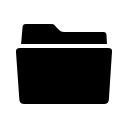
Uncategorised (4996)
This caused serious problems on the methanisation line that prevented stable operation of the facility.
Operators found huge levels of sediment in the digesters and floating layers, clogging of pipelines, while high losses of the digestible organics in the pre-treatment stage led to poor biogas and residue yields.

Another concern is that some overseas firms are providing new ‘biogas packages’ with, for example, CHP engines that sometimes don’t meet UK regulations.
Among those tracking such developments is Charlotte Morton, chief executive, Anaerobic Digestion and Biogas Association (ADBA), which works to support the AD industry and its customers, and the development of best practice.
“All AD plants are different, and the equipment requirements can vary hugely depending on the feedstock that will be processed and how biogas and digestate will be used," said Morton. “It is therefore vitally important that plant developers are well informed, and ask the right questions of their equipment suppliers.”
Fuel cell energy developer AFC Energy has selected GB Innomech to develop automated manufacturing equipment to assemble fuel cell stacks for the company’s EU-backed Power Up programme.
The work includes the development of automated equipment to dismantle stacks at the end of their working life, allowing key components and materials to be recycled and reused.
The appointment is being made with the support of a four-year, £4.9 m EU development grant that will enable AFC Energy and the Power Up consortium to develop and install commercial-scale energy generation plants using hydrogen as a fuel source.
One of the first clean energy plants will be located at Air Products’ industrial gas processing facility at Stade, northern Germany.
The first of two KORE systems is due to be installed in 2014 and the plant will generate a total of 500kW electrical output when fully operational.
MG, Novozymes plan world's first biomass-to-glycols plant in China
Administrator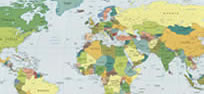
M&G Chemicals is to build a 1,000ktpa facility to produce glycols from biomass in China. Due on-stream in 2015, the biorefinery is expected to be the first of its type in the world.
The plant, in Anhui province, close to Fuyang in eastern China, is to be established through a JV between M&G Chemicals and Guozhen Group Co. of China. The Chinese partner is to provide 1,000ktpa of wheat straw and corn stover for the facility.
The plant will use Beta Renewables’ PROESA technology, with Novozymes to supply the enzyme technology for biomass conversion on an exclusive basis over a 15-year period. Novozymes will also provide financial support of $35 million to support M&G's project.
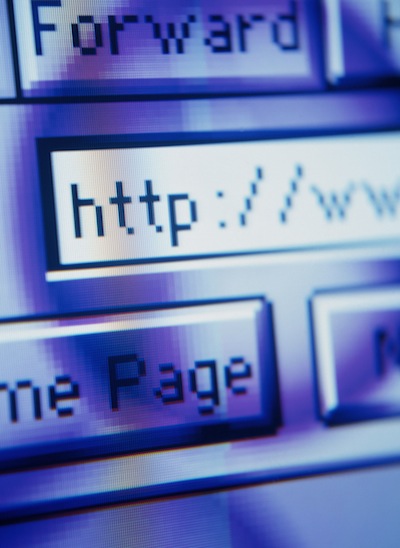
PI Match interview with Simon Coombs, business development director at Capula Ltd – an independent system integrator, specialising in solutions that combine automation control, real-time IT with electrical and instrumentation, and focused on the energy and utilities market sectors across the UK:
PIM How is the automation project pipeline flowing at the moment?
SC Overall, we continue to see automation projects coming to a close and a growing pipeline of opportunities across each of our market sectors. This is especially true for small and medium sized projects. However, we see some of our larger projects being delayed in approvals and it is momentum with these large projects that makes all the difference of course.
PIM Which sections of the markets served by Capula are most active, and why?
SC All our markets have on-going work on the back of increased investment in energy and infrastructure over the last few years within the UK. However, we measure activity in terms of new projects being let.
Power generation and renewable energy sectors are extremely active at the moment with a large increase in opportunities as clients' confidence increase with improved government incentives (to address future energy security of supply and carbon reduction targets), improved access to project finance, streamlined planning, etc.
Other markets are at a low in the delivery cycle. For example, the water industry coming towards the end of the current investment cycle (called AMP5) with new projects focusing on planning and conceptual design for the next investment period starting in a couple of years. This requires a different type of resource and structure to support these projects.
