
Super User
Bally Ribbon Mills Offers Industrial Fabrics Ideal for Polymer Manufacturing and Rolled Raw Material Processing
Specialty fibers withstands wear surface abrasion caused during manufacturing processes
Bally Ribbon Mills (BRM), an industry leader in the design, development, and manufacture of highly specialized engineered woven fabrics, offers specialty fabrics constructed of specialty polymer fibers ideal for polymer manufacturing and break bands for rolled raw material processing.
BRM’s proprietary narrow fabrics feature woven structures with finished woven structural edges that provide a strong belting material. Able to withstand flex-fatigue caused by bending motions, the fabric’s fiber structure withstands wear surface abrasion from manufacturing processes and offers resistance to wear caused by the movement and interaction with material being processed.
BRM also manufactures narrow fabrics that are used as break bands in the industrial processing of rolled raw materials, like weaving yarns and metallic wire processing equipment, where manufacturing efficiency requires tight control of the process and input volumes. With low elongation, high strength, and resistance to surface wear, BRM’s proprietary fabrics are ideal for manufacturing polymer fiber or metallic wire. The fabric is tensioned over a channeled spool-end which imparts frictional forces between the fabric and the spool flange to reduce roll inertia.
For more information on BRM’s industrial fabrics, go to www.ballyribbon.com.
About Bally Ribbon Mills
Bally Ribbon Mills (BRM) designs, develops, and manufactures highly specialized engineered woven webbing, tapes, specialty fabrics, woven preforms, and two dimensional and three dimensional structural fabrics. With more than 95 years of textile manufacturing experience, BRM has earned a reputation for meeting new advanced design challenges. Working in aerospace, defense, medical, safety, automotive, commercial, and industrial applications, BRM offers ingenuity, technical know-how, extensive weaving capabilities, and rigorous quality assurance systems. For more information, visit www.ballyribbon.com
Electric Actuation with the Speed and Reliability of Pneumatics
Warren Controls ARIA Series Designed with Customers in Mind
By Al Gunnarson, VP of Sales and Marketing Warren Controls, Inc.
Maintaining complex systems in the OEM industry can often times be a challenge, particularly when something goes wrong that causes automatic systems to leak. This not only creates burdensome operational downtime, it drains economic resources -- lost time means lost money. Historically OEMs have relied on control valves that are pneumatically actuated. But these systems have their drawbacks even when they do not require costly maintenance, with lags in fluctuation response time and hazards that are built into the pneumatic technology itself.
A standard pneumatic actuator modulating valve control will generally only spend 20 percent of the time actually moving and modulating-- sitting idle 80 percent of the time. In many application contexts, such as large corporate campuses, universities, and military bases, that require high temperature hot water systems a higher amount of energy expenditure is required to prevent overheated water. The implication here is that pneumatic systems require greater operational oversight to mitigate these risks manually. Greater oversight means both greater costs and a greater amount of labor time that could deviate from other urgent tasks.
Moreover, pneumatic actuators are highly sensitive to environmental factors including shock forces that many plant operators may be unaware of. For example, pneumatic actuators are vulnerable to shock forces that can occur from water hammer and piping systems, even steam piping systems. The velocity of steam can move at 70 miles an hour down a pipe and can slam right into a valve: if that valve is controlled with a plastic spindle, the pressure can cause an unintended break and likely leak into the system. When this happens, the maintenance costs rack up very quickly.
Electric Actuation: New Advances, New Solutions
For end users, these perils and costs associated with traditional actuators have always been a necessary compromise that comes with the technology itself. But the industry is starting to take notice of new solutions, particularly with respect to electric actuation. One problem, however, that has stalled this emerging market has been to develop electric solutions that retain some of the full advantages of pneumatic or hydraulic actuation -- namely, operational speed and consistency. Early electric solutions lacked the precision and responsiveness of pneumatic or hydraulic systems in controlling and regulating the force and speed. Moreover, while pneumatic systems carry a significantly higher operational cost than electric, the component costs for pneumatic systems have been lower. Traditional electric actuators carry risks of their own, as well, from overheating to moisture sensitivity.
