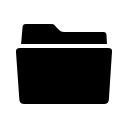
Uncategorised (4996)
Australian listed oil and gas independent, founded by two Scots, set to capitalise on major gas find onshore Western Australia
AdministratorWarrego Energy spuds second well on West Erregulla concession in the Perth Basin.
Warrego Energy, along with its 50:50 joint venture partner, Strike Energy, has announced the spudding of its second well, West Erregulla 3 (WE3) on the EP469 concession in the Perth Basin, onshore West Australia.
After a safe and successful mobilisation and third-party inspections, the joint venture’s Ensign Rig 970, began drilling on Monday 21st September 2020.
This is the second well to be drilled by Warrego following its ground-breaking WE2 well drilled last year. WE3 is the first of a three well appraisal drilling campaign on the West Erregulla field located within exploration permit 469 which Warrego Energy acquired in 2007. The field forms part of a triangle between Mitsui’s Waitsia wells and Beach Energy’s Beharra Springs Deep, which has been claimed to have the potential to hold a world-class hydrocarbon deposition.
West Erregulla-2 was spudded in June 2019 and drilled to a total depth of 5,100 metres, the deepest well drilled in onshore Australia, flow tests achieved a world class maximum flow rate of 69million standard cubic feet of gas per day.
Dennis Donald (left) and Duncan NacNiven of Warrego Energy
This latest appraisal drilling campaign is one of a string of positive announcements for Warrego Energy, which was formed in late 2007 by Scots Dennis Donald and Duncan MacNiven. For thirteen years, the founders have battled to build a leading international oil and gas company that will respect and tread lightly on the land. The company is managed by entrepreneurs and is committed to maximising stakeholder value through the application of new technologies and thinking.
Chief executive, Dennis Donald, said: “Despite significant odds, we have taken the company to a point where Warrego Energy has the potential to become a formidable energy business. The major discoveries of the West Erregulla-2 well helped consolidate our position as a key player in the Perth Basin and has laid the foundation for exploration and appraisal success through our current campaign.
“Warrego Energy truly is on the cusp of becoming a major, international onshore, conventional gas exploration and production company. Very few oil and gas businesses start with a bare exploration block and move through a ten-year plus work sequence to eventually take that block into production. We truly believe that we will achieve that distinction.
“We share the widely held view that natural gas is a transition fuel – one which will enable future renewable energy solutions. Natural gas, the cleanest burning hydrocarbon source, will play an increasing role in addressing climate change. LNG terminals are being constructed around the world at pace, making gas easily transportable and competitive with oil and other energy sources. With a significant, readily accessible, unencumbered conventional gas resource, Warrego Energy intends to play its part in the energy transition in Western Australia and Europe.
“With the advent of the 5-year delays to the offshore Browse and Scarborough projects the energy hungry Western Australian domestic market will be an even more receptive market for Warrego’s production gas.”
Following the reverse take-over of Petrel Energy in 2019, Warrego Energy acquired a listing on the Australian ASX market and excellent prospective assets in Spain. Their Tesorillo onshore project is in the final stages of gaining government permit approval. The North African Maghreb-Europe gas trunkline which makes landfall within the permit area, will provide ready access to lucrative Spanish and Portuguese gas markets.
Duncan MacNiven added: “It’s been a roller-coaster of a ride but we’re now well on our journey to realise the true underlying value of our total asset portfolio.
“Our interests in two continents, Australia and Europe, mean that we can fast-track key learning and introduce enabling technologies between each.
“Global political and economic conditions, which had deteriorated in 2019, have only worsened this year with the coronavirus pandemic. However, with our agile, responsive approach, free from the bureaucracy and overhead burden of many traditional oil and gas businesses, we are responding well. The skills and experience inherent in our lean team reduce technical and investment risk, ensure efficient execution and maximise the potential for all stakeholders.
“We’re concentrating on our high-grade assets with above average geological and geophysical features, excellent proximity to pipelines, infrastructure and markets and low-cost development potential.
“With David Biggs, a highly experienced and capable CEO, in place in Australia, Dennis and I are now focused on building out our European operations, engaging investors and maximising current appraisal and production projects in Spain.”
Deep Casing Tools continues its relationship with Shell Malaysia
AdministratorTechnology development company for the global energy sector, Deep Casing Tools (DCT), together with its regional partner for Asia Pac, EFTECH, has successfully ran 3 more of its Turborunner TM tools with Shell Sarawak, despite challenging conditions heightened by COVID-19.
The scope of work, which was awarded to DCT in 2018, required horizontal well completions in six new wells to ensure target depth (TD) could be reached. The work was carried out on the Naga 7 jack-up rig located offshore, Miri, Sarawak, which Shell Sarawak contracted from Velesto Drilling in 2018 to support its offshore oil exploration and production, and offshore gas production in the region.
