars worth of equipment was going missing on engineering projects. Moreover, if BP failed to deliver missing parts on time, it faced penalties in the contract that could dwarf the cost of the actual equipment.
"With past contracts, it has cost us millions of dollars because we have not delivered equipment and delayed production," Tookey said at the recent supply chain networking event in London, organised by SupplyChain Standard.
The search for a solution led the CTO team to study track-and-trace – a technology that is routine in industries, such as FMCG, but that has remained alien to the conservative world of oil & gas.
But, by taking a lead from companies in the automotive and aerospace industries, including Airbus, the CTO experts saw how electronic tagging technology could adapted for use in the oil & gas industry.
There were many options – barcoding, QR codes, passive and active RFID and GPS, but BP needed a system that could track everything from a washer all the way up to a multi-million dollar piece of equipment, in real-time and at minimum cost.
"Were we going to put a great big GPS tag on 100,000 pieces of equipment?: no because of the cost," Tookey said. "So we still had to decide how to get real-time tracking into this project and address other issues around health and safety, automated receipting and taking the human element out, to ensure 100% success."
And, while it has made sense to use a GPS tags on around 500 high-value items, these tags could have presented an explosion hazard if accidently left on.
So BP had to use specialist intrinsic safety (IS ) certified GPS tags from a Texas-based company called Geoforce. For tracking all other types of equipment BP opted to use laminated, printed RFID tag costing just $0.50 each.
Existing systems
From a systems perspective, BP wanted to ensure that AMEC, the engineering contractor for the project, and freight company Panalpina could follow the location of parts in real-time using their own existing systems. To achieve this, the oil and gas company put in 'middleware' called Crosstalk from Los Angeles-based Mojix, alongside Geoforce's system for tracking the satellite data.
Mojix, said Tookey, had invented a reader technology that can pick up RFID tags from distance in a warehouse and brought an "enormous understanding" of the electronic tagging market to the project.
For Clair Ridge, BP has established a base in AMEC's offices in London, where the RFID tags are printed and couriered out as soon as a vendor informs the team that work on a component is complete. The supplier is then sent tags with instructions on how and where to put two or three tags on each component box, which is then sealed so that as 'bonded goods' it won't be opened until it reaches HHI.
"We have asked 150 vendors to put them on. All have been very accommodating and have tagged the items as per our instructions" remarked Tookey.
BP has established two consolidation centres to handle the huge volumes of equipment involved. At these centres, in Antwerp and Milan, RFID handhelds are used to receipt the packages before they are put into containers, which have GPS tags put on then and also anti-tamper tags.
This allows real-time location of everything in the container based on the RFID information from then onwards. This is supported by a system to track the vessels during transit and so provide a full breakdown of where everything – from vessel to container to package to item – actually is at all times.
"Every piece of equipment is visible to us," said Tookey."You can go to a search button, key in a particular valve and it will tell you that that valve is in this package in this container on this ship, and when it left Antwerp and will arrive at HHI."
On arrival in South Korea, BP can again see the real-time location of the container via GPS, and then from the RFID tag once the boxes are in the warehouses - two have been leased as staging points for parts prior to delivery to HHI a couple of miles away.
BP also needs to know where every item is in the warehouse, as parts can often get moved around so that they can't be located when needed.
This requirement is being met by the installation of a Mojix Star Controller device on the roof of the warehouse. Based on technology originally developed by NASA, this device can pick up RFID tags 200 metres away – rather than the normal range of around two metres.
"That gives us real-time location of everything in the warehouse," said Tookey. "As it comes in, a package gets automatically receipted. Nobody has to do anything and the package is visible on the AMEC and Panalpina systems immediately. This means we can see what's ready for delivery to HHI."
Further opportunities
While the driver for the project was that BP did not want to lose anything, Tookey pointed to a range of additional gains, including efficiencies due to automated electronic data entry, the removal of paper and human error from the process, as well as the elimination of any delay in knowing when equipment is in South Korea.
Overall, said Tookey, the use of track-and-trace technology and the accuracy it offers, gives senior management confidence in a project programme with huge amounts of equipment involved. He is now starting talks with BP's top brass about possibilities for replicating it on the $28-billion Shah Dinez project – as well as broader applications for the technology.
