
Super User
Sheffield (UK) to be home for company developing new greener vehicle batteries
ULTIMATE BATTERY COMPANY CHOOSES SOUTH YORKSHIRE TO DEVELOP TECHNOLOGIES FOR GREENER VEHICLES
A revolutionary company set to develop a new generation of greener vehicle batteries has chosen Sheffield as the location for a new Research & Development and manufacturing facility.
The Ultimate Battery Company (UBC), based in Hyde, Manchester, selected South Yorkshire for the location of its new facility, after receiving support through South Yorkshire Mayoral Combined Authority and recognising this region’s potential as the green heart of the UK.
South Yorkshire Mayoral Combined Authority has pledged to provide a total of £5.2m in financial support (£3.2m loan and £2m grant) to the Ultimate Battery Company to enable them to develop technologies to reduce Carbon Dioxide emissions with transformative new technologies and energy storage solutions. The new R&D and manufacturing facility is expected to create 495 new jobs over the next few years.
Maurizio Cunningham-Brown, CEO of the Ultimate Battery Company, explains: “To develop these new technologies and products we needed to find a location with a green energy infrastructure and the support framework and supply network in place to help us achieve our ambitions. The team at SYMCA helped to guide us through the funding process and put us in touch with the University of Sheffield’s AMRC, which is now our partner in research and development of our new battery technologies.”
Maurizio adds: “We are really excited about locating our new facility in Sheffield and being able to create jobs here, now and in the future. Access to a talented workforce and the support available in this area for skills training and development were obvious draws to South Yorkshire.”
left to right (Front) Maurizio Cunningham-Brown CEO and founder of Ultimate Battery Company, Malcolm Earp Chief Operating Officer and Chief Commercial Officer of UBC, Dr Keith Ellis, Chief Security Officer and Dr Steve Bowles, AMRC Team Leader.
The Ultimate Battery Company is developing technologies which remove most of the obstacles to widespread electric vehicle uptake, including increasing battery run times, extending travel range and reducing costs for the customer.
The company’s aim is to design a new battery that provides a Lithium-like performance at 35% of the cost, enabling twice the energy to be stored in the same physical space and providing a faster charging rate. The batteries that the Ultimate Battery Company has developed also significantly reduce weight by up to 15Kg per vehicle, further driving down both CO2 emissions and manufacturing costs, while increasing energy densities.
Gareth Morgan, SYMCA Senior Business Development Manager for Trade & Investment, said: “The Ultimate Battery Company offers exciting opportunities for our region in terms of recruitment, education and development of new greener technologies. The company has been able to establish valuable connections with the AMRC, which offers excellent resources and expertise to help UBC to put their plans in motion. We are very pleased to welcome UBC to South Yorkshire, and we look forward to supporting the business further as it embarks on its ambitious growth plans.”
Steve Foxley, CEO of the University of Sheffield AMRC, said: “It has been a great pleasure to work with the Ultimate Battery Company around its manufacturing innovations for energy storage technology and we are delighted to see they are now building on that collaboration with inward investment into South Yorkshire, close to the research expertise of the AMRC. We look forward to working with them on future projects, accelerating the journey to net zero and opening up new opportunities around cheaper, greener future energy systems.”
Continuing to work alongside the AMRC, the Ultimate Battery Company is also setting its sights on making the switch to electric vehicles easier for manufacturers.
Malcolm Earp, Chief Commercial Officer & Chief Operating Officer at the Ultimate Battery Company, said: “The main reason for the slow uptake of electric vehicles is the increased cost compared with a traditional combustion engine motor vehicle. Our new battery changes the dynamics – not only will the electric vehicles achieve purchase price parity with traditional cars, but total cost of ownership will be significantly less in terms of both lower operating and maintenance costs.”
“The demand for these products is out there and has already been confirmed by a wide range of leading automotive manufacturers and other related industries. As such, we are confident that with the resources we will have in place at our new facility and the technology we are looking to bring online, we can accelerate the switch to electric vehicles long before the 2040 target.”
“In the meantime, we’re looking forward to being located in South Yorkshire to make these exciting plans a reality and working with SYMCA, AMRC and the DIT (Department of International Trade) to get our new facility up and running and push the start button on what will be the new car batteries of the future.”
