
Administrator
Aker wins largest UK subsea contract
Aker Solutions has won a contract worth up to $440 million to deliver the subsea production system for an oil field development in the UK North Sea. The company did not name of the field or the operator.
The deal, which is Aker's single-largest subsea contract in the UK, includes the delivery of 25 subsea trees and six template manifolds. It also encompasses associated controls, wellheads and tie-in equipment for one of the biggest projects currently under development in the UK North Sea.
According to Aker, the order includes subsea technologies that are new to the UK market, including manifolds and trees that can enable the use of hydraulically submersible pumps to improve oil recovery and flow assurance.
The Norwegian company will also provide diverless horizontal tie-in systems and slim line rigid lockdown wellheads for the development.
First deliveries are scheduled for the first half of 2014. Aker's main office at Fornebu in Norway will handle central management, engineering and procurement for the project.
Its Tranby facility outside of Oslo will manufacture the subsea trees, while production of the manifolds and system integration testing will be carried out at the company's offshore yard in Egersund on the west coast of Norway.
The company's subsea operations in Aberdeen will manufacture the control systems and wellheads and provide lifecycle-support services.
Motors for world's largest natural heat-pump system
MV motors from ABB are being used in the world's largest district-wide natural heat-pump system.
Based on technology from Star Refrigeration of Glasgow, the system will provide over 13MW of heat for Drammen, near Oslo, via a network of underground pipes.
The heat pump extracts heat from sea water by raising the temperature of an ammonia refrigerant via a heat exchanger.
The now gaseous ammonia is then compressed by a motor driven compressor, heating it to around 90°C. The heat from the ammonia is then transferred via another heat exchanger to the hot water supply system.
Six ABB 11 kV motors will be used to drive the ammonia compressors, three of 660 kW and three of 1250 kW.
AkzoNobel gains top water-saving certification
AkzoNobel’s UK decorative paints business has gained the Carbon Trust Water Standard, becoming one of only six companies in the world to receive the certification since its launch in February – joining major names such as Coca-Cola Enterprises and Sainsbury’s.
The award recognises reductions achieved through a huge programme undertaken to cut water usage at AkzoNobel. Measures have included the introduction of rainwater harvesting to feed manufacturing processes and a programme to reduce water leakage across plants.
AkzoNobel has also streamlined production processes reducing the number of cleaning cycles needed and increased storage capacity for wastewater at manufacturing sites. The latter step has meant that more wastewater can be incorporated into product formulations, cutting the need for fresh water.
AkzoNobel is the largest global paint and coatings company. The UK is a key location for the manufacture and retail of its decorative paints, including iconic brands such as Dulux, Dulux Trade, Polycell and Cuprinol.
The company has been ranked in the top three in the influential Dow Jones Sustainability Index since 2007 and was ranked first in the chemicals supersector last year. It also holds certification for carbon reduction from the Carbon Trust.
AkzoNobel's 1,100-employee UK decorative paints business will soon be expanded by the opening of a new site in Ashington in 2014. This plant will exemplify the business’s commitment to sustainability with ambitious plans including ensuring all water is re-used.
“Radical resource efficiency, doing more with less, is central to our sustainability strategy and water reduction is an important part of responsible resource management," said Chris Cook, AkzoNobel’s global sustainability director for decorative paints.
"We have driven down water usage at our plants and we are determined our new plant in Ashington will be the most sustainable paint plant ever with state-of-the-art processes driving down energy consumption and waste.”
Premier Foods to reorganise milling business

Premier Foods is to reorganise its milling business into two parts to strengthen its focus on its third-party customer base, while vertically integrating its remaining milling operations into its baking and grocery businesses.
The company is also planning to close its mill located in Barry, Vale of Glamorgan, by the end of October 2013. The move, it said, would help to align capacity with current market demands.
A new dedicated management structure is to be established to oversee the Rank Hovis third-party business. This will be largely serviced by the company’s sites in Southampton, Manchester and Newbridge.
The remaining mills in Wellingborough, Selby, Andover and Gainsborough will be organised into a vertically integrated flour supply business for the company’s baking and grocery business, said Premier Foods.