Despite challenging conditions including tight spots in all six wells, the runs were completed successfully by August 2020 by deploying DCT’s best in class turbine-powered completions tool, Turborunner TM, which allowed the energy major to reach TD.
Turborunner TM was deployed due to its track record of landing completion strings and liners at TD first time, even in complex wells and with challenging open hole conditions. It uses high speed reaming to reduce potential equipment damage, create less downtime, eliminate wiper trips and open hole exposure and enable cost-effective drill through and drill ahead.
In addition to the tight spots, the restrictions on travel for overseas personnel as a result of COVID-19 created further challenges. DCT was able to overcome this as a result of its well-established relationship with EFTECH, the leading provider of process and pipeline services to the offshore industry, which is headquartered in Malaysia.
Together, DCT and EFTECH were able to provide on-the-ground field support to oversee the running of the tools, whilst complying with social distancing requirements set by the local government and the operator. This was bolstered by remote support and monitoring by DCT’s technical operations team based at its headquarters in Aberdeen, Scotland. Furthermore, the customer benefited from rapid tool mobilisation due to the partnership’s in-region warehouses facilities.
Deep Casing Tools Workshop
Neil Hathaway, Regional Manager at DCT, said: “The success of this project is testament to our commitment over the last decade to grow our international capabilities through a network of experienced and dedicated partners around the world. By partnering with EFTECH who have amassed nearly two decades of experience of servicing the offshore sector in the Asia Pac region, we were able to deliver an unrivalled level of service to our customer Shell Sarawak.
“It is also another excellent example of our simple innovation which make operations safer and more efficient, even in the most complex and challenging conditions. We are looking forward to building the relationship further with EFTECH and Shell Sarawak, as well as continuing to bring further innovative solutions to the oil and gas downhole market.”
About Deep Casing Tools
- • Deep Casing Tools is a global oil and gas technology development firm
- • Established in 2008 and headquartered in Aberdeen
- • Focused on the UKCS, Middle East, Asia Pacific and North America
- • Unique, patented drillable turbine technology provides a step change in performance
- • Motorised reaming tools clear obstructions and ream tight hole without string rotation
- • Powering a reamer shoe at the bit provides maximum energy and reduces cost and risk
- • More than 500 tools sold to major oil and gas operators worldwide
- • Several exciting new solutions in development and testing
New AkzoNobel powder coatings plant rises up in digital transformation
AdministratorMore advanced powder coatings solutions will be available to customers in Taiwan now that a state-of-the-art and sustainable plant is being built by AkzoNobel in Chungli.
The fully automated plant, which represents a €20 million investment, will have the increased production capacity to fulfill growing demand in the architecture, auto accessories, telecommunications, electronic components, furniture, domestic appliances, sports equipment and machine tools markets.
Once operational, the new plant will bring the company closer to its overall energy and water sustainability ambitions. It’s expected to reduce energy consumption by 30%, increase the water reuse rate to 60% and achieve zero VOC emissions – in addition to creating a safer and healthier working environment.
“The COVID-19 pandemic has brought a lot of uncertainties to global markets,” said Fred Moreux, Director of Manufacturing for Asia at AkzoNobel. “Investing in a new plant in Taiwan at this critical time will help us streamline our supply chain while setting a new benchmark in the local paints and coatings industry.
AkzoNobel’s multisite in Chungli already consists of manufacturing plants for powder coatings, decorative paints, packaging coatings and specialty coatings. The addition of this new powder coatings plant is leading Taiwan’s industry upgrade process to create significant production leverage and value.
“AkzoNobel has been in the Taiwan market for more than 40 years and is a known leader of its paints and coatings industry,” said Karen Yin, Director of Commercial Powder Coatings at AkzoNobel. “The new plant is driven by growing customer demand for tailored solutions and will consolidate our leading position.”
The powder coatings plant in Chungli is expected to start operating in the third quarter of 2021.
About AkzoNobel
AkzoNobel has a passion for paint. We’re experts in the proud craft of making paints and coatings, setting the standard in color and protection since 1792. Our world class portfolio of brands – including Dulux, International, Sikkens and Interpon – is trusted by customers around the globe. Headquartered in the Netherlands, we are active in over 150 countries and employ around 33,000 talented people who are passionate about delivering the high-performance products and services our customers expect.
Nouryon launches new Levasil colloidal silica line for the electronics industry
AdministratorNouryon has introduced a new Levasil® colloidal silica product line dedicated to the electronics industry. This latest addition to the Levasil line provides customers with a colloidal silica of superior purity to shape, smooth and polish high-performance substrates such as silicon wafers, required in the production of integrated circuits for electronic devices.
Nouryon currently has Levasil products available with five modification types. The latest line, with potassium as the stabilizing ion, enables Nouryon to offer a new range of solutions to the electronics industry where purity and performance are essential. Demand is particularly strong in Asia, where the majority of customers for these materials are located.
