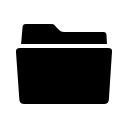
Uncategorised (4996)
Bakery and Confectionery equipment specialist standardises on Qdos pumps for pilot installations
AdministratorAn established Dutch food equipment designer, Tanis Food Tec, which specialises in process installations for bakery and confectionery products, is relying on Qdos peristaltic metering pumps from Watson-Marlow Fluid Technology Group (WMFTG) for all of its pilot machines. These pilot machines are deployed in R&D departments at major food manufacturers, where the accuracy of Qdos pumps in the dosing of colouring and flavouring is vital during development processes to help optimise the quality and cost of the end product.
Established in 1991, Tanis Food Tec has nurtured an enviable reputation for the development of sophisticated, fully automatic food processing solutions that involve operations such as weighing, preparing, pre-mixing, tempering, crystallising, plasticising, aerating, depositing, coating and decorating. The company says that these characteristics make it a future-orientated, reliable partner for confectionery and dairy manufacturers, as well as industrial bakers.
While Tanis Food Tec has hundreds of continuous, software-controlled production lines around the globe making millions of carefully crafted treats, the Lelystad-based company also produces numerous pilot machines for customers looking to develop new products and manufacturing processes. Since 2017 Tanis has been using Qdos pumps from WMFTG for this purpose.
“At Tanis Food Tec we use Qdos for the accurate dosing of colours and flavours within R&D departments, and today these pumps have become an integral part of our pilot machines,” confirms Piet Vader, the company’s Sales Manager. “The high precision with which the Qdos can handle both small and large volumes of fluid is crucial to adjust recipes and dosages, or perform exact process replication.”
Dosing accuracy saves on costs
ReNu peristaltic pumphead technology is at the core of the Qdos pump, ensuring the delivery of accurate and repeatable flow for fluids of wide ranging viscosities.
“The accuracy of the Qdos peristaltic pump is a key feature because colours and flavours are often very expensive ingredients,” says Mr Vader. “In fact, these ingredients can cost more than €10,000 per kg, so precise dosing is extremely important. Qdos pump accuracy is therefore important for both the quality and prime cost of the end product.”
Of course, the accuracy of Qdos pumps is an important asset for many industries, not just the food sector. A case in point is personal care.
“At Tanis Food Tec we focus primarily on the food industry, however, the use of Qdos pumps has allowed us to diversify beyond our traditional markets,” says Mr Vader.” For instance, we currently have one of our pilot machines installed at a large company that develops personal care products. It goes without saying that the cosmetics industry also uses expensive components in its products, which is why accurate and repeatable dosing is so vital."
Repeatable performance
Repeatability is a critical factor as the products pumped by Qdos pumps differ greatly in terms of viscosity, for example.
“And yet Qdos pumps maintain very accurate and continuous dosage at different system pressures,” says Mr Vader. “Additionally, ease of use is a great advantage. The display screen on Qdos pumps shows all the important information.”
“Among further benefits, removing and replacing the pumpheads can be done very quickly,” he adds. “Moreover, it is possible to change between pumping different substances without any risk of contaminating the surrounding environment or personnel.”
“Another significant advantage is that Qdos pumps need hardly any maintenance,” says Mr Vader. “Unlike membrane pumps, peristaltic pumps do not have suction and discharge valves that often demand higher levels of maintenance."
Using Qdos means that process uptime is maximised by facilitating quick, safe and easy pumphead removal and replacement, with no requirement for tools, specialist training or dedicated technicians. Unlike on many other pump types, using Qdos pumps means there are no valves or seals to clog, leak or corrode, reducing maintenance costs considerably.
Long-standing partner
Watson-Marlow has been known to Tanis Food Tec for many years, and has enjoyed high levels of satisfaction with the pump manufacturer’s service and support.
“In Watson-Marlow we’ve found a partner that offers quality at a fair price and honours all agreements between our companies,” states Mr Vader. “We really value these three factors when it comes to building relationships with suppliers."
So, is the Qdos pump set to remain the preferred choice at Tanis Food Tec?
“Yes, especially for this type of pilot installation, for which Qdos is ideal,” concludes Mr Vader. “It has become our standard solution.”
SRP700, system ready package, is a solution offering based on the FieldCare device configuration application and combined with new Health Monitoring Application software.
Endress+Hauser launches its Asset Health Monitoring Solution, a pre-engineered software-based solution for Rockwell Automation systems and tailored for various industries. The solution accesses field instrumentation diagnostics and presents it in easily readable format to plant personnel, improving transparency, reducing maintenance costs and increasing plant availability.
The SRP700 runs on traditional hardware or in a virtual machine environment and is comprised of a central monitor and gateway, a standard client for device configuration management as well as a mobile client, and the field-proven Field Xpert SMT70 IP65/Class 1 Div 2 industrial tablet. It is used to access and acquire data from a variety of field devices, primarily analyzers and instruments. A KPI Dashboard (optional) presents diagnostics, history, statistics, and other information. in an easily readable format.
