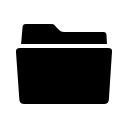
Uncategorised (4996)

National Grid has award ABB a major FACTS (flexible alternating current transmission system) project to help boost the flow of power from Scotland to England – part of preparations to meet the government’s target for 15% of the UK’s energy to be produced from renewable energy sources by 2020.
FACTS covers a group of technologies that enhance the security, capacity and flexibility of power transmission and distribution systems.
The project, to be carried out within the scope of National Grid’s Electricity Alliance Central (EAC) at the Hutton 400kV substation, near Kendal in Cumbria, and associated works at Harker, Heysham, Penwortham and Stanah substations.
The work will involve the design, supply, installation and commissioning of TCSC (thyristor-controlled series compensation) equipment, which is scheduled to go live in 2014. It is the first time that TCSC equipment will be installed in Great Britain.
This is one of a number of infrastructure enhancements on the existing AC power system which together will increase the power transfer capacity between the Scotland and England network boundary by around 1GW.
Series compensation is a technique usually used when transmitting electricity over long distances using alternating current. Series compensation improves power system stability and allows more power to be transferred through existing circuits.
The series compensation equipment to be installed at Hutton substation will use thyristor control to increase the power flow, mitigate sub-synchronous resonance and ensure that the power supply system remains stable.

Yorkshire Water is to become the first commercial user of SewerBatt – a device developed by Acoustic Sensing Technology (UK) Ltd to allow more effective surveying of sewer networks.
SewerBatt is the product of a joint research project between Yorkshire Water's innovation delivery team and the University of Bradford, which started around five years ago.
The project's aim was to find an alternative to traditional camera surveying, which can be time-consuming, and a significant drain on essential resources such as equipment and manpower.
The research work was completed around 18 months ago with the creation of an acoustic surveying device, which can be used by a single person and can "survey" a standard length of pipe in a couple of minutes.
According to Yorkshire Water, in trials the device proved just as accurate in its assessment of the pipe condition and service status as the traditional camera survey.
The University of Bradford has since taken the project forward and a new business was developed, Acoustic Sensing Technology (U.K.) Ltd, which began trading earlier this year.
In July, Acoustic Sensing announced that Goulburn Valley Water with Isle Utilities Pty Ltd and nine other Australian Water Utilities were performing a collaborative trial of the technology, with a view to its widespread adoption in Australia.
However, Yorkshire Water has become the company's first actual customer: taking delivery of six SewerBatt units late last month.
“The potential benefits of the SewerBatt for Yorkshire Water are to allow us to build on our existing surveying of the network to help productively reduce the number of escapes from the sewer network,” said Patrick Killgallon of Yorkshire Water.
The project backers now expect to see a sharp pick up in demand for the new device: citing interest from companies in the US – as well as the UK and Australia.

AB World Foods has added new rotary lobe blower pumps to reduce noise from its existing vacuum pump equipment used in the spice blending plant at its Leigh facility.
The installation of three Busch Tyr pumps from Busch UK Ltd has reportedly reduced noise levels down to 83dba, compared to 98-103dba with previous equipment.
The main aim was to improve the environment for our employees at the plant, which manufactures Patak, Levi Roots and Blue Dragon sauces, according to Tony Marsh, site engineering manager at AB World Foods.
“In this case, cost was not necessarily the issue, rather it was more important to us to significantly improve the noise levels as part of our drive to make our facility a more desirable place to work,” said Marsh.