Similarly, the nuclear sector has delays in starting legacy improvement projects and also new build of the next generation of nuclear power stations. If you are involved in providing feasibility studies and conceptual design, however, there is plenty of advisory work for automation specialists.
PIM What other drivers or barriers are influencing project approvals at the moment?
SC Clients' business performance continues to be kept under close scrutiny. Therefore, even if our clients have strong balance sheets and good access to funding, they are not starting projects unless there is a clear and compelling business case. Obsolescence upgrades and interesting demonstrator projects that historically were done simply for engineering reasons are tending not to get approved.
The response in the marketplace is to ensure that each of our projects will lead to a clear benefit to the our clients' businesses with defined approaches to minimising delivery and operation risk. Of course, this is increasing the importance of effective automation control and real-time IT solutions that can really make a difference for our clients. It is also increasing the importance of having domain expertise and proven credentials - in addition to a good price, of course!
PIM Any other factors emerging that might impact on these markets going forward?
SC The general trend for automation and drives over recent years has been to procure standardised products from the main, global vendors in order to benefit from their on-going funding in research and development and access to common, standard solutions across diverse markets.
Our clients are under increasing pressure to reduce their costs, both for capital or operational expenditure. They are pushing this pressure down their supply chains and are therefore looking for innovative approaches that can decrease the delivery and the whole-life costs of solutions.
However, this is conflicting with the trend by large, global automation vendors to steadily increase the price of their products year on year in response to increasing energy, materials and manufacturing costs.
As system integrators we find ourselves in the squeezed middle between these conflicting pressures. Therefore, a future trend might be the re-emergence of bespoke, innovative products from smaller, nimble vendors that can provide more cost effective, albeit less standardised solutions, for our clients.
Thank you
A tri-company project representing the best of British innovation and application expertise has won the Robotics & Automation category of the Food Processing Awards 2013 - part of the annual Appetite for Engineering event for the food manufacturing industry
The winning project - decided by votes from readers of Food Processing magazine - combines multi-axis robotics, 3D vision technology and development and integration expertise to automate baked-product decoration.
The three companies involved were robot technology provider Mitsubishi Electric, Scorpion Vision which provided a 3D machine vision system and Quasar Automation, which provides solutions for challenging applications in food manufacturing.
Explaining the winning baked-product icing system, Jeremy Shinton of Mitsubishi said the non-uniform shape of many food products makes applying decoration, such as piped icing, very much a manual task.
“Mitsubishi Electric and Scorpion Vision have teamed up with Quasar Automation to create a decorative depositing method that takes into account the irregular shapes but maintains the depositor at a constant height above the work piece," said Shinton.
"With such accuracy the decorative icing is applied in a repeatable way. This allows the optimum time for the icing to set, often a critical issue in real-world production processes,” he added.
In taking the Grangemouth operation to the brink, Ineos' billionaire main owner Jim Ratclffe essentially posed the question: 'Do you want to have a petrochemicals plant here and the thousands of jobs and massive contribution to GDP that go with it ... or not?'
This proposal led to an embarrassing retreat by leaders of trade union Unite, who had previously disputed the need for the company's 'survival plan' for Grangemouth.
However, there should also be some red faces among the political leaders, who scurried to come up with an improved support package to help Ineos establish a £300-million terminal to import US shale gas at the site.
They have contributed more than the unions to the crisis at Grangemouth - and at many other refinery and petchem facilities around the EU.
Whatever spin is put on things, European industry remains hobbled by environmental costs way in excess of those in competitor countries around the world.
Meanwhile, UK and EU leaders are, at best, dragging their feet over the development of shale gas that is giving the US and, increasingly, developing countries such as China, huge energy- and feedstock-cost advantages over European producers.
Taking Ratliffe's lead, industry should ask those in the corridors of power in Westminster and Brussels, and indeed the wider public, if they really want to continue to have a chemicals and refining industry in the EU, or not?
If the answer is - as the 'greens' would have it - 'no' then the obvious step is to focus future investment and employment elsewhere.
If it's 'yes', then let's see some real support for shale and a level playing field when it comes to environmental costs and requirements.
Within the UK process sector, demands for excellence, innovation, invention, R&D and new product and process design are now the leading imperatives so all companies should be aware of the powerful and increasingly valuable corporate tax incentive now available.
Qualification for R&D Tax credits as an SME (up to 500 employees) and large companies (LC) is simply to be registered as a UK company and be a going concern.