Around £1million has been earmarked to improve the capability of the Southampton and Wellingborough sites as part of this re-organisation.
The Barry closure is to be phased over the coming months with final closure expected by the end of October 2013, resulting in the loss of around 43 employees plus a smaller number of local contractors.
“By creating a dedicated structure aligned to our Rank Hovis customers, we will be able to improve further our customer focus and service levels,” said Bob Spooner, managing director of Premier Foods’ bread division and group supply chain director.
“It’s also critical that we take the tough decisions necessary to improve the longer term profitability and sustainability of the milling business by aligning our capacity to market needs.”
“We recognise the impact this proposal will have for our employees in Barry and we thank them for their contribution over the years. However, it’s not possible to continue on the current path given excess capacity in the marketplace.”
Energos taps Atkins for Glasgow EfW project
Atkins has recently been selected by Energos to help deliver an advanced conversion facility as part of Viridor and Glasgow City Council's £146 million Glasgow Recycling and Renewable Energy Centre (GRREC).
The GRREC will divert Glasgow’s domestic residual waste from landfill in line with Scotland's zero waste plan. It will operate a three-step process comprising a Smart Materials Recycling Facility to enhance recycling, anaerobic digestion to capture food and organic material and the Energos conversion Facility to recover renewable energy from post-recycling material that remains.
Under a framework engineering services contract, Atkins is assisting Energos in tendering of the major and long-lead plant items including the furnace and steam turbine generator packages. Once vendors have been selected, Atkins will provide engineering and commercial support.
The power generation plant forms part of the overall Viridor recycling-led clean energy recovery facility at Polmadie.
Energos' element of the project will produce electricity, and potentially heat for district heating, with the electricity used to power the remainder of the recycling facility as well as providing renewable electricity to the grid.
Building work will begin at Palmodie in the summer, with completion expected in early 2016.
Atkins has been involved in a number of energy from waste developments, most recently advising on environmental permitting and waste characterisation for TAQA, the global energy company based in Abu Dhabi.
Should Boris back shale?
For example, in a recent letter to The Times, London mayor Boris Johnson promised to ‘leave no stone unturned or unfracked’ if shale gas is found in London.
In a statement on his company's website, though, David Symons, director at consultancy WSP – a firm with significant international shale experience – responded by suggesting that Johnson was getting a bit carried away:
"Although oil has been found in many areas across southern England – from the Weald basin to even some small finds in north London - the reality is that shale gas is a new science and there’s still considerably uncertainty on where the resources are and whether they are economically viable to extract, " said Symons.
“Rather than big sweeping statements the Mayor could do much better to focus on the elements in the 2020 Vision that are in his control, such as making London a leader in energy efficiency."
Fair comment, I suppose, but the Mayor's robust stand does make a welcome departure from the unfounded scare stories about shale, which are still being peddled by many politicians, scientists and journalists.
Schenck units to convey biomasss at Drax
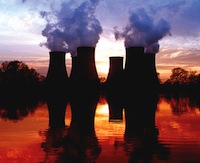
Schenck Process UK, based in Doncaster, has recently secured an order for the supply of new technology for the conveying of biomass material at the UK’s largest biomass conversion project which is underway at Drax Power Station in North Yorkshire.
The company's pneumatic conveying system will play a role in the project that will see Drax convert three of its six generating units to burn sustainable biomass in place of coal.
The Drax biomass storage and handling project includes the use of individual conveying and mill feeding systems, with each conveying vessel having multiple Clyde Process Dome Valves from Clyde Process Ltd – part of Schenck Process Ltd.
This specialised valve was selected for its reliability and is designed to operate up to one million times without the need for maintenance, according to a statement from Schenck Process.
To avoid unnecessary generation downtime during the construction phase of the project, the Schenck Process solution factors in considerations such as the location of the new day silos and conveyors in relation to existing infrastructure thus ensuring minimal disruption to power generation.
Schenck Process said it has worked closely with Shepherd Construction, the main contractor for the project, to ensure that the silo storage, and its associated conveying system, interfaces smoothly with the new conveying equipment.
