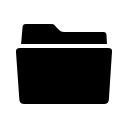
Uncategorised (4996)
Stewardship of the UK's energy market seems to be a more important role than ensuring health and safety throughout industry - judging, at least, by the salaries recently on offer for the top jobs at Ofgem and the Health & Safety Executive (HSE).
Energy market regulator Ofgem offered a salary of £190,000 plus an annual bonus of up to £15,000 to attract a new chief executive. The position is currently being filled on an interim basis by Andrew Wright, head of Ofgem's markets division.
Wright took on the role in June from Alistair Buchanan, who stepped down after 10 years in charge of the organisation, headquartered in Millbank, London.
With a requirement to provide strong and dynamic leadership, Ofgem said its next chief will need a strong track record of working in a senior leadership role in a complex organisation. Other requirements include strong management and leadership experience, ideally in competition and regulation or a regulated sector.
The HSE was looking for a chief executive, after Geoffrey Podger recently quit the role to lead a new workplace safety regulatory body in New Zealand. The UK executive put up a salary of £140,000 -£160,000 for the top role, which is based in Bootle Merseyside.
The HSE said its new boss must have a track record of leadership and strategic delivery in an organisation of comparable size. He or she must also have an full understanding of the regulatory sector, the workings of government, business, employers’ organisations and trade unions.
See Process Industry Jobs for the latest top vacancies in the sector.
ExxonMobil, Rosneft select contractors for Russia LNG project
AdministratorRosneft and ExxonMobil have selected CB&I UK and Foster Wheeler Energy as contractors for initial phase front end engineering and design (FEED) for a proposed Russian Far East LNG project.
A final project design is expected by the end of 2014, including front-end engineering and design documentation for the LNG plant, associated facilities and gas pipeline, as well as engineering studies and environmental impact assessment.
CB&I UK and Foster Wheeler Energy will be awarded separate contracts for the initial phase front end engineering and design. The scope of work covers a conceptual project including finalizing details for an LNG plant site, gas liquefaction technology and construction method.
Following submission by the companies of their respective concepts and design, Rosneft and ExxonMobil will evaluate the companies' work product prior to awarding a contract for the second phase of FEED.
The plant design capacity of the project is expected to be five million tons per year and may be expanded in the future. The liquefaction plant will receive natural gas feedstock from Rosneft’s reserves in the Far East and Sakhalin gas reserves.
“We are pleased with the technical progress of our joint team of experts from Rosneft and ExxonMobil,” said Rosneft president Igor Sechin. “With our initial FEED contractors on board now we will see the project begin to take shape in a matter of months. We are taking a determined approach with this project to help monetise the gas resources of Russia.”
“We look forward to working with Rosneft and our initial FEED contractors on further evaluation of specific technical and commercial aspects of a potential LNG project,” said Glenn Waller, president of ExxonMobil Russia.
Special attention will be given during the design phase to reduce the environmental impact on the unique ecosystem of the area and to developing local infrastructure, Waller added.
Mining and natural resource group Anglo American has signed up Weir Group to improve energy consumption and lower maintenance requirements across Anglo American’s operations in South Africa, South America, North America and Australia.
Under a global framework agreement (GFA) Weir is to help optimise total cost of ownership, guarantee security of supply, promote safety and improve reliability in ways that will be beneficial to both parties.
The GFA consolidates supply chain arrangements between the organisations at a global, national and regional level, and establishes standardised administrative arrangements to procure pumps and associated slurry handling equipment.
Under the GFA, Weir, as Anglo American’s predominant supplier of mill circuit pumps will accelerate the roll out of Wear Reduction Technology across Anglo American’s installed Warman pumps. Future considerations will include piloting Weir Mill Circuit Technology, promotion of the WBH range of slurry pumps in projects and wider use of Cavex hydrocyclones in dewatering applications.
In advance of today’s signing of the GFA, Anglo American conducted total cost of ownership benchmarking of slurry pumping, with Weir solutions providing significant productivity advantages and energy consumption improvements.
“This agreement strengthens our relationship with Weir and confirms our commitment to work collaboratively with our strategic partners to deliver sustainable value to our operations,” said Bruce Crane, group head of supply chain for Anglo American.
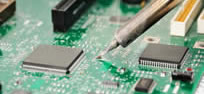
Despite a fall-off in its overall economic growth, China still offers huge opportunities for automation product suppliers – especially those that most understand how to do business in this very fast-changing market.
This was the message from speakers at the CC-Link Partner Association's ‘Gateway to China’ conference, which explored the opportunities and pitfalls for UK companies seeking automation business opportunities in the country.
During the event, staged 24 Sept at Mitsubishi Electric's Hatfield, UK base, Gambica's industrial automation sector head Steve Brambley highlighted current trends in China, which represents 43% of the £50-billion market for all types of automation products in the Asia/ASEAN region.
Citing a batch of recent market reports – from ARC, IMS and Global Automation Research – Brambley said that "while China’s industrial growth is predicted to continue slowing, there is what seems to be an inexorable increase in the growth of all types of automation."
Looking at the process sector specifically, Brambley cited figures showing how China's market for process instrumentation and automation products was set to reach $6.4 billion by the end of this year – representing a compound annual growth rate of 9% over the last 10 years.
On the other hand, while the long-term indicators for sales in the Asia-Pacific region all point upwards, industry should not expect to see a return to prolonged double-digit growth.
As the Gambica expert also concluded: "There is still time to build a market position [in China] from the UK, but you need to be quick."
Since a slowdown in the first half of 2012 – with only 3.7% growth in overall revenue from industrial automation equipment – the market has been in pick-up mode, reported John Browett, general manager of the CC-Link Partner Association Europe. The industrial automation sector set to grow by 6.2% in 2013.
In China the per capita energy use is still a long way behind most of Western Europe, meaning the potential for growth is still huge – meaning huge opportunities for European
But, said Browett, given "the sensitive current economic climate, many Asian companies are taking a more careful approach to investment; they are becoming more demanding towards their suppliers and making more enquiries before purchasing."