“The fast-changing electronics industry constantly increases demand for higher-performance, higher-purity solutions to be able to meet consumer needs today and in the future,” said Patrick Wilhelm, Vice President of Colloidal Silica at Nouryon. “This new product line has been developed to meet those demands,” he said.
Johan Landfors, President of Technology Solutions at Nouryon, added: “This is an important addition to our product portfolio and shows our dedication to deliver innovative solutions to our customers in high-tech industries. It is also in line with our growth ambitions for Asia.”
Click here for more information on Nouryon’s products for the electronics industry.
About Nouryon
We are a global specialty chemicals leader. Markets worldwide rely on our essential chemistry in the manufacture of everyday products such as paper, plastics, building materials, food, pharmaceuticals, and personal care items. Building on our nearly 400-year history, the dedication of our 10,000 employees, and our shared commitment to business growth, strong financial performance, safety, sustainability, and innovation, we have established a world-class business and built strong partnerships with our customers. We operate in over 80 countries around the world and our portfolio of industry-leading brands includes Eka, Dissolvine, Trigonox, and Berol.
Valmet signs an automation service agreement with Viridor in the United Kingdom
AdministratorValmet and Viridor have signed a three-year service agreement for six waste-to-energy plants in the United Kingdom. The agreement covers maintenance and technical support, cybersecurity services, and lifecycle services and upgrades for the plants’ automation systems, helping to ensure the availability and security of the systems also in the future.
The agreement was signed during the second quarter of 2020.
“We have selected Valmet for a new three-year, multi-site service agreement of the distributed control systems within our Energy Recovery Facilities. This is based upon the positive experience we have had with Valmet’s expertise and support across our fleet since the completion of our very first energy from waste plant,” says Dave Field, Viridor Director of Engineering (Energy).
Valmet and Viridor have signed a three-year service agreement for six waste-to-energy plants in the United Kingdom, one of which is Runcorn Energy Recovery Facility.
“We have had a positive relationship with Viridor for a long time, and we appreciate their trust for our services and Valmet in general. Our proactive services and response times are highly valued by Viridor as it makes system-related downtime negligible. With this service agreement, Viridor’s automation system will be even better protected and up to date in the future as well,” says Samuel Asuming, UK Area Service Manager, Automation, Valmet.
The long-term relationship further strengthened by the service agreement
Valmet has previously supplied Valmet DNA distributed control systems and services to Viridor’s waste-to-energy plants in Ardley, Beddington, Cardiff, Dunbar, Peterborough, and Runcorn. Now the agreements and services associated with each site have been unified with one service agreement covering all the plants.
Maintenance and technical support, cybersecurity services, and lifecycle services for the plants’ automation systems are covered by the new service agreement. Spare parts and repairs, lifecycle plans, and automation upgrades are carried out additionally by demand.
Information about the customer Viridor
Employing more than 3,200 people, Viridor is one of the largest recycling, energy recovery, and waste management companies in the UK with the UK’s largest network of 300+ advanced recycling, energy recovery and landfill diversion facilities. Viridor has 150 local authority and major corporate clients with 32,000 customers across the UK. Its full range of services includes recycling and waste advice and auditing, advanced materials recycling, glass and plastics reprocessing, composting, mechanical and biological treatment, anaerobic digestion, waste to energy, transport, collection, landfill disposal, and habitat restoration and management. In total it safely manages more than eight million tons of recyclables and waste materials for customers from all sectors across the UK.
Valmet is the leading global developer and supplier of process technologies, automation and services for the pulp, paper and energy industries. We aim to become the global champion in serving our customers.
Valmet's strong technology offering includes pulp mills, tissue, board and paper production lines, as well as power plants for bioenergy production. Our advanced services and automation solutions improve the reliability and performance of our customers' processes and enhance the effective utilization of raw materials and energy.
Valmet's net sales in 2019 were approximately EUR 3.5 billion. Our more than 13,000 professionals around the world work close to our customers and are committed to moving our customers' performance forward - every day. Valmet's head office is in Espoo, Finland and its shares are listed on the Nasdaq Helsinki.
Read more www.valmet.com
Valmet to supply filter fabrics with smart cloth technology to Karara Mining in Australia
AdministratorValmet will supply filter fabrics with smart cloth technology to Karara Mining Ltd in Western Australia. Karara is the largest mining operation and the first major magnetite mine in the Australia’s Midwest region.
The delivery includes filter fabrics to 11 chamber press filters used for concentrate and tailings de-watering.
The order was included in Valmet's orders received of the second and third quarter 2020. The value of the order will not be disclosed.