So all companies and the broadest ranges of activities are covered. Opportunities for the process industries are clearly among the most eligible for tax credits. The options are manifest.
If you are part of these industries, examine everything you do as a start to identifying those elements large and small, signification seemingly trivial that give your activities, products and processes their commercial, technical and functional edge.
Do not doubt or underestimate your own ability to undertake R&D even when, possibly, you didn’t realise you were doing it anyway! Don’t be over interpretive as to what might constitute R&D for this purpose.
If research and development leads to patent IP possibilities, you can claim additionally via the ten-per-cent Patent Tax Box scheme.
Take-up of R&D Tax Credits is relatively small. In some ways it is a disappointment to the Government that more companies have not taken this opportunity to develop and make R&D part of their normal operational structure.
Key drivers’ for all directors and their key executives to look at are:
• Identifying the actual wide scope and definition of what is likely to be accepted as R&D. HMRC’s CIRD Guidelines refer generally; however, interpretation is required.
• You can claim the last two accounting periods 2011- 2012; the current year 2013 and then year-on-year. The scheme encourages continuity and commitment.
• Identified R&D should be briefly and accurately written up to indicate research and development with relevance to your accounting periods.
• Don’t be over-ambitious and attempt to identify too much, concentrate on the small, seemingly marginal effects of design, research, test, trialling, innovation, prototypes, failures, successes and those key inputs, changes, adaptions, materials and spark-of genius or luck that created a new or better way. Begin to think R&D.
• Identify all key people likely to be involved in any way with R&D or activities involving innovation, meeting clients, technical, cost-efficiency and functional demands. These must be your key drivers who are also likely to be directly or indirectly involved with what you need to identify and associate as R&D.
• A driver is not to forget or miss the accounting period deadlines. This is expensive if missed.
The outlook for R&D Tax Credits is now good. It is here to stay and to be part of the UK drive for speciality products and processes. Resolve to get involved. Specialist assistance is available and you should seek it to get going and create an internal model to recover or save taxes going forward.
Greville Warwick Director
MSC Corporate Strategies Ltd
www.msc-corporate.com
01926 512 475
Windows upgrade warning, as cyber attacks rise six-fold
AdministratorMany manufacturers across Europe and, indeed in all world regions, are still using Windows XP within their organisations, - even though Microsoft will stop supporting the operating system from 8 April 2014.
Growing concern over cyber security, however, is likely to force these companies to upgrade sooner rather than later, particularly as Microsoft will no longer write security patches for any new vulnerabilities that emerge.
Following the Stuxnet and Shamoon attacks in the region, Middle East countries are taking a lead on this issue.
Under a recent decree in Saudi Arabia, for example, companies will have to upgrade to Windows 7 and Windows 2008 from this December, reported Jay Abdallah of Invensys' cyber security team for the EMEA region.
This follows an earlier mandate by the Saudi rulers requiring every single plant to have 'demilitarised-zone' protection against cyber attacks since July 2013, Abdallah explained in a recent presentation on cyber security developments in London.
Otherwise, Saudi-based companies lost connectivity to the corporate network, preventing them from sharing emails, scanning the web or sharing alarms or historian data.
"The people that are going to be most affect are those higher up," said Abdallah. "The operators will still be able to run the plant but they won't be able to share any data with the corporate network."
These measures are clearly justified, Abdallah noting that since 2010, there has been a 600% increase in industrial control system and SCADA vulnerabilities.
"I have never seen that in 15 years of tracking," said the IT expert, noting that the attackers are increasingly targeting oil refineries and other critical infrastructure facilities, including an average of 10,000 cyber attacks a month on power companies,
"These days, these are very targeted attacks with specific knowledge of a vendor or a platform. They are bringing in experts or ex-employees that know the industrial control system, PLC or SCADA system inside out to achieve complete infiltration. It is no longer a drive-by shooting, it is targeted at specific company."
The Shamoon virus, for example, hit three Middle East energy companies. Spread by USB then Microsoft auto-propagation services it affected around 42,000 systems, causing millions of dollars worth of damage. The attack hit only the corporate level domain and did not disrupt industrial control systems.
While Shamoon was written by amateurs, Abdallah said Stuxnet was written by experts for one specific SCADA system to cause physical damage to a nuclear centrifuge in Iran.
By telling the operator all was well even though the equipment was spinning to a point of destruction, it delayed Iran's nuclear programme for at least two years, he said.