Plant personnel can use the SRP700 to:
- • Take actions on diagnostic data provided by devices
- • Connect to devices for troubleshooting and configuration
- • See actual and past diagnostic data with corrective measures related with time stamps
- • Analyze historical device diagnostic data
The Rockwell Edition of Endress+Hauser’s Asset Health Monitoring solution leverages Rockwell Automation PAC and HART I/O infrastructure to directly monitor diagnostics from Endress+Hauser and 3rd party field process instruments for process technician users.
For more information visit https://eh.digital/3dNcIfL.
About Endress+Hauser in the U.S.
Endress+Hauser is a global leader in measurement instrumentation, services and solutions for industrial process engineering. Endress+Hauser provides sensors, instruments, systems and services for level, flow, pressure and temperature measurement as well as analytics and data acquisition. We work closely with the chemical, petrochemical, food & beverage, oil & gas, water & wastewater, power & energy, life science, primaries & metal, renewable energies, pulp & paper and shipbuilding industries. Endress+Hauser supports its customers in optimizing their processes in terms of reliability, safety, economic efficiency and environmental impact. The Group employs nearly 14,000 personnel worldwide and generated [net sales of] more than 2.6 billion euros (2.89 billion U.S. dollars) in 2019.
Cortec® Presents Detailed Guidelines for Layup of Offshore Drilling Rigs in Uncertain Times
AdministratorWith uncertainty and mounting challenges on the horizon for the oil industry, many rig owners are already or will soon be facing the question of whether or not it is time to stack their offshore drilling rigs. Concerned about cutting losses and reducing capital output, they need cost-effective solutions for preserving the value of millions of dollars’ worth of assets in harsh conditions until they can either be put back into service or sold. This requires a serious look at corrosion preventative measures that are both effective and require minimal effort in order to bring the equipment back online. To help owners and operators navigate this major undertaking, Cortec® Corporation has published a new guide to the layup of offshore drilling rigs.
The guide begins with an index of 74 offshore rig systems to be preserved, with critical items in bold. Before addressing each system in alphabetical order, the guide notes several basic instructions for general layup, such as removing existing rust with VpCI®-423, cleaning with VpCI®-415, and coating external equipment surfaces with VpCI®-391. It also identifies which corrosion inhibitor additives to use with different types of lubrication oils and hydraulic fluids and specifies which VpCI® Emitters to employ for varying sizes of void space.
The handbook then goes step by step through the many important aspects of offshore layup, from prepping worker accommodations to preserving alarms—from flushing ballast systems with corrosion-inhibitor treated seawater to taking measures to carefully shut down a blowout preventer (BOP) control system. It even includes options for treating and deodorizing toilets and holding tanks with biologicals from Cortec® subsidiary, Bionetix® International. Several common preservation materials resurface again and again:
- MilCorr® VpCI® Shrink Film serves a critical role in preserving offshore equipment on-deck. It has an outstanding track record of protecting offshore equipment even in hurricane weather, and it is easy to remove for speedy startup of equipment.
- ElectriCorr® VpCI®-239 and VpCI® Emitters (VpCI®-101 Device, VpCI® -105, VpCI®-111, and VpCI®-308 Pouch) are convenient and effective for protecting electronics and electricals.
- CorrLube™ VpCI® Lithium EP Grease can be used for layup on many components where lubrication is needed. It has the advantage of being viable both during storage and intermittent use.
- VpCI®-369 is another important product to have in good supply for rust prevention of many internal components on an offshore platform.
In addition to their excellent protective qualities, VpCI® Technologies are typically easy to apply and remove, if needed. These are important factors for completing a successful rig-stacking program with the intention of a smooth return to service when demand makes drilling profitable again. Compared to the hundreds of millions of dollars of value that could otherwise be lost by equipment corrosion, investing in a cost-effective layup program is a small price to pay for the astronomical value preserved. Cortec’s layup guide helps ensure that it is done well.
Click here to learn more about the layup guide and contact Cortec® for access:
https://www.cortecvci.com/layup-of-offshore-drilling-rigs/
Cortec® Corporation is the global leader in innovative, environmentally responsible VpCI® and MCI® corrosion control technologies for Packaging, Metalworking, Construction, Electronics, Water Treatment, Oil & Gas, and other industries. Our relentless dedication to sustainability, quality, service, and support is unmatched in the industry. Headquartered in St. Paul, Minnesota, Cortec® manufactures over 400 products distributed worldwide. ISO 9001, ISO 14001:2004, & ISO 17025 Certified. Cortec Website: http://www.cortecvci.com Phone: 1-800-426-7832
Prolonged turbulence in the meat industry caused by COVID-19 detrimental to consumer confidence, says GlobalData
AdministratorFollowing the news (June 3rd) that Brazilian labor prosecutors have filed a petition with a local court demanding the closure of a JBS SA pork plant due to the outbreak of novel Coronavirus, a decision that is still pending according to news reports;
Carmen Bryan, Consumer Analyst at GlobalData, a leading data and analytics company, offers her commentary on how this could impact consumer confidence:
“The challenges JBS are currently facing from COVID-19 are shared across the entire meat sector worldwide; meat processing plants are quickly being labelled as hotspots for the virus and, should this continue, it could deter many consumers from purchasing such products. Confusion around how the virus is spread and where it came from reinforces what we are already seeing as cautionary behavior from some consumers, and may lead them to opt for alternative meat offerings.
