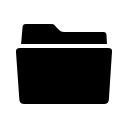
Uncategorised (4996)
Oil and gas service company, Tracerco, part of Johnson Matthey Plc, has received an Institute of Physics Award for Innovation for its level measurement technology.
The IOP award recognises the company's LevelFinderPlus measuring device, which provides operators with accurate level measurement of liquids in vessels, even in the presence of deposit build up and vapour density fluctuations.The patented technology is said to be the first instrument able to make these measurements and to provide unique insight into vessel operating conditions.
Conventional level measurement systems can have errors of over 40% due to build up and vapour density fluctuations meaning that operators are unable to optimise processes, often leading to significant loss of production and potentially dangerous operating conditions.
The device is designed for liquid level, interface and density measurements as well as solids monitoring in upstream and downstream vessels. It is suitable for the most challenging oil, chemical and petrochemical industry applications.
According to Tracerco, it provides accurate level measurement in the presence of build up, reducing unplanned shutdowns, improved product quality, allowing process optimisation and operator confidence to increase production and maximise throughput.
About Us
Tracerco originated in 1958 as a small research team within Imperial Chemical Industries (ICI) in Billingham, Teesside, UK. From its beginnings, Tracerco has continued to expand its product range and geographical reach, responding to customers' needs and market opportunities. Today, Tracerco is part of the Process Technologies Division of Johnson Matthey and is a world leader in its field. Its innovative range of products and services are invaluable to ensure full optimisation and efficiency of its customer's assets across the oil, gas and petrochemical industry. Our products and services include: radiation monitors, nucleonic instrumentation, process diagnostics, subsea technologies, reservoir characterisation, radiation protection, analytical services and product assurance.
Tracerco is renowned for its expert local delivery and excellent customer service. With over 30 operational offices and 500 people across the world, together with a network of agents and service partners we deliver our products and services to our customers anywhere in the world, whilst still retaining the important aspect of local service, which our customers value. Repeat business from existing customers provides a strong indication that we are providing the right products and services, at the right price with the correct level of customer service and support.
R&D will continue to underpin our ability to deliver innovative technology in the future. Our technical experts are renowned for their professionalism, creativity and expertise in safely applying specialist solutions to a diverse range of seabed-to-surface challenges. The success of Tracerco over the past 50 years can be attributed not only to its pioneering technology but also its ability to work with its clients to develop innovative, cost-effective solutions, which has been a major factor in achieving consistent growth.
For more info: http://www.tracerco.com/
Tracerco, part of Johnson Matthey Plc, has gained a £1 million grant from the ‘Let’s Grow’ programme – part of the £30 million Regional Growth Fund (RGF). The grant will be used to build a new R&D facility in the Tees Valley Enterprise Zone.
Tracerco, based in Billingham, already employs more than 150 people across the Teesside area are expected to create a further 50 new jobs as a result of the development.
The £8.6-million Measurement Technology Centre will take 12 months to complete and will generate a custom-made facility for Tracerco’s R&D team.
The facility will allow the company to more efficiently bring to market new innovative technologies for the world’s oil and gas industry, according to a 5 Aug press statement.
The Centre will include testing facilities for Tracerco’s instrumentation and subsea services. This includes a state of the art underwater testing tank, essential for the development of Tracerco’s rapidly expanding range of subsea products and services.
“This will be the platform for innovation for Tracerco, growing our Measurement Instruments business for the next decade," said Andy Hurst, managing director of Tracerco. "It will support the development of more unique and special diagnostic devices, to maintain our position as world leaders in our sectors.”
Tracerco recently received an Institute of Physics (IOP) Innovation Award, for its LevelFinderPlus measurement instrumentation.
The device is said to be unique in providing process industry operators with an accurate measurement of liquid level in their vessels, even in the presence of deposit build up and vapour density fluctuations.