To solve common challenges, the industry standard is rapidly moving towards electrically actuated, modulating globe control valves. The mission is to provide an instrument suited for challenging, modulating, industrial processes that require electric actuation with the actuation speed and solid reliability of pneumatics. Advances in the industry have allowed for the development of new technology has allowed us to move beyond these traditional limitations of electric actuation while retaining its significant cost-effective advantages.
Warren Controls, a leading manufacturer of control valves and specialty fluid handling products, has taken a noteworthy step forward in the market for novel actuation solutions with their ARIA Series of electrically actuated, modulating, globe control valves. Warren Controls entered into a research and development initiative spanning several years, specifically to resolve issues faced by the steam fired instantaneous water heater markets.
The valves are ideally suited for challenging, modulating, industrial processes that require electric actuation with the actuation speed and reliability of pneumatics. The new ARIA series is an upgraded version of Warren Controls’ AmurAct. The newly improved actuator is designed for 1.5 million cycles and can withstand ambient temperatures up to 150 degrees Fahrenheit, with travel speeds at 12 seconds per inch (nine seconds for ¾-inch stroke valves). ARIA is equipped with an electric spring fail safe (when opened or closed), robust enclosures with IP67 / NEMA 4X enclosure and water tight ½” NPT fittings, and has split range input capability for 1/3-2/3 high/low applications.
Engineering Integrity for the End User
The development of the new ARIA series provided a unique opportunity to stretch the imaginations of the Warren Controls engineering team, tasked with leveraging the power of electricity to improve, if not perfect, actuation speed and the reliability of pneumatics. By conducting exhaustive field trials, company engineers released a new series of electrically actuated, modulating, globe control valves with even greater performance and higher reliability with more features. The result is the worthy and improved successor to AmurAct. The ARIA series takes over and offers many features, including galvanically isolated control and feedback; the critical ability to split-range for Hi/Lo applications; and push button manual commissioning.
This solves a number of problems for users, and Warren Controls created the ARIA Series with customers in mind. It’s designed for 1.5 million cycles, and of course includes all common control and feedback systems. Four valve series are available with the ARIA actuator for customized use: the ARA is a three-way cast flanged steel valve for 1/2” – 2”; the ARB is a two-way or three-way threaded bronze or stainless steel valve for 1/2” - 2”; The ARC is a two-way or three-way flanged cast iron valve for 2-1/2” - 6”; and the ARD is a two-way flanged steel cage valve for 1/2” – 2.” The ARIA electric actuator has a NEMA 4x rating with a capability of withstanding ambient temperatures up to 150°F. This means ARIA could survive a really hot control room, and it also has very good resolution. It has an internal feedback mechanism for the linear stroke of 12 bits or 4000 parts of resolution. The advanced features like galvanic isolation between the inputs and the outputs means user systems don't end up with ground-loop problems when contecting to PLCs (programmable logic controllers) and other central control systems.
Customers in the district/campus energy sector, or those working source-side HVAC systems, where high temperature, hot water applications are in use (like a colleges/universities or military bases), will benefit from the ARA or ARD. The ARB and ARC are ideal for those in the food and beverage industry to control steam and water applications. Going with a high-resolution electric actuator means the controlled flow is adjusted very tightly to the flow requirement, unlike an HVAC actuator. HVAC actuators might only have 100 parts of resolution for full valve stroke, so it moves in 1 percent increments whereas high-resolution electric actuators move in a tenth of a percent increments.
The Warren Controls family of products bridges the gap between industrial, HVAC and district/ campus energy. Its “Product Builder” philosophy allows unique and specific engineered configurations to be created quickly, with timely checks and no delays. This translates into much shorter lead times than industry standards for similar products.
About the author:
Albert H. Gunnarson is the Vice President of Sales, Marketing & Product Development at Warren Controls, where he leads, trains and develops the essential materials and new projects needed in the Warren Controls product line. Albert has a BSEET from DeVry Institute of Technology and an MBA from The Lake Forest Graduate School of Management. He has been designing, specifying, applying and marketing control systems and control valves for more than 35 years. In his passion for educating customers in control valve design and proper valve selection, he co-created Warren Controls’ popular Valve Sizing & Selection program, ValveWorks®.