Meanwhile, according to IHS, several Chinese manufacturers are currently developing products which are in direct competition with the ones provided by Western suppliers of industrial automation.
These are only a few of the obstacles facing European vendors who want to penetrate the Asian market to change the way they do business, said Browett.
"Flexibility and the ability to respond to very specific demands are becoming essential factors when dealing with the Asian market," he concluded. "Being able to offer technologies and products which are compatible with the needs of Asian clients is [also] a must."
New entrants will also need to understand business relationships and how decisions are made within Chinese companies, said Lutz Berners, president of Stuttgart, Germany-based Berners Consulting, which helps Western companies enter the market.'Companies that do best in China are those that manage to stick to their core competences, while also paying attention to the nitty gritty of business frelationships there,' he advised.
For example, Berners said the emphasis in China is on in-group loyalty and forming relationships before the legal, technical or business case for a contract or project is hammered out. This he noted, was the complete opposite of what companies are used to in Europe.
"For Western companies, therefore, it is very important to have someone, for example, a trade association or other industry support body to bring them into the relationship," said Berners.
When it comes to actually buying equipment, the fast-changing nature of markets in China today mean there is less emphasis on long-term planning.
"People have a two-to-three year horizon [when buying} machines," said Berners, noting that this can pose a challenge for companies competing against suppliers of cheaper or lower-specification products.
Yokogawa Electric Corp. is releasing a new version of the ProSafe-RS safety instrumented system and has enhanced the DPharp EJX multivariable transmitter.
Target markets and applications include emergency shutdown and fire prevention/suppression, production, and other applications in process industries such as oil, natural gas, and petrochemicals.
The new Version R3.02.10 is said to offer improved functions for upstream oil and gas,, while the DPharp EJX multivariable transmitter has been enhanced to improve connectivity with ProSafe-RS.
In upstream oil and gas processes, wells and pipelines are typically distributed over a wide area and often have limited space for the installation of equipment. To improve operational efficiency and reduce hardware costs, there is a need to consolidate the functions performed by control and safety instrumented systems.
In response to these needs, the enhances system provides AGA (American Gas Association) gas flow rate calculation, Modbus communications between DPharp EJX and ProSafe-RS for gas flow rate calculation, and support for many networks used in oil and gas upstream applications.
To monitor and control gas wells and pipelines, gas flow rate compensation is required. The in-situ gas volume needs to be compensated to a standard volume because the gas volume rises or falls significantly depending on the process temperature and pressure.
This compensation is usually carried out by a control device or dedicated flow computer. For customers in regions such as the Americas and the Middle East who wish to eliminate the need for such dedicated devices, Yokogawa has incorporated a gas flow rate calculation function in ProSafe-RS R3.02.10.
ProSafe-RS, which is certified for use in SIL3 applications, is therefore now suitable for use both in safety instrumentation and monitoring & control. SIL is a standard relating to the functional safety of electrical and electronic equipment that was established by the IEC.
Safety integrity levels (SIL) are defined by the IEC61508. At SIL3, the risk factor for a plant where safety measures are not in place has been reduced to a range from 1/1000 to 1/10000.
To compensate the gas flow rate, differential pressure, static pressure, and temperature must be measured. The DPharp EJX multivariable transmitter is a sensor that can measure all three of these variables.
Yokogawa has added Modbus protocol support to the DPharp EJX multivariable transmitter. This sensor can thus be used together with ProSafe-RS to perform highly reliable and accurate gas flow rate calculations.
The Modbus protocol - an industrial communications protocol developed by the US company Modicon – now owned by Schneider Electric – is widely used in upstream oil and gas processes for communications between sensors and gas flow rate compensation devices,
A variety of networks are used to link ProSafe-RS at the site to the Yokogawa FAST/TOOLS SCADA system. Some networks use high-bandwidth optical fibre, while others rely on low-bandwidth wireless links.
By optimising the frequency of data collection and the volume of transmitted data, ProSafe-RS R3.02.10 can now link up with other systems using low-bandwidth media. This improves maintenance efficiency by enabling remote engineering. Essential data is stored on the ProSafe-RS controller, ensuring continuity in the event of a network failure.
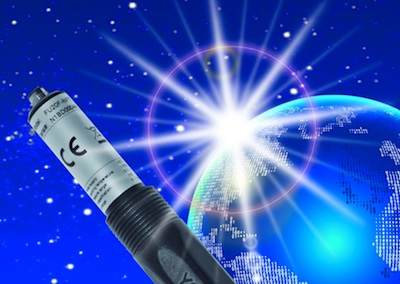
Yokogawa has combined its pH and ORP sensor technology with integrated digital communications and signal-processing circuitry to produce a range of self-contained smart sensing solutions.
The SENCOM smart sensor is designed to enable improved maintenance management and diagnostics. The unit has its own permanent calibration memory, allowing it to be calibrated in the lab before returning it to the field.
The sensors are said to maintain specific measurement and calibration data and this information can be exchanged between the sensor and a transmitter such as Yokogawa’s FLEXA family. Dedicated SENCOM SPS24 management software is also available for use with a Windows PC.
Utilising historical measurement, calibration and diagnostic data from the sensor, the SPS24 data management system provides users with the tools necessary to predict maintenance and calibration frequency and estimate sensor life. The calibration information can be managed, analysed and conveniently documented by the SENCOM SPS24 software.
Another benefit, says Yokogawa, is that the unit makes it possible to monitor sensor aging in real time using a sensor “wellness” feature. Users can also carry out reference impedance measurements for the early detection of diaphragm clogging.
Yokogawa adds that the new SPS24 SENCOM PC software makes it possible to optimise the performance of pH/ORP sensors for enhanced reliability and process safety.
The software, it explains, allows the operator to continuously monitor pH/ORP sensor measurements, perform calibrations and configure the various parameters, keeping track of up to 100 different SENCOM sensors.