About Us
Tracerco originated in 1958 as a small research team within Imperial Chemical Industries (ICI) in Billingham, Teesside, UK. From its beginnings, Tracerco has continued to expand its product range and geographical reach, responding to customers' needs and market opportunities. Today, Tracerco is part of the Process Technologies Division of Johnson Matthey and is a world leader in its field. Its innovative range of products and services are invaluable to ensure full optimisation and efficiency of its customer's assets across the oil, gas and petrochemical industry. Our products and services include: radiation monitors, nucleonic instrumentation, process diagnostics, subsea technologies, reservoir characterisation, radiation protection, analytical services and product assurance.
Tracerco is renowned for its expert local delivery and excellent customer service. With over 30 operational offices and over 300 people across the world, together with a network of agents and service partners we deliver our products and services to our customers anywhere in the world, whilst still retaining the important aspect of local service, which our customers value. Repeat business from existing customers provides a strong indication that we are providing the right products and services, at the right price with the correct level of customer service and support.
R&D will continue to underpin our ability to deliver innovative technology in the future. Our technical experts are renowned for their professionalism, creativity and expertise in safely applying specialist solutions to a diverse range of seabed-to-surface challenges. The success of Tracerco over the past 50 years can be attributed not only to its pioneering technology but also its ability to work with its clients to develop innovative, cost-effective solutions, which has been a major factor in achieving consistent growth.
For more info go to http://www.tracerco.com
Northumbrian Water has added four new centrifuges and a complete spare rotating assembly’s at a new energy-from-sludge facility serving its Bran Sands sewage treatment works in Teesside.
The project was a part of the overall £33-million scheme which uses anaerobic digestion to treat sludge from the wastewater treatment works, generating biogas which is used onsite in the CHP unit.
The centrifuges – Hiller Decapress model DP76–402 VAHY units – and spare assembly were supplied by MSE Hiller, via JN Bentleys
The Northumbrian Water project used CAMBI thermal hydrolysis process (THP), using heat and pressure to break down cell walls increasing enzyme hydrolysis and therefore digestion rates. This is said to lead to halve volume of sludge produced and significantly increase biogas quantity.
The new plant generates some 4.7 MWe from biogas which is used to power the treatment process. This has reportedly reduced the plant's reliance on natural gas to less than 10% of its former figures, aiding the path to become self-sufficient for energy.
Two of the new centrifuges are used to pre thicken sludge prior to the THP plant providing a controlled discharge of cake at 18 % dry solids at flow rates of up to 100 m3/hr each, explains MSE Hiller.
The HMR5000 control system and hydraulic scroll drive enables the machine to counter for variances in feed dry solids and continuously optimises machine performance, the supplier added.
Post THP the digested sludge is dewatered at flowrates of 35 to 70 m3/hr using two of the Hiller DP76-402VAHY centrifuges to a cake of over 30% dry solids. It can then be disposed off site as a Class A bio solid with no detectable pathogens and as a valuable agricultural fertiliser.

Energy efficiency will be a major focus for Mannheim, Germany-based Crop Energies AG as its works to improve the performance of its newly acquired bioethanol facility in the UK.
As a member of Südzucker group, one of the largest sugar producers in the world and a multinational food producer, CropEnergies seems to have access to the funds and expertise needed to make Ensus profitable.
Ensus started up its bioethanol plant in early 2010, employing around 100 people. However, the operation had to be halted a number of times due, it said, to commercial and regulatory issues affecting the biofuels market.
But, while £50 million has been earmarked for investment in the UK bioethanol site, the main priority at the moment is to get the plant back up and running, according to Dr. Marten Keil, COO of CropEnergies AG.
"There will be some investments during this phase, such as maintenance, early optimisations and building up working capital," said Keil. "Later on we plan to invest in increasing capacity utilisation and - and this is a focus in all CropEnergies plants – we want to optimise the energy efficiency."
Crop Energies operates three large bioethanol plants in Europe and has built up significant experience in introducing improvements regarding efficiency and capacity utilisation at each of these facilities.
"Our know-how does not only stretch to running plants, but along the whole value chain," added Keil. "Over the years, we have built very good partnerships with our suppliers and customers at each of our plants.
"An additional asset of CropEnergies is ... risk management which has kept our plants running even when the market conditions were difficult. We want Ensus to benefit from this knowledge."