This includes the use of active sensor tags for condition monitoring for temperature, humidity and shock. These were to be used on the Clair Ridge project, but time constraints and the need to get approvals around radio frequencies got in the way.
"The inspection teams are really keen," said Tookey. "They want to know if something has fallen off a truck or if the electronics have been subject to high temperature before it is actually put on to the plant and doesn't work.
"They can get it back to the manufacturer, there and then, rather than ship it out to South Korea and find it doesn't work. That is important for them. and we have already done trials with these sensor tags," he explained.
Looking further forward, Tookey said tagging everything on an item-by-item basis could benefit a whole host of manufacturing processes. Applications could range from planning of processes to improving safety, for example, by enabling workers to recognise valves and other critical components.
"If you tag something from the manufacturer and leave that then for the logistics and then for the operations [department] that could add huge value. We are probably 10 years away from the ultimate vision of getting everything tagged by the vendor, " said Tookey.
Standing in the way of this vision is the conservatism in the oil & gas sector, though Tookey said that Norway was making progress in introducing the technology into its oil & gas sector.
"You need an industry-wide approach as in FMCG," said Tookey. "I could put so many projects into BP if the vendor community were tagging things routinely. This is an enormous opportunity to add value across BP and the entire industry."
Project opportunities: Q&A with ABB
Process Industry Match Q&A with ABB on the current flow of project opportunities, particularly in he oil and gas sector – the main fouc of the company's processs control and automation activities in the UK:
PIM - Overall, how is the automation project pipeline flowing at the moment?
The pipeline for automation projects globally is steady, driven primarily by the demand from the large oil and gas operators for the latest control system technology to enhance functional safety and cyber security. As the installed asset base ages, there is a rising demand for life cycle services, to help operators extend asset life through upgrading.
In many parts of the world there are some major projects being instigated and ABB in the UK has been successful in securing significant automation projects primarily as it acts as centre of excellence for project execution and safety. Most notable have been the Queensland Curtis LNG project in Australia and Sadara Chemical project in Saudi Arabia.
Because of this global reach from the UK, ABB can access a global resource. More importantly, we are able to continue to invest and see growth, so while some industries in some countries may be flat or in decline, other industries or geographies will be strong.
This is important for ABB and important too for customers as it brings consistency of resources, teams and expertise, in a market with skills shortages. We also can continue to expand our capabilities and investments in R&D.
Economic and political instability in many parts of the world does have an impact on the number of projects that could be undertaken. Another contributing factor to the slowdown in projects is a global shortage of engineering skills at all levels.
PIM - Which vertical industry sectors are most active, and why?
For DCS and ancillary and supporting equipment, ABB in the UK focuses on oil and gas. It is also a global centre of excellence for project execution and safety and as such has a wide portfolio of projects in chemicals, oil and gas in many parts of the world.
The arrival of independent operators such as Premier Oil, Enquest and Ithaca, are helping to drive investment with some 30% coming from these players.
Meanwhile some of the major operators are focusing on large new developments and divesting existing assets. There is increasing influence from the Chinese with purchases last year of Nexen (Nexen CNOOC) and Talisman (Talisman Sinopec). In fact Chinese companies are now responsible for some 15% of the total UK oil production.
Among the drivers in the oil and gas sector are the global focus on safety, efficiency and reliability with the aim to enhance safety, increase production and generally improve every aspect of operational efficiency.
Practically all aspects of a control room are currently being reviewed. One key area is operator effectiveness and alarm management. Many incidents occur due to operators being distracted and ABB is investing heavily in designing efficient ergonomic operator workstations.
Other industry sectors showing growth are metals, with significant investments from the likes of Tata Steel. The automotive sector is also showing growth with significant investments coming from Jaguar Land Rover (part of the Tata group) and BMW. Meanwhile, the chemicals industry - although a long way from where it was - is still seeing investment and revamps of existing facilities.
PIM - What other drivers or barriers are influencing new project approvals at the moment?
Today oil prices are high at over $100 per barrel and the gas price is pushing 65p per therm. A key driver in the oil and gas (O&G) sector is the shift in world economies led by the growing middle class in emerging countries.