Karara’s target is to increase cloth life, improve machine availability and subsequently increase the production with new technology. In the beginning of 2020, Karara organized a pilot project to identify a supplier who could provide world class filter fabrics with technical support. Valmet’s filter fabrics stood out with excellent results.
“We are always seeking for innovative and world class technology, and for that reason we organized a pilot project to select the cloth with best performance. The average cloth life of Valmet cloths is approximately 5,500 cycles whereas the current supplier’s is approximately 1,500 cycles, which brings tangible benefits to our operation,” says Gavin Kelly, Production Coordinator, Karara.
“The extensive site trials provided the customer with valuable data insight regarding the technical and commercial benefits. We are happy to win the order based on our proven technology and trusting relationship with the customer,” says Michael Murphy, Product Sales Manager, Australia, Valmet.
Information about the delivery
Valmet cloths are equipped with smart cloth technology, Valmet's Industrial Internet application for optimizing filter cloth performance to increase productivity and create savings in filtration processes. Operators use an easy-to-use tablet interface to load data during cloth installation and removal. The online reporting portal provides real time concise data to the stakeholders, such as early stage plate damage and failure patterns that enables real time process improvement.
Information about Karara Mining Ltd
Karara Mining Ltd was established in 2007 through a joint venture between China’s Ansteel Group – the Anshan Iron and Steel Group Corporation and Gindalbie Metals Limited to develop and operate the Karara mine. Karara produces a premium, high-grade (66-68% Fe) magnetite concentrate at a design production rate of 8 million tons per annum.
For further information, please contact:
Jaegen Peet, Director, Australia and New Zealand, Valmet, tel: +61 400016281
Valmet is the leading global developer and supplier of process technologies, automation and services for the pulp, paper and energy industries. We aim to become the global champion in serving our customers.
Valmet's strong technology offering includes pulp mills, tissue, board and paper production lines, as well as power plants for bioenergy production. Our advanced services and automation solutions improve the reliability and performance of our customers' processes and enhance the effective utilization of raw materials and energy.
Valmet's net sales in 2019 were approximately EUR 3.5 billion. Our more than 13,000 professionals around the world work close to our customers and are committed to moving our customers' performance forward - every day. Valmet's head office is in Espoo, Finland and its shares are listed on the Nasdaq Helsinki.
Read more www.valmet.com
AFRY acquires the software and expertise company Ramentor in Finland
AdministratorWith the acquisition of Ramentor, AFRY further strengthens its digitalisation capabilities and advances RAMS offering for clients. Ramentor develop and distribute Reliability, Availability, Maintainability and Safety (RAMS) software tool, ELMAS. In addition, Ramentor also provide expert services and solutions, and training related to the RAMS methodology.
RAMS services are used by major technology, manufacturing and industrial service companies, including private and public infrastructure companies, both with local and global coverage. By using RAMS, AFRY can help clients make more informed decisions, optimise their risk level and overall life-cycle costs and support them in their digital transformation to more sustainable and cost-efficient solutions.
- RAMS engineering and consulting services are foreseen to be increasing in the coming years and are a key part of our energy and industry markets transition strategy. By integrating RAMS to current industry technical design practices we will create a unique differentiator for our services, says Richard Pinnock, Head of Division Energy, AFRY.
- We are excited to be part of AFRY. We have two decades of solid R&D and pragmatic industry project history on dependability management, and the market is clearly maturing now along with digitalisation. Together with AFRY we can take our services to the next level by adding a significant global client base and support in future engineering and digitalisation, says Timo Lehtinen, Managing Director of Ramentor.
The company has annual sales of about SEK 7,4 million and has 6 employees in Finland. Ramentor is planned to be consolidated into AFRY’s Energy division by early 2021.
AFRY is an international engineering, design and advisory company. We support our clients to progress in sustainability and digitalisation. We are 17,000 devoted experts within the fields of infrastructure, industry and energy, operating across the world to create sustainable solutions for future generations.
Making Future.
The wind power company Svea Vind Offshore now starts Svea Green Foundation to accelerate the transition to a sustainable society for current and future generations. The foundation will work locally, regionally, nationally and eventually also internationally.
- The climate issue is urgent which means that leadership and action are required, from politics, business and society at large. Through Svea Vind Offshore, we work to increase the proportion of renewable energy and thus want to contribute to restructuring society. With a foundation, we can complement that work and have the opportunity to work even more broadly. Through the company and the foundation, we have taken leadership in the green transition, says Maria Brolin, founder and chairman of Svea Green Foundation.
Lisa Wärn och Maria BrolinThe foundation's initial focus in the transition to a sustainable society are efforts that limit global warming in order to contribute to the development of sustainable scenarios presented by the UN's climate panel IPCC. The foundation's work can be done both by initiating and running projects and by supporting or participating in projects or innovations that align with the foundation's purposes.
