
Administrator
Process part of €22bn EU innovation plan
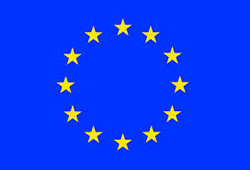
The European Commission, EU Member States and European industry will invest more than €22 billion over the next seven years under a new innovation plan announced by the EC 10 July.
According to the Commission, most of the investment will go to five public-private partnerships (PPPs) in innovative medicines, aeronautics, bio-based industries, fuel cells and hydrogen, and electronics (see below).
Overall, a proposed €8 billion investment from the next EU research and innovation programme, Horizon 2020, will secure around €10 billion from industry, and close to €4 billion from EU Member States, said an EC statement.
Several of the announced PPPs put emphasis on chemical sector innovations and include new processes, increased use of renewable feedstock, recycling and re-use.
Some will leverage existing programmes including Cefic PPPs (BRIDGE (Bio-based and Renewable Industries for Development and Growth in Europe) and SPIRE (Sustainable Process Industry) which that have strategic research and innovation roadmaps and are ready to start.
SPIRE, for instance, is a Cefic flagship initiative to bring together innovative companies from eight industrial process industry sectors committed to innovate not only within their current frames but also to explore synergies between them.
The SPIRE PPP covers areas such as energy use, water, renewable feedstock and process optimisation that are essential for efficiency and competitiveness, according to the industry group.
“The Commission initiative is a major step forward sending a clear positive signal for the process industries to establish innovative approaches that will spur European competitiveness," Gernot Klotz, Cefic executive director for research and innovation.
“These new PPPs set as top priority the need to cross ‘the valley of death’ from research to the marketed solutions our society needs. We must jointly act fast and efficiently to face the challenges of global competition and sustainability goals.”
The five PPPs – called joint technology initiatives (JTIs) – are:
- Innovative Medicines 2 (IMI2): to develop next generation vaccines, medicines and treatments;
- Fuel Cells and Hydrogen 2 (FCH2): to expand the use of clean and efficient technologies in transport, industry and energy;
- Clean Sky 2 (CS2): to develop cleaner, quieter aircraft with significantly less CO2 emissions;
- Bio-based Industries (BBI): to use renewable natural resources and innovative technologies for greener everyday products;
- Electronic Components and Systems (ECSEL): to boost Europe’s electronics manufacturing capabilities.
Thomas Swan plans AD power plant

Independent chemicals maker Thomas Swan & Co. Ltd is seeking local approvals to establish an anaerobic digestion (AD) plant on its site in partnership with Hallwick Energy.
Under the plan, Hallwick is to lease land from Consett, County Durham-based Thomas Swan, build and run the plant and sell the energy to the company. Any surplus is to be fed into the national grid.
The AD plant would give Thomas Swan the opportunity to use power which is sustainably produced and less susceptible to ever rising prices, explains Harry Swan, managing director of the company.
"The cost of power is a huge problem for many companies in the UK. We are committed to using renewable energy which is reliable and makes us self-sufficient – reducing our overheads, protecting existing jobs and hopefully, creating new ones," said Swan.
In May 2012, Bridgnorth, Shropshire-based Hallwick Energy announced the start-up of its first AD project. The unit, on a farm near Buntingford in Hertfordshire, was installed to export electricity to the national grid.
This was followed a month later by the company's commissioning of a second 1Mw AD plant. The site, near Dunstable in Bedfordshire was being run on farm-based crops and crop residues as well as some grass silage from nearby Luton Airport.
(image source: Thomas Swan)
Capula to supply controls for Drax bio-units
Capula is to provide the control and automation systems for the new boiler distribution system at Drax Power Station. The award was made by contractor Shepherd Engineering Services (SES)
Drax is installing new receipt, storage and distribution systems are being constructed at its Yorkshire coal-fired power station to help switch to a predominantly biomass-fuelled operation.
Capula was recently been awarded a contract by SES for the provision of the control and automation systems for the new biomass storage facility at Drax Power Station.
The firm will be providing a Schneider-based control solution for the boiler distribution system, which consists of two sections: the common systems and unitised systems.
The common systems will deal with the reception of fuel from storage. The unitised systems will control the eventual transport of the fuel to the boilers of the three converted generating units.
Clarke biogas engines for Tamar Energy AD projects
Tamar Energy has signed up Clarke Energy of Liverpool, UK, to supply combined heat and power systems for four anaerobic digestion projects in the UK.
The order is for six biogas engines with a total renewable power output of 8MWe to Tamar Energy’s anaerobic digestion plants at: Holbeach, Lincolnshire – 1 x J420, total electrical output 1.5MW; Retford, Yorkshire – 2 x J420 (3.0MW); Farleigh, Wiltshire – 1 x J420 (1.5MW); and Halstead, Essex – 2 x J416 (2.2MW).
The four of GE Power & Water’s J420 and two J416 containerised Jenbacher gas engines are fitted with heat exchangers to facilitate cogeneration, recovering heat as hot water for use in the heating of the digesters and pasteurisation.