For more information about the Ultimate Battery Company, visit: The Ultimate Battery (theultimatebatteryco.com).
For more details about the South Yorkshire region, visit www.southyorkshire-ca.gov.uk.
About the South Yorkshire Mayoral Combined Authority
We are the South Yorkshire Mayoral Combined Authority (SYMCA).
Led by Mayor of South Yorkshire Dan Jarvis, we bring together the local authorities of Barnsley, Doncaster, Rotherham and Sheffield and the private sector through our Local Enterprise Partnership (LEP).
The Mayor, MCA and LEP have a shared purpose to create a stronger, greener, fairer South Yorkshire. We work together to unlock the potential of our people, businesses and places and ensure they prosper.
Our Strategic Economic Plan (SEP) provides the blueprint for how we will transform our region. We will keep people and businesses moving and help them grow, delivering a world-class public transport network and attracting investment to create a stronger, greener, fairer South Yorkshire by 2040.
Our vision is to grow an economy that works for everyone. We will develop inclusive and sustainable approaches that build on our strengths in innovation and embrace the UK’s 4th Industrial Revolution, to contribute more to the country’s prosperity and enhance quality of life for all.
We have powers and resources, devolved from Westminster to South Yorkshire, which mean we can take decisions locally about our economy, transport, skills, housing and infrastructure.
We use these to create a vibrant, thriving South Yorkshire where people want to live and work.
We attract new investment to our region. We build the conditions for inclusive economic growth which benefits everyone. We help create good jobs, by backing businesses to grow, invest and locate in South Yorkshire.
We support people so they have the training and skills to find work, remain in work or progress in work. We help businesses secure the skills they need to be more productive and grow.
MediaTek and Anritsu Achieve Industry First Dual Active Protocol Stack (DAPS) Handover for 5G New Radio (NR)
MediaTek inc. and Anritsu Corporation are pleased to announce that the first DAPS handover for 5G New Radio (NR) has been verified with a device containing the MediaTek M80 5G modem and Anritsu’s MT8000A Radio Communication Test Station with Rapid Test Designer (RTD) application software.
The 5G NR standard is evolving beyond the traditional Enhanced Mobile Broadband (eMBB) to support use cases for Ultra Reliable Low Latency Communication (URLLC). URLLC targets latency of 1ms or lower and reliability of over 99.999%, and these targets must be maintained during handover of mobile terminals across cells. The current Handover procedures have a Handover Interruption Time (HIT) of 30ms – 60ms during which a mobile terminal cannot transmit or receive user data. DAPS handover has been introduced in 3GPP Release 16 to shorten the HIT to as close to zero ms as possible. DAPS allows a mobile terminal to receive and transmit data simultaneously to source and target cells in a handover ensuring seamless data continuity.
“The ongoing collaboration of MediaTek and Anritsu continues to strengthen with this milestone achievement. Anritsu’s industry-leading test platforms directly benefit our R&D activities, enabling us to continue creating technology-leading 5G modems,” said JS Pan, General Manager of Wireless Communication Technology at MediaTek.
“We have achieved yet another important industry milestone and are looking forward to our continued partnership with MediaTek to bring advanced 5G use cases to market” said Takeshi Shima, President of Test & Measurement Company, Anritsu Corporation.
Product Outline
The Radio Communication Test Station MT8000A is an all-in-one platform supporting RF and protocol testing, functional and application operation testing, beam characteristics testing and more. As well as supporting both NSA and SA-mode base-station simulation functions required for development of 5G chipsets and terminals, it also covers FR1 frequency bands, including 600 MHz, 2.5 GHz, 3.5 GHz, 4.5 GHz, and 6-GHz unlicensed bands, as well as the FR2 24 GHz, 28 GHz, 39 GHz, and 43-GHz mmWave bands, to support all the main bands used by 5G services. Additionally, MT8000A supports the functions required for high-speed communications, such as 4x4 MIMO in FR1, 8CC and 256QAM in FR2 as well as supporting the latest 3GPP Release 16 features. Furthermore, the MT8000A provides a versatile and efficient test environment that is easily configured using a simple user interface and software to test device performance.