Lisa Wärn has been appointed CEO of the foundation. Until recently, she worked as deputy chief of staff and communications director at TCO, The Swedish Confederation of Professional Employees. Lisa Wärn has worked in politics, communication and with leadership issues for 20 years in Government Offices, civil society and the business world.
- We are thrilled for having recruited Lisa Wärn as CEO of Svea Green Foundation. Her broad experience from both politics, business and civil society combined with her deep commitment to society and climate issues means that we know that she will undertake the task in a responsible way, says Maria Brolin, founder and chairman of Svea Green Foundation.
- For me leading Svea Green Foundation is a fantastic opportunity. My commitment to environmental issues began at the age of 10 and now the climate issue is more pressing than ever. We cannot wait to implement measures, we must act very forcefully, says Lisa Wärn, CEO of Svea Green Foundation.
Svea Vind Offshore is an entrepreneurial company that acts as a catalyst as we enable wind power in suitable locations based on economy, technology and the environment. The company was started in 2015. The founders are driven by a desire to make a difference and contribute to a sustainable world both in terms of climate and job creation locally where they operate. The head office is located in Gävle, Sweden.
Semcon leads new research project to investigate how big data can streamline product development
AdministratorHow can companies use big data to improve their product development? With this question in focus, the Research Council of Norway is awarding funding to Semcon for a new research project. The project will investigate how companies delivering complex systems can use big data to increase the efficiency of their technology and innovation processes.
The rapid evolution and increasing complexity of technology places higher demands on companies to collaborate and share best practice. In particular, since technology and systems now need to integrate with each other. How this can best be achieved will be investigated in the new research project "Harvesting value from Big Data and Digitalisation through a Human Systems-Engineering Innovation Framework".
"The aim of the project is to strengthen the participating companies and academia by creating a framework for collaboration. The focus will be on tools and methods to improve the product development process. It is essential to be able to make data-aided decisions early in the development process", says Lasse Bjørkhaug, Project Manager at Semcon and for the research project.
In addition to creating a framework for collaboration, the project will investigate in more detail how information from data can be adapted to users. Furthermore, the project will develop a validated process to ensure that companies can efficiently use big data in co-creative processes when technology needs to be integrated.
– Today the access to data is enormous. Norwegian companies can, with the right approach and right algorithms, structure and make use of big data in a way that can give decisive competitive advantages in an international market, says Kristin Falk, professor at the University of South-Eastern Norway (USN).
The research project is phase 2 of the program “Human Systems-Engineering Innovation Framework (H-SEIF), which aimed at making product development more focused on user needs. A total of twelve partners will participate in the project, including USN where Semcon is working closely with Campus Kongsberg.
"It is very important for us to always stay up-to-date with the latest research in order to be able to offer our customers leading-edge technology. To be able to run this project creates great opportunities going forward, not only for all of the participants in the project but also for Semcon's customers", says Lasse Bjørkhaug.
Semcon has been awarded funding from the Research Council of Norway for the research project, which will be run by Semcon in collaboration with USN and will extend over three years. Other partners include The Oslo School of Architecture and Design, Ulstein Group, Kongsberg Maritime, Kongsberg Defence and Aerospace, ETH Zürich, Indra Navia, Kongsberg Innovasjon, Chalmers University of Technology, Norwegian Mapping Authority and TechnipFMC.
Read more about research and innovation at Semcon.
Semcon is an international technology company that develops products based on human needs and behaviours. We strengthen our customers’ competitiveness by always starting from the end user, because the person who knows most about the user’s needs creates the best products and the clearest benefits to humans. Semcon collaborates mainly with companies in the automotive, industry, energy and life science sectors. With more than 2,000 specialised employees, Semcon has the ability to take care of the entire product development cycle, from strategy and technology development to design and product information. Semcon was founded in Sweden in 1980 and has offices in over 30 locations in eight different countries. In 2019, the Group reported annual sales of SEK 1.9 billion. Read more on www.semcon.com
Azelio strengthens its presence in California further by joining The California Solar & Storage Association, CALSSA. The association is the state’s largest clean energy business group with over 550 member companies.
“California is one of the largest and most successful solar markets in the world, where we also see a strong interest in our energy storage solution. By joining CALSSA we show our commitment to building a strong regional platform and becoming part of the community,” says CEO Jonas Eklind.
“We warmly welcome Azelio into CALSSA,” said Bernadette Del Chiaro, Executive Director of the California Solar & Storage Association. “California embraces all forms of solar energy and energy storage into our vibrant, competitive, and expanding marketplace and we are thrilled to have Azelio’s unique offerings come here.”
After having signed three MoUs for California in the past year, Azelio continues to consolidate its position in that market. California is the world’s fifth largest economy and has set a goal of relying entirely on zero-emission energy sources for its electricity production by 2045. To reach its goal, the state aims for 50 percent of its electricity to be powered by renewable resources by 2025 and 60 percent by 2030. Energy storage will play a critical role in this transition making solar and wind power available around the clock. Specifically, long duration storage solutions, such as Azelio’s TES.POD can contribute to providing resiliency and security of power supply, especially in the critical periods of Californian wildfires.