“It’s worth noting that, as of week 10 of GlobalData’s weekly COVID-19 tracker survey, published on June 3rd, 73% of Brazilian consumers are concerned about the safety of product packaging* – and such concerns will also translate to production further down in the supply chain, particularly as people demand more transparency from brands and operators.
Across different sectors, COVID-19 has highlighted the importance of adapting operations to guarantee people and product safety in the face of the crisis – something that the meat industry continues to strive to achieve.”
*GlobalData’s Coronavirus (COVID-19) Tracker Survey – Week 10 (June 3rd) – Brazil – combined ‘Strongly agree’ and ‘Somewhat agree’
About GlobalData
4,000 of the world’s largest companies, including over 70% of FTSE 100 and 60% of Fortune 100 companies, make more timely and better business decisions thanks to GlobalData’s unique data, expert analysis and innovative solutions, all in one platform. GlobalData’s mission is to help our clients decode the future to be more successful and innovative across a range of industries, including the healthcare, consumer, retail, financial, technology and professional services sectors.
Coal to play integral part in Japan’s power sector as COVID-19 hurts solar projects’ development, says GlobalData
AdministratorIn the wake of the COVID-19, electricity demand in Japan has dropped and the power prices have declined. The drop in demand and the increase in solar power generation are eventually driving down the wholesale electricity prices. The ongoing economic contraction, delays in the shipment of photovoltaic (PV) modules from China, and low nuclear availability are likely to facilitate the use of coal and gas to support the baseload power requirement in the country, says GlobalData, a leading data and analytics company.
Solar is the major driving force for renewable deployment in the country. Before the COVID-19 outbreak, revisions in the tariff structure and grid interconnection issues were likely to slow down deployment. Amid these times, the country witnessed a halt in construction activity, which is expected to further delay the installation of fresh capacities.
With hiccups in the solar front, coal is expected to continue to play an integral role in the country’s power sector. Despite the low power demand, the abnormal weather conditions and low availability of nuclear facilities are expected to support the high consumption of coal for electricity generation. In the first three months of 2020, Japan imported 44.8 million tons of coal, which increased by 3.4% in comparison to 43.3 million tons imported in the first quarter of 2019.
Somik Das, Senior Power Analyst at GlobalData, comments: “ Japan, in its quest to meet the target of having 24% of its energy use from renewables by 2030, made investments in the solar and offshore wind a priority. However, these efforts are expected to experience a set back due to the COVID-19 outbreak. As China forms an integral part of the solar supply chain, the onset of the pandemic has affected the shipment of photovoltaic modules and other equipment for many Japanese developers.
“As per the last amendments to Renewable Energy Act, solar projects have to meet strict deadlines to reach commercial operation, the government has released an aid to help the projects bound by power purchase agreements (PPAs). In the US$1.1 trillion stimulus package, the government has made provisions of US$1bn for the development of onsite renewables which are expected to support corporate power purchase agreements (PPA) under their commitment to the RE100 initiative.”
- Comments provided by Somik Das, Senior Power Analyst at GlobalData
- This insight was based upon data and information sourced from proprietary databases, primary and secondary research, and in-house analysis conducted by GlobalData’s team of industry experts
About GlobalData
4,000 of the world’s largest companies, including over 70% of FTSE 100 and 60% of Fortune 100 companies, make more timely and better business decisions thanks to GlobalData’s unique data, expert analysis and innovative solutions, all in one platform. GlobalData’s mission is to help our clients decode the future to be more successful and innovative across a range of industries, including the healthcare, consumer, retail, financial, technology and professional services sectors.
DNV GL, the technical advisor to the oil and gas industry, has approved as qualified, technology for a full-scale demonstration project in Norway to remove carbon emissions at a cement plant. Gassnova, the Norwegian state’s agency for implementation of carbon capture and storage projects, initiated the project which will apply carbon capture technology developed by Aker Solutions at Norcem’s cement plant in Brevik, Norway.
Globally, the cement industry accounts for 5-7% of total CO2 emissions – from all industries and sectors. Aker Solutions’ post-combustion technology is intended to capture and liquefy 400,000 tons per year of the released carbon dioxide at the Norcem plant. Once the technology is applied this will contribute to Norway’s target of becoming a low-emission society by 2050.
DNV GL engaged with Norcem and Aker Solutions to verify the application of DNV GL’s recommended practices DNVGL-RP-A203 Technology Qualification and DNVGL-RP-J201 Qualification procedures for carbon dioxide capture technology at the plant.
Novel elements of Aker Solutions’ carbon capture technology and potential technological risks were evaluated and mitigation identified. Documentation was reviewed to provide a better understanding of the technology and the specific application and conditions at Norcem’s plant.