The worrying thing, continued Abdallah, is that these viruses or malware programmes are now so sophisticated that they can actually sit dormant for an average of five years before they are ever detected.
He concluded: "If the technology is not up to date to track the newest versions of the threats, then we may never know that there is something wrong with the environment.
"The question is not re we ready for the latest attacks, but rather are we ready for what has already happened."
Pressure to reduce costs across the process supply chain is prompting companies to reconsider their automation-buying strategies, according to an executive of systems integrator Capula.
While there now is a growing pipeline of automation project in the UK, approvals for some larger projects are still being delayed, said Simon Coombs, business development director of the independent SI, focused on energy and utilities markets.
"It is momentum with these large projects that makes all the difference," noted Coombs, adding that even clients with strong balance sheets and good access to funding are not starting projects without a "clear and compelling" business case.
For example, he said that "obsolescence upgrades and interesting demonstrator projects that historically were done simply for engineering reasons are tending not to get approved."
Capula specialises in combining automation control and real-time IT with electrical and instrumentation systems. It increasingly has to demonstrate how these projects clearly benefit clients' businesses with defined approaches to minimising delivery and risk.
These demands, said Coombs, are "increasing the importance of effective automation control and real-time IT solutions ... and of having domain expertise and proven credentials - in addition to a good price, of course."
Over recent years in the automation and drives sector, companies have tended to buy products from the main global vendors. This has been seen as the best way to keep up-to-date with the latest R&D and standardisation requirements across different markets.
But Coombs said the need to reduce capital or operational costs means clients are "looking for innovative approaches that can decrease the delivery and the whole-life costs of solutions.
However, he added, this is conflicting with the trend by large, global automation vendors "to steadily increase the price of their products year-on-year in response to increasing energy, materials and manufacturing costs."
With system integrators being squeezed between these conflicting pressures, Coombs concluded that a future trend might be "the re-emergence of bespoke, innovative products from smaller, nimble vendors that can provide more cost effective, albeit less standardised solutions, for our clients."
Support for tried-and-tested energy from waste (EfW) technologies and scepticism over newer alternatives seems to be the order of the day for major players in the waste management industry.
Among the technologies to have earned its spurs is anaerobic digestion, according to Adam Read, practice director responsible for waste management and resource efficiency at Ricardo-AEA – an international consultancy covering global energy and environmental issues
"While the UK might not have the 1000s of facilities operating that the government predicted, AD is now proving itself as long as you've got the feedstock quality and the site and markets," Read told delegates at the recent Green in the City conference in London.
CHP with large- or medium-sized thermal facilities was another viable and deliverable technology and would play an increasingly significant role in the UK's energy security over the next five to 10 years, he forecast.
"I am a big fan of heat production in terms of thermal efficiencies but you can only do that if you have got a heat-user on tap nearby: logistics centres, refrigeration units, industrial units all make ore sense than an old landfill site in the middle of nowhere," he said.
On the other hand, while he saw a role for newer technologies such as gasification and pyrolysis, Read would "not be putting my money into any just yet: "Give it another year and I think you will see some newer facilities operating to give us more comfort about the scale of those projects and the quality of the feedstock and the outputs. "
Axion Polymers processes rigid waste plastics and ELV shredder residue at plants in Salford and Manchester , Company director Roger Morton emphasised the need to be realistic about the chances for newer schemes, particularly in the areas of gasification and pyrolysis.
"We have been working on that for up to 12 years and I am also having to say the same things like gasification to make liquids doesn't work without a very expensive gasifier that is fed with oxygen, There are lots of air-blown gasifier projects that claim to make liquids, but don't believe it.
"Another myth is that pyrolysis of biomass can make a usable liquid; it makes a horrible soup of disgusting carcinogenic chemicals. You can make it with a great yield but not a reusable liquid fuel."
A better bet, perhaps was fuel-from-plastics. This technology, said Morton, is showing promise but still required more effort to get the waste plastic clean enough to give a good yield in a pyrolysis plant than simply making recycled material from it.
"On the whole we think that mechanical recovery is a good idea," he said. "If you are going to burn it, and usually about half of our material is burned, then a lot of the pyrolysis and gasification technologies around are really incineration by another name only more expensive.
However, the choice of which EfW technology to back is no longer just a game for big guys within the waste management industry, according to Peter Jones of Ecolateral.