The California Solar & Storage Association represents an array of businesses that manufacture, design, install, finance and provide other resources to the growing local solar and storage market in California. The association has advanced the common interest of the solar and storage industry for over 40 years, making California the most robust market in the U.S.
About Azelio
Azelio is a public Swedish company specialising in thermal energy storage with dispatchable power. The technology is revolutionary for its unique capability to produce electricity and heat from the storage on demand at all hours of the day. The system stores energy in recycled aluminium and has a total efficiency of up to 90% from energy to heat and electricity. It is scalable and cost-efficient from 0.1 MW up to 100 MW and suffers no reduced capacity over time. Azelio has 150 employees, is headquartered in Gothenburg with production facilities in Uddevalla, development centres in Gothenburg and Åmål (Sweden), as well as a presence in Stockholm, Beijing, Madrid, and Ouarzazate (Morocco).
Azelio is listed on Nasdaq Stockholm First North. FNCA Sweden AB is the company’s certified adviser: +46(0)8-528 00 399, This email address is being protected from spambots. You need JavaScript enabled to view it.. More about Azelio: www.azelio.com
More...
~ Three equipment upgrades for agility and efficiency ~
In July 2020, the Met Office reported that most UK water companies have seen an increase in average water consumption during lockdown, especially those operating in suburban areas. It’s clear that COVID-19 measures around the world have resulted in societal changes that are directly impacting when and how much water people are consuming. So, how do water companies prepare for an unexpected surge or drop in demand? Here, Marek Lukaszczyk, European and Middle East marketing manager at WEG a leading global manufacturer of motors and drives, explores three equipment upgrades that water companies can make, which will increase their agility and efficiency.
The United Nations World Water Development Report 2020, states that global water usage has increased by a factor of six over the past 100 years. Climate change is undoubtedly a longstanding consideration for water management, but low rainfall, high population density and intensive agricultural or industrial activity may also result in sustainability issues — without throwing a global pandemic into the mix.
Faced with these challenges and aging infrastructure, the European water industry is focussing on rejuvenating its existing assets, building resilient systems, and improving operational and energy efficiency. So where should a water company start in implementing system upgrades?
The totex based approach for the water industry
Firstly, it’s important to build an effective strategy. The totex (total expenditure) approach continues to reshape the water industry. This framework considers total cost throughout the lifecycle of a project, allowing water companies to be assessed against long-term outcome measures. In addition to cutting costs, the framework looks to provide better value to consumers, achieve better efficiency management and operational efficiency. Predictability is therefore high on the optimisation agenda, through close integration and collaboration with manufacturers at the design stage.
Cutting down wastage
Waste, in the form of unnecessary energy usage or pesky pipe leaks, can be a real problem, affecting a water company’s maximum output. According to the International Energy Agency, a quarter of the electricity consumed by the water sector is for wastewater collection and treatment. For this reason, it is especially important that companies operating in this space consider investing in energy efficient technologies. Reducing energy wastage not only offers environmental and cost saving benefits, but also allows businesses to commit more resources to meet changing demands.
Opting for an energy efficient motor that conforms to IE4 and IE5 standards is a good place to start, but it’s also important to ensure the motor is matched to the load. For example, at a water pump station in Surrey, UK, WEG supplied three 900kW W50 IE4 super premium efficiency motors with IP55 protection, operating at 96.9 percent efficiency. With new pump impellers, gearboxes, drives and the WEG motors, the facility was upgraded from its existing 400 mega litres per day capacity to 750 mega litres per day, with an efficiency increase from 80 percent to 86 percent.
Water treatment
Condition monitoring
To ensure that motors are running optimally, water plant managers can retrofit sensors. By using smart technology such as Industrial Internet of Things (IIoT) data, water companies can monitor their assets and processes in real-time, allowing them to ensure that their systems are performing optimally and respond quickly to unexpected events.
Key metrics such as vibration and temperature changes can be early indicators of more serious system faults. This predictive maintenance approach reduces the risk of downtime and consumer disruption.
Using a variable speed drive (VSD)
Pumps consume a large proportion of the energy usage of electric motors. Upgrading to a VSD instead of a fixed speed motor allows companies to account for varying process load. A VSD can automatically control the speed of the motor and rapidly respond to the required demand. This also allows for a more efficient operation, instead of continually operating at a water flow designed for maximum demand of the system.
Going one step further, companies can invest in sophisticated process control software, such as WEG’s Pump Genius. This built-in VSD software enables engineers to increase their process accuracy and protection, while offering system monitoring. The software, allows one VSD to control up to five pumps, monitoring the operating hours and adding and subtracting pumps as demand changes. Automatic broken pipe detection in the VSD can also identify fluid leakage and adjusts motor performance accordingly.