The first SENCOM sensor to be introduced in Yokogawa’s new family is a pH/ORP sensor, targeting applications requiring easy, accurate and reliable measurements.
Future sensors will target the full spectrum of pH and ORP applications in the power, utilities, petro-chemical, chemical and pulp & paper industries.
Andy Burns, technical business manager at Global Heat Transfer explains what you need to know when it comes to testing thermal fluid for compliance under the Dangerous Substances and Explosive Atmospheres Regulations 2002 (DSEAR):
The key information required from test reports is carbon level, which indicates if a thermal fluid is breaking down due to thermal cracking and/or oxidation, total acid number (TAN), which is a measure of acidity, usually due to the oxidation process and flashpoint which indicates how well a system vents-off light fractions which re generated by the thermal cracking process.
Test reports need to be read with respect to carbon level and TAN in terms of longevity of fluid, but also with respect to contamination from particulates, wear particles and water intake in terms of performance.
Speaking to customers in the field about test reports has prompted Global Heat Transfer to use a red-amber-green (RAG) status indicator based on threshold limits being reached.
For example, green would mean no action is needed and amber would mean action should be taken imminently to avoid problems, while red would mean a critical threshold has been reached, needing urgent action.
A level of one percent carbon is critical, as is a TAN level of one percent. We stick to these limits rigorously at GHT in the interest of operational efficiency.
Fluid awareness training examines the consequences of excessive carbon build-up which can cause the system to clog up and fail. Carbon collects inside pipework and heaters and affects thermal efficiency, acting as an insulating layer and causing hot spots in heaters which can melt coils and cause fires. The emphasis is on diagnosis and planned preventative maintenance, potential problems arising from poorly maintained thermal fluids.
In terms of DSEAR training, all thermal fluids break down at some point and the rate of decomposition varies in report to the type of fluid and temperature and fluid durability in direct proportion to the proximity to its maximum recommended bulk operating temperature.
A fluid’s gradual degradation through thermal cracking will lower its flashpoint, fire point and corresponding auto ignition temperature and action is needed when this reaches 115 degrees centigrade (red warning for a mineral fluid) although a cautionary amber alert is triggered once a closed flash point reaches 130 Centigrade. A closed flash point value less than 80 Centigrade can be disastrous as in the event of a loss of containment, ignition is likely without an ignition source.
Understanding a thermal oil’s material safety data sheet (MSDS) is a key training objective because the document outlines all of the fluid’s characteristics, including operation temperature range, fluid density, fluid viscosity, flashpoints, auto-ignition, pour point and boiling point. Not all thermal fluids have a high starting flashpoint, which reiterates the importance of sampling on a scheduled basis, because a synthetic fluid for example will generally have a lower flashpoint than a mineral fluid.
Global Heat Transfer is running on-site or off-site training courses on the Dangerous Substances and Explosive Atmospheres Regulations 2002 (DSEAR), thermal fluid awareness and managing and understanding of oxidation. The courses focus on sampling methods for thermal fluids and on understanding what to look for in test results.
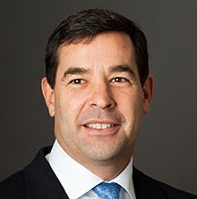
Speech by Bob Fryar, BP executive vice president, safety & operational risk, at this summer's Piper 25 conference Aberdeen, UK. The event marked the 25th anniversary of the Piper Alpha accident:
When the Piper Alpha accident happened, I was still very new to the industry. I had only worked in it for a couple of years. As for most people, the thing that stood out to me with great sadness was the loss of life and the impact that the accident had on so many families and communities.
It also tragically reinforced the fact that we work in a hazardous industry. Our task is to bring energy to people around the world. That task is full of hazards and risks that must be understood and managed at all times.
Since that time I have worked in operations for most of my career, and I have therefore been able to see and be part of the industry’s response to this incident. I have worked in BP’s North America Gas business, the deepwater Gulf of Mexico team, in Trinidad and Tobago, in deepwater Angola. In all of those businesses, I have felt the positive response to Piper Alpha.
This shows up in changes in the way work is controlled, how engineering is used to prevent fires and explosions, and many other areas.
The response from industry and government was very effective. Lord Cullen produced a landmark report and the accident acted as a real catalyst for change.
Despite all of these improvements, the fact is that in general the hazards and risks haven’t changed. They are still there. What changes is the way we relate to those hazards and risks as we learn and improve over time.
And when you look at lost time frequency in the UK offshore over the last 25 years, there has been real improvement.
From looking at the results, three things jump out for me.
First, while I recognise we are only looking at one metric, continuous improvement seems to have occurred over the last 25 years. Rarely do you see a subsequent year frequency exceed the preceding year. This improvement has substantially reduced the number of people being hurt, which is a goal we all share.
The second thing that you can see from the data is that there are some changes in the slope of the line. Where there have been big reductions in the lost time injury frequency, many times this is associated with a particular event.
The Step Change in Safety campaign, for example, was launched in 1997 and was an effort to refocus the industry. They set an ambitious target of a 50% improvement in the safety performance of the industry in the UK over the next 3 years. I believe it made a real difference.
Like the Piper Alpha accident and the Cullen report, Step Change in Safety served as a driver to make real safety improvements in a relatively short period of time. These examples show that industry-wide effort and commitment can take us forward. And the good news is that these improvements have been sustainable.
However, the third thing that you can see from the data is that for the last several years, we are in a flat spot.
As Malcolm has observed, the purpose of the time spent together this week should be to re-energize ourselves and the industry to make a fresh effort to reduce still further the safety and environmental risks associated with the possibility of a major accident in our industry. And the flattening out of the data suggests that this is a good time to be making that renewed commitment.
We all have our own personal reasons for making that commitment afresh. One of mine is that my eldest son will start his first job in this industry in two weeks’ time.
But also, as for others in BP and across the industry, it is the memory of friends and colleagues lost in tragic accidents such as Piper Alpha and Deepwater Horizon. And a determination to do everything in our power to avoid further loss of life and environmental damage.