About Anritsu
Anritsu Corporation (www.anritsu.com), a global provider of innovative communications test and measurement solutions for 125 years. Anritsu’s philosophy engages customers as true partners to help develop wireless, optical, microwave/RF, and digital solutions for R&D, manufacturing, installation, and maintenance applications, as well as multidimensional service assurance solutions for network monitoring and optimization. Anritsu also provides precision microwave/RF components, optical devices, and high-speed electrical devices for communication products and systems. The company develops advanced solutions for 5G, M2M, IoT, as well as other emerging and legacy wireline and wireless communication markets. With offices throughout the world, Anritsu has approximately 4,000 employees in over 90 countries.
Welcome to the first issue of PIM Metals incorporating IMT magazine
Welcome to the first issue of PIM Metals incorporating IMT magazine, firstly we must thank all the readers of IMT for now completing the registration for PIM Metals plus those newly registered readers. What is pleasing to see is the diversity of our readers in terms of geography and the industry sectors covered.
Geographically readers in Europe represent 59% of the total individuals followed bye the Asia Pacific region with 27%, then the Americas with 13% and the rest of the world at 1%. When we look at the broad industry breakdown 68% have put Metal Tube & Pipe production and processing as there number 1 activity and the balance is shared with sheet, strip wire & rod (metal producers and processors = 100%). Machinery and equipment producer’s registrations are kept on a separate database and form no part of the 17,500 initial circulation.
As many of you will have seen Tube & Wire Dusseldorf was recently moved to June 20-24 inclusive to ensure it was as accessible as possible to the thousands of visitors the show attracts from around the world, PIM Metals will present as much pre-show news as possible in the June issue published 1 week prior to the opening. However, in our next issue April we welcome editorial items and article proposals on any of the following: Tube & pipe bending and forming technology, Production & processing software plus Laser & plasma cutting.
Click the banner on the right or follow this link to download the issue
Article proposals are required no later than April 8th , news items are required on or before April 19th and should be sent to This email address is being protected from spambots. You need JavaScript enabled to view it.
Hébert Group joins forces with PulPac and sets up Dry Molded Fiber production
Hébert Group becomes a licensee and sets up production with PulPac’s pioneering Dry Molded Fiber technology. The production platform “PulPac Modula”, developed by PulPac and its partners, will be installed this summer in their facilities located in Orgelet, in the East of France.
Hébert Group has a history of constant focus on innovation and looking to the future, with sustainability as a key driver. With an expertise in thin wall packaging and in-mould labelling, the company supports some of the biggest brands in the global food industry.
Julien Hébert, Technical & Sales Director, Hébert Group said “We believe that the packaging industry is entering a new era driven by fast-evolving regulatory systems and customer expectations. At Hebert Group, we take pride in being in the forefront of that market shift and our collaboration with PulPac will allow us to develop and manufacture truly competitive fiber-based solutions. PulPac’s pioneering technology is not only about strengthening our offering and our customers’ brands, but also about leading the way in our industry.”
Dry Molded Fiber, invented and owned by PulPac, is a fiber forming technology that can replace single-use plastic with sustainable fiber-based alternatives at low cost. To accelerate the shift, PulPac has together with partners developed the PulPac Modula standardized machine platform. The company is on a mission to replace single-use plastics at scale, and this is a first in a stream of Dry Molded Fiber machinery rolling out to licensees, setting a new standard for sustainable fiber-based packaging.
Sanna Fager, Chief Commercial Officer, PulPac said “We are truly impressed by Hébert Group’s innovative mindset and ability to adapt to new technology, which has created very solid partnerships with some of the biggest names in the global food industry. We look forward to a long-term partnership where we can share know-how and expertise to leverage the full potential of dry molding within Hébert Group’s operations and customer network.”
About Hébert Group
Hébert Group is a family-owned company with an expertise in the development and the manufacturing of packaging solutions for the food and cosmetic markets. They have been supporting key FMCG companies in the large-scale industrialization of some of the most iconic designs in the packaging industry. www.hebert-group.com
About PulPac
PulPac provides the packaging industry with a groundbreaking manufacturing technology for low-cost, high-performance fiber-based packaging and single-use products. By pioneering the technology of cellulose molding PulPac enables their customers to replace single-use plastics with a sustainable and cost competitive alternative globally. www.pulpac.com
About Dry Molded Fiber
Dry Molded Fiber, invented and patented by PulPac, is a manufacturing technology designed for the circular economy. It leverages globally available, affordable, and renewable cellulose fibers to produce high performance fiber-based packaging and single-use products with highly competitive unit economics. Dry Molded Fiber also saves significant amounts of valuable water resources and energy, resulting in up to 80% lower CO2 footprint compared to alternatives. The process is up to ten times as efficient as conventional fiber molding invented over 100 years ago.