Kerry Flavours & Ingredients has worked with machine builder SP Filling Systems and Mitsubishi Electric to develop an improved machine for filling catering sized bottles with flavouring syrups for coffee, ice cream and other desserts.
Filling is a critical step in the company's process, as spills and drips can lead to product wastage, spoiled packaging and hygiene issues, according to Colin Jones of SP Filling in Llandrindod Wells in Mid-Wales.
To help provide a system that met the demanding operating specification and was flexible enough to cope with future changes, Jones brought in motion and control specialists from Mitsubishi Electric at an early stage in the project.
"However, the Mitsubishi specialists suggested we look at the company’s MRE servo motor, which met the cost criteria and whose closed loop configuration would lead to guaranteed long term accuracy and easy reprogramming.”
Jones was also surprised at the tech team’s suggestion for a control system, as he had assumed a small PLC for each pump/motor, plus a larger one in a supervisory role.
Viscosity, tendency to foam, drip and dribble, all have a direct bearing on how they are best handled. The shape of the bottles is also important: a clear exit route is needed for the displaced air to avoid bubbles and inaccurate volumes.
For the syrup filler, the Mitsubishi control system consisted of a single Q-00J with one output card, an eight-channel pulse chain driver that controls all the filling axes in one hit with little system configuration or commissioning effort required.
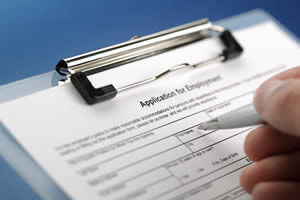
Malton Foods Ltd has gained planning permission to build a biomass-fuelled boiler and turbine system at its site in Amotherby, Yorkshire. This is to provide process steam for its food processsing and research facility, which employs 217 people.
The project involves replacing an existing inefficient coal and oil-fired boilers including the existing chimney stack. Without this the company said the factory would become uncompetitive in terms of competition and energy overheads.
There were some local objections concerning noise levels from machinery delivering wood fuel to the boiler and traffic as the boiler will burn a tonne of fuel an hour.
Ryedale District Council, however, ruled that the biomass boiler would generate less noise than existing boilers, while lorry movements would not be significantly increase.
Approving the project, the planners also cited support for the use of renewable fuels under the National Planning Policy Framework.
Just two technology standards accounted for over 50% of all wireless-enabled industrial automation equipment shipped in 2012, according to a new report from market analysts IHS.
Wireless LAN (WLAN/802.11a/b/g/n) accounted for a 31% share of shipments of wireless-enabled industrial automation equipment, while Bluetooth held 22% of the market. IHS said it expects this dominance to continue over the next few years at least.
The report, entitled 'The World Market for Wireless Communications in Factory and Process Automation'. found the rest of the market populated by a range of mainly 'proprietary technologies' including WirelssHart and ISA100.11a.
IHS predicts the share of the market held by 802.11a/b/g/n WLAN and Bluetooth (both Classic and Low Energy variants) will continue to rise at least through the year 2017.
“There are many other technologies offered by a number of vendors which cater to the industrial market,” said Tom Moore, industrial communications analyst for IHS. “These technologies are usually based either around the 2.4 gigahertz (GHz) band or the lower sub-GHz band, which can offer distance benefits over high frequencies.
"The sub-GHz bands also have an advantage of being free from the busy 2.4 GHz space, which is dominated by consumer products. By moving to this sub-GHz space, the bands are more freely available and can be cheaper to operate in.”
These various proprietary technologies that populate the market are helping promote the adoption of wireless as the individual vendors all push their own technologies. However, having these sundry technologies can make end users cautious to adopt because of the lack of standardisation.
According to Moore, such caution is prudent, given the war between Ethernet/fieldbus that still rages on.
“Users who want to implement wireless want a standard, unified solution they can rely on,” he commented. “This is more difficult with proprietary solutions as there is less scope for interoperability.
"However, there are a number of more widely available technologies, such as Bluetooth, WirelessHART, or ISA, which can answer to this.”
Overall however, the biggest gap wireless has yet to bridge is the perceived reliability of an unstable network.
“Implementers don’t want a wireless network that’s unreliable,” Moore added. “They believe that the current crop of technologies can be unreliable, but in most cases this isn’t true,” Moore continued.
“Education through advertising and workshops will be essential to helping users understand that wireless can be very suitable for some applications. In most cases, these applications will be data gathering and monitoring, but control may likewise become an application as wireless technology progresses.”
Wireless also has the potential to be a great addition to a factory’s network. While still in the early phases of adoption, it has huge growth potential, especially as networks are similarly being upgraded to more modern Ethernet solutions.
The introduction of four new pumps is enabling Anglian Water to reduce maintenance downtime at its Whitlingham Water Recycling Centre near Norwich, UK.
The units are used for pumping warm sludge at 40°C. Before the installation, removing a pump for repair or service would mean at least a day off-line, acording to Andy Pope of Anglian Water.
“Rebuilding the old pumps or just servicing them was always a difficult task because they are awkward, heavy and located in very tricky place," said Pope. "However, the new units – MIP (maintenance-In-place) pumps from Borger – have made maintenance far more efficient.
"And in what is a harsh environment, they are also proving extremely reliable in pumping the sludge”.
The specially designed Borger PL 200 pumps for Whitlingham have reduced foot-print helical drive upright 5.5Kw drives and special motor-mounted Inverters, helping resolve a restricted space issue.