Asked if there were there any plans to introduce changes to the processes or capacities of the Ensus site, Keil said: "There will be some improvements, but we are not planning any major changes in technology at the moment.
"Firstly, we want to commission the plant and run it at capacity. We are looking into some possibilities, but there are no specific plans about capacity expansion at the moment."
From its three production facilities in Germany, Belgium and France, CropEnergies produces around 700,000 cubic meters of bioethanol per year, and 500 kiltonnes per annum (ktpa) of protein food and animal feed products.
The acquisition of Ensus has increased CropEnergies' bioethanol production capacity to more than 1.2 million cubic metres a year. The UK site has an annual capacity of 350ktpa of dried protein animal feed and also supplies carbon dioxide for use in the food and drinks industry.
The programme targets the increase of the processing capacity to 7 million tons/year, the increase of the refining yield as well as the improvement of the product quality and the reduction of the environmental impact.
Rominserv has carried out similar projects within Rompetrol's refineries Petromidia Năvodari and Vega Ploieşti – reaching a capacity of 5 million tons at Petromidia - the biggest in Romania.
In the first stage, the Romanian company will ensure the project and the procuring of materials and equipment for the construction of new installations, as well as for the upgrading of the existent ones.
During 2014, Pavlodar refinery will study the launching of the second phase of the project, which aims to improve the yield of the crude and increased production of high quality fuels. This phase is expected to be completed during 2018.
The modernization program includes the revampl of 10 plants: Crude Distillation Unit, Vacuum Distillation Unit, Kero Hydrotreater, Diesel Hydrotreater Unit, Merox, Naphta Hydrotreater, Vacuum Gas Oil, Catalytic Cracking Unit, Catalytic Reforming Unit, Utilities and Off-sites.
New facilities will also be built: Penex isomerisation unit, Sulphur Recovery Unit, Sour Water Stripping, Amine Regeneration Unit and Diesel Hydrotreater and Dewaxing.
The Pavlodar refinery, situated in the North-West of the country, was built in 1978, being designed for the processing of the Siberian oil. A member of KazMunayGas since 2009, is the biggest oil production unit in Kazakhstan and the most modern in Central Asia. In 2012, Pavlodar refinery processed 5 million tons of oil.
Rompetrol is owned by Kazakhstan national oil and gas company KazMunayGas and is present in 12 countries. The majority of its assets are in France, Romania, Spain and South Eastern Europe.
With annual sales of around $11bn in 2012, Rompetrol is involved in refining, marketing and trading activities, as well as in exploration and production activities, oil and industrial services.
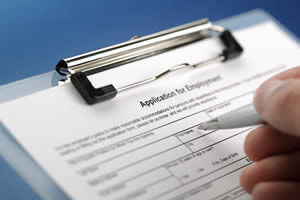
Saudi Arabian Mining Co. (Ma’aden) has recently awarded an EPC contract for the first major project in the development of its world scale Wa’ad Al Shammal phosphate complex.
The project includes mining and processing plants at Wa’ad Al Shammal Mineral Industrial City, as well as ammonia and phosphate and compound fertiliser facilities at Ras Al Khair.
Ma’aden on 9 July issued an award to Daelim Industrial Co Ltd (OOK) & Daelim Saudi Arabia Co Ltd (IK) to build the ammonia plant at Ras Al Khair. The $825m (SAR 3.09bn) award covers detailed EPC of the 1,100ktpa ammonia plant, which is due for completion in late 2016.
The investment cost of the entire phosphate complex is estimated at SAR 26bn, of which approximately SR 21 billion will be invested in the King Abdullah Project for the Development of Wa’ad Al Shammal. The project will double Ma’aden’s phosphate production and improve its access to key global markets.
The new facility is expected to commence in late 2016 with a total capacity of about 16,000ktpa
The facilities are to produce, as finished product, approximately 3,000ktpa of fertiliser products, as well as about 440ktpa of downstream products including purified phosphoric acid, sodium tripolyphosphate, and calcium phosphates used in the manufacturing of animal feed.
Apache Corp. said its third well in the Bacchus Field in the UK sector of the North Sea has pushed field production past 17,600 barrels of oil per day (bpd). Apache has a 50% stake in the field. The Bacchus B-1 development well, which commenced production in July, currently is producing 9,400 bpd.