We expect to see a shift in O&G production - not a net increase, but more consumption in growing economies and a decline in our energy needs going forward. However, there remains an insatiable demand for energy, with the UK alone expected to consume 70% of its energy needs from O&G up to 2030.
In many ways, O&G has been immune to recessionary pressures, especially upstream, where it is has become a fundamental component in the way we live, just like food and air. However, the days when the UK was a net exporter of O&G are over so we need to have a broad energy mix and keep our options open.
The mature areas for O&G production will continue to produce for many years to come. However, new technologies will be essential to allow us to recover a lot more of the reserves and to access more marginal fields that weren’t previously economically viable.
At the same time new technology developments are making the production of unconventional O&G more realistic. Unconventional O&G, such as shale gas, requires a totally different approach.
Traditional ways of producing O&G in the North Sea typically sees large platforms and pipelines whereas shale gas production utilises multiple wells over large geographic areas with sophisticated gas gathering systems. The process involves huge quantities of water and the technological challenge is to find a way of handling that.
Other exciting new areas include the oil sands of northern Canada. Here oil is trapped in sands and produced through mining processes. At present this is expensive but it is only a matter of time before the technology is developed to make oil sands more cost effective.
There is major infrastructure development in the established O&G fields of the UK continental shelf (UKCS), where the move is to target deep sea opportunities. This is a fundamental shift from the current fixed platforms.
However, deep water activities in the Atlantic are very different to those in the Gulf of Mexico or Brazil primarily because the weather conditions are so much more severe in the North Atlantic.
Based on Opec’s own figures, the group’s members have ratcheted up spending on new oil production, with $300bn worth of projects currently in the pipeline. This increased investment has not delivered a significant fall in prices. However, Opec argue these prices need to be maintained at, or above, $100 a barrel in order to cover the cost of production and provide revenue.
PIM - What about opportunities in asset replacement?
The North Sea is a mature market. There are not a huge number of projects being developed. Today the vast majority of spend is on brownfield sites and maintaining current assets. Some assets are approaching 50 years of age. The challenge is keeping them running and safely.
The legacy associated with mature installations and their assets creates challenges around obsolescence of instrumentation, automation and hydraulic systems and extended maintenance, leading to plant life extension. This challenge is compounded by the fact that the major operators are moving on and leaving the assets to new entrants. New entrants are less experienced operators and they have to build engineering capability, depending on companies like ABB to arrest that legacy.
The North Sea industry is yet to face the decommissioning challenge when the assets eventually are removed.
Operating companies have some difficult decisions to make moving forward. BG have major opportunities in Tanzania, UK, Australia, Brazil, Canada etc - but with overall project costs so high, limited resources, and project schedules challenging, they need to prioritise on which investments they can make, or look for partners.
PIM - How big an issue is skills shortages today?
The single biggest challenge is getting the resources: the people, the expertise the engineers and the project managers to undertake the work. A lot more could be achieved if the industry had unlimited supply of good, experienced people.
The route cause can be traced back to the 1990s when a dip in the oil price resulted in many redundancies which has left a huge skills gap. Today the majors and the new entrants are trying to rebuild that lost resource through training and competency programs.
Key to this are better training facilities such as the carbon capture pilot plant installed at Imperial College London in 2012. Such facilities provide students with hands-on experience of operating real-life plant. The plant was built in collaboration with ABB and more such joint ventures between academia and industry are essential to secure the future supply of engineers.
Another priority is the need to maintain the highest safety levels imaginable.
Balancing process safety, asset development activity and day-to-day support together with short term and long term projects is difficult.
PIM - What is the outlook for the cost of production?
Some estimate that we are half way through the life of the North Sea in terms of production. During the first half, production was relatively low. With oil at $12 per barrel it was estimated production was costing $10 a barrel.
However, the next phase costs are high driven by demand, difficulties in reaching the reserves and the fact that extraction costs are at $40 per barrel.
So where is that money flowing?
PIM - How helpful is the UK's current tax regime?
The UK government’s recent decision not to support new gas storage investment in the UK has now put on hold a large number of high value projects as companies respond by shelving their plans.