Arve Johan Kalleklev, Regional Manager, Norway and Eurasia, DNV GL – Oil & Gas said: “Carbon capture, and subsequent storage, is currently the only technology that can achieve significant reductions in CO2 emissions from industrial processes. Carbon capture can play a vital part in decarbonizing our planet. DNV GL’s qualification review of Aker Solutions’ technology is a great example of how we engage to enable implementation of this crucial technology. “
As a result of the qualification procedure review, DNV GL issued a ‘Statement of Qualified Technology’ for Aker Solutions’ carbon capture and heat recovery technology, applicable for the conditions at the Norcem Brevik cement plant.
Per Brevik, Director Sustainability and alternative fuels in HeidelbergCement Northern Europe states: “Aker Solutions have tested their technology at Norcem Brevik for 18 months. Their world class expertise, systematic work and the promising results from pilot testing in Brevik give us confidence that realisation of the full-scale capture plant will be successful. Based on the third-party technology qualification professionally executed by DNV GL, we trust that the project risk related to novel technology elements is low.”
The Norcem Brevik carbon capture plant forms part of Europe’s first industrial demonstration of CO2 capture, transport and storage. The captured CO2 is to be transported and injected into a CO2 storage site offshore Norway, developed by the Equinor-headed Northern Lights consortium.
Oscar Graff, Head of CCUS in Aker Solutions said: “The extensive experience and systematic qualification procedures from DNV GL have been a great support for our engineers in our technology development. The procedure is an excellent tool to identify risk elements and to propose how to solve them. To get a statement of qualified technology from DNV GL, as a recognized third party, has high value for Aker Solutions and our clients.”
About DNV GL
DNV GL is the independent expert in risk management and quality assurance, operating in more than 100 countries. Through its broad experience and deep expertise DNV GL advances safety and sustainable performance, sets industry benchmarks, and inspires and invents solutions.
Whether assessing a new ship design, optimizing the performance of a wind farm, analyzing sensor data from a gas pipeline or certifying a food company’s supply chain, DNV GL enables its customers and their stakeholders to make critical decisions with confidence.
Driven by its purpose, to safeguard life, property, and the environment, DNV GL helps tackle the challenges and global transformations facing its customers and the world today and is a trusted voice for many of the world’s most successful and forward-thinking companies.
DNV GL is the technical advisor to the oil and gas industry. We bring a broader view to complex business and technology risks in global and local markets. Providing a neutral ground for industry cooperation, we create and share knowledge with our customers, setting standards for technology development and implementation. From project initiation to decommissioning, our independent experts enable companies to make the right choices for a safer, smarter and greener future.
About Norcem
Norcem is the leading Norwegian supplier of cement, the main component of concrete. Norcem has a wide distribution network of depots along the Norwegian coast. Norcem is also the sole producer of cement in Norway, with plants in Brevik and Kjøpsvik.
Norcem is a company in HeidelbergCement Group, a global player in cement, aggregates, concrete and downstream activities, making it one of the world's largest manufacturers of building materials. The company employs about 60 000 people in more than 60 countries.
About Aker Solutions
Aker Solutions is a global technology and service company providing solutions and products for the industry. Aker Solutions is offering low carbon solutions such as floating wind power and Carbon Capture, Utilization and Storage (CCUS). Aker Solutions has developed an Advanced Carbon Capture Technology since 2005 and are now offering commercial plants in the market, both modularized and large-scale integrated plants. Aker Solutions is providing technology and products for the entire CCUS value chain, from capture, via transport, injection, storage and Enhanced Oil Recovery (EOR). The company employs about 16 000 people in about 20 countries and 50 locations.
Depressed demand and falling oil and gas prices challenges global LNG sector, says GlobalData
AdministratorThe global liquefied natural gas (LNG) sector has been hit by supply overhang followed by COVID-19-induced economic slowdown and lower demand worldwide.
Haseeb Ahmed, Oil and Gas analyst at GlobalData, comments: “Due to the sharp fall in oil prices, spread between oil-indexed long-term LNG contracts and spot contracts have considerably reduced. This can make it challenging for LNG producers to meet their revenue targets. In addition, a rapid decline in gas demand is affecting financing of capital-intensive new liquefaction projects, leading to inordinate delays and capex reductions.”
To keep a check on spends, several operators are delaying their upcoming LNG projects. Operators are reducing their expenditures for 2020 as a measure to counter the impacts of COVID-19. Woodside Energy and Exxon Mobil have resorted to downsizing their capex by 60% and 30%, respectively, for 2020. In the meanwhile, British Petroleum has pushed the timeline for its Tortue FLNG project from 2020 to 2023 in response to the COVID-19 impact. Similarly, Qatar Petroleum has also postponed the project timelines of its Ras Laffan North Field LNG terminal development by a year to 2025.
Ahmed concludes: “A silver lining amid all the chaos induced by the pandemic outbreak is increased opportunities for new entrants to the LNG sector. Global LNG oversupply, as well as low LNG prices, might encourage new countries and companies to start importing LNG, contributing to LNG industry growth. Sustained low LNG prices will encourage several gas-importing countries to switch from coal and oil to cleaner natural gas.”