Today is primarily about remembering Piper Alpha, but, when we review progress since 1988, it is inevitable that people will focus on the accident we and others experienced three years ago, Deepwater Horizon.
So let me briefly look back to 20 April 2010. That was the day when the Deepwater Horizon rig experienced a blowout as its crew was working on the temporary abandonment of the Macondo well. 126 people were on board.
Hydrocarbons escaped from the well resulting in explosions and a fire that burned for two days until the rig sank.
Tragically, 11 men lost their lives and others were injured. Hydrocarbons continued to flow from the well for 87 days.
We deeply regret our role in this accident. Several organizations have conducted investigations and published reports. These include our own BP investigation and the report of the President’s National Commission. All official reports and our own internal investigation concluded that the accident was the result of multiple causes, involving multiple parties.
Several factors stand out in the findings of these reports.
The cement at the bottom of the well did not seal off the hydrocarbons in the formation.
The negative pressure test carried out to check that the well was sealed was misinterpreted.
And the blow-out preventer did not seal the well at the seabed. It is clear that the blind shear rams failed to seal.
Before I look at what we’re doing across the company, let me say a few words about the response to the oil spill itself.
Our intention in the response was to step up and do what was right – going well beyond the statutory legal obligations - so we put a huge amount of resource into it.
It was a complex and massive undertaking. Plugging the leak meant working with robot submarines to apply containment equipment to a high pressure well a mile below the ocean. No one had done that before.
Cleaning up the spill meant a huge effort with thousands of people and vessels as well as airplanes and the largest deployment of boom ever – approximately 13.5 million feet.
At the time, I was running our deepwater business in Angola and I was one of many leaders from around BP who flew to the Gulf. I spent 4 months working on the response, and I will always remember the dedication of the people and the response of the industry and community as well as our own company.
When I arrived, shortly after the accident occurred, my first task was to call other companies to seek their help. I remember making phone calls in the morning, and, by the afternoon, we had experts from Anadarko, Shell, Exxon and others in the office helping us. Additionally, other companies called and asked how they could help. BP deeply appreciates how people offered their assistance, and the difference they made.
And as I mentioned earlier, the experience generated a deep desire across the team to learn from the accident and to seek to prevent the repetition of such a tragedy.
I also want to mention the community’s part in the response. The majority of the people who took part in the response came from the local community. I grew up in Louisiana and have lived on the Gulf Coast for almost 40 years. I am really proud to say that I am from the community that responded in the ways that folks from the Gulf Coast did.
Because of the accident, a number of these folks and businesses were affected. And we have committed to compensate folks who suffered damages resulting from the spill. As well as spending more than $14 billion in operational response and clean-up costs, BP has paid more than $10 billion in claims, settlements and other payments.
I would like to turn now to talk more broadly about the areas that we are focusing on across the company. As I said before, we do not claim to have all the answers, but I hope that some of this may be useful.
First I will talk about our work on deepwater capability in wells, notably on implementing the recommendations from the Bly report.
Then I will go on to talk about what we are doing company-wide, with an emphasis on systematic operating which we believe also benefits our global deepwater operations.
Following the accident, Mark Bly, who was my predecessor as Head of the Safety and Operational Risk function, led the BP internal investigation of the accident, which was conducted by a team including internal and external expertise.
The resulting Bly Report included 26 recommendations addressing important areas of deepwater drilling, including cementing guidelines, equipment certification, assuring the competence of individuals, and testing of blow-out preventers.
The recommendations directly addressed the findings of the investigation. For example, they recommend a review of all cementing contractors and new mandatory practices for cementing.
They recommended revising the relevant BP engineering technical practice to include more details on negative pressure tests, including areas such as success criteria, responsibilities of personnel and configuration of valve positions.
With regard to blow-out preventers, the recommendations contained new provisions on maintenance, testing and design.
The implementation of these recommendations is an ongoing major programme of work within BP. Each recommendation has to be applied across multiple locations – and many require new processes or agreements with contractors.
We have broken down each of the recommendations into defined and measurable deliverable actions. The closure of the recommendations is verified by our Safety and Operational Risk audit team, which worked with the Bly report program team to make sure that the deliverables flowing from the recommendations would be verifiable. Closure is also verified by an independent expert who was appointed by BP’s Board of Directors in June 2012.
Fourteen of the 26 recommendations are now complete.
As well as implementing the recommendations of the report, we have also taken a number of broader measures to further support safety and risk management in our upstream organisation.
One of the first things that we did was to look at the organisation itself. We wanted our upstream organization to be structured in a way that would encourage the building of capability and the consistent application of standards across the world, wherever they apply.
We did this by moving from an asset model to a functional model. What does that mean? It means that, instead of organizing the company in regional teams, we organized our upstream in centralized functions that bring together the people who do the same jobs around the world. All the explorers report to the head of exploration. All the people who build new projects report to the head of the Global Projects Organization. The people involved in drilling, completions and interventions all report to the head of the Global Wells Organization.
A benefit of this is that we can build on our expertise within the teams to deliver excellence in each function and also drive standardization more readily where we wish to do so, with each team using standard procedures. We believe these procedures contribute to consistent implementation and safer execution of work.
We also have looked at capability development within the framework of the new functional organisations. Part of this is about technical specialist capability. In our global wells organisation, we have brought deep expertise in house. We now have 12 cementing specialists in the company, as well as the cementing contractors we work with. We also have a team of 30 dedicated solely to BOP reliability.
But maintaining and enhancing capability is also about training. We have set up the Global Wells Institute, which brings all our Wells training under one roof. The institute emphasises practical, experiential learning and a big part of that learning occurs in the state of the art well simulator area which we have commissioned. The simulators are used by BP personnel as well as by the contractors who actually drill the wells and who ultimately are responsible for well control. I’m told that the room contains the world's largest collection of drilling simulators in one space. The simulators replicate three major operations: the offshore environment, land-based drilling, and workovers. This simulator allows for the observation and assessment of individuals as they manage hypothetical well control incident scenarios.