To facilitate the successful implementation of equipment upgrades in the water industry, it’s important to have strong partnerships with reliable equipment manufacturers. By implementing the totex framework, intelligent design decision making can be achieved, which will give water companies of all types, added flexibility, better performance and superior cost savings.
For further information about WEG’s energy efficient motors, VSD’s and pump genius systems for the water industry, visit the website
About WEG: Founded in 1961, WEG is a global manufacturer of electrical and mechanical equipment for industrial sectors across all continents. With manufacturing units in 12 countries and present in more than 135 countries, the company has more than 31,000 employees worldwide with net revenue of over R$13.3 billion in 2019.
Offering energy efficient solutions across all sectors including water, steel, pulp and paper, oil and gas, mining, among many others, WEG is constantly developing solutions to meet the major trends in energy efficiency, renewable energy, sustainability and electric mobility. For more information, visit www.weg.net
Ref: WEG024/06/20
Goodfellow is pleased to announce the addition of six chemical compounds for use in Li-ion batteries. Each of these materials offers something different in terms of the variables associated with Li-ion batteries, such as energy density, potential safety, cost, recharging time, cycle life, scalability, etc. Customers are encouraged to contact a member of the Goodfellow technical team to discuss specific application requirements.
A lithium-ion battery consists of a cathode (positive electrode), an anode (negative electrode), and an electrolyte (used as a conductor) with a charge-discharge cycle.
Li-ion battery technology
Cathode materials*
LiCoO2 Lithium Cobalt Oxide
As one of the most common oxide cathode materials for traditional Li-ion batteries, LiCoO2 (LCO) is also under consideration for use in all solid-state batteries.
LiMn2O4 Lithium Manganese Oxide
The spinel lithium manganese oxide (LiMn2O4 or LMO) is an exceptional cathode material for aqueous and organic lithium-ion batteries due to its low cost, environmental friendliness and suitable potential capabilities.
LiNi0.5Mn1.5O4 Lithium Nickel Manganese Oxide (LNMO)
Lithium nickel manganese oxides are promising, being nontoxic while having high thermal stability. They currently are attracting attention as alternative cathode electrode materials to the commercial LiCoO2 electrode.
Anode materials*
Li4Ti5O12 Lithium Titanium Oxide
LTO (Li4Ti5O12) has been highlighted as anode material for next-generation lithium ion secondary batteries due to advantages such as a high rate capability, excellent cyclic performance, and safety.
Solid electrolytes*
Li7La3Zr2O12 Lithium Lanthanum Zirconium Oxide (LLZO)
Solid-state electrolyte lithium lanthanum zirconium oxide garnet (LLZO) has attracted a great deal of attention due to its high room temperature conductivity of lithium ions and stability against lithium metal electrodes.
Li4SiO4 Lithium Orthosilicate
This is a solid-state electrolyte for lithium-ion batteries and specifically for the production of solid-state thin film batteries (TFB).
Other products available from Goodfellow which can be used in lithium batteries
Li3PO4 Lithium Phosphate – a thin film solid electrolyte material known as LiPON used in thin film lithium batteries (TFB).
Copper foils (as current collectors), nickel foils, cobalt foils, aluminium foils (battery slurry)
Graphite – for negative electrodes
Silicone elastomer in any form
PVDF films – used as binders, depending on the battery
*Available as sputtering targets, or in powder form upon request.
About Goodfellow
For more than 50 years, Goodfellow has been a leading supplier of metals, polymers, ceramics and other materials to meet the needs of science and industry worldwide. The company specialises in supplying small quantities (a few grams to a few kilos) of metals and materials for research, prototype development and specialised manufacturing applications. Standard products can be found online at the comprehensive Goodfellow Catalogue. Custom products and materials in larger quantities are available upon request at This email address is being protected from spambots. You need JavaScript enabled to view it..
Goodfellow Cambridge Limited
Ermine Business Park, Huntingdon, PE29 6WR, UK
Telephone: +44 1480 424800 Fax: +44 1480 424900
E-mail: This email address is being protected from spambots. You need JavaScript enabled to view it. Web: www.goodfellow.com
Logistics specialist, the Rhenus Group, has invested in its automotive offering, with the launch of its Full Vehicle Logistics department in the UK to further meet the needs of its automotive customers worldwide.
The Rhenus Group, which has a longstanding history working across the automotive sector, has expanded its in-house capabilities to offer customers a full range of logistics services under one provider.
To date, Rhenus UK has largely supported the automotive sector with the transportation of vehicle parts and sub-assembly projects, with the support of its automotive competence centres across Europe. With the introduction of Full Vehicle Logistics, it has increased its capabilities to work on additional specialist automotive movements, from transporting one-of-a-kind prototypes through to managing full customs clearance for individual vehicle shipments across the globe.