The projects are part of Tamar Energy's long-term aim of building a UK network of 40 plants and producing 100MW of renewable base-load electricity. UK government agencies aim to support the establishment of up to 3-5 Terawatt hours of electricity from anaerobic digestion by 2020.
"Clarke Energy’s technical solution, backed up by the largest network of dedicated gas engine specialists in the UK, were key factors in us awarding these orders," said Dan Poulson, engineering and strategy director of Tamar Energy.
Egdon cleared to drill UK on-shore well
Egdon Resources plc has received planning approval from North Lincolnshire Council to drill an exploratory borehole on Licence PEDL 180 targeting the Wressle prospect in onshore UK in the second half of 2013.
Egdon Resources has a 25% stake in the block and is the operator. The other partners are: Europa Oil & Gas, which has a 33.34% working interest in the block, alongside Celtique Energie Petroleum Ltd (33.33%); and Union Jack Oil plc (8.33%).
PEDL180 covers an area of 100 km2 on the western margin of the Humber Basin in the East Midlands Petroleum Province. The Wressle-1 well will target the highly petroliferous Brigg Broughton anticline trending WNW through PEDLs 180, 182 and 241.
Several oil discoveries have been made along this trend at Brigg, Broughton and Glanford and it also includes the Crosby Warren oil field operated by Europa. The operator estimates Wressle holds mean gross unrisked prospective resources of 2.1 million barrels of oil.
Drilling operations at Wressle are expected to commence in the second half of 2013. The well is targeting multiple prospective sandstone reservoirs in a structurally favourable position near the crest of the Wressle structure within the Upper Carboniferous and will be drilled as a deviated well to a total depth of about 2,300 metres with a maximum offset of approximately 1,250 metres.
"Wressle-1 is the first of up to five wells to be drilled across our asset base over the next eighteen months, each of which has the potential to transform our existing production profile and reserves," said Europa's CEO Hugh Mackay.
With mean gross un-risked prospective resources of 2. 1 mmbo, Wressle is small compared to our Mullen and Kiernan prospects in the South Porcupine Basin, offshore Ireland, and Berenx, the deep gas appraisal project in onshore France.
However, said Mackay, drilling success at Wressle "would generate considerable near term cash flow that we would reinvest into proving up and monetising other highly prospective exploration and appraisal projects in our portfolio."
AstraZeneca selects Cambridge as global R&D/HQ hub
AstraZeneca's new UK-based global R&D centre and corporate HQ will be located at the Cambridge Biomedical Campus on the southern outskirts of the city. By 2016, the new site will house a highly-skilled workforce of approximately 2,000, said an 18 June announcement.
The investment in a £330 million facility in Cambridge is part of the company’s move to create strategic global R&D centres in the UK, US and Sweden to improve pipeline productivity and to establish AstraZeneca as a global leader in biopharmaceutical innovation.
The purpose-built site in Cambridge will bring together AstraZeneca’s small molecule and biologics research and development activity, opening up opportunities to exploit the promise of small and large molecule combinations.
The Cambridge Biomedical Campus will be the new UK home for biologics research and protein engineering carried out by MedImmune, AstraZeneca’s biologics arm. MedImmune already employs around 500 people at Granta Park, to the south east of the city.
The new site will also become the company’s largest centre for oncology research as well as hosting scientists focused on cardiovascular and metabolic diseases, respiratory, inflammation and autoimmune diseases and conditions of the central nervous system.
Work carried out in Cambridge will include medicinal chemistry and high-throughput screening and the facility will accommodate a number of AstraZeneca’s pre-clinical research capabilities.
Other global functions will join the R&D teams at the new facility and Cambridge will become AstraZeneca’s corporate HQ.
The Cambridge Biomedical Campus site is home to leading research, academic and healthcare organisations including the University of Cambridge School of Clinical Medicine, Addenbrooke’s Hospital, the Medical Research Council (MRC) Laboratory of Molecular Biology, the Wellcome Trust-MRC Institute of Metabolic Science and the Cancer Research UK Cambridge Institute.
The AstraZeneca facility will occupy about 11 acres of the 70 acre campus in central Cambridge.
Nestlé to find 20,000 jobs for under 30s
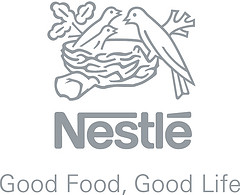
Nestlé plans to help at least 20,000 people across Europe under the age of 30 find employment over the next three years, the company announced.
The “Nestlé in Europe” Youth Employment Initiative will offer jobs and create thousands of apprentice positions and traineeships by 2016.
As part of the new initiative, further details of which will be announced in September, Nestlé will also encourage its European suppliers to offer a job, apprenticeship or traineeship to young people.
Roles on offer as part of the initiative will be across all the different business areas and at all levels within the company – from operators on the factory floor to sales assistants and business management, said Nestlé.
Young people with vocational skills and training are a particular focus of the initiative, as are graduates seeking their first position after university.
“Governments alone cannot resolve the problem of youth unemployment in Europe – companies must play their part,” said Laurent Freixe, Nestlé executive VP and zone director for Europe.