A series of tax incentives from 2011 through to 2103 have, in general, been welcomed by the oil and gas industry, citing them as an important step forward in ensuring that the UK can maximise the potential of its natural resources in the North Sea. Field allowances are deliberately designed to encourage production from “small or technically challenging new fields”, or fields where production is diminishing.
Since the Chancellor, George Osborne, took up office he has handed out a further five tax breaks to the oil and gas industry worth well over £3bn. These include:
- October 2012 - Planned tax regime to encourage investment in shale gas
- September 2012 - Brown fields allowance
- July 2012 - Shallow water gas fields
- July 2012 - Decommissioning relief deeds
- July 2012 - UK Guarantees
- July 2011 - Ring Fence expenditure supplement
Furthermore, the Government is entering into contracts with oil and gas companies to guarantee the basis on which tax relief for decommissioning will be available.
These contracts take the form of Decommissioning Relief Deeds (Deeds) which will be signed between the Government and eligible companies. Any company that has carried on a ring fence trade, and the associates of those companies, are eligible to be party to a Deed.
The package of measures provide companies with greater certainty in respect of decommissioning tax relief and allow them to adopt post-tax securitisation arrangements for the future costs of decommissioning assets on the UK continental shelf (UKCS).
This package supports the Government's objective of maximising economic production of oil and gas reserves in the UKCS. The package aims to achieve this by providing greater certainty over the availability of decommissioning tax relief.
This should enable companies to provide for decommissioning costs on a post-tax rather than pre-tax basis and so removes barriers to the transfer of licence interests and increases capacity for additional investment in the UKCS.
PIM - Any other points?
Some of the key remaining points include the limited resources within operating companies and EPC's to execute and also the limited availability of drilling rigs, FPSO's etc. The are also issues with project overruns - cost and schedule
The global nature of energy-related automation projects increases the need to adapt and collaborate across boarders. Innovation is also required to enable collaboration, subsea technology, enhanced oil recovery, cyber security.
CPI replacing 'troublesome' seal system
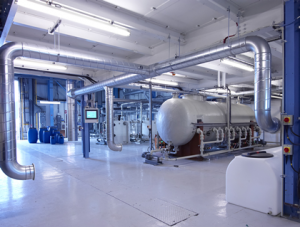
The Centre for Process Innovation Ltd has recently finished accepting proposals for a contract covering thesupply, installation and commissioning of a fermenter seal system
Furthermore the seal system vendor should identify any steps or checks which have to be carried out by CPI to achieve and sustain this level of reliability.
The vessel is used for biofermentation and uses standard CIP chemicals (NaOH) to clean. The steam and air systems are clean. The fermenter is cleaned in place after every campaign.
Sterilisation of the fermenter and the seal is a requirement before every batch. This is carried out using locally generated low pressure (2barg) steam at 133°C. Sterilising of the seal is carried out with the agitator stationary.
A bursting disc for 5barg is fitted. Operating pressure is normally in the range 0.5barg to 1barg. A process trip is set at 2.4barg at which point the exhaust bypass opens.
Pentair targets desalination projects
"Our proprietary membranes, membrane housings, pumps, valves, controls and filters work together to create highly efficient, integrated solutions for a variety of customer needs," he claimed.
Pentair is providing equipment and expertise from both its Valves & Controls and Filtration & Process businesses for the planned desalination plant, which will supply fresh water to the city's five million residents.
Asia is changing the market place for UK machine builders
Article by Amaechi Oduah, marketing manager, Mitsubishi Electric UK:
Wage and consumption levels are rising in the developing economies of Asia, including China. This is opening up an enormous market to UK machine builders and automation engineers who can help them keep production costs down.
At a recent UK Machine Builder conference, hosted by Mitsubishi Electric, strategies for entering Asia and China and building sustainable business were explored.
The great rush into Asia has been underway for some years but until recently the call for manufacturing automation and production machinery had been relatively modest but now, with local labour rates increasing and domestic consumption growing, things are changing fast. In China there is a further twist in that the senior figures of national government are giving way to new leaders who are charged with growing and developing the internal economy of the country – and where China leads, its neighbours are likely to follow.