Expanite provides sustainable alternative to Teflon® & Co.
Expanite – The technology of the Danish pioneer for surface hardening of stainless steel and titanium is used more and more frequently when it comes to alternatives to classic fluoroplastic coatings such as Teflon®, Halar® or Xylan®. In addition to technical and commercial advantages, the environmental compatibility and sustainability of the Expanite process are playing an increasingly important role for customers.
After the discovery of PTFE (polytetrafluoroethylene) - also known as Teflon® - in 1938, some time passed before technically usable applications for the highly inert material paved their way. Today, coatings based on per- and polyfluoroalkyl substances (PFASs), known by their trade names such as Teflon®, Halar® or Xylan® or more generally referred to by the abbreviations ECTFE, PFA, FEP, ETFE, PVDF etc., are applied in many areas to optimize the sliding and non-stick properties as well as wear and corrosion resistance of components.
In addition to the well-known disadvantages of coatings, i.e. inhomogeneous layer thicknesses, layer detachment and increased corrosion attack if the coating is damaged, PFAS-based products have another substantial deficit: the highly stable and therefore not completely degradable carbon-fluorine compounds are harmful not only for humans but also to the environment and can cause cancer, among other things.
Accordingly, there has been a trend towards avoiding the use of these materials since the early 2000s, and especially when it comes to improving wear and corrosion resistance, Expanite surface hardening offers a cost-effective and sustainable alternative.
The Expanite technology is based on a gas process in which carbon and nitrogen are diffused in the component surface. The otherwise comparable soft and wear-prone stainless steel material hardens by a factor of up to 10 and while classic diffusion processes impacting corrosion resistance of the material, the Expanite processes generally improve the corrosion properties of the component.
Sustainable against wear and galling
Besides the elimination of carcinogenic substances, Expanite's gas-based diffusion process is significantly more energy-efficient and environmentally friendly than comparable wear protection processes, and thanks to the treatment in a vacuum, no time-consuming cleaning of the parts, e.g., with aggressive chemicals, is necessary after hardening.
"The different cases in which Expanite is used as an alternative to such plastic coatings are widely spread and can be found, for example, in the areas of pumps and valves, food & beverage or general industrial applications," explains Dr. Holger Selg, application expert and Expanite Sales Director DACH, and continues: "First and foremost, we increase the wear and galling resistance of stainless steel components. By hardening the surface, the sliding properties are improved at the same time and, depending on the application, offer an adequate replacement for fluoroplastic coatings.”
The Expanite technology, specially developed for corrosion-resistant materials, offers a solution for austenitic, martensitic, ferritic, and duplex stainless steels as well as for expensive nickel-based alloys such as Inconel and Hastelloy. Moreover, ExpaniteHard-Ti, which the Expanite team of experts has developed to market maturity in recent years, is used for titanium grades.
About Expanite:
Expanite was founded in 2010 by leading experts in material and surface hardening whose research dates back to 2000. The company is headquartered in Hillerød near Copenhagen and has treatment centers in the USA, Germany, Korea and China. Expanite's solutions are flexible and can be tailored to the customer's own product line within the framework of a license agreement.
EGAT deploys Siemens’ software solutions for the world's largest Hydro-Floating Solar Hybrid Project
The Electricity Generating Authority of Thailand (EGAT) has moved forward with its policy of using clean energy and reducing carbon dioxide emissions with smart technology by deploying Siemens' SICAM Microgrid Control and Photovoltaic Plant Control to balance the energy mix generated by the world's largest Hydro-Floating Solar Hybrid Project at Sirindhorn Dam, Ubon Ratchathani Province. The project with a solar power generation capacity of 45 megawatts and a hydroelectric capacity of 36 megawatts, capable of generating electricity from renewable sources day and night, recently began commercial operation, acclaimed as the first of its kind in Thailand.