- Comments provided by Sujith Singh – Oil & Gas Analyst at GlobalData
- This report was built using data and information sourced from proprietary databases, primary and secondary research, and in-house analysis conducted by GlobalData’s team of industry experts.
About GlobalData
4,000 of the world’s largest companies, including over 70% of FTSE 100 and 60% of Fortune 100 companies, make more timely and better business decisions thanks to GlobalData’s unique data, expert analysis and innovative solutions, all in one platform. GlobalData’s mission is to help our clients decode the future to be more successful and innovative across a range of industries, including the healthcare, consumer, retail, technology, energy, financial and professional services sectors.
Switzerland attempts to lift solar PV market with rebates amid COVID-19 pandemic, says GlobalData
AdministratorIn the wake of the COVID-19 pandemic, the Swiss solar PV market is on the verge of experiencing a slump. To offset this threat and support the residential and commercial rooftop solar, Switzerland has offered to increase financial support through rebates by another US$47m. This means around US$387.6m will be available under the solar PV rebate scheme. This attempt is in line to arrest any possible slump in the solar market due to the pandemic, says GlobalData, a leading data and analytics company.
After hydropower and nuclear power, solar PV installations forms the third major source of power in Switzerland.
Somik Das, Senior Power Analyst at GlobalData, comments: “In 2018, the Swiss Photovoltaic Association, Swissolar, introduced the rebate scheme to benefit the residential and commercial PV customers. The rebate scheme was targeted at not only reducing the waiting time for the implementation of FIT contracts but also guarantee maximum coverage of 30% of the investment costs. The scheme acted as a massive push for more consumers to apply for the solar PV systems.”
Within months of implementation of the scheme, a large number of residential PV project applications came in and further applications of projects up to 100 kW had to wait for another two years. In 2020, applications under the scheme were coming in at a steady rate until January, however more recently, owing to the pandemic, applications have significantly reduced. In all probability, consumers have started predicting that the worsening pandemic situation would lead to the authorities failing to compensate for the project costs. Even with supply chain disruptions and prospective rise in investment costs, the guaranteed coverage, of the rebate scheme, has chances of experiencing a drop.
Das concludes: “The increase in the funding of the rebate program would put these concerns to rest. The extra funding will not only expand the rebate budget, helping authorities to maintain the guaranteed coverage against investment cost but also help reduce the waiting time for payments.
“The number of large projects awaiting payments has already started decreasing. Clearly, in the pandemic, the Swiss government with the expanded rebate budget averted the solar PV sector to experience a major blow.”
- Comments provided by Somik Das, Senior Power Analyst at GlobalData
- This insight was based upon data and information sourced from proprietary databases, primary and secondary research, and in-house analysis conducted by GlobalData’s team of industry experts
About GlobalData
4,000 of the world’s largest companies, including over 70% of FTSE 100 and 60% of Fortune 100 companies, make more timely and better business decisions thanks to GlobalData’s unique data, expert analysis, and innovative solutions, all in one platform. GlobalData’s mission is to help our clients decode the future to be more successful and innovative across a range of industries, including the healthcare, consumer, retail, financial, technology and professional services sectors.
[Success story] Halyard Health: Three Layers Lamination Line for Medical Use in an Integrated System
AdministratorHalyard Health (Halyard), a company now part of the Owens & Minor family of companies, acquired in 2018, is a supplier of protective medical clothing and materials, such as sterilization wrap, face masks, gloves and surgical drapes and surgical drapes, to more than 100 countries.
With 11 manufacturing facilities across the globe, Halyard relies on superior machinery to produce top-quality products.
Upon acquiring Halyard, Owens & Minor continued to support a previously recognized need to insource all production of film laminate fabrics in-house, as the production of these fabrics had been with an external supplier. The timing of this expansion (completed in 2019) was important, as the unexpected shock in demand with the COVID-19 pandemic began to be visible late that same year. The increase in demand for medical film laminate nonwovens in 2020 has been a challenge Halyard has risen to, thanks to A.Celli’s help.
The underlying problem of the previous lamination line
Halyard was using film laminate fabrics for its highest protection gowns made by an external supplier. However, due to higher costs and less control of the supply chain, it was recognized that this production needed to be in-house. In addition, there were limitations with the capacity of the external supplier that would not allow Halyard to meet the needs of any unplanned surge in demand. Halyard needed a solution that would boost production without compromising quality or significantly increasing costs.
Read more: 3 ways to boost lightweight laminated nonwoven production (with 0 risks)
Why did Halyard choose A.Celli
Halyard did their research and discovered A.Celli and their history of innovation, superior machinery and unparalleled customer service. That is why Halyard reached out to us through our website to request information about capabilities of our lamination machine solutions.
Launched as a family-run business in 1944, A.Celli has grown into a renowned international company that supplies high-end machinery and technological solutions for both the tissue and nonwovens industries. One of the elements for which we are universally recognized is the innovative character of everything we do.
A.Celli is specialized in tissue, nonwovens and paper winding and rewinding, complete turnkey tissue plants, multifunctional solutions for nonwovens plants (including lamination, spooling and printing systems), upgrades/updates, rebuilding and retrofit of obsolete machinery and digital solutions designed to optimize production and maintenance and monitor every stage of the production processes.