"People at big companies like Air Products and IneosChlor are reading the Ofgem report warning that we could be having brow outs next year. If you think about the political impct of brown-outs in Jan, Feb March 2015 just before a general election. These are big energy users are going to start putting in facilities and making them work,
For the major chemical and process companies, EfW offers a way to reduce their exposure to the vulnerabilities of the international coal, gas or other energy markets.
"Those are the people that are going to move in: we are just in this phoney war period," the waste management expert concluded.
More...
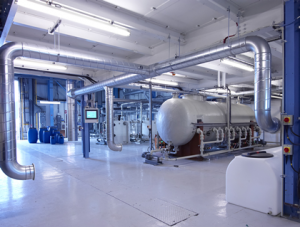
The Centre for Process Innovation Ltd has recently finished accepting proposals for a contract covering thesupply, installation and commissioning of a fermenter seal system
Furthermore the seal system vendor should identify any steps or checks which have to be carried out by CPI to achieve and sustain this level of reliability.
The vessel is used for biofermentation and uses standard CIP chemicals (NaOH) to clean. The steam and air systems are clean. The fermenter is cleaned in place after every campaign.
Sterilisation of the fermenter and the seal is a requirement before every batch. This is carried out using locally generated low pressure (2barg) steam at 133°C. Sterilising of the seal is carried out with the agitator stationary.
A bursting disc for 5barg is fitted. Operating pressure is normally in the range 0.5barg to 1barg. A process trip is set at 2.4barg at which point the exhaust bypass opens.
"Our proprietary membranes, membrane housings, pumps, valves, controls and filters work together to create highly efficient, integrated solutions for a variety of customer needs," he claimed.
Pentair is providing equipment and expertise from both its Valves & Controls and Filtration & Process businesses for the planned desalination plant, which will supply fresh water to the city's five million residents.
The UK's Green Investment Bank (GIB) has announced an investment by its fund, managed by Greensphere Capital LLP, to purchase and upgrade an operational biomass plant in Port Talbot, Wales.
UK Green and Sustainable Waste and Energy Investment Ltd Partnership (UKGSWEI), is investing £11 million to take a minority stake in the plant. The UKGSWEI fund, in which GIB is a cornerstone investor, is managed by Greensphere.
Co-investment was sourced by Greensphere from Signia Wealth Management and Stobart PLC.
"This investment will secure the long-term future of an important Welsh renewable energy plant and will improve its efficiency and sustainability," said Shaun Kingsbury, chief executive, UK Green Investment Bank.
The Greensphere fund was set up, in part, to help support the UK's waste wood biomass sector and its first acquisition of an operational asset is an important step, Kingsbury pointed out.
The plant, Western Bio-energy Ltd, is a 14.7 MW biomass facility and was the first commercial-scale power station of its kind in Wales. It has been operational since 2008.
The investment in the Port Talbot plant will see a number of upgrades implemented. These will include an increase in grade A waste wood as a fuel source, and refurbishment of the plant. This is expected to improve operational efficiency and reduce operational risk.
Greensphere has negotiated a contract to provide feedstock for the lifetime of the plant with Stobart Biomass, which will significantly increase feedstock reliability and reduce costs.
After the scheduled refurbishment, the plant will be able to accept c.55% grade A waste wood, a significant increase. The refurbishment, which is expected to take place in Summer 2014, is likely to create a number of local jobs.
The Greensphere-managed fund forms a key part of GIB's investment strategy into the waste and bioenergy sector. GIB initially awarded the competitive fund mandate to Greensphere to drive investment into small scale waste to energy projects. This is the fund's second investment since it was set up in July 2012.
"We see the Port Talbot plant as a cornerstone of the waste-wood-to-energy platform we are building in this sector," said Divya Seshamani, managing partner, Greensphere Capital.
Indian food manufacturer Simtom Food Products, based in Leicester, UK. has upgraded its production line as part of an expansion plan.
The company makes own-recipe Indian sauces, seasonings, marinades, pickles, and chutneys for retail and wholesale markets.
Simtom has secured facilities including asset finance and working capital facilities from Yorkshire Bank to support day-to-day trading and the new production facility.
“By investing in a new production line we have replaced our ageing machinery with new equipment, which will allow us to realise greater returns and achieve sustained economic growth," said Bhavin Chandarana, director at Simtom.
Simtom expects sustained growth over the next five years with the company looking to increase its customer base. To meet expected demand, plans forecast the workforce expand with up to 50 new posts likely to be created by 2015.