Oscar Mayer is saving hundreds of thousands of pounds a year through the use of a new waste-treament and green energy system at a UK site. The project was triggered by a 50%-plus hike in its effluent bills.
Waste4Generation (W4G) supplied a system for separating FOG (fats, oils and grease), COD (chemical oxygen demand) and TSS (total suspended solids) from the effluent. The compact system uses a concentrated feedstock, and a high-rate anaerobic digestion (AD) process.
By reducing the retention time of the reactors to under 24 hours, the design removed the need for large effluent storage tanks and enabled Oscar Mayer to treat its own waste and use its own renewable energy, explained the supplier.
As part a pre-feasibility study, a mobile demonstration plant recorded data on feeding regimes and loading and removal rates. This allowed W4G to tailor the proposed plant; widening the scope of equipment supply, reducing the price and treating all of the waste on site.
The trial exercise produced recommendations on water consumption and the capture of high-strength wastes and also identified how cost savings could be made on two existing treatment systems without effecting effluent quality.
A trial of the digestibility of the waste streams on site was conducted using a mobile demonstration plant, added W4G. This achieved results above initial predictions, with removal rates of over 95% and 76% methane composition in the biogas produced.
After a week on site, W4G said it was able to restrict the effluent bill rise to only 7% – below the 10% Wessex Water standard increase – while achieving the lowest trade-effluent results sampled and analysed by the utility in over a year.
As well as reducing effluent bills by 50%, W4G said the pre-treatment process and high-rate AD system could deliver up to 20% of Oscar Mayer’s electricity requirement, over £260,000 annual revenue through FIT, and £70,000 from RHI and heat savings. The conditioned waste, it added, could also command a fee in the future.
Growing global demand for natural gas is driving a strong recovery in capital spending on LNG facilities around the world, market analyst Douglas-Westwood’s (DW) has reported.
In its latest edition of 'World LNG Market Forecast', DW predicts that global Capex in LNG projects will total nearly $228bn during 2013-2017, an increase of 109% over the preceding five years.
DW expects liquefaction developments to contribute $143bn (63%) of forecast Capex. Import terminals’ spend will grow and total $50bn (22%). Gas carrier expenditure will increase at a CAGR of 25% and total $35bn (15% of forecast Capex.)
Spending will be on base-load onshore and offshore fixed LNG liquefaction, LNG carriers and LNG regasification via both onshore and offshore fixed import terminals.
This will be underpinned by huge financial commitments to both liquefaction projects and gas import facilities, said report author, Michelle Gomez. In particular, she noted that liquefaction developments in Australasia and North America will play a lead role.
Spending will peak in 2015 and decline slightly in 2016 and 2017, Gomez, noting that the current surge of Australian LNG export projects reaching completion.
"The decline is, however, offset to some extent by significant growth in most other regions, particularly Eastern Europe & FSU, Africa and Asia," she commented.

QA Weld Tech Ltd of Middlesbrough, UK is expanding both premises and staff numbers to help it deliver £5m of new orders – for BP’s redevelopment of the Scheihallion field West of Shetland, the huge Ichthys LNG Project in Australia, as well as in Brazil’s offshore pre-salt areas.
The work has created 12 new positions in production management, estimating, welding engineering and quality management and jobs for welders, and CNC machinists.
“Three years ago we took on additional fabrication space and built a new two-story office block that, at the time, seemed almost too big for our needs," said managing director, Charles Tighe.
"We’ve now filled that with new employees and have taken on further facilities to house shot-blasting equipment and fabrication bays for our Brazilian projects."
Tighe said opportunities in Brazil were huge and that country is the focus of the first overseas expansion of the business with the development of QA Weld Tech Brazil.
"We also have plans to increase our machine shop capabilities, add further weld cladding equipment, and redevelop our pressure testing bays,” he said.
More...