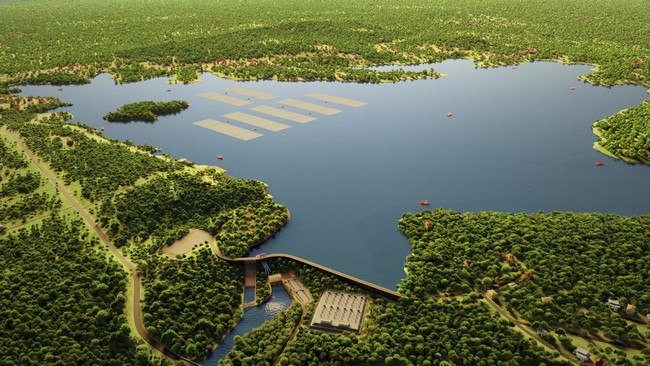
www.siemens.com/smartinfrastructure
In fiscal 2021, which ended on September 30, 2021, the Siemens Group generated revenue of €62.3 billion and net income of €6.7 billion. As of September 30, 2021, the company had around 303,000 employees worldwide. Further information is available on the Internet at www.siemens.com.
Bearings can help the environment
~ How chrome steel can fight the beast of climate change ~
Reducing your carbon footprint is like a marathon: dedication and discipline will only get you so far. To get first place, you will need to be efficient in every step you take. Similarly, businesses must strive to be efficient to meet tighter goals to reduce CO2 emissions. Here, Chris Johnson, managing director of SMB Bearings, explains how industry can use advanced chrome bearings to go green and, at the same time, reduce electricity consumption.
According to the International Energy Agency (IEA), around 30 per cent of global electricity is consumed by electric motors in industry. Furthermore, motors are the asset that consume the most electricity in manufacturing, accounting for 70 per cent of global electricity in the industry. From this, we can calculate that a 0.1 per cent reduction in industry consumption could save enough electricity to sustain the UK for almost a month.
ABB Group has found, using IEA data, that 51 per cent of all motor failures are related to their bearings. The common causes for these failures include exceeding recommended load ratings, vibrations and overheating. Choosing the right bearing for a motor can not only reduce the chance of failures; it can also bring down a business’s emissions and maintenance costs.
No universal fit
There is no one-size-fits-all for bearings. AISI-440 grade stainless steel small motor bearings can sustain temperatures of up to 300 degrees Celsius, which makes them ideal for machinery that operates under high heat. However, the same process that allows the stainless steel to obtain these properties will also soften the metal. This makes the internal components more susceptible to physical damage.
Chrome steel small motor bearings are not only less expensive, but are also better suited for most applications. They have low-noise and low-vibration properties that make them less wasteful in applications below 150 degrees Celsius. While some situations may require the superior anti-corrosion properties of stainless steel, most industries will benefit from the more efficient chrome steel alternative.
Vibration and noise can also be caused by exceeding the recommended payloads of a motor. Fortunately, chrome steel has 20 per cent higher load rating than 440C grade stainless steels so these symptoms of failure are less likely to occur. Higher load ratings are also associated with longer life cycles, and therefore lower maintenance costs.
Win-win scenario
Choosing chrome steel bearings is not only likely to be more effective than 440C stainless steels, but also less expensive in the short and long term. The energy converted in noise and vibration is lost, resulting in further wasted time and energy for downtime and motor repairs.
Electricity wasted on poorly-matched motors and bearings can prevent your company from being as environmentally-friendly as it could be. That’s why selecting a bearing that can sustain the loads it is subjected to, can drastically increase the product’s lifetime while reducing the energy that is thrown away. In the long run, we will need to be as efficient as possible about energy consumption.
Just like in marathons, dedication and effort alone will not get you the best time. Efficiency is key, which also applies if businesses are to help save the climate and also reduce costs. If you’d like to be a leader in industry by reducing your carbon footprint, while making the best of your machinery, then get in touch with SMB Bearings at https://www.smbbearings.com.
About SMB Bearings: SMB Bearings originally specialised in miniature bearings, thin-section bearings and stainless steel bearings. By natural progression, the company expanded the range to include other corrosion resistant bearings such as plastic bearings, 316 stainless bearings and ceramic bearings.