When Halyard contacted us on January 2017, the initial calls were for a feasibility assessment and understanding of what options could be available for a solution with Halyard. Our sales department promptly made an offer based on their request and, shortly after this, a meeting was arranged in North Carolina to evaluate their plant and their specific needs.
Halyard was impressed by what we had to offer and, after various technical discussions and Owens & Minor approval of a capital expenditure, a contract was signed on July 18, 2018.
A.Celli got straight to work, building a lamination machine that matched Halyard’s needs. In May 2019, the operation of the machine was tested on the A.Celli premises with excellent results and the machine was then shipped to Halyard and arrived in July 2019, installed in Halyard’s Linwood, NC plant in August and tested onsite in September.
Halyard was incredibly satisfied and signed off on the final acceptance on October 11, 2019.
How Halyard boosted its production: the project
At the time the Linwood, North Carolina Halyard plant was acquired by Owens & Minor, the plant was a traditional spunlaid nonwovens plant with several Spunbond and SMS lines, primarily supporting medical nonwoven fabric production. In addition, the facility has Converting assets that manufacture some finished product like Sterilization Wrap and AAMI2 Cover gowns.
The Film Laminate equipment provided to Halyard by A.Celli included:
- Unwinder and unwinder loading system
- Web handling and transfer rollers, including spreader systems and tension control equipment
- Lamination frame to host adhesive bonding equipment
- In-line slitting winder, edge trim removal systems and roll handling system
- Shaft extraction system and crane for returning empty shafts back to the winder
A specific list of the equipment supplied includes:
- Two Nonstop Shaftless Unwind Stand for Spunbond/SMS
- One Nonstop Shaftless Unwind Stand for PE Film
- Product Threading and Passage Structure
- Lamination Frame
- Defect Management System (DMS)
- Automatic Winder with In-Line Slitting “Stream”
- Flag Applicator System
- Shaft Handling System
- Roll Handling System
The A.Celli solution implemented the automation of processes along the production line. These automated processes include:
- Winding
- Slitting
- Reel ejection and core loading
The results of the new A.Celli lamination machine
The automation of these processes made it possible for Halyard to make their highest protection gown fabrics while improving overall costs, and with the added benefit of internal product quality control. In addition to this, the new line is equipped with world-class barrier safeguards and interlocks for improved safety.
With increased fabric demand for medical Personal Protective Equipment (PPE) for protection against the COVID-19 virus, this new lamination line is now running at double the original forecast volume. In addition, Halyard has hired an extra 16+ operators to support the additional production shifts. Overall, production of all of the plant’s nonwovens fabrics and finished products has increased due to demand for PPE and there are plans to expand to additional nonwoven fabric offerings.
If you are interested in expanding your nonwovens capacity or starting a new production line, please contact us: we will discuss together the best solution for your needs.
New disconnect terminal blocks implement plug-in technology, safe design, and space savings with testing capabilities for use in CT and VT secondary circuits.
Dinkle International announces the availability of its DPT DIN rail disconnect terminal blocks to provide efficient, safe disconnect and testing of current transformer (CT) and voltage transformer (VT) circuits.
CTs and VTs isolate a primary power feed from a secondary circuit, permit grounding of the secondary circuit, and step-down the current or voltage to an appropriate level for measurement. Terminal blocks are then used as the termination points for instrument loops on the secondary circuit.
Panel builders have traditionally incorporated barrier-type terminal blocks in CT circuits—but these are challenging to access, require proper tools, and take time for backplane mounting and screw-down wire terminations. Additionally, there is always the danger of under-torqueing and loose wiring connections, or over-torqueing and stripped screw threads.
Dinkle’s DPT DIN rail series terminal blocks address these issues by providing easier access, DIN rail mounting with no tools required, and push-in design to ensure secure wiring connection while reducing time and tools required for termination.
The DPTD6 model block also provides direct-testing technology, enabling a user to test the circuit current without undoing any wired connections. To perform direct-test for a single or three-phase circuit, the user switches a lever on the terminal block to disconnect a de-energized circuit. The user then places a current-measuring device across the block at its test points using either 4mm test probes or securely fastened 2.3mm test plugs. The DPTL6 model version is similar to the DPTD6 but without a disconnect lever for testing.
Both blocks are UL rated up to 30 amps at 600 VAC. The blocks are DIN rail mountable and measure 8mm in width by 103.2mm in height by 50-57.5mm in depth (depending on DIN rail depth), allowing for easier installation and space saving compared with traditional barrier-type terminal blocks.
These push-in style blocks accommodate wire sizes from AWG20 to AWG8, and also feature plug-in slots for bridges (jumpers), providing reliable continuity between any combination of blocks on the same DIN rail. They are completely touch-safe—back of hand and finger protection—and operate at temperatures from -40°C (-40°F) to 120°C (248°F).
Users can employ these DPT series blocks to safely disconnect secondary circuits between measuring instruments and safety equipment in CT shorting and other applications. A safe disconnect can be achieved by placing the block in front of the measurement instrument.