The latest shipment from the Rhenus Full Vehicle Logistics team was a Bugatti Divo, valued at £5m and one of only 40 models produced.
The Full Vehicle Logistics team focuses on servicing three key customer groups - individuals, dealerships and OEMs.
Spencer Davern, Air & Ocean director at Rhenus UK, commented: “The launch of Full Vehicle Logistics allows Rhenus to further expand its automotive offering and focus on the movement of complete cars via air, ocean or road. The fact we have invested in a new department during these unprecedented times is a testament to our dedication to the automotive sector. As we head towards the completion of Brexit, it is going to be more beneficial than ever for businesses to keep their transportation needs under one roof, with a provider that can deliver complete support from start to finish, including customs clearance.
“I’m proud to be working with such a talented team and look forward to completing many more high security, high profile and high value movements.”
For more information on Rhenus visit https://www.rhenus.com/en/uk/
About Rhenus
The Rhenus Group is a leading logistics service provider with global business operations and an annual turnover of EUR 5.5 billion. Rhenus has business sites at 750 locations worldwide and employs 33,000 people. The Rhenus Group provides solutions for a wide variety of different sectors along the complete supply chain; they include multimodal transport operations, warehousing, customs clearance as well as innovative value-added services.
Industry-leading technology to manage, connect and optimize heat trace systems
Thermon Group Holdings, Inc. (NYSE:THR) (“Thermon”), a global leader in industrial process heating, announces the Genesis™ Network, a new solution providing site-wide operational awareness and supervisory control of heat trace systems.
With the Thermon Genesis Network, users save maintenance hours, increase up-time, and can make upgrades and changes with greater flexibility. Users can easily monitor, maintain, and troubleshoot even the largest heat trace systems that may include over 10,000 heat trace circuits. The Genesis Network connects heat trace controllers with the control room using wireless communications. The solution presents alarms, history, and operational data via a user-friendly, browser-based interface accessible from any network connected computer or mobile tablet. Utilizing an adaptive, self-healing wireless mesh network and event-driven communications, users experience reliable, real-time status reporting and responsive control of their heat trace systems.
“We are excited to introduce the Genesis Network, a step forward to the true industrial internet of things (IIoT) for our customers and our industry. Like the Genesis Controller, the Genesis Network delivers a smart, fully-connected experience that is easy to learn and use. Thermon is bringing the best of high tech to our industry. We look forward to helping customers safely increase efficiency, reduce maintenance time, and optimize operations with this solution,” said David Buntin, Senior Vice-President, Thermon Heat Tracing.
The following new components work together to form a Genesis Network:
- ·Genesis Server- An on-premises or cloud deployable server
- ·Genesis Gateway- A communications device between the server and wireless mesh
- ·Genesis Bridge – A communications device between the mesh and heat trace controllers
Streamlined Maintenance and Operations
Maintenance personnel need timely and complete awareness of the trace heating system to prevent downtime and optimize operations. They also require information at their fingertips to troubleshoot issues quickly and accurately. The Genesis Network answers these challenges by delivering alarm management, setting optimization, historical analysis and operational reporting. The solution can save hundreds of man-hours through the use of historical data to optimize settings and accurately flag outlier behaviors while avoiding nuisance alarms, resulting in fewer maintenance hours. The Genesis Network also saves time by filtering and prioritizing alarms and generating reports with the right information to make efficient decisions.
IIOT Advantage
The Genesis Network is architected as a true IIOT (industrial internet-of-things) solution. An intuitive browser-based user interface gives users quick access for performing alarm management, report generation, data trending, and performance optimization of heat trace circuits while on-the-go from any network-connected laptop or mobile tablet with a browser. Adding or changing devices is a simple drag-and-drop activity. Software updates to the network can also be deployed to all devices via the browser interface making the roll out of new features simple, increasing the value of the solution over time. The solution brings the best of IIOT technology to our customers.
Security
Designed with security in mind, from data encryption and authentication to secure updates, operational leaders can deploy the Genesis Network with peace of mind. In applications where wireless communications are prohibited, the network can be configured using a traditional wired solution.
The Genesis Network is an industry leading IIoT solution that streamlines maintenance operations by providing operational awareness, management and supervisory control of heat trace systems. To inquire about the new system, contact This email address is being protected from spambots. You need JavaScript enabled to view it., or visit www.thermon.com.
About Thermon
Through its global network, Thermon provides safe, reliable and mission critical industrial process heating solutions. Thermon specializes in providing complete flow assurance, process heating, temperature maintenance, freeze protection and environmental monitoring solutions. Thermon is headquartered in Austin, Texas. For more information, please visit www.thermon.com.