From port to foundation - Mammoet and OFCO's integrated transport solutions
Combined marine and land transport offering creates solid foundation for project market logistics in the Middle East.
The complexity of moving heavy cargo, sourced globally for projects, requires a partner with a combination of readily available resources for both marine and onshore transports and the expertise to overcome logistical obstacles and bottlenecks.
Specialized knowledge can be very beneficial, particularly in large and complicated projects, since experts in various specialties can provide valuable services. However, this often involves contracting various independent suppliers, each responsible for only their own part in the logistics chain. Excessive costs and delays can result from poor coordination and communication between these specialists.
Hence, project owners, EPCs and freight forwarders can benefit from working with service provider partnerships, such as the alliance between marine transport specialist - OFCO, Offshore International, and onshore transport and installation specialist Mammoet. Each organization’s expertise and resources are combined, and a single point of contact for communications ensures the alignment and optimization of logistics and installation schedules.
Double banking operation and marine transport for a power plant in Sharjah
A recent example of turnkey logistical solutions was the swift delivery of a critical project cargo for a power plant in Sharjah, UAE. Two 140t transformers needed to be received from a container vessel in Jebel Ali Port and then transported to the site in Sharjah for further installation.
Following comprehensive risk assessment and engineering, the team proposed receiving the cargo via a double banking operation and marine transport to Sharjah’s Khalid Port. The cargo was efficiently discharged by a floating crane onto a landing craft provided by the alliance and then transported to Khalid Port. The transformers were then offloaded using a RORO method using self-propelled modular trailers, before being safely transported to the site. Once on site they were installed using a jacking and skidding method.
Marine Operations Manager at Mammoet MEA, Harshad Deshpande, commented: “By involving the alliance in the logistics of the power plant components, the customer took advantage of the increased flexibility for the cargo move, both marine and onshore, thereby saving time and additional costs such as port charges and double handling of the cargo.”
Captain Maktoum Al Houqani, Chief Corporate Authority Officer and Acting Head of Maritime Cluster at AD Ports Group, and Chairman of OFCO – Offshore International said “The recent success of the delivery of critical project cargo intended for a power plant in Sharjah serves as a prime example of how service provider partnerships, such as the one held today between OFCO and Mammoet, can facilitate highly specialised and complex projects combining logistical transport solutions across both land and sea.
“We look forward to the continuation of our collaboration, which combines the long-standing expertise and resources of both organisations, to deliver a unique and competitive offering for customers seeking a robust end-to-end solution to meet their logistical needs.”
Loadout and marine transport in Dammam, Saudi Arabia
Other examples of successful and streamlined logistics include the loadout and marine transport of critical boiler components from Mina Zayed Port to Ruwais; the delivery of nearly 40 components from Khalifa and Ras Al Khaimah ports to Das Island for an ongoing expansion project and the delivery of two 94t storage tanks from Mina Zayed Port to ICADII jetty in Abu Dhabi.
“The vision for our partnership was to create a unique offering and a real value for our customers in the GCC. By engaging us, the customers benefit from our optimized planning and operations, in-house assets, expertise and engineering know-how. Reduced interface management within the logistics chain of projects give our customers the required peace of mind to concentrate their energies towards their business goals.” commented Thomas Wylie, Sales Director - Projects, Mammoet MEA.
“With the recent major project awards in the region, we are well positioned to provide the complete package of heavy lifting and transportation services, both onshore and offshore, from local ports to foundation, thereby advancing our continuous pursuit to help our clients speed up productivity.” he concluded.
About OFCO, Offshore International
Unveiled under the umbrella of Abu Dhabi Ports at the start of 2021, OFCO – Offshore International is one of the largest cost-efficient providers of onshore and offshore integrated logistics solutions and subsea services in the GCC.