Of course, plant and equipment is also important. As well as introducing this new kit for training, we have also taken action with regard to the equipment and technology we use in actual deepwater drilling.
We have reviewed our requirements for drilling rigs in service on BP-operated wells. Any proposed departures from those requirements need approval from the appropriate person in our Safety & Operational Risk organisation – what we call S&OR. I’ll be saying a little more about S&OR shortly.
But we are mindful that technology, plant and equipment can serve us in many ways. Strengthening deepwater capability is not all about the kit that actually does the drilling. We have also set out to use technology to enhance our integrated decision-making on drilling and wells.
In Houston we have created a Monitoring Center that enables offshore crews to consult in real time with onshore experts – viewing the same data and linked by video. While the responsibility for well monitoring remains with the rig crew, having a monitoring center means more people can be available as resources in a given circumstance. We believe this can lead to more considered decisions by those who have ultimate accountability. And, of course, I should be clear that accountability for the final decision will always remain with the rig crew – the Monitoring Center is about informed decisions, not collective decisions.
Obviously our top priority is to prevent accidents but part of building deepwater capability is to be prepared for the worst. Since 2010 there has been a strong industry-wide programme of activity in the area of spill response.
At the international level, the Global Industry Response Group was set up and has launched several work-streams. One is looking at data from incidents and communicating good practice, so the entire industry can learn together. Another relates to developing a well capping toolbox. Another is focused on response in general – capturing the lessons we learned in areas such as relief well drilling and crisis management.
BP has built its own capping stack and other containment equipment. It is stored in Houston but can be mobilised worldwide quickly.
Here in Britain, Oil & Gas UK has taken the lead and worked with the Oil Spill Prevention and Response Advisory Group to develop a response toolkit that includes a capping device. So we are seeing a number of these devices positioned around the world.
So hopefully that has given some flavour of how we have responded to the Deepwater Horizon accident across our global wells organisation.
We want to operate systematically everywhere, not just in deepwater, but onshore, downstream and in all parts of our business.
So I would like to share with you briefly how we are systematically approaching safety and operational risk at the company level. I believe these initiatives are making an important contribution to the safety of our deepwater operations.
Following the Deepwater Horizon accident, we established a Safety and Operational Risk organization – “S&OR”. As I mentioned, Mark Bly initially headed the organization and I have recently taken over from Mark.
The S&OR organization helps us provide an expert view of safety and risk that is independent of the business and its line management.
The S&OR team is made up of hundreds of professionals whose focus is on safety and operational risk. Many of these professionals are based around the world alongside our operating businesses. For example, we have an independent S&OR team right here in Aberdeen - not part of our North Sea business, but part of the S&OR organisation that I lead.
I should stress that the existence of S&OR does not absolve the line managers of responsibility for safety and operational risk. Indeed we make it crystal clear that the line is accountable for safety. The people who do the work must shoulder that accountability but we – S&OR – are here to help them manage the risks effectively and to conduct risk-based assurance. Yes, and to challenge them where necessary.
The organization has very clear roles:
setting clear Safety and Operational Risk requirements
maintaining its independent view of risk – in particular by conducting assurance and audits on the work of the line organization
providing deep technical expertise. This includes expertise in engineering, security, safety (both personal safety and process safety), health and the environment; and, if necessary, intervening to cause corrective action based on our independent view.
We believe that systematic operating is the foundation of a safe and strong BP – it drives both efficiency and safety, and therefore long-term value – a safe business is a successful business.
We’ve been taking action to implement three enduring principles which, we believe, together add to a framework for safe, reliable and efficient operations. Under these principles, we are pursuing five specific areas of focus that relate to them and which dictate our programmes of work and activity.
The first is about people – further deepening capabilities and maintaining a strong focus on safety; this very much includes the nature of leadership. So building organisational capability across BP and strengthening leadership and culture are two specific focus areas for us.
The second principle is about the actual system we use to drive systematic operating and to manage safety and operational risk - called our operating management system or OMS. So continuing to embed OMS and to enhance risk management are two further focus areas for us.
The third principle is about what we call assurance – essentially assuring ourselves as to whether capabilities are present and OMS is working to continuously strengthen our operations. This includes collating data (measurement and assessment) – and also inspecting, auditing, and checking. These are layers of assurance or ‘checks and balances’. So this gives us a fifth focus area - strengthening our checks and balances. As you’ll see, our global S&OR organisation has a key role to play in this area,
Let me tell you a little about each of these principles and some of what we’re doing under each of them at the company level.
Our CEO Bob Dudley has been really clear in his expectations of the company with respect to safety – that safety lies at the heart of BP and at the heart of good business. He has also been clear that he expects leaders to spend time in the field and maintain great sensitivity to risk.
In the last three years we have introduced several measures to further support and train our leaders.
I’ll come to training in a moment, but it is also worth mentioning the way we are expecting leaders to spend time in the field and engage with staff on the front line. We are providing them with tools and guidance on how to do that effectively, giving them valuable insights into conformance, barriers and risk management in the operations for which they are responsible.
We have also enriched our leadership team with people who bring experience from other industries with strong records in managing high hazard operations.
We have some former NASA astronauts – including one who worked on the Challenger Space Shuttle response. We have former nuclear industry professionals and military safety experts.
And as a voice of great wisdom on our Board we have Admiral Skip Bowman who is a former leader of the US Nuclear Submarine navy. That fleet has a safety record that is renowned worldwide, and Admiral Bowman brings us decades of experience in maintaining a successful safety culture. He has advised our safety leaders, monitored inspections and personally taught in one of our development programmes.
And performance contracts require every employee to set priorities relating to safety and risk management as well as behaviour that embodies our values of safety, respect, excellence, courage, one team.
Now let me talk about what we are doing in the area of capability. We want our leaders and operators to have the skills they need to do the job and lead systematic operations.
We have enhanced our programs to help equip people with the capabilities they need.