Apache logged 2,057 feet net oil pay along a horizontal completion segment in high quality Jurassic-aged Fulmar sandstone in the field's western fault block. Oil from the Bacchus Field is produced through a subsea tie-back to Apache's Forties Alpha platform.
Following its recent success at Bacchus, Apache has extended its current Forties 3-D seismic survey area to cover other Jurassic development and exploration targets in Apache licenses in the Bacchus area. The seismic survey is expected to be completed in September.
Apache has brought three new fields — Bacchus, Maule and Tonto — on production in the Forties area since 2009. All three developments qualified under the UK government's small field allowance system, which provides economic incentives for operators to bring these discoveries into production.
"Utilising existing infrastructure within the Forties Field area enables Apache to bring these smaller discoveries on production in a cost-effective manner," said James House, region VP and managing director of Apache North Sea.
"A little more than a year after first production, Bacchus has produced 3 million barrels of oil and has already paid out."
(Image: © Apache)
Arla is to close its dairy and distribution facility at Ashby-de-la-Zouch in April 2014, and transfer volume to its near-complete, new mega-dairy in Aylesbury.
The proposed closure in April 2014, could mean the loss of up to 370 jobs, the company said 31 July.
The one-billion-litre dairy in Aylesbury is on track to be processing milk commercially by autumn and volumes are ahead of original expectations, according to Lars Dalsgaard, head of Arla UK’s supply chain
“We intend to maximise the use of our well-invested dairies, complemented by our new, cutting edge, processing facility in Aylesbury, to meet the requirements of our customers,” said Dalsgaard..
Arla UK has a milk pool of 3.2 billion litres and is looking to expand its supply by a further 500 million litres by 2017.
(Related story: World's greenest dairy))
INEOS Bio starts 'world's first' cellulosic ethanol plant
AdministratorINEOS Bio has started what it believes is the world's first commercial-scale cellulosic ethanol plant. The unit is using its gasification and fermentation technology to convert biomass waste into bioethanol and power.
The $130-million unit is located near Vero Beach, Florida at the Indian River BioEnergy Center – a joint venture project between INEOS Bio and New Planet Energy.
The Centre will serve as a reference plant for future INEOS Bio facilities and for companies and cities interested in licensing the technology for similar facilities, said INEOS.
“We are producing commercial quantities of bioethanol from vegetative and wood waste, and at the same time exporting power to the local community – a world first," said Peter Williams, CEO of INEOS Bio and chairman of INEOS New Planet BioEnergy.
"We expect to spend the remainder of 2013 putting the plant through its paces, and demonstrating full nameplate capacity,” added Williams.
"We remain convinced that the ability to divert waste materials from communities by converting them into competitively priced renewable fuel and power offers an excellent value proposition."
The facility has already converted several types of waste biomass material into bioethanol, including plant and yard waste, and citrus, oak, pine, and pallet wood waste. It will have an annual output of eight million gallons (24kta) of cellulosic ethanol and 6MW (gross) of power.
The Centre has 65 full-time employees and created more than 400 direct construction, engineering and manufacturing jobs during its development.
(Image source: Ineos)

Stobart Biomass Products Ltd has won a new, long-term contract to supply fuel to the Evermore Renewable Energy Plant – a 15.8 MWe recycled wood-fuelled CHP station to be constructed in Derry/Londonderry for start-up by summer 2015.
Stobart Biomass will supply the Northern Ireland plant with over 115,000 tonnes of recycled wood per annum and is contracted to supply fuel for 15 years from the commencement date. It expects to generate revenues of approximately £75 million over the life of the contract.
A key element in enabling a project such as this to obtain funding is the provision of a long-term, reliable, sustainable fuel supply.
Funding for the £80 million Evermore plant has been provided principally by the UK Waste Resources & Energy Fund (UKWREI), a fund managed by The Foresight Group and in which the UK Green Investment Bank plc is a cornerstone investor, Investec Bank plc and Eksport Kredit Fonden.