Throughout Asia much of the recent economic development has been around coastal ports, which provide easy access to export markets. In China development has concentrated on the eastern seaboard, leaving the vast interior to follow in later years.
When people leave agriculture to work in new manufacturing industries, they also move into urban environments where they were unable to grow their own food. This results in them buying food and the rise of retail activities, which quickly develops into the consumption of other goods and services too. Thus demand for manufactured goods and consumables develops alongside the export side of the economy.
This has been apparent in the Asian economies, where naturally wage levels have also increased. It was also inevitable that as industry developed it would be impossible for these countries to produce enough engineers, other professionals and skilled workers.
Economists call this the Lewis Turning Point, where people are no longer willing to work for very low wages because they have opportunities to change to higher paid jobs. In this way, Asia’s eventual need for automated production was predictable and put simply, its time has come.
It is also worth noting at this point that the vast interior regions of China are now developing too. They are some years behind the coastal region but their development will be quicker and more assured, so over time they will catch up.
Slowdown
There has been some worry that Asian growth has slowed in recent years. But to put this into perspective, the main engine, China, has slowed to 8 per cent! In the well developed coastal centres growth is down to 5% and 65% of its economy is now service, an indicator of a maturing economy – and an increasing need for automation!
In a developing country there is inevitably some resistance to importing goods and services. Furthermore the amount of help available to companies for translations, currency exchange, tariffs, visas etc will also be low and there is probably a culture of wanting to ‘buy local’. So in order to win business in Asia and China, overseas companies must have a strong USP or specialism.
Robert Doak, a conference speaker from UK Trade & Investment (UKTI), says that British companies may have their own technical USP but that collectively they are also very good at combining products and service/support:
“Some countries can supply excellent goods; others sell intellectual expertise. But few can achieve the goods and service mix of the UK,” he says. “This is a tremendous strength for machine builders, whose goods will probably need commissioning, regular servicing and frequent redevelopment to adapt to changing end-user demands.”
Doak is also keen to stress that exporting halfway around the world is not the sole preserve of big companies. “There are many opportunities for SMEs, and once established in China a steady stream of work is likely to develop. Getting set-up initially can seem dauntingly complicated, but good initial research and exploratory visits are the first steps. Then there are layers of help available from UKTI, trade associations, business councils, export agencies, all of which are invaluable.”
Another point raised by Doak was that many UK companies think only of China and forget its expansive neighbours, which also need the goods and services of international machine builders. The 10 or 12 nations south of China form a significant sized market, with a combined GDP (gross domestic product) of about US$2trillion (about one-third the size of China or four times the size of the UK). Also in the region are Japan (GDP US$5.5trillion) Korea (US$1trillion) and Hong Kong (US$0.25trillion), all of which are potential markets. Collectively Asia has a GDP comparable to the USA or the EU (US$15-17trillion).
Speaker Stewart Ferguson from the China-Britain Business Council focussed on China’s vast economy. He pointed out that it is not a unitary market, but that the different regions are semi-autonomous, and often culturally very different.
“The language of business throughout China is Mandarin,” he says. “But the local accents and dialects can be so pronounced that they are effectively different languages – even the Chinese sometimes have difficulty understanding people from other regions. There are also major differences in culture, attitudes and manners that you have to allow for if you travel across the country.”
China has a bewildering mix of private companies and state-owned enterprises. Most Chinese companies will only pay in the local currency and will make no effort to help suppliers import their goods. But it is worth noting that China also has many resident non-Chinese companies, so UK machine builders may find it easier to deal with or through these rather than setting up their own distribution arrangements.
UK companies also need to think about how they are going to repatriate their money out from Asia and to make sure they are able to cope with currency fluctuations. There is also the issue of local regulations and protecting intellectual property rights.
Another speaker was Grant Collier from the PPMA Group of automation-focused trade associations. His organisation is very pro-active in helping companies set up in China and has formalised procedures into its three-tiered Dragon Service.
“Our Silver Dragon provides support services, such as market overview research, translations, media contacts,” he says. “With Gold we make introductions, arrange business tours and build contact networks.
“Platinum is what really set us apart. We run an office in Shanghai and will recruit and employ people for clients. They have tenancy in our office and we manage their activities on your behalf. Thus we remove just about all the risks from that initial setting up period.”