Combining the long-standing maritime expertise of SAFEEN with AMLS’ diversified fleet and experience in offshore logistics and supply chain management, the company’s “one-stop-shop” offering is ideally suited to meet the complex logistical requirements of customers within the oil and gas, energy, and offshore markets.
About Mammoet Middle East
Launching a regional head office in the UAE along with the branch offices in Saudi Arabia, Qatar, Bahrain and Oman back in 1974, Mammoet has been delivering efficient and cost-effective solutions for engineered heavy lifting and transportation projects across the Middle East for almost 50 years, supporting numerous projects across a multitude of industry segments including the offshore, power, oil and gas and civil industries. Its acquisition of ALE in 2020 created the world’s largest global provider of engineered heavy lifting and transport services.
FutureOn launches innovative visual workflow tool, FieldTwin Collaborate
FutureOn, the global energy software company, has today launched FieldTwin Collaborate – a digital project sharing forum, which offers open communication and engagement, enabling quick adaptability and accountability for teams across the energy sector and supply chain.
More than a data visualisation tool, FieldTwin Collaborate brings multiple contractors together in one space, benefiting operators and project teams by ensuring accessibility, integrity and real-time updates on integrated projects.
The latest addition to the company’s arsenal enables teams to problem solve complex challenges as they appear. The data analysis capabilities, multiple perspectives and the shareability of assets enables enhanced forecasting and troubleshooting for projects.
This means that both operators and engineering, procurement, and construction team members work on the same shared data model while ensuring secure granular access and control of users and data for all.
FieldTwin Collaborate is an optional application which can be added to the company’s award winning FieldTwin software - a cloud-based digital platform which creates and maintains a digital copy of a physical asset, enabling maximum asset performance and value. This technology acts as the foundation for the collaborative visual workflows between multiple stakeholders.
Last year, the Energy Systems Catapult and Offshore Renewable Energy Catapult launched an Offshore Energy Digital and Data Strategy taskforce, with the aim of creating a digital and data strategy spanning oil, gas and renewables. FieldTwin Collaborate is a prime example of digital innovation that will go towards accelerating and embedding technologies and digital solutions across the energy industry.
Jostein Lien, Senior Vice President of Product at FutureOn, commented:
“By establishing a two-way secure connection between stakeholders using the platform, we have enabled a real-time collaboration opportunity. This will be a revolutionary tool for our customers and their stakeholders as they manage projects around the world.
“We are seeing ambitious goals outlined for reductions in personnel on board, emissions related travel and more efficient technology as we progress toward net zero. FieldTwin Collaborate is the perfect project management tool to enable this, and we look forward to rolling it out to our existing and new customers.”
Last year, FutureOn announced a strategic partnership with Kongsberg Digital (KDI), the digital division of the Kongsberg Group, strengthening its position as a leading international digital twin software provider.
To learn more about FieldTwin Collaborate, sign up for our webinar taking place on Tuesday 1 March at 11:00am GMT: https://globuc.com/digitalsolutions/unlock-true-collaboration/
About FutureOn
Experts in data visualization, FutureOn emerged from Xvision in 2016 to become a standalone provider of state-of-the-art visual engineering for the global energy sector. The company transforms the performance of complex capital projects with cutting-edge visualization and collaboration technology enabling the energy industry transition to Net Zero.
FutureOn is proud to offer its global customer base industry-leading software solutions to create digital twins that deliver a complete asset visualization and integrated data model that unlocks value through increased efficiency, improved safety, reduced costs, risk mitigation, lower emissions and increased uptime.
Outokumpu has limited exposure to Russia and Ukraine
Outokumpu has been closely following the developments in Ukraine, and the company regrets to see that the conflict has now been escalated into war after Russia’s military attack. Outokumpu does not have employees or subsidiaries in neither of the countries.
In the short term, Outokumpu does not expect any material impacts from the situation on its business and operations.
If the situation continues, it could impact Outokumpu’s procurement of raw materials and energy gases.
- Outokumpu’s main raw material is recycled steel which accounts for more than 90% of production. There is no dependency on Russia or Ukraine in recycled steel and only a limited amount of total nickel requirements is currently sourced from Russia. Supplies of additional raw materials have only a limited exposure to Russian origin materials and mitigation actions are already in place to resource such materials.