Dinkle provides a complete product line of DIN rail terminal blocks to complement the DPT series, including but not limited to power distribution, sensor/actuator, diode embedded, and pluggable fuse blocks. Their products carry safety approvals including UL, CUL, CSA, VDE, and GB. The material used for manufacturing is compliant with RoHS and REACH environment standards set by EU. For more information, please visit Dinkle online at www.dinkle.com.
About Dinkle International
Founded in 1983, Dinkle is the largest terminal block manufacturer in Asia, with headquarters in Taipei and offices in over 40 countries. Since 1995, Dinkle products have been made at their Electrical R&D center and CNAS-certified laboratory in Kunshan, China. Dinkle’s products are used in industrial automation applications across many sectors including discrete part manufacturing, machinery, process plants and transportation. All Dinkle factories have received ISO 9001 and ISO 14001 certification.
More...
To enhance the turnkey solutions that it provides to its growing customer base, Borger has created a new partnership with long-established engineering business Panks - for sales, repair and installation of Borger pumps, macerators, separators and feed technology.
Panks (established 1842), will cover all of East Anglia for Borger, with whom they have already established a close working relationship after many years of successful projects in the water and agricultural sectors.
“We’ve now made our thriving partnership official”, said Borger UK’s Managing Director, David Brown.
“The engineers at Panks have always delivered the goods to the highest of standards. As we look to expand our turnkey option to clients, including the AD/biogas and industrial markets, we know we are in very safe hands”.
Chris Pank, Managing Director of the Norwich-based business, added: “We work well together with Borger, who always provide excellent technical and practical support for what is a very reliable and robust range of pumps. This partnership is good news for customers. It is a very good fit”.
Early Stage Funding for Startups Falls by 41% globally in Q1, Risking Job Recovery.
AdministratorEarly-stage startups have been hit the hardest in the first quarter of 2020, with early-stage funding rounds dropping by a massive 41% globally as compared to Q1 of 2019, according to a study by HexGn, startup research and consulting firm. Echoing the sentiment, the number of deals for early-stage funding has dropped to 2000 in the last quarter, from 3600 in Q1 of 2019.
At the global level, the impact of COVID-19 will be seen from this quarter onwards. Things don’t look bright for 2020, in Q1 itself, the number of startup deals globally has fallen by over 56%, signalling a deep slide ahead. Prelim data points that the number of transactions globally in the first quarter has fallen from 6500 levels to 4100, indicating gloomy sentiment, says HexGn study. Global startup funding has dropped by 15 percent to $60 billion in the first quarter of 2020 as compared to the first quarter of last year.
These numbers are early guidance, and there could be slight changes as more companies make announcements on funds received. We are anticipating delays in sharing of such information amid the coronavirus outbreak that has disrupted businesses worldwide.
At the global level, the impact of COVID-19 will be seen from this quarter onwards. Things don’t look bright for 2020, in Q1 itself, the number of startup deals globally has fallen by over 56%, signalling a deep slide ahead. Prelim data points that the number of transactions globally in the first quarter has fallen from 6500 levels to 4100, indicating gloomy sentiment, says HexGn study.
On the global front, the bad news continues to pour in for China, where funding in Q1 dropped by a massive 45 per cent from the previous year. The drop is even steeper when compared to the first quarter of 2018, dipping by 63 per cent. Asia has seen a massive dip, from $21 billion to $14 billion, mainly due to a drop in China’s numbers. European Startup investments have dipped from $10.8 billion to $9 billion in the said quarter. Even the global powerhouse, North America, saw its tech startup funding dip by 10 per cent last quarter, from $38 billion in Q1 of 2019.
All is not lost, there is some good news too for early stage entrepreneurs, Oceania, South America and Africa have seen a spurt in investments in the first quarter. Though the numbers remain small; it signals that investors are looking at other geographies for value investments. Africa has moved from $102 million in 2019 to $240 million, South America from $237 million to $434 million, Oceanic from $311 million to $511 million in the first quarter of this year as compared to the first quarter of 2019. Early stage entrepreneurs from mature markets could work across these newer markets and get access to startup funding.
With increased layoffs and a record number of unemployed in most countries, many jobless could take recourse to entrepreneurship and aid in economic recovery; however, the lack of investor appetite for idea-stage startups will derail the process. At this stage governments, large corporates and VC funds must support by providing, access to funds, grants and online acceleration programs to increase investor readiness of these startups. Now is not the time to sit on a high pedestal and reject funding decks, its about taking everybody together to restore dignity in people’s life by restoring work.
About HexGn
HexGn, through its global research, industry events, and online programs, equips individuals and businesses to tap into new opportunities and future proof themselves.
Engineers Learn from Home, Strengthen Skills for Current and Post-COVID-19 Pandemic Workplace
AdministratorASME brings flexible, affordable and applicable virtual training solutions to engineers everywhere
Lifelong learning for engineers doesn’t stop, even under quarantine during the COVID-19 pandemic. According to a recent survey of approximately 3,000 engineers conducted by the American Society of Mechanical Engineers (ASME), eight in 10 engineers anticipate a change in operations due to COVID-19 and reduction of business overall. This escalation of change in an already evolving industry landscape has prompted ASME to offer even more flexible, affordable, and applicable virtual training solutions to help engineers strengthen their skills for the current and post-pandemic workplace.