Remaining a specialist business, SMB Bearings provide a high level of product knowledge, providing bearing and lubrication solutions to existing or potential customers, whether individuals or large corporations. SMB Bearings does not just sell bearings, but helps to solve your problems.
For further information please visit http://www.smbbearings.com
Metso Outotec to start next phase in development of its Metals business
Metso Outotec will take the next structural development steps in its business portfolio, following the completed integration of its Minerals business and the successful turnaround of its Metals business. The company plans to change its business area structure and related reporting segments by transferring the Hydrometallurgy business from Metals to Minerals. The objective of the change is to accelerate Metso Outotec’s profitable growth in the minerals processing industry by more efficiently leveraging the opportunities and synergies in the minerals and hydrometallurgical processes.
Having Hydrometallurgy as part of the Minerals business will enable enhanced customer service with a competitive and fully integrated Planet Positive product offering, as well as closer integration with the customers’ processes through digitalization. Going forward, gold and battery chemicals businesses are among the interesting new synergistic growth areas.
A strategic review will be conducted in the remaining Metals business area, consisting of the Smelting, Metals & Chemical Processing and the Ferrous & Heat Transfer business lines, as well as related aftermarket services. The review will focus on evaluating the best environment for developing the Metals business and its strategic fit in Metso Outotec’s business portfolio. All potential options will be considered, including development by Metso Outotec, co-development with a partner, or divestment. The review has no impact on Metals’ daily business conduct, sales, or project execution, which will continue with full commitment.
Metso Outotec’s financial reporting will be adjusted to reflect the new segment structure as of January 1, 2022. The financial year 2021 will be reported in line with the segment structure used during 2021. The restated segment financials will be provided prior to the Q1/2022 reporting.
Metso Outotec is a frontrunner in sustainable technologies, end-to-end solutions and services for the aggregates, minerals processing and metals refining industries globally. By improving our customers’ energy and water efficiency, increasing their productivity, and reducing environmental risks with our product and process expertise, we are the partner for positive change. Metso Outotec is committed to limiting global warming to 1.5°C with Science Based Targets.
Headquartered in Helsinki, Finland, Metso Outotec employs over 15,000 people in more than 50 countries and its sales for 2020 were about EUR 3.9 billion. The company is listed on the Nasdaq Helsinki. mogroup.com
Mammoet starts investigation of patent infringement by Huisman and BMS
Mammoet is investigating the possible violation of its intellectual property rights by Huisman and BMS.
The investigation concerns the recently announced series of land cranes, including a 3000-ton ring crane, by Huisman and BMS.
If any violations are apparent, Mammoet will take steps to actively enforce its legal rights in any and all applicable jurisdictions.
Huisman and BMS crane (left), Mammoet SK350 crane (right).
As the global leader in heavy lifting and transport, Mammoet drives innovation in the industry. This includes major developments such as SPMT trailers, hydraulic skid systems, Mega Jack series and containerized (ring) cranes.
This innovation is one of the foundations of Mammoet’s business and therefore any violation of its rights, including its intellectual property, will be pursued via legal enforcement.
Mammoet
Mammoet helps clients with Smarter, Safer and Stronger solutions to any heavy lifting or transport challenge. We aim to develop long term relationships in order to understand their businesses and challenges best, so we can realize the most efficient and cost-effective approaches. We have a unique global network and an unparalleled fleet of equipment. Through deep and longstanding engineering expertise and the highest quality and safety standards in execution we bring an intelligent and flexible approach to projects across a wide breadth of industry sectors. Clients trust us to help them achieve feats that were once considered impossible, and we have often broken records in doing so.
For more information, visit www.mammoet.com
AFRY main engineering partner for Boliden in zinc production expansion in Norway
Boliden has awarded AFRY engineering and site services assignment for the Odda zinc smelter expansion project. The expansion enables Boliden Odda to almost double zinc production and, at the same time, reduce already world-class low carbon dioxide intensity by 15 percent.
Boliden has decided to expand the zinc smelter in Odda, southern Norway. The project named Green Zinc Odda will increase the annual production capacity for zinc products to 350,000 tonnes. In addition to zinc products, it will also enable extract of the bi-metals lead, gold, and silver. Boliden’s total investment value is EUR 700 million, and the project will be completed at the end of 2024.