- Outokumpu acquires energy gases in the European market, Russia being one of the indirect supplier countries. Alternative sources are being tested.
- Our ferrochrome sources are independent, as we have our own chrome mine and ferrochrome production in Finland.
Outokumpu has an indirect stake in the Fennovoima nuclear plant project in Finland driven by Russian-owned company Rosatom. Outokumpu stated in its financial statements release that the fair value of the Fennovoima project was decreased to zero due to increased project risk.
In case of any direct and material financial impact, Outokumpu will announce them without delay.
Outokumpu is the global leader in stainless steel. The foundation of our business is our ability to tailor stainless steel into any form and for almost any purpose. Stainless steel is sustainable, durable and designed to last forever. Our customers use it to create civilization’s basic structures and its most famous landmarks as well as products for households and various industries. Outokumpu employs some 9,000 professionals in more than 30 countries, with headquarters in Helsinki, Finland and shares listed in Nasdaq Helsinki. www.outokumpu.com
Rotork actuators provide critical flow control at giant Beijing Daxing International Airport
Over 130 Rotork actuators have been installed at the new Beijing Daxing International Airport, Beijing’s second international airport. This builds on an existing relationship with China Aviation Oil, which controls the jet fuel supply at Beijing Capital and Beijing Daxing International Airports. At Beijing Capital, IQ Rotork actuators have been in operation since 1999.
Beijing Daxing International Airport is in competition for the title of the world’s biggest airport, with four runways currently built and a terminal building that covers an area of 700, 000m². Rotork actuators carry out several duties at the airport, including the control of the relief valves at the tank farm. These are in place in the event of a dangerous build-up of pressure, which can then be released by the opening of the valve. The pump room, oil tanks, oil station and landing field ground wells use both IQ3 and IQT3 actuators to operate a variety of valve types, including gate, ball, plug and butterfly valves. The oil tanks and oil station also use electro-hydraulic linear actuators, which can provide a fail-safe function on power loss.
The actuators are connected with a Pakscan loop on a General Purpose Field Control Unit. Pakscan is a redundant loop network which enables the remote control of actuators. It was selected as the unique loop back function and diagnostic ability made maintenance and service much easier. In an airport environment where hundreds of people can be displaced by breakdowns and delays, increasing reliability and reducing maintenance time is essential. Additionally, the customer was pleased that they were able to connect the actuators to the Pakscan loop, alongside actuators from another manufacturer.
Rotork Site Services (RSS) worked closely with the airport’s engineers, providing training to ensure that they understood how to operate and service the actuators installed on site.
Siemens and Desert Technologies launch solar and smart infrastructure development and investment platform, Capton Energy
Siemens and Desert Technologies have launched a joint venture to develop and invest in solar and smart infrastructure in Africa, the Middle East and Asia, as announced at Expo 2020 Dubai. The venture, Capton Energy – which aims to build up a portfolio of investments in projects with an aggregate capacity of more than 1 gigawatts (GW) – will support projects providing clean, reliable, and affordable energy in areas that need it most.
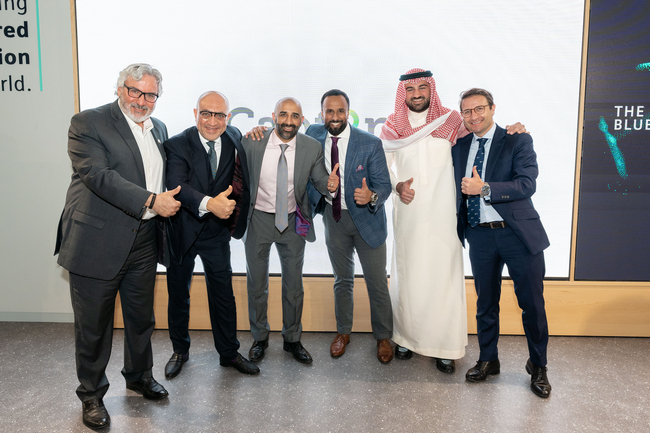
EcoAir® Biobased Outdoor Coating: New Addition to Cortec® Sustainable Corrosion Solutions!