Pumps manufacturer Hayward Tyler has reported new orders worth £13.9 million from the nuclear, oil & gas and power generation sectors. Work booked between April and June, was 42% more than the same period last year, the company added.
Hayward Tyler said it is seeing more nuclear and power generation aftermarket orders. Elsewhere, collaboration between its North American and Chinese operations has resulted in a first order for several 'mission critical' canned motor pumps from the Chinese chemical industry.
The company has also picked up a further order in the North Sea oil and gas sector after last year’s clarification over how decommissioning of rigs at abandoned wells would be treated for tax purposes.
Momentum seen in the three months to March has continued into the current financial year, accordign to Ewan Lloyd-Baker, Hayward Tyler’s chief executive.
“We are encouraged with the progress being made by the group which gives us confidence in meeting our expectations for the current financial year," said Baker.
Hayward Tyler's order intake totalled £49.5 million in the 15-months to March, up 25% on a pro-rata basis over 2011’s figure of £31.6 million.
The company's power generation business accounted for 58% of this, with the oil & gas business accounting for 19% and nuclear the remainder.
On-the-go-food company Greggs has postponed plans to build a £35-mlllion frozen food manufacturing plant in Hinckley, Leicestershire. The proposed 300-employee facility was flagged up in April as part of the group's expansion plans.
These ambitions have, however, now taken a knock after a £4.6-million fall in first-half pre-tax profits to £11.4 million. The group, most famous for selling sausage rolls, also reported a 3% dip in like-for-like sales to £362 million.
Factors affecting profits for the six months to 29 June included energy and food ingredient costs, which came in 6% and 4% higher respectively.
Greggs will now focus on improving operational effectiveness, explained chief executive Roger Whiteside, who highlighted a need to invest £25 million over five years in process and systems replacement.
Whiteside's targets include, for example, replacing legacy of autonomous divisional manufacturing & warehousing systems with an integrated ERP-based stock system.
The CEO also aims to introduce new ordering processes to ensure better product availability and reduced waste and more transparent supplier management and purchasing processes.
Energy buyers have welcomed moves by major suppliers to pull the plug on rollover contracts that can automatically put companies – including many SMEs in the process sector – on punitively high rates if they miss renewal deadlines.
nower has announced that from April 2014 it will stop offering default auto-rollover contracts to new business customers. The move, it claimed, was part of a wider approach to offer smaller businesses more choice in how they manage their energy costs.
Existing npower customers will benefit from November 2014, to allow time for wider changes in the market to be implemented, the power company added. The new options will include fixed-term and variable-term contracts as well as those focused on energy efficiency.
npower followed a lead set by British Gas, which on 17 July became the first supplier to end auto-rollover contracts. Its new customers are to be offered alternative products from September, while existing ones will have revised renewal options by June 2014.
“Increasing numbers of our small business customers have told us they don’t like the way the energy industry automatically moves them onto new contracts," admitted Stephen Beynon, managing director of British Gas Business.
"We're calling on the industry and the regulator to work together to ensure that all customers have a transparent choice of products that never include auto-rollover," added Beynon.
Among those to cheering this 'conversion' is energy purchasing consultancy ENER-G Procurement. it has described rollover contracts as a source of excess profits for suppliers over the years and believes the practice has no place in today's market.
"The term 'rollover' implies a soft landing, yet the reality is that organisations which fail to meet deadlines to renew or switch energy contracts are automatically 'rolled over' into uncompetitive auto-renewal prices or even to extortionate 'out of contract' rates," said its general manager Mark Alston.
"This is often made worse by a lack of transparency and short timescales involved in the termination process," added Alston. "We believe customers should be free to choose whether to enter into a term agreement, or simply pay a variable tariff which is reflective of the actual costs of supply incurred, plus a fair margin for the supplier.
ENER-G is also working to achieve greater transparency among suppliers for their third party charges. These can amount to up to 50% of an energy bill, yet are not always firm within many suppliers' "fixed price" offerings.
As customers can be unaware that up to 50% of their budgeted cost is liable to increase, Ener-G wants suppliers to categorise their offers for greater transparency and to produce "100% genuine fixed offerings".
Thames Water has started repair work after removing what it believes to be the UK's biggest ever 'fatberg' from a sewer in the London suburb of Kingston.
The 15-tonne lump of waste food fat mixed with wet wipes could have led to sewage flooding many homes, streets and businesses in the suburb of Kingston. The damage caused will take up to six weeks to repair.
"We've never seen a single, congealed lump of lard this big clogging our sewers before, said Gordon Hailwood, waste contracts supervisor for Thames Water said:
“Given we’ve got the biggest sewers and this is the biggest fatberg we’ve encountered, we reckon it has to be the biggest such berg in British history."
According to Hailwood, the bus-sized lump had left the sewer almost completely clogged, which could have led to raw sewage spurting out of manholes across the whole of Kingston.
CCTV investigations found the mound of fat had reduced the 70x48cm sewer to just 5% of its normal capacity. The blockage was initially discovered after residents in nearby flats complained that they couldn’t flush their toilets.
Thames Water began repairs to 20 metres of damaged pipe on 5 Aug and expected the work to take up to six weeks to complete.
(Image by CountyClean / Source Thames Water)