AFRY’s extensive assignment includes detail engineering, site services and project procurement support. The services will be delivered 2022 - 2024. The value of AFRY’s assignment is not disclosed. The expansion project will improve energy efficiency, use only fossil-free electricity, and use sustainable technologies in all production phases. Most of the production facilities will be expanded, and production processes will be modernized by increasing digitalisation and automation. Also, Boliden’s solution for waste handling will be expanded.
“We are extremely proud to be Boliden’s trusted partner in this strategic project. AFRY’s mission is to support transition towards more sustainable societies and this project is perfectly aligned with that target. Our operating model where local presence and knowhow is supported by global competencies enables us to deliver world-class solutions to Boliden”, says Janne Tikka, Head of Mining & Metals, Process Industries Division, AFRY.
Boliden is a Swedish mining and metals company with a focus on sustainable development. The company’s core competence lies within the fields of exploration, mining, smelting and metal recycling and it operates in Sweden, Norway, Finland and Ireland.
“AFRYs deep and long relationship with Boliden covers their operations in all mines and smelters. Our expertise within sustainability and mining & metals enables us to support and create additional value for Boliden also with this project”, says Andreas Johansson, Global Key Account Manager Boliden at AFRY.
For further reading: Zinc is one of the most widely consumed metals in the world. Zinc is an incredibly important metal for the development of a sustainable society, and it is used in e.g. in automotive, buildings and infrastructure. Read more about AFRY’s offering within mining & metals, afry.com/en/area/mining-metals
AFRY is a European leader in engineering, design, and advisory services, with a global reach. We accelerate the transition towards a sustainable society.
We are 16,000 devoted experts in infrastructure, industry, energy and digitalisation, creating sustainable solutions for generations to come.
Making Future
Protolabs joins elite group of suppliers with JOSCAR recognition
The world’s leading digital manufacturer is setting its sights on a £multi-million opportunity after it secured a prestigious supplier accreditation for the aerospace, security, space and defence industries.
Having supported the sector for several years, Protolabs is now officially recognised as a fully compliant and credible supplier to major businesses within the associated industries.
JOSCAR (Joint Supply Chain Accreditation Register) is valued by many of the largest purchasers in the stated industries, such as BAE Systems, NATS, Rolls Royce, Airbus and the MOD.
The global accreditation indicates that organisations have successfully gone through an invite only process that demonstrates commitment, reliability, technical ability and capacity, as well as helping purchasers meet the growing and diverse nature of regulatory requirements when it comes to managing third party risk in the supply chain.
Bjoern Klaas, Vice President and Managing Director of Protolabs Europe, commented: “We are delighted to have achieved JOSCAR accreditation, joining an elite group of global suppliers in the process.
“It is testament to the quality and reliability of our output and our capacity to deliver prototypes and production parts in such a way that is valued by our customers in aerospace, security, space and defence industries.”
He continued: “We take great pride in achieving excellence in this way, whether being at the forefront of innovation or providing a trusted digital manufacturing service to the industrial supply chain.”
Protolabs, which was founded in 1999 and has been established in Europe since 2005, offers world-leading 3D printing, CNC machining and injection moulding services to design engineers.
Klaas went on to add: “We are already a well-established service provider to the aerospace supply chain, but this accreditation, alongside our ISO 9001 quality award, will further cement our reputation in the wider security and defence industries.
“In addition, we recently became one of the first manufacturers in the EMEA region to achieve DNV certification, bringing new levels of assurance relevant to maritime and offshore industries, as well as the broader defence sector and JOSCAR-associated industries.”
Inconel 718, the DNV-certified 3D printed metal, is a high-strength, corrosion-resistant nickel chromium that hardens with age, making it the ideal choice for fabricating complex parts.
It can be used within extreme hot and cold temperature limits and is founded in numerous components in the aerospace, maritime and defence space.