Leatherhead opens DirtyLab

The facility will support and expand the group's existing capabilities for challenge testing by providing an environment that directly replicates a food production area, according to Dr Wayne Morley, LFR head of food safety.
Opening DirtyLab, Dr Paul Cook of the microbiological food safety branch, Food Standards Agency, said: I know from personal experience, having worked in a Food Science laboratory at a university, the challenge of doing experiments on a pilot scale from the benchtop through to full scale production.
Several confidential projects have already employed LFR's DirtyLab services. In addition, a project on pathogens in low-moisture foods, is currently being carried out in the facility; research is being undertaken to systematically establish the heat resistance and survival of pathogens in dry foods such as nuts, seeds, powder ingredients and flavours.
Southern Water adds heat exchanger for poo-power
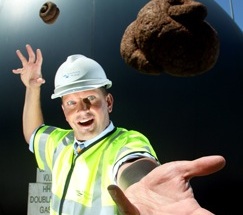
Southern Water has installed a new heat exchanger to help harness poo power at its Budds Farm Wastewater Treatment Works in Havant.
The unit has been added to the site’s Combined Heat and Power (CHP) plant which captures bio-gas created during the treatment process. This gas, which would otherwise have been burnt off in a flare, is used to produce renewable energy with any surplus exported to the National Grid.
The heat exchanger recovers heat from the engine and exhaust systems using water which is then used to warm the treatment tanks, helping speed up the bacterial digestion of the waste.
“This new heat exchanger means we are able to recover even more energy from the wastewater treatment process," Morné Cloete, Southern Water project manager.
“I’m sure people in the Portsmouth area will be delighted that they are helping us minimise the environmental impact of our business, dealing with their business – by generating electricity with poo power.
“CHP plants help us reduce our carbon footprint while also cutting our energy costs and are just one of the innovative ways Southern Water is helping protect the communities and environment in which we work.”
Budds Farm treats flows of around 2,400 litres a second from almost 400,000 people in and around Portsmouth, including Waterlooville, Havant and Hayling Island.
Southern Water recently announced an investment of more than £1 million in a CHP plant to capture bio-gas at its at Bexhill and Hastings Wastewater Treatment Works. The site is capable of generating 5.1 Gwh of electricity.
As well as generating electricity, the CHP plant also recovers heat from the engine and exhaust systems via water from heat exchangers. This water is then used to warm the treatment tanks to speed up the bacterial digestion.
The projects are part of the company’s multi-million pound investment in carbon mitigation and energy efficiency schemes between 2010 and 2015.
These are to help Southern Water reduce its carbon emissions and contribute to its target of generating 20% of its energy usage from renewable sources by 2020. The company currently has the capacity to generate 15% of its energy from renewable sources.
Southern Water already harnesses poo power at 13 of its wastewater treatment works through the use of CHP plants.
The installation at Bexhill and Hastings WTW was carried out by Southern Water supplier Cogenco.
(Image from Southern Water)
Improvement project saves £10m at SABIC UK site
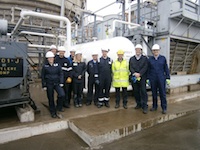
SABIC UK Petrochemicals Ltd expects annual productivity gains of over £10 million following an improvement programme, led by Reliable Manufacturing, at its ethylene liquefaction plant on Teesside.
The programme has delivered a "dramatic turnaround" after nearly 20 years of under-investment by the previous owners at the 700-employee site, according to Reliable Manufacturing – a change-management company, based in Warrington, UK.
After just 18 months, the Teessite site has noted a major reduction in plant breakdowns and performance issues. Further savings of over £1 million a year were delivered through better communications between Teesside and SABIC's other main UK site at Wilton, near Redcar.
'Asset care improvement' teams have uncovered issues making great efficiency savings, which on just one propylene dryer is estimated to be in excess of £400,000 a year, a statement from Reliable Manufacturing explained.
“We’ve managed to achieve reliable production week after week, despite the plants age and without any significant investment,” said Wayne Alexander, former senior operations manager. “It’s about the teams operating the plant correctly, being slick at what they do, and working to plans and targets.”
“Our best results are in what have traditionally been our worst months, so the performance is stellar, especially if we can lock it in going forward; that’s the next phase of the project," added Alan Wasson, engineering director.
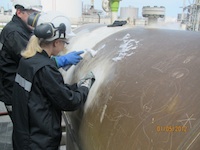
Chiller rejuvenation work
An important aspect of the project was winning the support of the "previously disenfranchised workforce," Reliable Manufacturing's statement continued.
This, it said, involved adopting an approach to "defrost the existing culture" and establish a new one of ongoing continuous improvement. Employees, thereby, got behind the project, with an estimated 75% of process team members involved in some way.
“It’s about having a workforce that’s really engaged and aligned with where the business needs to go and seeing their job as one of continuously improving business peformance,” said Mike Ducker, manufacturing director.
SABIC UK Petrochemicals is part of the European operations of Saudi-owned SABIC – one of the world’s largest manufacturers of chemicals, fertilisers, plastics and metals.