These programs reach from senior operations leaders down to the front line of the operating organization and those that supervise and conduct work. For example, our Operating Essentials program is for front line staff – delivered on site among teams – and more than 6000 folks attended last year. This is helping the front line develop skills in areas like continuous improvement techniques, Control of Work and Hazard Identification.
We’re now just piloting another program called Leading in the Field which is specifically about how leaders engage staff and inspect operations.
So I’ve covered leadership and capability – which relate to our first principle about people and culture.
The second principle is about applying the BP Operating Management System or OMS.
OMS is the foundation of our operations. It is a framework that sets out what has to be done – and also how – and it has an annual cycle designed to drive continuous improvement.
First of all, the ‘what part of OMS’ is shown on the left - it has 8 elements – leadership, organization, risk, procedures, assets, optimization, privilege to operate and results.
Each element contains a series of statements on what each operation must do – from leaders providing clear direction through to collecting and learning from performance data. Where necessary, the statements are backed up by standards and procedures that set out how to meet them.
The ‘how part’ of OMS is the performance improvement cycle or PIC cycle (on the right of the slide). It is designed to run at least annually and is based on the International Standards Organisation: Plan-Perform-Measure-Improve cycle. Its purpose is to identify, prioritise and implement planned improvements.
OMS is used at all our operations sites - meaning that they are using it to progressively align their existing procedures and practices with the high level statements set out in OMS. We have created ways whereby sites can learn from each other, including a program called EXEMPLAR which brings specialist coaches onto sites to help them accelerate in particular areas of OMS.
Our fourth focus area is risk assessment and risk management. Let me now briefly explain how we manage safety and operational risks.
As well as the many procedures used at the frontline to manage individual risks on a daily basis, we have a single BP-wide required framework within which risks are identified, understood, managed, reduced and if possible eliminated.
Every BP operation performs an annual review of the risks it faces, refreshed as necessary during the year if there are substantial changes in circumstances. The operation confirms that controls are in place and sets priorities for further reduction or elimination. The output of the work can be captured in a matrix where risks are plotted to show both their potential severity and probability.
In the 2013 risk process, more than 50 businesses comprising many hundreds of facilities – in other words all of BP’s operations - are completing risk assessments and risk action plan reviews, and these will become inputs to their 2014 plan.
This is very powerful; it allows us to set accountabilities for specific risk reduction actions, track the completion of those actions, and confirm when risks have been reduced or eliminated entirely.
As I travel around the world to our various operating sites, I talk to folks at the front line who have embraced this systematic approach to understand their risks, the necessary barriers or controls in place and the health of those barriers. And I can see that this helps them to manage, and in some cases to eliminate, the specific point risks that we have in our assets. The front line is very engaged in this process.
One of the tools we find effective is the bowtie tool – many of you will be familiar with this tool. On the left it shows the barriers we create to prevent incidents – and on the right, the things we do to mitigate the impact if an incident occurs. It helps users to understand and manage both prevention barriers and mitigation barriers in place for each risk. This contributes to a deep and consistent understanding of the specific risks and can be used to help drive risk down.
The last principle and focus area is Checks and Balances. This is about inspection, checking, audit – what we generically call ‘assurance’. When it comes to safety, as long as you are careful to maintain clear accountabilities and a clear sense of ownership by decision-makers, two heads can be better than one and three can be better than two.
So we have a three-tier approach to assurance.
As the line is accountable for safety, they conduct self-verification to confirm whether they are conforming to OMS and their barriers are robust, and to enable them to take action as needed. This is the first tier.
Second, S&OR provides targeted, risk-based assurance by checking to see how the line is meeting requirements and maintaining and operating barriers. We do this on a structured way where we have a set topic, say control of work, where we see how well the line is demonstrating conformance. From looking across the company through these assessments, we can determine if there are points that need to be addressed across the company.
Last, we have audit. In addition to the company’s group internal audit team that looks beyond safety and operational risks, we have an audit team which sits inside S&OR and conducts a risk-based programme of regular safety and operations audits of the businesses operating on our OMS. We also audit third party rigs and ships to see if they meet our applicable standards.
If you’re wondering whether all of this is making a difference, let me tell you that I challenge myself on this every day.
And I believe that it is. Here’s one illustration of why I believe we’re seeing improved outcomes. You can see from this slide some of key metrics and how we are performing – this is data for BP Group.
We continue to see downward trends in process safety events and losses of primary containment – LOPCs - which are essentially leaks.
In 2008 when we first put the LOPC metric in place we had 658 releases. Last year we had 292. That was a 19% reduction versus 2011.
Process safety events are categorized by tiers depending on their severity, with tier 1 being the most significant. For BP, we saw a 42% reduction in Tier 1 PSEs in 2012 on 2011.
Of course, while such data is encouraging, tracking this data is only part of BP’s efforts to drive continuous improvement. But I believe the data suggest we are beginning to see the benefits of the various ongoing activities I’ve described. Even one LOPC can have high consequences, and any accident is one too many - and of course there is always more to be done.
Admiral Skip Bowman says “when you think things are going the best, you should be losing the most sleep”. And of course that is a clear message about never being complacent.
So that brings me to the end of my talk. I hope that from what I have shared with you that it is clear that safety and operational risk are truly at the heart of BP.
It all starts with leadership. From Bob Dudley our CEO on down, the tone, message and expectations are clear.
We have been working hard to implement the lessons of 2010. We are becoming even more systematic in how we operate. Our management system and risk process are key components to drive continuous improvement.
Our new Safety and Operational Risk organization is acting as an independent expert body in BP to help further improve the quality of operations
And while we believe these things are making a difference, we also know there is always more to do at BP and in the industry, and we must remain vigilant.
The Piper Alpha and Deepwater Horizon accidents remind us all of the consequences when things go wrong. They also provide lessons from which we all can learn and improve.