Dust Control for paper recycler
PM Shotton, one of the UK’s largest recyclers of used newsprint and magazines, has installed a complete dust extraction plant, from Dust Control Systems Ltd, at its new £17-million materials recovery facility (MRF) in North Wales.
Located at the site of the Finish-owned company’s UPM Shotton paper mill, the 250ktpa facility is designed to sort mixed recyclables from kerbside collections such as plastic bottles, cardboard, newspapers and metals.
Around 120kt will be newspapers and magazines, which will provide 20% of the recovered paper used as raw material in the mill’s paper production.
DCS Ltd was contracted to provide a complete turn-key package, including design, supply, installation and commissioning of a material stream dust control system serving drum feeders, sort conveyors, optical sorters and screens.
The DCS installation comprises an externally located filter unit, strategically-sited extraction hoods, interconnecting ductwork and a briquetting press.
The ATEX compliant filter is a high-efficiency Schuko EcoVar 04 series 2030 modular unit, which has a filter surface area of 677m2, and a total airflow capacity of 60,000m3/hr.
The filter is fitted with tubular filter elements designed for duty on fibrous dusts, and its 75kW fanset provides 24/7 extraction. Collected dust waste is discharged pressure-free from the filter hoppers, via a heavy-duty conveyor and rotary valve, directly into a pre-receiving briquetting hopper.
Extracted dust is then screw fed to the briquettor which is capable of pressing up to 100kg of extracted dust per hour to form 60mm diameter briquettes to be used as boiler feed. Return air ductwork is provided to allow warm cleaned air to be returned to the building in winter and discharged to atmosphere in summer by the manual operation of summer/winter dampers.
Variable speed technology is employed to control and vary fan speed should there be a need to increase or decrease extraction efficiency to different areas of the plant. Air volumes are automatically adjusted when manually operated dampers are closed and re-opened.
DCS worked very closely with UPM Shotton throughout the specification, supply and installation process, and also with Machinex who supplied and installed the recycling plant, said John Barker of DCS Ltd.
"UPM required clearly defined activity schedules to match their own building programme," he said. The contract also included final warranty tests based on HSG 258 (Control of Airborne Contaminates at Work) plus visual tests which were carried out using a high intensity light beam.
(Image source: DCS)
Boris and shale fever
While most in the process sector have welcomed the UK government's belated backing for shale gas, some engineers now see a need to manage expectations of some of the more enthusiastic converts.
For example, in a recent letter to The Times, London mayor Boris Johnson promised to ‘leave no stone unturned or unfracked’ if shale gas is found in London.
In response, though, David Symons, director at consultancy WSP, which has international shale experience, suggested that Boris was getting a bit carried away with the shale fever:
"Although oil has been found in many areas across southern England – from the Weald basin to even some small finds in north London - the reality is that shale gas is a new science and there’s still considerably uncertainty on where the resources are and whether they are economically viable to extract, " said Symons.
“Rather than big sweeping statements the Mayor could do much better to focus on the elements in the 2020 Vision that are in his control, such as making London a leader in energy efficiency."
"The Vision, quite rightly, commits to retrofitting every badly insulated home in the city – as a way to save energy and be ‘a formidable creator of employment.’
Making London the leader in energy efficiency is far more practical and far more deliverable than big rhetoric which inspires passion but little else.”
Fair comment, I suppose, but the question still remains about how cities like London set about tapping into shale and other energy resources – especially given all the uncertainties over power supply in the years ahead.
Energos for MK energy-from-waste site
Energos has been appointed as technology provider for a thermal conversion facility, as part of AmeyCespa's proposed Milton Keynes waste recovery park.
The proposed project involves a three-stage waste treatment process to treat household waste, using mechanical treatment to sort recyclates, anaerobic digestion and thermal treatment. Start up is scheduled for 2016, subject to the project gaining planning consent.
UK-based Energos' technology would be used at the final process stage to convert any remaining, non-recyclable waste into a syngas. This would be used to produce high-temperature steam that can then be converted into electricity in a turbine.
According to Energos, the facility would be able to process more than 90,000 tonnes of non-recyclable waste and could generate 7MW of electricity.
(Image credit: Race Cottam Associates Ltd)