Mitsubishi Electric in Asia
Partnerships key to opportunities in China
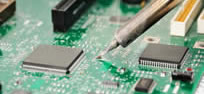
Despite a fall-off in its overall economic growth, China still offers huge opportunities for automation product suppliers – especially those that most understand how to do business in this very fast-changing market.
This was the message from speakers at the CC-Link Partner Association's ‘Gateway to China’ conference, which explored the opportunities and pitfalls for UK companies seeking automation business opportunities in the country.
During the event, staged 24 Sept at Mitsubishi Electric's Hatfield, UK base, Gambica's industrial automation sector head Steve Brambley highlighted current trends in China, which represents 43% of the £50-billion market for all types of automation products in the Asia/ASEAN region.
Citing a batch of recent market reports – from ARC, IMS and Global Automation Research – Brambley said that "while China’s industrial growth is predicted to continue slowing, there is what seems to be an inexorable increase in the growth of all types of automation."
Looking at the process sector specifically, Brambley cited figures showing how China's market for process instrumentation and automation products was set to reach $6.4 billion by the end of this year – representing a compound annual growth rate of 9% over the last 10 years.
On the other hand, while the long-term indicators for sales in the Asia-Pacific region all point upwards, industry should not expect to see a return to prolonged double-digit growth.
As the Gambica expert also concluded: "There is still time to build a market position [in China] from the UK, but you need to be quick."
Since a slowdown in the first half of 2012 – with only 3.7% growth in overall revenue from industrial automation equipment – the market has been in pick-up mode, reported John Browett, general manager of the CC-Link Partner Association Europe. The industrial automation sector set to grow by 6.2% in 2013.
In China the per capita energy use is still a long way behind most of Western Europe, meaning the potential for growth is still huge – meaning huge opportunities for European
But, said Browett, given "the sensitive current economic climate, many Asian companies are taking a more careful approach to investment; they are becoming more demanding towards their suppliers and making more enquiries before purchasing."
Meanwhile, according to IHS, several Chinese manufacturers are currently developing products which are in direct competition with the ones provided by Western suppliers of industrial automation.
These are only a few of the obstacles facing European vendors who want to penetrate the Asian market to change the way they do business, said Browett.
"Flexibility and the ability to respond to very specific demands are becoming essential factors when dealing with the Asian market," he concluded. "Being able to offer technologies and products which are compatible with the needs of Asian clients is [also] a must."
New entrants will also need to understand business relationships and how decisions are made within Chinese companies, said Lutz Berners, president of Stuttgart, Germany-based Berners Consulting, which helps Western companies enter the market.'Companies that do best in China are those that manage to stick to their core competences, while also paying attention to the nitty gritty of business frelationships there,' he advised.
For example, Berners said the emphasis in China is on in-group loyalty and forming relationships before the legal, technical or business case for a contract or project is hammered out. This he noted, was the complete opposite of what companies are used to in Europe.
"For Western companies, therefore, it is very important to have someone, for example, a trade association or other industry support body to bring them into the relationship," said Berners.
When it comes to actually buying equipment, the fast-changing nature of markets in China today mean there is less emphasis on long-term planning.
"People have a two-to-three year horizon [when buying} machines," said Berners, noting that this can pose a challenge for companies competing against suppliers of cheaper or lower-specification products.
Yokogawa advances safety system capabilities
Yokogawa Electric Corp. is releasing a new version of the ProSafe-RS safety instrumented system and has enhanced the DPharp EJX multivariable transmitter.
Target markets and applications include emergency shutdown and fire prevention/suppression, production, and other applications in process industries such as oil, natural gas, and petrochemicals.
The new Version R3.02.10 is said to offer improved functions for upstream oil and gas,, while the DPharp EJX multivariable transmitter has been enhanced to improve connectivity with ProSafe-RS.
In upstream oil and gas processes, wells and pipelines are typically distributed over a wide area and often have limited space for the installation of equipment. To improve operational efficiency and reduce hardware costs, there is a need to consolidate the functions performed by control and safety instrumented systems.