Selecting the right float switch for level-sensing applications
Administrator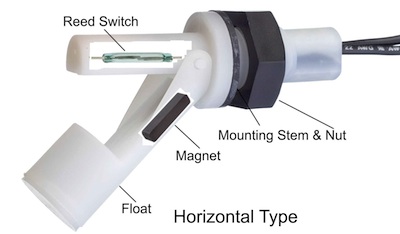
When selecting a float switch for a liquid level sensing application, a number of factors need to be considered, including float switch and gasket materials, physical arrangement, electrical ratings and cable type, says Simon Dear of Cynergy3 Components:
Many industrial processes require devices that are able to sense the level of liquid stored within various types of tank or chamber. The signals from these devices may be used to control the production process or to provide indication of the status.
One of the most reliable, well-proven technologies for liquid level sensing is a float switch. This type of switch comprises a magnet contained within a float, as well as a magnetic reed switch contained within a fixed housing.
The movement of the float, due to the changing liquid level, will cause the reed switch to operate (i.e. close or open) at a particular level. This tried and trusted technology is based on a relatively simple design that offers long term reliability without the need for the user to calibrate the switch.
Whilst there are different methods available for selecting the right float switch for a particular application, the main factors to consider include the following:
Physical arrangement and style
The choice of styles that may be suitable for an application will depend on the physical arrangement of the tank, the available mounting positions and whether access is available to the inside of the tank. The main styles are horizontal/side mounting and vertical mounting.
The horizontal/side mounting type normally has a fixed housing, which passes through the sidewall of a tank, with a hinged float attached to the fixed housing. Vertical mounting types normally have a fixed vertical stem, which is installed through the top or bottom of a tank, along which slides a cylindrical float.
Another important consideration is whether a build up of deposits from the liquid on the float body is likely to occur. These deposits can, over a period of time, accumulate to such an extent that the float switch can fail to operate.
Whilst particular types of float switch have been developed to limit the effects of this build up, the experience and knowledge of the switch manufacturer is also critical here.
Material selection
It is critical to select a float switch that is constructed from the right materials that are compatible with the liquids and temperatures of the particular application.
Component damage as a result of incorrect materials selection can ultimately cause failure of a float switch, which may have severe consequences. Typical float switch materials include:
- Nylon: suitable for many oils, diesel, organic chemicals and MEK-based printing inks.
- Polypropylene (PP): suitable for many acids and alkali, detergents, inorganic and organic chemicals, oils and water.
- Polyphenylene sulphide (PPS): suitable for many of the more aggressive chemicals and higher process temperatures, up to 120ºC.
- Buna/Nitrophyl: suitable for many oils, diesel, petrol and water (non-potable applications).
- D300 foam (PVC): suitable for most hydraulic oils and many chemical solutions.
- Stainless steel: suitable for most medical and food applications, chemicals, hydraulic fluids, fuel oils and applications with process temperatures up to 135ºC.
Selection of the most suitable materials for both float switch and gasket can be made by referring to a ‘Chemical Compatibility’ table. These tables provide a good indication of the suitability of the various float switch materials in a wide range of liquids.
For some process liquids, it may be necessary to obtain a sample float switch in order to test the compatibility.
Electrical
It is important to fully understand the nature of the load that needs to be switched and to ensure that the float switch is capable of handling this load.
The electrical ratings, which most manufacturers provide in their float switch specifications, are for purely resistive loads. Any loads that have either inductive or capacitive components should have the appropriate contact protection measure applied.
Cables
In applications where aggressive liquids may spill onto external wiring, it is important to specify particular materials for the cables used to connect to the float switches. There are standard, UL-approved cable types for the various float switches, as well as high temperature, low smoke zero halogen (LSZH) and other specialised materials.
Custom engineered float switches
The operating environment is critical to the choice of float switch. A water tank for an industrial process may only require a simple plastic float switch.
However, if the application is in a hazardous area, for example, a petrochemical storage tank where flammable gases, vapours or dust are present, a stainless steel, explosion-proof float switch will be required.

Metso has reported winning a "high-value" contract to supply pneumatic ball valves and butterfly valves to Yantai Wanhua Polyurethanes Ltd – its first deal with the Chinese chemicals producer.
The valves will be used in an MDI (diphenymethane disocyanate) integration project at the company's existing factory site and a new PO/AE integration project under construction in China (epoxy propane and acrylic ester).
Yantai Wanhua is the largest MDI manufacturer in the Asia-pacific region, currently owning three MDI plants with a combined capacity of 1000ktpa. The company achieved 2011 revenues of $2.28 billion, net profits of $308 million.
The company has invested around $5 billion in the two projects. The PO/AE integration project includes plants for propane dehydrogenation, acrylate, and acrylic acid resin, propylene oxide, and polyhydric alcohols, as well as a LPG storage cavern.
”Metso’s valve solutions were chosen because they meet the strictest standards regarding leakage class and low fugitive emission,” says Steven Wang, account manager, Automation, Metso.
Metso will supply ball valves including its X series, D series stemball valves, 9000 series flanged valves, S6 series metal seated high pressure valves, and the R-series V-port segment control valves. Materials of construction range from WCB and CF8M grade to Hastelloy, 316L and Monel per the customer’s specification.
The key components of the MDI project, which includes plants for producing isocyanate, oxidized hydrogen chloride, and nitrobenzene, require valves that deliver a superior tightness in difficult applications over long time and which promise control of fugitive emissions.
Metso’s deliveries include 700, L6 Neldisc triple eccentric butterfly valves that are engineered to accommodate the specific requirements of the projects.
The Neldisc L6 series is a triple eccentric butterfly valve with a metal seat. The trim consists of a precision elliptical disc and a chrome-plated seat attached to the casing with a stainless steel clamp ring. This is said to make it easy to assemble and dismantle for maintenance.
According to Metso, such metal seats are more resistant to abrasion and more tolerant of liquids at a high pressure and temperature, all of which ensures a longer operational life.
When the valve is open, the disc and seat are separated, which significantly reduces abrasion between the sealing components, reduces operational delays and wear on sealing surfaces, and also lowers valve torque.