“Stobart Biomass is seeing increased demand for its range of products across the UK," said CEO Andrew Tinkler, noting that the company now has an extensive pipeline of opportunities in this area.
More...

SSE Hornsea Ltd has awarded Yokogawa Electric Corp. a multi-million pound contract for the upgrade of its underground gas storage facilities at Atwick, UK.
Subsidiary, Yokogawa United Kingdom Ltd is to install the automation group's Centum VP integrated control system to control the gas compressors, and ProSafe-RS integrated safety instrumented system.
The Atwick gas storage facility comprises nine man-made salt cavities that have been leached into a salt layer 1.8 km underground, creating around 325 million cubic metres of gas storage space.
Gas imported to the east Yorkshire site is injected into the cavities for storage. When needed, the gas is then withdrawn from the cavities, dried, and exported to the national transmission system.
SSE is working to extend the life of the Atwick site and allow its use for both peak shaving and longer term storage by improving control, compression, and metering.
The project remit includes ensuring the viability of the asset's control systems and replacing the obsolete control systems with modern, maintainable, and supportable control and safety systems, noted a 16 July press statement from Yokogawa.
SSE's is one of many new construction or upgrade projects at underground gas storage sites in Europe and North America. The extra capacity is required to meet changes in energy supply, including the rise in shale gas production in these regions.
"Yokogawa is targeting the natural gas industry, and we believe that this project will allow us to gain further expertise in gas storage control and safety applications that we intend to share with the entire Group," said Herman van den Berg, president, Yokogawa Europe BV.
Renamed Severn Subsea Technologies Ltd, the Cornwall company is to provide research, development and test facilities to enhance Severn Glocon’s subsea valves capability.
In addition to modelling and engineering design services, the Redruth facility has a machine shop equipped for manufacturing prototypes. It will now be a nucleus for the group's subsea R&D and systems integration activity.
The latest deal builds on the acquisition of LB Bentley in 2012: increasing the scope for new subsea systems developments based on LB Bentley’s small-bore subsea valve technology.
The Cornwall company will operate in tandem with LB Bentley’s R&D team and the Severn Unival Brighouse valve innovation centre.
“Offshore operating conditions are becoming ever more extreme, so hardware engineers and manufacturers need to invest in developing breakthrough technologies, according to Maurice Critchley, chief executive of Severn Glocon.
"At Severn, we’re using intelligence-led R&D to identify potential technology gaps and focus our engineering expertise in the right places," explained Critchley. "Calidus brings a valuable new set of skills to our portfolio as we upscale our R&D efforts.”
Tipton-based Midland Tool and Design has leased three units near its current HQ, following the award of a new contract – stamping motor laminations for a major manufacturer of domestic heating appliances.
The 20% expansion will enable MTD to diversify into a new area of assembly, including spot-welding, and single action press work (up to 125 tonnes), complementing a high speed progressive press shop of up to 200 tonnes.
The firm has invested £50,000 in new machinery, and recruited another five staff, including one apprentice, taking the workforce to almost 50.
“We secured this contract due to the range of services we can provide in-house," said managing director Darren Booton. “We have manufactured a complete set of press tools, which will be used to stamp the laminations and finish and weld the assemblies.
“We are moving into a very exciting phase for the business, with a number of other potential projects on the horizon as well as the expansion. “We can be optimistic about the future.”
Established in 1969, MTD was originally a precision tool-making business and now provides services ranging from prototyping, to product development, to manufacturing. It supplies companies in the aerospace, medical and automotive engineering sectors.
Air Products PLC is reportedly in talks with Falkirk Council about company plans to establish an energy-from-waste plant at Grangemouth in Scotland.
While declining to confirm the plans, an Air Products spokesman said the company "could not deny" such talks – as reported in the Falkirk Herald and based on details received by a local group under the Freedom of Information Act.
Air Products is currently constructing its first plasma-gasification energy-from-waste facility on Teesside, with a second such facility proposed for an adjacent site.
"We are considering further opportunities in the UK, but no specific plans or locations have yet been decided. If and when more information becomes available, we will communicate at the appropriate time," said a company statement.
Image: Installation of the gasifier unit at the Air Products site on Teesside