In response to these needs, the enhances system provides AGA (American Gas Association) gas flow rate calculation, Modbus communications between DPharp EJX and ProSafe-RS for gas flow rate calculation, and support for many networks used in oil and gas upstream applications.
To monitor and control gas wells and pipelines, gas flow rate compensation is required. The in-situ gas volume needs to be compensated to a standard volume because the gas volume rises or falls significantly depending on the process temperature and pressure.
This compensation is usually carried out by a control device or dedicated flow computer. For customers in regions such as the Americas and the Middle East who wish to eliminate the need for such dedicated devices, Yokogawa has incorporated a gas flow rate calculation function in ProSafe-RS R3.02.10.
ProSafe-RS, which is certified for use in SIL3 applications, is therefore now suitable for use both in safety instrumentation and monitoring & control. SIL is a standard relating to the functional safety of electrical and electronic equipment that was established by the IEC.
Safety integrity levels (SIL) are defined by the IEC61508. At SIL3, the risk factor for a plant where safety measures are not in place has been reduced to a range from 1/1000 to 1/10000.
To compensate the gas flow rate, differential pressure, static pressure, and temperature must be measured. The DPharp EJX multivariable transmitter is a sensor that can measure all three of these variables.
Yokogawa has added Modbus protocol support to the DPharp EJX multivariable transmitter. This sensor can thus be used together with ProSafe-RS to perform highly reliable and accurate gas flow rate calculations.
The Modbus protocol - an industrial communications protocol developed by the US company Modicon – now owned by Schneider Electric – is widely used in upstream oil and gas processes for communications between sensors and gas flow rate compensation devices,
A variety of networks are used to link ProSafe-RS at the site to the Yokogawa FAST/TOOLS SCADA system. Some networks use high-bandwidth optical fibre, while others rely on low-bandwidth wireless links.
By optimising the frequency of data collection and the volume of transmitted data, ProSafe-RS R3.02.10 can now link up with other systems using low-bandwidth media. This improves maintenance efficiency by enabling remote engineering. Essential data is stored on the ProSafe-RS controller, ensuring continuity in the event of a network failure.
Yokogawa combo offers smarter sensing
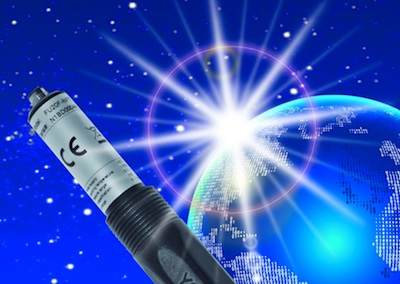
Yokogawa has combined its pH and ORP sensor technology with integrated digital communications and signal-processing circuitry to produce a range of self-contained smart sensing solutions.
The SENCOM smart sensor is designed to enable improved maintenance management and diagnostics. The unit has its own permanent calibration memory, allowing it to be calibrated in the lab before returning it to the field.
The sensors are said to maintain specific measurement and calibration data and this information can be exchanged between the sensor and a transmitter such as Yokogawa’s FLEXA family. Dedicated SENCOM SPS24 management software is also available for use with a Windows PC.
Utilising historical measurement, calibration and diagnostic data from the sensor, the SPS24 data management system provides users with the tools necessary to predict maintenance and calibration frequency and estimate sensor life. The calibration information can be managed, analysed and conveniently documented by the SENCOM SPS24 software.
Another benefit, says Yokogawa, is that the unit makes it possible to monitor sensor aging in real time using a sensor “wellness” feature. Users can also carry out reference impedance measurements for the early detection of diaphragm clogging.
Yokogawa adds that the new SPS24 SENCOM PC software makes it possible to optimise the performance of pH/ORP sensors for enhanced reliability and process safety.
The software, it explains, allows the operator to continuously monitor pH/ORP sensor measurements, perform calibrations and configure the various parameters, keeping track of up to 100 different SENCOM sensors.
The first SENCOM sensor to be introduced in Yokogawa’s new family is a pH/ORP sensor, targeting applications requiring easy, accurate and reliable measurements.
Future sensors will target the full spectrum of pH and ORP applications in the power, utilities, petro-chemical, chemical and pulp & paper industries.