“The COVID-19 pandemic has had a profound impact on lives and livelihoods. The engineering work landscape has been rapidly evolving, and the pandemic has accelerated and changed the landscape in ways we are only beginning to understand,” says ASME Executive Director/CEO Tom Costabile. “Engineers are applying technologies including artificial intelligence, robotics and 3D printing to help respond to the public health crisis, and also to adapt processes in many industrial sectors and transform supply chains for the future.”
ASME Director of Learning and Development Arin Ceglia adds, “A significant number of engineers graduate with powerful textbook knowledge of fundamentals and theory, but lack the skills needed to apply that knowledge in their day-to-day work. Even experienced engineers might become siloed and not have the ability and awareness to keep pace with the rapidly evolving technical field.”
These two factors have combined to create a skills gap that worries industry leaders and educators. In manufacturing, for example, a 2018 (pre-pandemic) Deloitte study had estimated 2.4 million jobs would remain unfilled between 2018 and 2028, with an estimated economic impact of $2.5 trillion.
“Addressing this skills gap is critical, and it informs how those of us working in engineering learning and development approach everything from course design to education technology,” says Ceglia.
Many courses featured in ASME’s current training portfolio are based on the application of ASME codes and standards—from boilers and pressure vessels and gas turbines to piping and pipelines and design and materials. Others include opportunities for advancing engineering technology, including additive manufacturing, cell manufacturing and industrial automation. These courses fulfill a need to deliver this information faster, smarter, and in a more convenient way, and are now available with significantly discounted pricing.
ASME courses are built as part of a competency framework, or a learning architecture, so they also contribute to completing a stronger picture of a learner’s knowledge capabilities, indicating levels achieved in a set of core competencies, along with skills. Employers can track their employees’ progress in these competencies or skills, identifying areas of progress as well as where improvement (and targeted investment) is needed.
Visit https://resources.asme.org/learnfromhome for a list of current course offerings and more information.
About ASME
ASME helps the global engineering community develop solutions to real-world challenges. Founded in 1880 as the American Society of Mechanical Engineers, ASME is a not-for-profit professional organization that enables collaboration, knowledge sharing and skill development across all engineering disciplines, while promoting the vital role of the engineer in society. ASME codes and standards, publications, conferences, continuing education and professional development programs provide a foundation for advancing technical knowledge and a safer world. For more information visit asme.org.
Disruptions to supplies from China due to COVID-19 might slowdown wind installations in India, says GlobalData
AdministratorWind energy has been the fastest growing renewable energy sector in India in terms of installed capacity. India is the world’s fourth-largest onshore wind market with a cumulative installed capacity of 38.1 GW as of 2019. The COVID-19 pandemic is expected to cause wind commissioning project delays due to disruptions to the supplies from China, says GlobalData, a leading data and analytics company.
However, India would consider requests for extensions and waivers over previously decided project delivery deadlines.
India announced that the COVID-19 should be considered as a case of natural calamity and a force majeure event. This gives the right to state authorities and green energy agencies, including the Solar Energy Corporation of India Limited (SECI) and National Thermal Power Corporation Limited (NTPC), to grant developers certain time extensions to the commissioning deadlines mentioned in their contracts.
Somik Das, Senior Power Analyst at GlobalData, comments: “With time extension granted to developers, the government has provided relief to project developers facing shutdowns due to the COVID-19 outbreak. The pandemic has led to a lockdown due to its high contagiousness. According to the new policy, developers will be able to apply for extended construction schedules if they show evidence and documents proving that the COVID-19 pandemic is impacting their supply chains.”
With the ongoing issues caused by the COVID-19 pandemic across the country, there is expected to be a delay in the engineering and construction activities of projects that were due to be commissioned in the second quarter of 2020.
Das concludes: ”Lack of viable alternatives, transit delays, and the right to invoke force majeure clauses will, in all probability, see the estimates for wind annual installations decline in 2020. Since India is sufficient in terms of turbine production, India’s expected annual wind additions would perhaps not see a drastic decline.
“However, further extension of the current COVID-19 lockdown might perhaps lead to a significant reduction in the project commissioning forecast for 2020. Like other nations, the second half of 2020 will be a critical period for the wind sector of the country.”
- Comments provided by Somik Das, Senior Power Analyst at GlobalData
- This insight was based upon data and information sourced from proprietary databases, primary and secondary research, and in-house analysis conducted by GlobalData’s team of industry experts
About GlobalData
4,000 of the world’s largest companies, including over 70% of FTSE 100 and 60% of Fortune 100 companies, make more timely and better business decisions thanks to GlobalData’s unique data, expert analysis and innovative solutions, all in one platform. GlobalData’s mission is to help our clients decode the future to be more successful and innovative across a range of industries, including the healthcare, consumer, retail, financial, technology and professional services sectors.