Cortec® is pleased to announce the release of EcoAir® Biobased Outdoor Coating powered by Nano VpCI®. Since its inception, Cortec® Corporation has been looking for ways to make corrosion prevention more environmentally responsible. Sometimes this takes place in giant steps. Other times it is done by baby steps, such as replacing a petroleum-based chemical with a biobased ingredient to improve sustainability. With the release of EcoAir® Biobased Outdoor Coating powered by Nano VpCI®, Cortec® has addressed two aspects of environmental responsibility while expanding its options for user convenience.
Biobased Temporary Protective Coating
EcoAir® Biobased Outdoor Coating powered by Nano VpCI® is a ready-to-use temporary coating designed for severe marine and high humidity conditions. It comes in a convenient EcoAir® spray can, and it is classified as non-flammable. It provides multi-metal corrosion protection that is temperature stable to 180 °F (82 °C). It leaves behind an oily protective film that does not dry and offers outstanding rust prevention in outdoor applications.* When the protection period is over, EcoAir® Biobased Outdoor Coating can be removed by rinsing with a Cortec® VpCI®-41x series cleaner degreaser.
In addition to its key corrosion inhibiting quality, the most significant fact about EcoAir® Biobased Outdoor Coating by Nano VpCI® is its classification as a USDA Certified Biobased Product that contains 65% USDA biobased content. This high level has been achieved by combining renewably sourced oil and solvent materials with Cortec’s proprietary VpCI® corrosion inhibitor formulation for effective protection.
EcoAir® Spray Can Benefits
While Cortec® has offered biobased coating technology similar to EcoAir® Biobased Outdoor Coating in the past, now is the first time Cortec® has packaged it in an EcoAir® bag-on-valve spray can. This makes the coating easy to carry around and spray where needed, even in remote locations that do not have readily available electricity to run power spray equipment. EcoAir® cans can be sprayed in any direction, even upside down, making it easy to apply the coating in hard-to-reach areas.
EcoAir® cans also have environmental, health, and safety benefits. Instead of using traditional chemical propellants such as CO2 or flammable propane/isobutane, EcoAir® Biobased Outdoor Coating is powered by compressed air and is classified as non-flammable. An EcoPouch® inserted into the pressurized can contains the liquid, which is expelled by the surrounding pressure as the valve is depressed. When the can is empty, the metal can be recycled after the pouch is removed.
Where to Use
EcoAir® Biobased Outdoor Coating powered by Nano VpCI® is a convenient, more sustainable option for temporary protection of metal parts almost any place a wet film corrosion inhibitor is desired. For example, tube manufacturers who need to temporarily store piping on sheltered outdoor racking can protect unpainted ends with a quick spray of EcoAir® Biobased Outdoor Coating. Offshore layup crews in the habit of protecting bare metal moving equipment parts with a petroleum-based wet film corrosion inhibitor can substitute EcoAir® Biobased Outdoor Coating while still getting a high level of protection in a marine environment. EcoAir® Biobased Outdoor Coating is also a great option for manufacturers who want to spray a light oily biobased protective coating on metal components before shipping or storage (e.g., automotive service parts)
Take Advantage of Biobased Options
For anyone who wants a biobased rust preventative temporary coating in convenient spray can format, EcoAir® Biobased Outdoor Coating powered by Nano VpCI® is an exciting addition to the market. EcoAir® Biobased Outdoor Coating helps users achieve wet film corrosion protection with a biobased, air-powered spray can alternative to petroleum-based corrosion inhibitors packaged in traditional aerosols.
Contact Cortec® to learn more about this new release:
https://www.cortecvci.com/contact-us/
View the product data sheet here:
https://www.cortecvci.com/Publications/PDS/EcoAir_Biobased-Outdoor-Coating-3690.pdf
Cortec® Corporation is the global leader in innovative, environmentally responsible VpCI® and MCI® corrosion control technologies for Packaging, Metalworking, Construction, Electronics, Water Treatment, Oil & Gas, and other industries. Our relentless dedication to sustainability, quality, service, and support is unmatched in the industry. Headquartered in St. Paul, Minnesota, Cortec® manufactures over 400 products distributed worldwide. ISO 9001, ISO 14001:2004, & ISO 17025 Certified. Cortec Website: http://www.cortecvci.com