When the valve is closed, the sealing is achieved through the elasticity of the valve seat; assistance from pressure generated by flowing liquid is not required, meaning that a firm sealing can be achieved even where the pressure differential is low.
More...
FLI Energy has started construction work on a new biomethane-to-grid plant in Ellough, Suffolk, UK with a thermal energy capacity of 12MW.
The anaerobic digestion project will produce around 2,000m3/hour of raw biogas from locally produced crops. and deliver 1,100Nm3/hour of biomethane. It will also deliver organic fertiliser back to local farmers.
“Injecting biomethane produced through anaerobic digestion into the gas grid is one of the most efficient uses of biogas," said FLI Energy’s managing director Declan McGrath "Biomethane from AD could potentially deliver 10% of the UK’s domestic gas demand.”
The Ellough project is being led by BioCore Environmental Ltd which contracted FLI Energy to provide a full EPC-wrapped project, including the design, construction and commissioning of the plant, as well as a five-year maintenance and process analysis support contract.
The contract scope includes detailed civil and process design, ground-works, site secondary containment bunding, drainage, silage clamp, digestate storage, AD plant technology, 500 kWe CHP, biogas upgrading, propane addition and biomethane network entry.
Biocore awarded the contract through funding partner Cambridge-based funding partner Eastern Counties Finance (ECF). It has financed more than 100 on-farm energy projects in the last two years, from wind turbines and solar panels, to AD and biogas plants.
FLI Energy offers turnkey AD plant construction, processing agricultural and commercial organic feedstocks to produce biogas and generate renewable energy. It is part of the FLI Group, based in Kempston, Bedfordshire, which provides design, project management, contracting, project delivery and operational services across the environmental, waste, water and energy sectors.
FLI Energy works in co-operation with its AD technology designer Host BV, based in The Netherlands. Projects are delivered by F.L.I. Energy using in-house resources in project management, process, civils, M&E and operations.
HoSt is currently the largest provider of AD technology infrastructure in the Netherlands with over 70 international operating plants, digesting mixed feedstocks.
BioCore Environmental has established a significant presence in the UK and Ireland in the development and operation of AD plants and in the sludge management services sector. It is currently developing AD plants with a combined power output in excess of 25MW.
Landia is to supply equipment for two new wastewater treatment plants that are being built in Guilin, China.
The order, for a total of 78 flowmakers, mixers and recirculation pumps was based on the reliability and performance of 20 Landia flowmakers that have served Guilin since 1995.
The POPL-I flowmakers will be installed in the aeration, anoxic and anaerobic zones at Guilin, where their low rotations provide flexibility for wastewater treatment. The units, which are designed for harsh conditions, will also agitate, homogenise and keep solids in suspension.
Meanwhile, Landia’s energy-saving AXP-I pumps, which recirculate large volumes of water at low head will recirculate activated sludge from the Aeration Zone into the anoxic zone at Guilin.
This latest export order for Landia follows its recent contract with Triveni Engineering & Industries Ltd to supply 18 BioMover mixers for a water treatment plant in Agra, India.

RWE is pulling the plug 3,100 MW of generation capacity in response to price pressures in the electricity markets linked to the growing use of solar power.
The cutbacks reflect reduction in power station margins as evidenced by an almost two-thirds drop in first half operating profits at the group's 'conventional power generation' division.
According to RWE, the continuing boom in solar energy, many power stations throughout the sector and across Europe are no longer profitable to operate.
Indeed, it has been cushioned from the full impact as it sold most of its electricity production two to three years in advance. These deals were made on the forward-market prices that have since declined.
In response RWE is taking 3,100 MW of generation capacity offline in Germany and The Netherlands. Further power stations are being assessed and all options to improve the company’s economic efficiency are being explored.
In the first half of 2013, RWE produced 111.3 billion kWh of electricity – 1% less than in the same period last year. Electricity sales to external customers declined by 4% to 135.9 billion kWh.
The industrial and corporate customers segment experienced a significant decline after RWE stopped auctioning off electricity in Germany from 1 Jan 2013. In Germany, the group was able to gain new customers in the distributor segment.
RWE npower and Essent had to absorb competition-induced sales losses among its industrial and corporate customers, the group also noted.
The UK Offshore Operators Group has voiced concern over the actions of protesters who have forced a temporary suspension of Cuadrilla's operations in Balcombe in West Sussex.
While acknowledging the current debate surrounding shale and onshore gas extraction and the right to protest peacefully, Ken Cronin, chief executive of the UKOOG condemned the threats and intimation directed at the company and its workers.
In an open letter about the protests, Cronin said: "We cannot, however, allow single issue pressure groups to subvert the rule of law and prevent Cuadrilla’s workers from carrying out their lawful operations, as well as having the safety of the company’s staff and Balcombe’s residents compromised."
According to XXXX, the UK has benefited from having an onshore oil and gas industry for over a century. Over 2,000 wells have been drilled – many of them hydraulically fractured – and over 300 are currently operational. Several thousand families in the UK already rely on the onshore oil and gas industry for their income.
Cuadrilla – and the wider onshore gas industry – complies with all legal and regulatory channels with regards to its operations, the UKOOG leader continued.
The industry, he said, operates in compliance with UK environmental legislation, which among the strictest in the world.
"Every member of UKOOG abides by the shale well guidelines which are highlighted on our website for all to see," said Cronin. "The exploratory well at Balcombe – which by the way is a conventional oil exploration site, not a shale gas site - is a continuation of that tradition.
"As we begin the exploration for oil and gas from previously undeveloped sources, we will work with local communities to ensure that they understand what we are doing, how we are doing it and the steps we will take to mitigate concerns around safety, noise, dust, truck movements and other environmental issues."
While welcoming dialogue with local communities and the wider public, Cronin concluded: "It is not right that the onshore oil and gas industry has to deal with threats of direct action, intimidation and “mass civil disobedience” against our staff and property, which prevent us carrying out our lawful operations."