For further information, please visit www.protolabs.co.uk
ABOUT PROTOLABS
Protolabs is the world-leading digital manufacturing source for custom prototypes and low-volume production parts. The technology-enabled company uses advanced 3D printing, CNC machining and injection moulding technologies to produce parts within days. The result is an unprecedented speed-to-market value for product designers and engineers worldwide.
Aspects:
- An automated quoting system and proprietary software translate digital 3D CAD models into instructions for high-speed manufacturing equipment by creating a digital twin of the desired part. The result is parts that are produced in a fully digitalized fashion and shipped in 1 to 15 days.
- The company is anchored by three flagship services: injection moulding, CNC machining and 3D printing (additive manufacturing).
- Injection moulding is used for quick-turn prototyping, bridge tooling and low-volume production of up to 10,000+ parts as well as for end of life parts at lower volume. More than 100 thermoplastics resins, metal and liquid silicone rubber are offered.
- Protolabs uses three and five-axis indexed milling and turning to machine engineering-grade plastic and metal prototypes and functional end-use parts in quantities of less than 200.
- Additive manufacturing employs advanced 3D printing technologies that can create extremely accurate prototypes with complex geometries. Additive parts are built by stereolithography, selective laser sintering, Multi Jet Fusion, PolyJet and direct metal laser sintering processes, and in a range a plastics and metals.
Microban® International teams up with Rifra masterbatches
Microban International, a pioneer in the development of antimicrobial product protection technologies, is proud to announce a new distributor agreement with Rifra Masterbatches, a global player in the production of tailor-made additives – such as colour or various complexes – used to process plastic products. The two companies share a goal of providing novel masterbatches with antimicrobial properties, to be able to offer their injection, blow moulding, extrusion and compounding customers more choice in solutions.
Rifra Masterbatches has provided various additives to the packaging, building, medical device, E&E, and toy industries for over 40 years and, from its very earliest origins, has thrived on the philosophy of addressing the needs of its customers. The company has recognised an increasing interest in including antimicrobial technologies into plastics – especially in the heightened awareness of the current COVID-19 pandemic – and welcomes the opportunity to work with Microban, a leading expert in the field, to address this unmet need.
Antimicrobials have always been of interest for manufacturing companies, but adding them into products can be challenging and is fraught with regulatory loopholes. Microban has a wealth of expertise in incorporating built-in antimicrobial protection into a vast array of products, and has a similar customer-focused approach to Rifra. The partnership will begin as a distributor agreement, but both parties look forward to exploring further opportunities for the co-development of unique additive products which will combine features and simplify formulations.
Giorgio Rimini, Director of Business Development for Europe at Microban, said: “We are particularly excited about partnering with Rifra Masterbatches. It is a global player in the plastic additives field with an extremely bright future, and we look forward to discovering some really exciting prospects on the horizon together.”
Elisabetta Rampa, General Manager at Rifra Masterbatches, added: “Most masterbatch producers have decided to avoid an antimicrobial product portfolio because of the challenges associated with formulation and regulatory requirements. However, we wanted to address the needs of our customers, and have chosen to work with Microban, the global leader in the field, to achieve this goal.”
About Microban International
Part of Barr Brands International (BBI), Microban International is a global specialist in antimicrobial, odour control, smart surface and disinfection technologies. Our proactive systems keep products cleaner, and control odours better by preventing problems before they start. Microban drives innovation by combining science and creative solutions that enhance high-quality consumer, textile, industrial and medical products around the world. Today the Microban brand and technologies are featured on thousands of products worldwide. The company is headquartered in North Carolina with operations in North America, Europe and Asia Pacific. For more information, please visit www.microban.com.
About Rifra Masterbatches
Rifra Masterbatches SpA was born more than 40 years ago in Italy, and is one of the global players in the masterbatches field. With its mantra of “We complete your process”, the company strives to address, facilitate and solve problems related to the production process of its customers in various applications. At the base of the company’s Corporate Governance choices lies the value of fairness as an inspiring principle. One of the main values of Rifra is the person, therefore, the company has established a long collaboration with all of its stakeholders. Rifra guarantees the lowest possible impact on the environment and plays a large role in safeguarding social and environment sustainability. For more information, please visit https://www.rifra.it/en/.